- Creating Reference Planes
- 1. Using the Reference Plane Command
- 2. Offset Reference Planes
- 3. Angle Reference Planes
- 4. Tangent Reference Planes
- Creating Extrude Features
- 1. Direction 1 and Direction 2
- 2. From Option
- 3. Thin Feature
- Applying Draft and Selecting Contours
- Creating Revolve Features
- Creating Swept Features
- Creating Loft Features
- Conclusion
SolidWorks is a powerful 3D CAD (Computer-Aided Design) software widely used by engineers, architects, and designers for designing complex 3D models and assemblies. Whether you're a seasoned SolidWorks user or just starting out, understanding advanced modeling techniques is crucial for efficient and precise design. In this blog, we'll delve into the intricacies of creating reference planes, extrude, revolve, sweep, and loft features while exploring various options within each feature to help you complete your 3D modeling assignment and take your skills to the next level.
Creating Reference Planes
Reference planes in SolidWorks serve as the foundation for your 3D model, offering a structured and precise space for sketching and constructing features. They play a pivotal role in defining the spatial context of your design. In this chapter, we will explore the various aspects of creating reference planes and how to use them effectively to enhance your SolidWorks modeling skills.
1. Using the Reference Plane Command
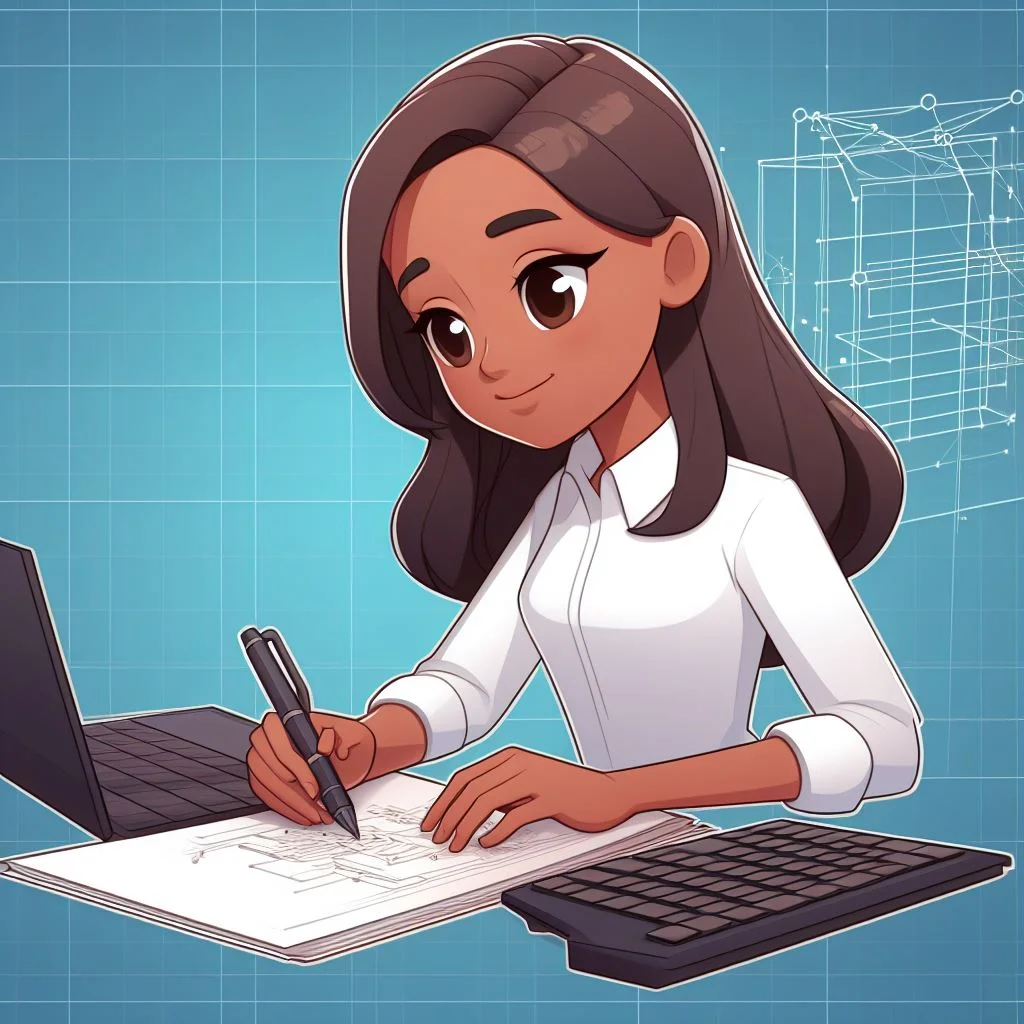
To initiate the creation of reference planes, you need to access the "Reference Plane" command within SolidWorks. Follow these steps:
- Access the Command Manager: Start by navigating to the Command Manager at the top of the SolidWorks interface. The Command Manager is where you'll find various tools and features for creating and modifying your 3D model.
