- Understanding the Basics of Sheet Metal Design
- Efficient Sketching Techniques
- Mastering the Art of Flange Features
- Advanced Bend Allowance Control
- Incorporating Gussets and Stiffeners for Strength
- Efficient Material Utilization with the Flat Pattern
- Streamlining Documentation with Drawing Templates
- Collaborative Design with SolidWorks PDM
- Staying Updated with SolidWorks Tips and Tricks
- Conclusion
SolidWorks stands out as a powerful and versatile tool, especially in the realm of sheet metal design. Its array of features and capabilities significantly contribute to streamlining the design process and optimizing efficiency. Whether you're a seasoned professional well-versed in SolidWorks or just embarking on your journey with the software, the following tips and tricks will prove instrumental in mastering the intricacies of sheet metal design. If you need help with your sheet metal assignment, these insights can provide valuable assistance in navigating the complexities of your task.
An essential aspect of harnessing SolidWorks for sheet metal design lies in comprehending and utilizing its foundational features. A thorough understanding of concepts like bend radius, K-factor, and sheet metal thickness forms the cornerstone for navigating the more complex aspects of the software. These basics are not merely theoretical; they serve as practical guidelines that shape the precision and accuracy of your designs.
As you progress in your SolidWorks sheet metal design endeavors, delving into parametric design becomes pivotal. Parametric features empower you to create designs that are not only precise but also flexible and easily modifiable. This adaptability proves invaluable when adjustments and iterations are required, allowing you to navigate changes seamlessly without compromising efficiency.
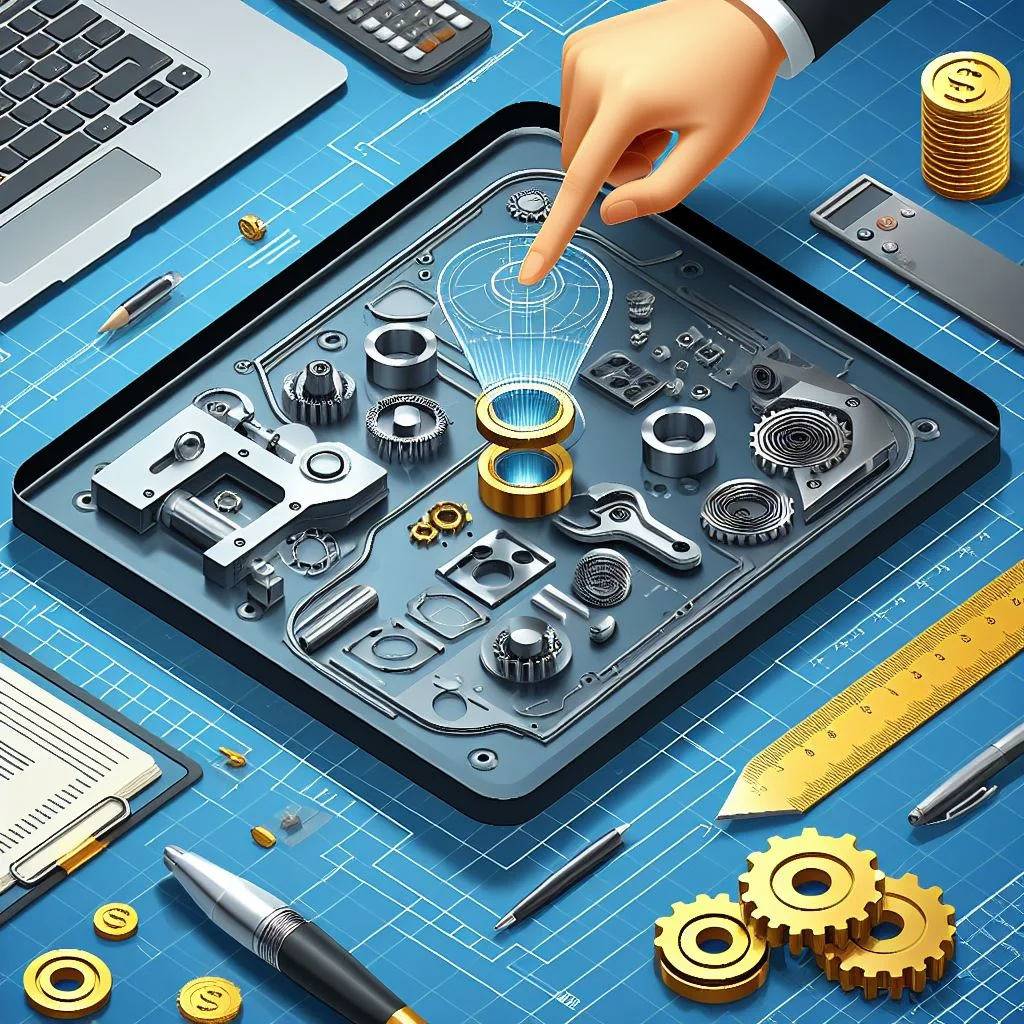
Sketching is the fundamental language of design, and in the context of sheet metal, efficient sketching is paramount. SolidWorks offers a repertoire of tools, and among them, the "Convert Entities" tool stands out. This tool enables the conversion of existing edges into sketch entities, eliminating redundancy and ensuring that your sketches are not only accurate but also easily editable.
