- Understanding the Basics
- Efficient Sketching Techniques
- Utilizing Design Tables for Parametric Control
- Leveraging Custom Properties for Documentation
- Integrating Simulation for Structural Analysis
- Advanced Flange Features and Forming Tools
- Streamlining Manufacturing with Flat Pattern and Unfold
- Collaborative Design with 3DExperience Platform
- Embracing Industry 4.0: IoT and SolidWorks Integration
- Conclusion
SolidWorks, a premier computer-aided design (CAD) software, stands out as an indispensable tool in the realm of sheet metal design. Its robust suite of features caters to both seasoned professionals and beginners, providing a versatile platform to conceptualize and execute intricate designs. The importance of optimizing the sheet metal design process cannot be overstated, as it directly influences efficiency and overall project outcomes. In the following sections, we'll unravel a treasure trove of expert tips and secrets aimed at refining your approach to SolidWorks sheet metal design. If you need assistance with your sheet metal assignment, exploring these expert tips and secrets can enhance your proficiency and effectiveness in utilizing SolidWorks for your design projects.
Before delving into the intricacies, it's crucial to grasp the fundamental essence of SolidWorks sheet metal design. This software is more than a tool; it's a comprehensive ecosystem where every command and feature is meticulously crafted to cater to the unique challenges posed by sheet metal. Whether you're sketching a basic form or manipulating complex geometries, SolidWorks provides an intuitive interface and a plethora of tools designed to meet your specific needs.
Efficiency in sheet metal design starts with mastering the art of sketching. Precise sketches serve as the foundation for your components, and SolidWorks offers advanced sketching techniques to elevate your designs. Dive into the world of reference geometry, parametric design, and strategic dimensioning to ensure that your sketches are not only accurate but also adaptable to changes that may arise during the design process.
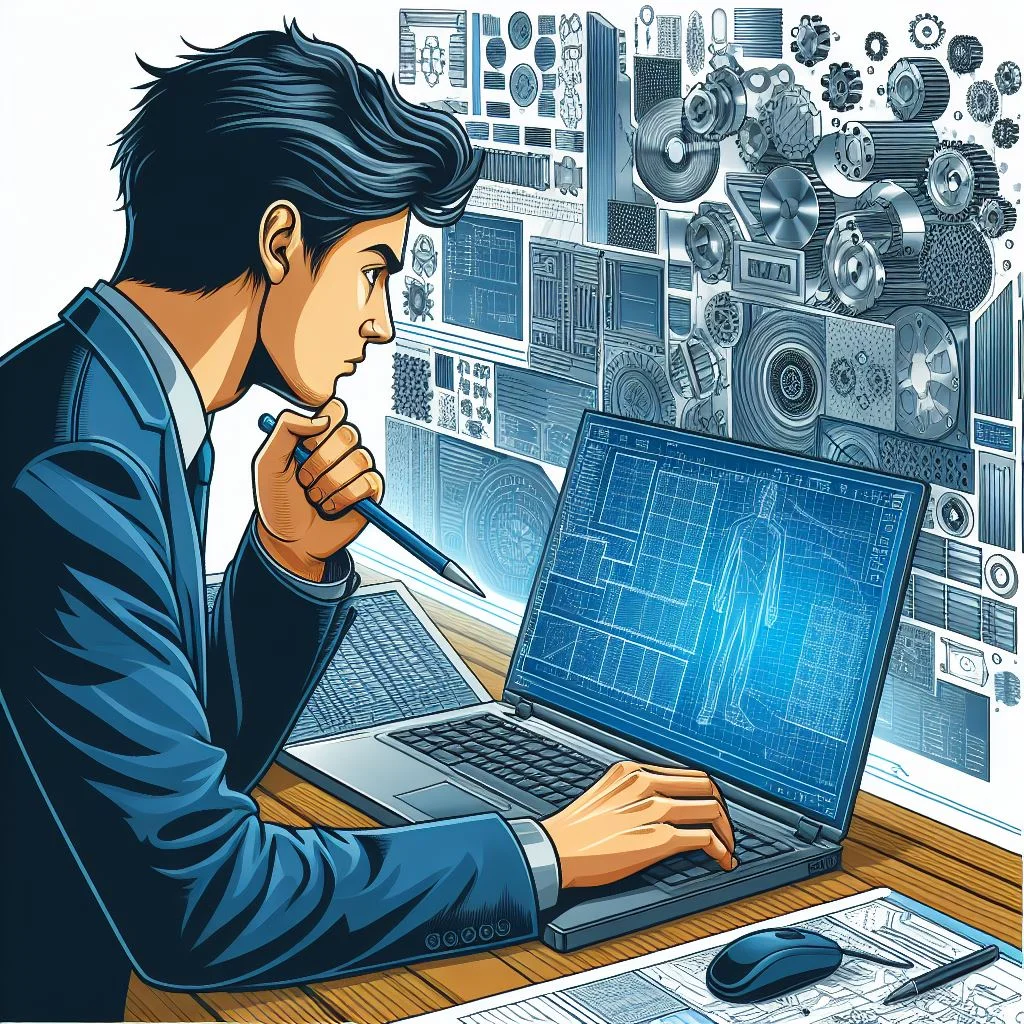
A hidden gem in the SolidWorks arsenal is the use of design tables for achieving parametric control. This feature empowers designers to create relationships between variables, allowing for swift adjustments and updates. Imagine the time saved when a single tweak in a design variable automatically propagates through the entire model. Design tables, when mastered, become a dynamic tool for efficient iterations in the sheet metal design process.
Moving beyond the basics, the integration of simulation tools becomes paramount for ensuring the structural integrity of your sheet metal designs. SolidWorks offers a robust simulation environment where you can subject your models to various forces and conditions, obtaining critical insights into potential issues. This not only enhances the reliability of your designs but also facilitates informed decision-making based on simulation results.
