- SolidWorks: A Brief Overview
- Exploring the Pros of SolidWorks
- Exploring the Cons of SolidWorks
- Comparing with AutoCAD
- Pros of AutoCAD
- Cons of AutoCAD
- Comparing with Fusion 360
- Pros of Fusion 360
- Cons of Fusion 360
- Comparing with CATIA
- Pros of CATIA
- Cons of CATIA
- Conclusion
Computer-aided design (CAD) software has revolutionized the way engineers, architects, and designers create and visualize complex designs. Among the myriad of CAD tools available, SolidWorks has gained prominence as a leading player. However, it's essential to recognize that there are other CAD software options available, each with its own strengths and weaknesses. In this blog, we'll dive into the world of CAD software, comparing SolidWorks with some of its counterparts, and highlighting their pros and cons. Whether you're looking to do your SolidWorks assignment or explore alternatives, understanding the landscape of CAD tools is crucial.
SolidWorks: A Brief Overview
SolidWorks, developed by Dassault Systèmes, is a parametric solid modeling CAD software widely used for 3D design, simulation, and data management. It provides an intuitive user interface and a comprehensive suite of tools for creating intricate 3D models and assemblies. Its parametric modeling allows users to create design relationships and constraints, enabling dynamic changes to the model as design parameters are modified.
Exploring the Pros of SolidWorks
SolidWorks, a cornerstone in the world of CAD software, offers a multitude of benefits that make it a top choice for engineers, designers, and manufacturers. Let's delve into the advantages that SolidWorks brings to the table:
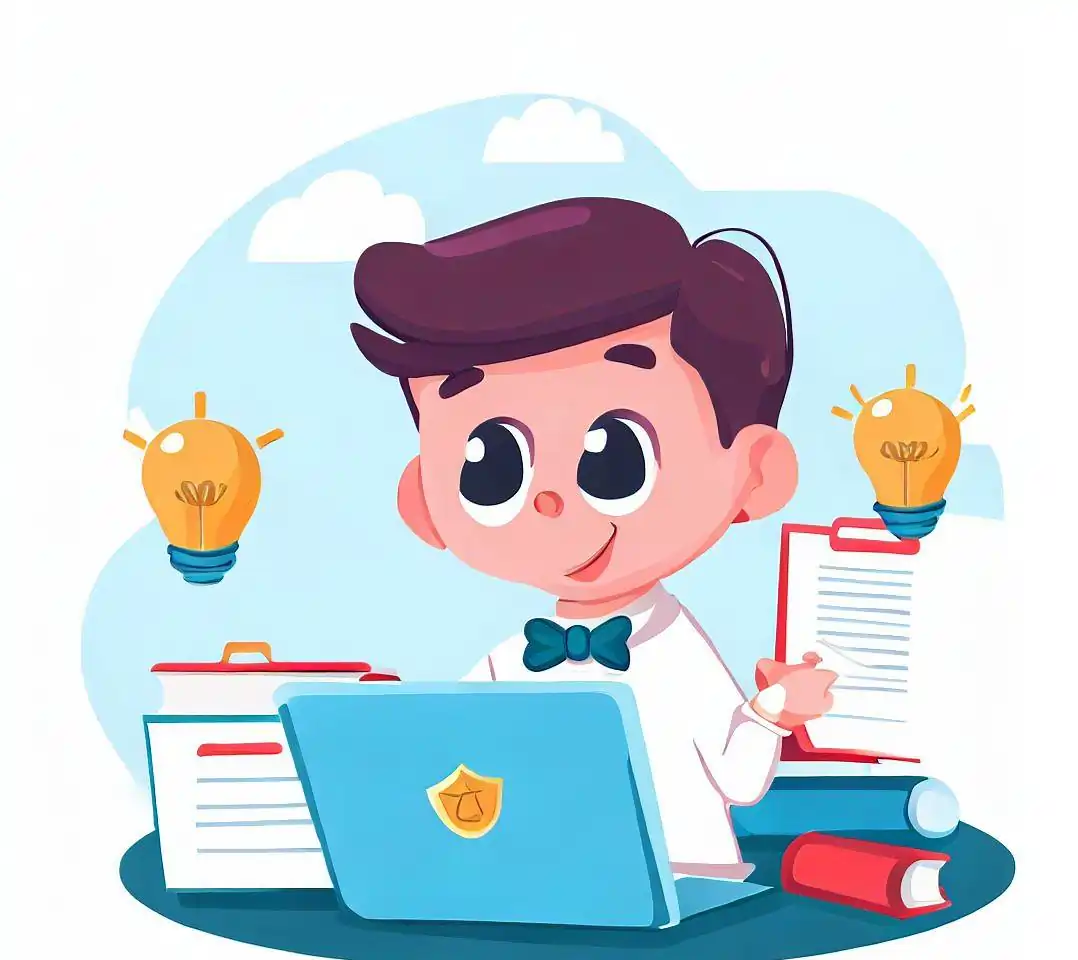
- Parametric Modeling
- User-Friendly Interface
- Wide Range of Features
- Strong Community and Resources
- Integration with Other Tools
Parametric modeling is at the core of SolidWorks' strength. This methodology enables designers to create relationships and constraints between different design elements. When modifications are made to one part of the model, the software automatically updates all associated features, maintaining the design's integrity. This feature significantly enhances design flexibility, reduces errors, and expedites the design iteration process.