Flanges, being integral components in sheet metal design, warrant a closer look. SolidWorks provides various options such as base flanges, miter flanges, and edge flanges. Mastering the art of employing these features enables you to craft intricate designs with the desired outcomes. Understanding how to customize flange parameters becomes crucial, allowing you to tailor designs to specific requirements with finesse.
Bend allowance is a nuanced aspect of sheet metal design that demands attention. SolidWorks facilitates advanced control over bend allowances, empowering designers to fine-tune this element for different materials and bending processes. The incorporation of the "Sheet Metal Gauge Table" further enhances efficiency by providing a systematic approach to managing and customizing bend allowances.
Moving beyond the fundamental aspects, reinforcing your sheet metal designs becomes essential. Gussets and stiffeners play a pivotal role in enhancing structural integrity. Strategically placing these features ensures that critical areas are reinforced, minimizing distortion during the fabrication process. SolidWorks equips designers with tools that simplify the addition and customization of these crucial elements.
Efficient material utilization is a goal that aligns with both economic and environmental considerations. SolidWorks aids in achieving this goal through the flat pattern feature. This feature allows designers to unfold complex sheet metal designs into flat patterns, optimizing material usage and simplifying the manufacturing process.
The journey of a sheet metal design doesn't end with the 3D model; it extends to detailed documentation. Drawing templates in SolidWorks prove indispensable for creating comprehensive manufacturing drawings. Customizing these templates with essential information, such as dimensions, annotations, and material specifications, ensures that your designs are communicated accurately.
For collaborative projects, SolidWorks Product Data Management (PDM) becomes a linchpin. Teams engaged in sheet metal design can benefit immensely from the centralized repository, version control, and collaborative capabilities that SolidWorks PDM offers. It transforms the design process into a seamless collaborative effort, fostering efficiency and teamwork.
Continuous learning is the key to staying ahead in the dynamic landscape of SolidWorks. Regularly checking SolidWorks forums, blogs, and official documentation ensures that you are abreast of the latest tips and tricks. This commitment to ongoing education ensures that you harness the full potential of SolidWorks and continuously refine your sheet metal design skills.
Understanding the Basics of Sheet Metal Design
Before venturing into the intricacies of advanced sheet metal design features, it is imperative to establish a robust foundation by comprehending the basics. A sound understanding of fundamental concepts such as bend radius, K-factor, and sheet metal thickness lays the groundwork for more complex designs.
Bend radius, a key parameter, determines the curvature of bends in the sheet metal. Knowledge of the appropriate bend radius is critical for avoiding material deformation and ensuring structural integrity. The K-factor, representing the ratio of the neutral axis to the material thickness, influences the calculation of flat patterns and bend allowances. Understanding how variations in the K-factor impact the final design is essential for precision.
Equally important is familiarity with sheet metal thickness, as it directly affects the overall strength and manufacturability of the design. Different materials may require adjustments in sheet metal thickness, and this awareness is pivotal for achieving optimal performance.