Advanced flange features and forming tools within SolidWorks open up avenues for creating complex geometries and intricate bends with precision. Understanding the nuances of these features is akin to unlocking a new dimension in your design capabilities. Whether you're working on a project that demands intricate folds or a design with unique forming requirements, SolidWorks provides the tools needed to bring your vision to life.
In the realm of documentation, leveraging custom properties in SolidWorks proves to be a game-changer. Streamline the creation of bills of materials (BOMs) and other essential documentation by customizing and automating data entry. This not only enhances accuracy but also ensures consistency across different aspects of your sheet metal design.
The transition from design to manufacturing is a critical phase, and SolidWorks facilitates this seamlessly with features like Flat Pattern and Unfold. Generating accurate flat patterns for manufacturing processes such as laser cutting or waterjet cutting becomes a breeze, minimizing errors and optimizing material usage. These features bridge the gap between the digital design realm and the physical manifestation of your sheet metal creations.
Collaborative design takes center stage with the integration of the 3DExperience platform into SolidWorks. This cloud-based solution revolutionizes teamwork, allowing multiple stakeholders to contribute seamlessly to the sheet metal design process. Enhanced communication and real-time collaboration become the pillars supporting a more dynamic and efficient design workflow.
As we look toward the future of sheet metal design, embracing Industry 4.0 becomes imperative. The integration of Internet of Things (IoT) technologies with SolidWorks opens up new horizons. Real-time data and connectivity provide invaluable insights into manufacturing, maintenance, and product lifecycle management. This forward-looking approach ensures that your sheet metal designs not only meet current standards but are also future-proofed in the rapidly evolving landscape of technological advancements.
Understanding the Basics
Before diving into advanced tips, it's crucial to have a solid understanding of the basics. Mastering the foundational elements of SolidWorks sheet metal design sets the stage for efficiency. As you embark on your sheet metal design journey, familiarize yourself with the software's interface, commands, and tools tailored specifically for sheet metal applications. Understanding how to navigate the user interface seamlessly will enhance your overall design experience.
Delve into the specialized commands that SolidWorks offers for sheet metal design. These commands, often distinct from general CAD tools, empower you to create and manipulate sheet metal components with precision. Familiarity with tools like the Base Flange, Edge Flange, and Miter Flange is essential for crafting accurate and intricate sheet metal designs.