- Select "Reference Geometry":Click on the "Reference Geometry" dropdown in the Command Manager. This dropdown contains a variety of options for defining reference elements in your model.
- Choose "Plane":From the "Reference Geometry" dropdown, select the "Plane" option. This action will prompt SolidWorks to initiate the reference plane creation process.
- Specify Orientation and Position:With the "Plane" option activated, you can now specify the orientation and position of the reference plane. This is crucial for ensuring that the reference plane aligns with your design intent.
- Orientation:You can set the orientation of the plane by choosing its normal vector. This defines the direction in which the plane faces, and you can control this orientation to suit your specific design requirements.
- Position: Determine the position of the reference plane concerning existing geometry. You can specify distances, offsets, and angles to precisely locate the reference plane within your model space.
2. Offset Reference Planes
Creating offset reference planes allows you to establish planes at specific distances from existing planes or surfaces. This is a valuable technique when you need to work with multiple reference planes that are parallel or perpendicular to each other. Here's how to create offset reference planes:
- Select an Existing Plane or Surface:Begin by selecting an existing reference plane or surface as a reference point for your offset plane. This will serve as a starting reference.
- Define the Offset Distance: Specify the desired offset distance. You can enter this value manually, or you can use dynamic dragging to interactively adjust the distance.
- Orientation: Just like when creating regular reference planes, you can set the orientation of your offset plane. This ensures it aligns precisely with your design intent.
Offset reference planes are valuable for tasks like creating complex assemblies or working on multi-part designs where alignment and spacing are critical.
3. Angle Reference Planes
Angle reference planes are particularly useful when you need to create features in your model at specific angles. Here's how to utilize angle reference planes:
- Select the "Angle" Option:Within the Reference Plane creation dialog, you can choose the "Angle" option.
- Define the Angle:Specify the desired angle for the reference plane. You can enter this angle manually, or you can use dynamic dragging to interactively adjust the angle.
- Position:As with other reference planes, you can also specify the position of the angle reference plane concerning existing geometry.
Angle reference planes are beneficial in situations where you need to model features with complex orientations, such as inclined cuts or specialized components.
4. Tangent Reference Planes
Tangent reference planes are particularly helpful when dealing with cylindrical or conical surfaces. These reference planes are designed to be tangent to such surfaces, facilitating the creation of features that follow the contour of the underlying geometry. Here's how to work with tangent reference planes:
- Select "Tangent" Option: In the Reference Plane creation dialog, choose the "Tangent" option.
- Select the Surface:Click on the cylindrical or conical surface to which you want to create a tangent reference plane. The reference plane will align itself with the surface, ensuring it remains tangent.
- Orientation and Position:As always, you can specify the orientation and position of the tangent reference plane to fine-tune its location and alignment.
Tangent reference planes are essential for creating features like fillets, chamfers, or any geometry that smoothly transitions along curved surfaces.
Reference planes in SolidWorks are fundamental elements that provide a structured and precise space for sketching and creating features. Understanding how to create these planes, whether through the Reference Plane Command, offsetting, adding angles, or creating tangent planes, is crucial for precise and efficient 3D modeling. As you master these techniques, you'll find yourself better equipped to tackle complex design challenges and create intricate 3D models with confidence. SolidWorks empowers you to bring your design ideas to life, and reference planes are the first step in that journey to precision and creativity.
Creating Extrude Features
Extrude features are the cornerstone of 3D modeling in SolidWorks, allowing you to add depth and volume to your 2D sketches, ultimately creating complex 3D shapes. In this chapter, we'll delve into the intricacies of creating extrude features, exploring various options that SolidWorks offers for enhancing the flexibility and precision of your designs.
1. Direction 1 and Direction 2
One of the primary attributes of an extrude feature is its direction. SolidWorks provides two distinct directions, Direction 1 and Direction 2, which offer flexibility in how your extrusion extends in the model space.
- Direction 1:When you create an extrude feature and specify Direction 1, the feature extends in a defined direction from the sketch plane. This direction is typically outward from the sketch plane, allowing you to build your model in a specific direction.
- Direction 2:Direction 2, on the other hand, enables you to extrude in the opposite direction, retracting from the sketch plane. It's particularly useful when you need to create cuts or recesses in your model.
Understanding and choosing the appropriate direction is crucial for ensuring that your extrude feature aligns with your design intent and the geometry of your 3D model.