By grasping these foundational elements, designers can navigate the complexities of sheet metal design with confidence. This knowledge not only facilitates accurate modeling but also enables informed decision-making throughout the design process. As we delve deeper into advanced techniques, the significance of these basics will become even more apparent, shaping the efficiency and success of your sheet metal designs.
Efficient Sketching Techniques
Efficient sketching is undeniably the cornerstone of successful sheet metal design, laying the foundation for accurate and well-defined models. One key technique to master is the utilization of the "Convert Entities" tool within SolidWorks. This tool proves invaluable in streamlining the sketching process by allowing designers to convert existing edges into sketch entities. By doing so, redundant work is significantly reduced, and precision is enhanced.
The "Convert Entities" tool essentially enables designers to trace the contours of existing geometry, transforming them into editable sketch entities. This not only expedites the sketching process but also ensures that the new sketch aligns seamlessly with the underlying geometry. As a result, the risk of inaccuracies is minimized, promoting a more robust and error-free design.
Moreover, the ability to convert entities serves as a time-saving mechanism, especially when dealing with complex or intricate designs. Instead of recreating geometry from scratch, designers can leverage the tool to capture the essence of existing edges, arcs, or lines. This not only accelerates the design workflow but also allows for quick modifications and adjustments as the project evolves.
Mastering the Art of Flange Features
Flanges play a pivotal role in sheet metal design, serving as essential components for achieving structural integrity and design functionality. SolidWorks offers a diverse array of flange options, each catering to distinct design needs. Among these, base flanges, miter flanges, and edge flanges are commonly employed to achieve desired outcomes.
Base flanges serve as the foundation for many sheet metal designs. By understanding the nuances of base flanges, designers can establish a robust starting point for their projects. Miter flanges, on the other hand, facilitate the creation of intricate joints and intersections. Learning to wield miter flanges effectively allows for the seamless integration of complex geometries within a sheet metal design.
Edge flanges, another integral feature, provide designers with the flexibility to define flanges along the edges of a base flange or an existing flange. This versatility empowers designers to adapt their creations to specific project requirements, ensuring a tailored approach to sheet metal design.
Customization of flange parameters adds another layer of sophistication to SolidWorks' capabilities. Designers can fine-tune parameters such as flange length, angle, and relief to align with precise specifications. This level of customization not only enhances the aesthetic aspects of the design but also contributes to the overall efficiency of the manufacturing process.
Advanced Bend Allowance Control
Fine-tuning your sheet metal designs involves mastering the intricacies of bend allowance control, a critical aspect in achieving precision and accuracy in fabrication. SolidWorks provides robust tools to accommodate variations in bend allowances based on different materials and bending processes. This level of control is indispensable when working with diverse materials or when manufacturing processes necessitate specific bend allowances for optimal results.
A key tool in SolidWorks for managing and customizing bend allowances efficiently is the "Sheet Metal Gauge Table." This feature allows designers to create a comprehensive table specifying bend allowances for various materials and thicknesses. By utilizing this table, designers can seamlessly adapt their designs to the unique characteristics of different materials, ensuring that the final product meets both functional and aesthetic requirements.
Understanding the nuances of bend allowance control is essential for achieving consistency in sheet metal designs. Designers can experiment with different bend allowances to find the optimal balance between material flexibility and structural integrity. The flexibility offered by SolidWorks in this regard empowers designers to tailor their approach to the specific needs of each project, resulting in more efficient and precise sheet metal designs.
Incorporating Gussets and Stiffeners for Strength
Enhancing the structural integrity of your sheet metal designs is a crucial aspect of creating robust and reliable products. Incorporating gussets and stiffeners strategically can significantly contribute to reinforcing critical areas and preventing distortion during the fabrication process. In SolidWorks, these elements are not only easy to add but also highly customizable, allowing for precise tailoring to meet specific design requirements.