Additionally, take the time to explore the unique features designed for sheet metal, such as Bend Allowance and K-Factor settings. A thorough grasp of these parameters ensures the accuracy of your designs, particularly when it comes to predicting how materials will behave during the bending process.
By immersing yourself in the foundational aspects of SolidWorks sheet metal design, you lay the groundwork for a more efficient and productive design process. Take the time to build this expertise, and you'll find that navigating the complexities of sheet metal design becomes second nature.
Efficient Sketching Techniques
Effective sheet metal design begins with precise sketches. In SolidWorks, mastering advanced sketching techniques is essential for creating accurate profiles that lay the foundation for successful sheet metal components. One key aspect to explore is the utilization of reference geometry, allowing you to establish relationships between different parts of your design. This feature provides a dynamic approach, ensuring changes in one part of the sketch seamlessly propagate to others.
Furthermore, delve into the realm of parametric design within SolidWorks. This powerful capability enables you to establish relationships between various parameters, providing flexibility in making design adjustments. By defining these relationships, you can easily modify dimensions and characteristics, maintaining design integrity throughout the iterative process.
Dimensioning strategies also play a crucial role in efficient sketching. SolidWorks offers a range of dimensioning tools that go beyond basic measurements. Discover how to use smart dimensioning and geometric dimensioning and tolerancing (GD&T) to convey precise information about your sheet metal design. Implementing these strategies not only enhances accuracy but also streamlines the overall design process.
Utilizing Design Tables for Parametric Control
Unlock the power of design tables in SolidWorks for parametric control over your sheet metal designs. This advanced feature allows you to create parametric relationships between variables, enabling quick adjustments and updates. Dive into examples of how design tables can revolutionize your design process.
Design tables are a game-changer in SolidWorks sheet metal design, offering a systematic approach to managing parameters and dimensions. By defining variables within a design table, you gain unparalleled control over your model's dimensions, configurations, and features. This not only enhances the adaptability of your design but also facilitates efficient exploration of various design scenarios.
Imagine a scenario where you need to modify the thickness of a sheet metal component across multiple configurations. Instead of manually adjusting each dimension, a design table empowers you to make universal changes by updating a single parameter. This not only saves time but also minimizes the risk of errors associated with manual adjustments.
Furthermore, design tables enable the creation of multiple configurations with distinct parameter sets. This proves invaluable when dealing with diverse product lines or variations within a design. The ability to quickly switch between configurations and visualize the impact of parameter changes streamlines the decision-making process.
Incorporating design tables into your SolidWorks sheet metal workflow fosters a dynamic and adaptable design environment. Whether you're addressing client feedback, accommodating material variations, or responding to manufacturing constraints, design tables provide the flexibility needed to meet evolving requirements. Embrace the power of parametric control through design tables and elevate your sheet metal design capabilities to new heights.
Leveraging Custom Properties for Documentation
Efficient documentation is crucial in sheet metal design, playing a pivotal role in the seamless transition from design to manufacturing. One key aspect that can significantly enhance this process is leveraging custom properties within SolidWorks. These properties allow you to attach specific information to components, facilitating the automated creation of bills of materials (BOMs) and other documentation.
Custom properties act as metadata for your sheet metal designs, providing essential information about each component. By customizing and automating data entry through these properties, you not only enhance the accuracy of your documentation but also save valuable time during the design process. This becomes particularly beneficial when dealing with large and intricate assemblies, where manual data entry can be time-consuming and prone to errors.
For instance, you can assign properties such as material type, thickness, or part numbers to components. When generating BOMs or other documentation, SolidWorks can automatically populate these details, ensuring consistency and accuracy throughout the project. This streamlining of the documentation process not only improves efficiency but also facilitates effective communication between design teams and stakeholders, contributing to the overall success of your sheet metal design projects.
Integrating Simulation for Structural Analysis
Enhance the reliability of your sheet metal designs by incorporating simulation tools within SolidWorks. Structural analysis can identify potential issues and optimize your designs for performance and durability. By simulating real-world conditions, you gain insights into how your sheet metal components will behave under various loads and stresses. This empowers you to make informed design decisions, ensuring that your products meet performance expectations and comply with safety standards.