2. From Option
The "From" option in SolidWorks extrude features provides control over where your extrusion starts. It's a fundamental choice when creating extrusions and can significantly impact the final shape of your model.
- Extrude from Sketch: When you select the "From Sketch" option, you are specifying that the extrusion should originate from the sketch you've created. This is particularly useful when you have a detailed sketch in place and want to use it as the basis for your extrusion.
- Extrude from Surface:Alternatively, you can choose to extrude from a surface. This option allows you to start your extrusion from a specific surface within your model. It's useful when you need to align your extrusion with an existing surface or when creating complex shapes that require reference to other surfaces.
The "From" option provides the flexibility to determine precisely where your extrusion begins, ensuring that it's positioned according to your design requirements.
3. Thin Feature
Creating thin-walled parts is a common requirement in various design scenarios, such as sheet metal components or lightweight structures. SolidWorks offers the "Thin Feature" option to address this need effectively.
- Define Thickness:When you select the "Thin Feature" option, you can define the thickness of your extrusion. This thickness can be less than the profile you're extruding. This feature is particularly useful when you need to create walls or structures with a specific thickness, as it simplifies the modeling process.
- Controlling Wall Thickness: You have control over the thin feature's wall thickness, enabling you to create structures with varying thicknesses within a single model.
- Avoiding Interference:Using the "Thin Feature" option, you can ensure that the extrusion does not interfere with other model components, as SolidWorks automatically trims and removes any excess material that might cause conflicts.
- Efficient Sheet Metal Design:For sheet metal design, the "Thin Feature" option simplifies the process of creating walls and flanges, allowing you to work with precise dimensions and maintaining the integrity of the design.
Creating extrude features is a fundamental aspect of 3D modeling in SolidWorks, and understanding the various options available is essential for efficiently and accurately building your 3D models. The ability to control the direction, specify the "From" option, and create thin-walled parts gives you the flexibility to bring your design ideas to life.
Whether you are designing mechanical parts, architectural components, or any other 3D models, the extrude feature in SolidWorks empowers you to shape and structure your designs with precision. By mastering the nuances of extrusion, you'll be better equipped to tackle a wide range of design challenges and create intricate, functional, and visually appealing 3D models.
Applying Draft and Selecting Contours
Draft is crucial for designing parts that can be easily ejected from molds or assembled with other components. Here's how to apply draft and select contours:
- Applying Draft: When creating extrude or revolve features, you can add draft to the feature. Specify the draft angle and the faces to apply it to.
- Selecting Contours:Selecting contours is an essential part of creating various features. Contours define the shape and size of the feature. SolidWorks provides tools for easily selecting the contours you want to use in your feature.
Creating Revolve Features
Revolve features involve rotating a sketch profile around an axis. Here's how to create revolve features with SolidWorks:
- Selecting Axis: Specify the axis around which you want to revolve your sketch profile. The axis can be an edge, a sketch line, or even an axis you create.
- Thin Features:Similar to extrusions, you can create thin-walled parts using the thin feature option. Define the thickness of your revolved feature.
- Selecting Contours: Carefully select the contours that make up your sketch profile to ensure precision and accuracy in your revolve feature.
Creating Swept Features
Swept features are essential for creating complex shapes in SolidWorks. Let's explore how to create swept features:
- Selecting Profile and Path: For a swept feature, you need to select a profile sketch and a path sketch. The profile sketch defines the cross-section of the feature, and the path sketch defines the trajectory the profile follows.
- Thin Feature: Like extrude and revolve features, you can create thin features when sweeping a profile along a path.
Creating Loft Features
Loft features are advanced modeling tools that allow you to create smooth transitions between different profiles. Here's how to create loft features in SolidWorks:
- Selecting Profiles:Loft features require a minimum of two profiles. You can select more profiles to create complex shapes. SolidWorks smoothly blends between the selected profiles.
- Guide Curves: For more control over the shape of the loft, you can add guide curves. These curves help define the trajectory the lofted feature follows, allowing for precise modeling.
Conclusion
SolidWorks offers a wide range of tools and features to help you create complex 3D models with precision and efficiency. In this blog, we've explored creating reference planes, extrude features, revolve features, sweep features, and loft features. Mastering these advanced modeling techniques will empower you to design intricate and accurate 3D models for a variety of applications.
As a student or professional, these techniques are invaluable for tackling complex SolidWorks assignments and projects. So, whether you're working on a simple part or a complex assembly, you now have a solid foundation to create, modify, and optimize your 3D models using SolidWorks. With practice and application, you'll become a proficient SolidWorks user capable of tackling the most intricate design challenges.