Gussets are flat, triangular-shaped plates often used to reinforce corners or junctions where two sheet metal components meet. By strategically placing gussets in these areas, you distribute stress more evenly, reducing the risk of deformation and enhancing the overall strength of the structure. SolidWorks offers a user-friendly interface for adding gussets, allowing you to specify dimensions, angles, and attachment points with ease.
Stiffeners, on the other hand, are longitudinal members added to sheet metal designs to resist bending and provide additional rigidity. Understanding how to effectively place stiffeners in key locations is essential for optimizing the structural performance of your design. SolidWorks provides tools that enable you to customize the shape, size, and orientation of stiffeners, ensuring they align seamlessly with your design objectives.
By mastering the incorporation of gussets and stiffeners, you not only bolster the strength of your sheet metal designs but also contribute to the longevity and reliability of the final product. These features play a pivotal role in preventing buckling, minimizing distortion, and ensuring that your designs meet the highest standards of structural integrity in real-world applications.
Efficient Material Utilization with the Flat Pattern
Optimizing material utilization is a critical aspect of sheet metal design, and SolidWorks offers a powerful tool to achieve this goal—the flat pattern feature. This feature allows designers to unfold complex three-dimensional sheet metal models into their flat, 2D representations, providing a clear layout of the material before manufacturing begins.
By understanding how to work with the flat pattern feature in SolidWorks, designers can ensure efficient material utilization. Unfolding the design into a flat pattern enables a comprehensive view of the layout, allowing for precise placement of components and minimizing waste. This is particularly crucial in sheet metal fabrication, where material costs can significantly impact the overall project budget.
Furthermore, the flat pattern feature simplifies the manufacturing process. Manufacturers can use the unfolded design as a template for cutting and shaping the sheet metal, reducing production time and enhancing accuracy. The ability to visualize the flat pattern also aids in identifying potential issues, such as interference or clashes, before the fabrication process begins, preventing costly errors and rework.
Incorporating the flat pattern feature into your SolidWorks sheet metal design workflow not only promotes efficient material utilization but also contributes to a streamlined and cost-effective manufacturing process. Mastering this aspect of SolidWorks empowers designers to create designs that are not only functional but also economically viable, aligning with industry best practices for sustainable and resource-conscious sheet metal fabrication.
Streamlining Documentation with Drawing Templates
Efficient documentation plays a pivotal role in conveying design intent and ensuring seamless communication throughout the manufacturing process. SolidWorks provides a robust solution through its drawing templates, allowing designers to streamline the creation of comprehensive and accurate manufacturing drawings. By leveraging drawing templates, designers can significantly reduce the time and effort required to generate drawings while maintaining consistency across different projects.
SolidWorks drawing templates offer a range of customization options, empowering users to tailor templates to their specific needs. This includes incorporating essential information such as precise dimensions, annotations, and material specifications directly into the template. By establishing standardized templates, designers not only enhance the clarity of their documentation but also ensure that crucial details are consistently communicated to manufacturers and other stakeholders.
Moreover, the customization capabilities of SolidWorks drawing templates extend beyond visual elements. Designers can implement predefined settings for units, tolerances, and drawing scales, fostering a standardized approach across the entire design and manufacturing workflow. This not only accelerates the drawing creation process but also reduces the likelihood of errors and discrepancies in the final documentation.
Collaborative Design with SolidWorks PDM
For teams engaged in intricate sheet metal design projects, the integration of SolidWorks PDM (Product Data Management) stands as a transformative solution. SolidWorks PDM acts as a pivotal force in fostering collaborative design efforts within teams. By establishing a centralized repository for design data, this tool ensures that all team members have access to the latest versions of files, minimizing the risk of errors and discrepancies that can arise from working with outdated information.
One of the primary advantages of SolidWorks PDM is its robust version control system. Team members can confidently work on their assigned tasks, knowing that changes are tracked systematically. The ability to roll back to previous versions offers a safety net, allowing teams to explore different design iterations without the fear of irreversible mistakes.
Beyond version control, SolidWorks PDM promotes seamless collaboration. Team members can easily share their work, provide feedback, and make real-time updates. This collaborative environment enhances communication and coordination, fostering a more efficient and cohesive design process.