Explore how to interpret simulation results effectively, considering factors like stress distribution, deformation, and material behavior. This knowledge allows you to refine your designs, address potential weak points, and optimize for structural integrity. By integrating simulation early in the design process, you can avoid costly errors and rework, leading to more efficient and reliable sheet metal designs.
Advanced Flange Features and Forming Tools
Advanced Flange Features and Forming Tools in SolidWorks offer a pivotal set of capabilities to take your sheet metal designs to the next level. These sophisticated tools empower designers to explore intricate geometries, bends, and forms with an unparalleled level of precision. By delving into the nuances of these advanced features, designers can unlock a myriad of possibilities for creating complex and innovative sheet metal components.
One key aspect to focus on is the ability to create flanges with variable parameters. SolidWorks allows you to tailor flange features to meet specific design requirements, enabling the development of components with varying thicknesses and geometries. This adaptability proves invaluable when working on projects that demand a diverse range of sheet metal configurations.
Forming tools further enhance the designer's toolkit by providing a means to replicate real-world manufacturing processes within the virtual environment. Understanding how to leverage forming tools enables the simulation of intricate bends, folds, and deformations, ensuring that the designed sheet metal components align seamlessly with the manufacturing process.
Optimizing these advanced flange features and forming tools for various manufacturing processes is paramount. By tailoring your designs to the nuances of specific fabrication methods, you can minimize production challenges and enhance the overall efficiency of the manufacturing workflow. This level of optimization not only streamlines the design process but also contributes to cost savings and improved final product quality.
Streamlining Manufacturing with Flat Pattern and Unfold
Efficiently transitioning from design to manufacturing is a pivotal phase in sheet metal fabrication, and SolidWorks provides indispensable tools to simplify this process. The Flat Pattern and Unfold features play a crucial role in translating your intricate 3D designs into practical, manufacturable components.
Mastering these features empowers you to generate accurate flat patterns tailored for various manufacturing techniques such as laser cutting, waterjet cutting, or stamping. SolidWorks offers a user-friendly interface for unfolding your 3D models, allowing you to visualize and refine the flat patterns with precision.
As you delve into the nuances of Flat Pattern and Unfold, it's essential to explore best practices that can significantly impact the manufacturing efficiency. By minimizing errors and optimizing material usage, you not only save costs but also contribute to sustainable and eco-friendly manufacturing practices.
Considerations such as bend allowances, relief cuts, and nesting strategies become paramount. SolidWorks provides tools to simulate the unfolding process, enabling you to identify potential issues and make adjustments before sending your designs to the manufacturing floor.
Incorporating these best practices into your sheet metal design workflow ensures a smooth transition from the virtual realm to the physical product, aligning your designs with manufacturing requirements and industry standards. This holistic approach enhances not only the efficiency but also the overall quality of your sheet metal components, establishing you as a proficient SolidWorks user in the realm of manufacturing.
Collaborative Design with 3DExperience Platform
Collaborative design is a game-changer in the realm of sheet metal design, and the integration of SolidWorks with the 3DExperience platform amplifies this transformative potential. This cloud-based solution not only facilitates seamless communication but also fosters a collaborative environment where multiple stakeholders can actively contribute to the sheet metal design process.
By leveraging the 3DExperience platform, designers, engineers, and manufacturers can work together in real-time, breaking down traditional silos that often hinder efficiency. This collaborative synergy allows for instant feedback, reducing the likelihood of errors and ensuring that all team members are on the same page throughout the design journey. Whether it's conceptualizing new ideas, reviewing designs, or making crucial decisions, the 3DExperience platform provides a centralized hub for enhanced teamwork.
Furthermore, the cloud-based nature of this platform means that collaborators can access the project from anywhere, promoting flexibility and accommodating diverse work arrangements. This accessibility ensures that geographical boundaries don't impede collaboration, making it easier for global teams to work together seamlessly. As a result, the 3DExperience platform becomes an indispensable tool for not just improving the design process but also fostering a culture of innovation and teamwork within your sheet metal design projects.