SolidWorks has earned a reputation for its user-friendly interface, making it accessible to both beginners and experienced users. The software's intuitive drag-and-drop features, contextual menus, and customizable toolbars streamline the design process. This ease of use minimizes the learning curve, allowing users to focus on the creative aspects of design rather than grappling with complicated software mechanics.
SolidWorks stands out by offering an extensive array of features that cater to various stages of product development. Whether you're creating complex 3D models, assembling intricate components, performing simulations, conducting stress analysis, or generating photorealistic renderings, SolidWorks provides a comprehensive toolset under one roof. This eliminates the need to switch between multiple software programs, enhancing productivity and cohesion in the design process.
SolidWorks benefits from a thriving user community that actively engages in sharing knowledge, troubleshooting, and offering valuable insights. This expansive network contributes to an abundance of tutorials, forums, and resources readily available online. Whether you're a novice seeking guidance or an expert seeking optimization tips, the SolidWorks community provides an invaluable platform for learning and growth.
SolidWorks doesn't exist in isolation; it seamlessly integrates with other engineering tools, enabling holistic product analysis and simulation. For instance, integration with Finite Element Analysis (FEA) software empowers engineers to assess the structural integrity of designs. Likewise, coupling SolidWorks with Computational Fluid Dynamics (CFD) software facilitates the analysis of fluid flow and heat transfer within a design. This integration ensures that designs not only look good but also perform effectively.
Exploring the Cons of SolidWorks
While SolidWorks has garnered immense popularity and a slew of benefits, it's essential to acknowledge its limitations:
- Cost
- Resource-Intensive
- Steeper Learning Curve for Advanced Features
- Not Ideal for Large Assemblies
One of the most significant drawbacks of SolidWorks is its cost. The software is priced at a premium, which can be a substantial investment for small businesses, startups, or individual users. The financial commitment includes licensing fees, annual maintenance costs, and potential upgrade expenses. This cost factor might make it challenging for budget-constrained entities to fully embrace the software.
Complex designs, particularly those involving intricate assemblies and high levels of detail, can place significant demands on computational resources. This resource-intensiveness might result in slower performance, rendering times, and responsiveness. Users with limited hardware capabilities could face challenges in working with large and intricate designs efficiently.
While SolidWorks prides itself on its user-friendly interface, mastering its more advanced features can require a considerable investment of time and effort. Functions like simulation, surface modeling, and intricate assemblies might necessitate a steeper learning curve. Users must invest in training and practice to harness the software's full potential.
While SolidWorks performs admirably with most assembly sizes, handling extremely large assemblies can be a daunting task. The software might experience performance bottlenecks when dealing with assemblies that contain a vast number of components, impacting both design speed and overall user experience.
Comparing with AutoCAD
AutoCAD, developed by Autodesk, is a pioneering CAD software renowned for its proficiency in 2D drafting. Widely embraced in the architectural and mechanical design industries, AutoCAD presents a distinctive set of advantages and drawbacks that differentiate it from its counterparts.
Pros of AutoCAD
- 2D Drafting Prowess: AutoCAD's foundation is its exceptional capability in 2D drafting. The software equips users with a comprehensive toolkit for crafting precise and intricate 2D drawings. From creating detailed floor plans to schematic diagrams, AutoCAD empowers designers to communicate their ideas with accuracy and finesse.
- Industry Standard: AutoCAD has cemented its status as an industry standard, cultivating a broad acceptance of its design files across diverse fields. This compatibility facilitates seamless collaboration and communication, as design professionals across domains can easily interpret and work with AutoCAD drawings.
- Customization: AutoCAD's flexibility extends to customization. The software allows users to generate custom commands, routines, and scripts through AutoLISP. This scripting capability empowers users to automate repetitive tasks, boosting productivity and efficiency.
- Diverse Applications: AutoCAD's versatility transcends industries. While it excels in architecture and mechanical design, its applicability extends to fashion, interior design, electronics, and more. This adaptability makes AutoCAD a go-to solution for a wide range of design tasks.
Cons of AutoCAD
- Limited 3D Capabilities: While AutoCAD has incorporated 3D capabilities, they are not as robust as those found in dedicated 3D modeling software like SolidWorks. Complex 3D designs might be more challenging to execute in AutoCAD.
- Steep Learning Curve: Proficiency in AutoCAD, particularly in executing complex 3D tasks, often requires an investment of time and effort. The software's expansive features and intricacies contribute to a potentially steep learning curve, especially for newcomers.
- Separate Modules for Specialized Tasks: Advanced functionalities within AutoCAD may necessitate separate modules or verticals. This approach can increase the software's overall cost and complexity, as users might need to acquire additional modules tailored to specific tasks.
- Less Intuitive 3D Workflow: AutoCAD's 3D modeling workflow might feel less intuitive compared to specialized 3D modeling software like SolidWorks. Designers well-versed in traditional 2D drafting might find the transition to complex 3D designs less seamless within the AutoCAD environment.