Moreover, SolidWorks PDM ensures data integrity by preventing conflicting modifications. With features like check-in and check-out, multiple team members can work on the same project simultaneously without risking data corruption. This functionality streamlines collaboration and supports concurrent design efforts, ultimately accelerating the overall project timeline.
In essence, SolidWorks PDM emerges as a cornerstone for collaborative success in sheet metal design projects. Its capabilities go beyond mere file management, empowering teams to work harmoniously, share insights, and collectively contribute to the realization of superior sheet metal designs. As the dynamics of collaborative design continue to evolve, SolidWorks PDM remains an indispensable tool for teams striving for efficiency, accuracy, and innovation.
Staying Updated with SolidWorks Tips and Tricks
SolidWorks, being a dynamic software, undergoes continuous evolution with regular updates and the introduction of new features. Staying abreast of these changes is crucial for any proficient designer. By actively participating in the SolidWorks community, whether through forums, blogs, or referring to official documentation, designers can tap into a wealth of knowledge and insights.
SolidWorks forums provide a platform for users to share experiences, seek advice, and discuss the latest advancements. Engaging in these discussions exposes designers to real-world challenges and innovative solutions, fostering a collaborative learning environment. Additionally, blogs dedicated to SolidWorks often feature in-depth tutorials, case studies, and expert opinions, offering a rich source of practical tips and tricks.
Official SolidWorks documentation is a treasure trove of information, providing comprehensive guides and detailed explanations of new features. Regularly checking for updates ensures that designers are aware of the latest tools and functionalities, empowering them to optimize their workflow and enhance efficiency.
Continuous learning is not just about adapting to new features; it's about refining existing skills and exploring alternative approaches. Embracing a mindset of ongoing education ensures that designers not only keep up with industry trends but also maximize their proficiency with SolidWorks, ultimately leading to more robust and innovative sheet metal designs.
Conclusion
In conclusion, mastering sheet metal design in SolidWorks is a journey that involves a combination of foundational knowledge, advanced techniques, and continuous learning. By understanding the basics, such as bend radius and K-factor, and honing your parametric design skills, you lay a solid foundation for efficient sheet metal designs. The art of sketching is paramount, and the use of tools like "Convert Entities" can significantly enhance accuracy and streamline the sketching process.
Flange features play a pivotal role in sheet metal design, and exploring options like base flanges, miter flanges, and edge flanges provides versatility in creating complex geometries. Fine-tuning bend allowance control is essential for precision, and SolidWorks offers tools to customize allowances based on materials and bending processes. Adding gussets and stiffeners strategically reinforces designs, ensuring structural integrity and minimizing distortion during fabrication.
Efficiency in material utilization is achieved through mastering the flat pattern feature. Unfolding intricate designs into flat patterns not only optimizes material usage but also simplifies the manufacturing process. Drawing templates further enhance efficiency by facilitating the creation of detailed and accurate manufacturing drawings. Customizing templates with dimensions, annotations, and material specifications streamlines documentation and communication of design intent.
For collaborative projects, SolidWorks PDM proves invaluable. This product data management solution centralizes design data, provides version control, and fosters collaboration among team members. Staying updated with the latest tips and tricks ensures that you leverage SolidWorks to its fullest potential, taking advantage of new features and improvements.
As you embark on your journey to master sheet metal design in SolidWorks, remember that continuous learning is key. Regularly check SolidWorks forums, blogs, and official documentation to stay informed about updates and new features. Embrace challenges as opportunities for growth, and don't hesitate to explore innovative approaches to problem-solving.
In essence, the world of sheet metal design in SolidWorks is dynamic and ever-evolving. By incorporating the tips and tricks discussed, you not only enhance your efficiency but also open doors to more creative and sophisticated designs. The ability to adapt to new challenges and integrate the latest features ensures that you remain at the forefront of sheet metal design expertise.
In your pursuit of excellence, leverage the power of SolidWorks to transform your designs from concepts to tangible, manufacturable products. The combination of technical expertise, creativity, and a commitment to continuous improvement will undoubtedly set you on a path to success in the exciting realm of sheet metal design.