Embracing Industry 4.0: IoT and SolidWorks Integration
In the fast-evolving landscape of sheet metal design, staying abreast of technological advancements is paramount. One such frontier is the integration of Internet of Things (IoT) technologies with SolidWorks, marking a pivotal step into Industry 4.0. This integration brings forth a paradigm shift in the sheet metal design process by introducing real-time data and connectivity.
With the infusion of IoT into SolidWorks, designers can access a wealth of data that goes beyond the confines of traditional design parameters. Real-time insights into manufacturing processes allow for swift adjustments and optimization, ensuring that designs align seamlessly with production requirements. This connectivity extends to maintenance aspects, where IoT-enabled sensors can provide continuous feedback on the health and performance of sheet metal components.
Moreover, the integration of IoT with SolidWorks transcends the design phase and extends into product lifecycle management. By harnessing data throughout the lifecycle, from conception to disposal, designers can make informed decisions that enhance durability, reduce downtime, and contribute to sustainability goals.
Conclusion
In the expansive realm of SolidWorks sheet metal design, the journey we've embarked upon is a testament to the intricate dance between creativity and precision. As we draw the curtain on our exploration of expert tips and secrets, it's crucial to distill the essence of our discoveries and reflect on the transformative impact these insights can have on your design process.
The foundation of efficiency in sheet metal design lies in a nuanced understanding of SolidWorks, transcending it from a mere tool to a dynamic ecosystem. The software's intuitive interface and diverse set of features cater to the spectrum of design complexities, empowering both seasoned professionals and novices alike. It is within this environment that our exploration began—a journey to unravel the mysteries that elevate sheet metal design from the ordinary to the extraordinary.
At the heart of this exploration is the acknowledgment that efficiency is not a singular achievement but a series of well-orchestrated moves. Mastery of sketching techniques lays the groundwork for precision, while the adept use of reference geometry and parametric design ensures adaptability in the face of design changes. SolidWorks becomes not just a canvas but a responsive medium through which your ideas take shape with finesse.
The revelation of design tables as a tool for parametric control is akin to discovering a hidden passage to efficiency. The ability to create relationships between variables adds a layer of agility to your design process, turning what could be a time-consuming task into a dynamic and iterative dance. Design tables, when harnessed, transform the way you interact with your model, allowing you to effortlessly explore variations and fine-tune your sheet metal designs.
Simulation emerges as a guardian of design integrity, providing a virtual realm to subject your models to the rigors of real-world conditions. The insights gained from this virtual testing ground not only bolster the reliability of your designs but also empower you to make informed decisions. SolidWorks simulation is not merely a validation tool; it's a partner in ensuring the structural soundness of your sheet metal creations.
As we ascend the ladder of complexity, advanced flange features and forming tools come into play, offering a gateway to intricate geometries and precise bends. The mastery of these features is a transformative step, propelling your design capabilities to new heights. Whether you're crafting components with demanding folds or seeking precision in forming, SolidWorks provides the tools to turn your vision into reality.
In the realm of documentation, the integration of custom properties streamlines the often meticulous task of creating bills of materials and other essential documents. Automation becomes a silent ally, reducing the risk of errors and ensuring consistency across the documentation spectrum. SolidWorks, in this regard, is not just a design platform; it's an assistant in the meticulous art of documentation.
The journey from digital design to physical manifestation is marked by the seamless transition facilitated by features like Flat Pattern and Unfold. The accuracy in generating flat patterns for manufacturing processes becomes a testament to the efficiency of the SolidWorks ecosystem. Bridging the gap between the virtual and physical worlds, SolidWorks ensures that your designs are translated into reality with precision and reliability.
Collaboration takes center stage as the 3DExperience platform integrates seamlessly with SolidWorks. The cloud-based solution transforms teamwork, enabling multiple contributors to participate in the sheet metal design process in real-time. Communication becomes fluid, and the collaborative spirit fosters a dynamic workflow where ideas converge and evolve, ultimately enriching the final design.
As we stand at the crossroads of the present and the future, the integration of Industry 4.0 principles marks the next frontier. The marriage of SolidWorks with Internet of Things (IoT) technologies heralds a new era of connectivity and real-time data. This forward-thinking approach ensures that your sheet metal designs are not only relevant in the current landscape but also equipped to adapt to the ever-evolving landscape of technological advancements.