Comparing with Fusion 360
Autodesk Fusion 360 has gained traction in the CAD landscape due to its integrated approach to design, simulation, and collaboration. As a cloud-based CAD/CAM tool, Fusion 360 offers a unique set of advantages and challenges that set it apart from other CAD software options.
Pros of Fusion 360
- Integrated Design Environment: Fusion 360 presents a cohesive platform that seamlessly integrates design, simulation, and collaboration features. This integration fosters a fluid transition between different stages of product development, allowing designers to explore ideas, simulate their performance, and iterate designs efficiently.
- Cloud Collaboration: The cloud-based nature of Fusion 360 enables real-time collaboration among team members, regardless of their geographical locations. Multiple users can simultaneously work on a design, view changes in real time, and provide feedback, enhancing team collaboration and reducing delays.
- Parametric and Direct Modeling: Fusion 360 offers both parametric and direct modeling approaches. This versatility grants users the freedom to choose the modeling method that best suits their design workflow. Parametric modeling provides associativity between design elements, while direct modeling allows for more flexible and intuitive adjustments.
- Affordability: Fusion 360 employs a subscription model, making it more accessible to startups, small businesses, and individual users. This pricing structure minimizes upfront costs and enables users to access a robust suite of design tools without a substantial initial investment.
Cons of Fusion 360
- Reliance on Internet Connection: Fusion 360's cloud-based architecture mandates a stable internet connection for seamless access to design files and collaboration features. In scenarios where internet connectivity is compromised, users might face limitations in accessing their work.
- Performance for Large Assemblies: Similar to other cloud-based tools, Fusion 360 can encounter performance issues when handling large assemblies or intricate simulations. This limitation might affect the efficiency of design exploration and analysis for complex projects.
- Learning Curve for Advanced Features: While Fusion 360 aims to be user-friendly, mastering its more advanced features could still pose a learning curve. Designers seeking to harness the full potential of the software's simulation and CAM capabilities might need to invest time in learning and training.
- Data Security Concerns: Storing design data in the cloud introduces data security and intellectual property concerns for some users. Organizations that handle sensitive or proprietary designs might be cautious about entrusting their data to cloud-based platforms.
Comparing with CATIA
CATIA, developed by Dassault Systèmes, stands as a pinnacle of CAD software, renowned for its intricate capabilities in industries demanding precision, complexity, and innovation. Let's explore the unique benefits and challenges that CATIA brings to the table.
Pros of CATIA
- Advanced Surface Modeling: CATIA excels in the creation of complex and high-quality surfaces. This proficiency is particularly advantageous for industries that prioritize aesthetic design, such as aerospace and automotive. CATIA empowers designers to craft intricate and visually appealing surfaces with precision.
- Large Assembly Handling: CATIA's prowess extends to handling massive assemblies and intricate designs. This capability is crucial for industries where products comprise a multitude of intricate components that need to be seamlessly integrated into the final design.
- Industry-Specific Modules: CATIA offers specialized modules tailored to specific industries, such as aerospace and automotive. These industry-specific tools provide targeted features and functionalities that align with the unique demands of these sectors, enhancing design efficiency and accuracy.
- Collaborative Design: CATIA supports collaborative design and concurrent engineering, enabling multiple users to work on the same project simultaneously. This capability streamlines the design process, reduces lead times, and fosters effective cross-functional collaboration.
Cons of CATIA
- High Cost: CATIA's advanced features and specialized modules contribute to a high price point. While the investment might be justifiable for large enterprises in aerospace or automotive, it could prove financially burdensome for smaller businesses and startups.
- Steep Learning Curve: The extensive feature set and advanced capabilities of CATIA translate into a steeper learning curve. Proficiency in using CATIA's intricate tools requires dedication, training, and a significant time investment.
- Resource Intensive: Similar to SolidWorks, CATIA can be resource-intensive, demanding powerful hardware for optimal performance. This requirement might present a challenge for users with limited computing capabilities.
- Less Suitable for 2D Drafting: While CATIA does offer 2D drafting capabilities, it is not as refined in this aspect as software explicitly designed for 2D tasks, like AutoCAD. Users primarily focused on 2D drafting might find CATIA's capabilities less intuitive and efficient.
Conclusion
In the realm of CAD software, SolidWorks stands as a versatile and powerful tool that's well-suited for a wide range of design tasks. However, it's crucial to understand that other CAD software options exist, each catering to specific needs and industries. AutoCAD excels in 2D drafting, Fusion 360 offers cloud-based collaboration, CATIA targets advanced industrial design, and each has its unique set of strengths and limitations. Choosing the right CAD software depends on factors like the nature of your projects, industry requirements, budget, and your own proficiency. While SolidWorks shines with its parametric modeling capabilities and robust simulation tools, it's essential to evaluate your individual requirements and objectives carefully. By considering these factors, you can make an informed decision to select the CAD software that best aligns with your specific needs and maximizes your design efficiency. Remember, the choice of CAD software can significantly impact your productivity and the quality of your work, so thorough research and consideration are key to making the right decision for your design endeavors.