- 1. Selecting Geometries: The Selection Manager
- Basic Selection Methods
- Advanced Selection Methods
- 2. Multiple Body Concepts
- Creating Multiple Bodies
- Editing Multiple Bodies
- Using the Combine Tool
- 3. Creating References: Points, Axes, and Coordinates
- Creating Reference Points
- Generating Reference Axes
- Working with Coordinates
- 4. Creating Curves
- Split Curve
- Project Curve
- Composite Curve
- Curve Through Points
- Helix and Spiral
- Conclusion
SolidWorks is a powerful 3D CAD software widely used by engineers, designers, and students for creating complex 3D models. In this blog post, we will delve into two critical aspects of SolidWorks - selecting geometries using the Selection Manager and working with curves. These are essential skills for anyone looking to become proficient in SolidWorks, whether you're a student working on assignments or a professional tackling real-world projects. If you need help to complete your SolidWorks assignment, we are here to provide the assistance you require.
1. Selecting Geometries: The Selection Manager
The Selection Manager is a central component of SolidWorks that significantly influences your modeling experience. It acts as your gateway to interact with the elements of your 3D model. Here, we'll expand on the importance and utility of the Selection Manager and its basic and advanced selection methods.
Basic Selection Methods
Understanding and efficiently utilizing the basic selection methods is the first step in harnessing the power of the Selection Manager. These methods allow you to precisely choose the entities you wish to work with:
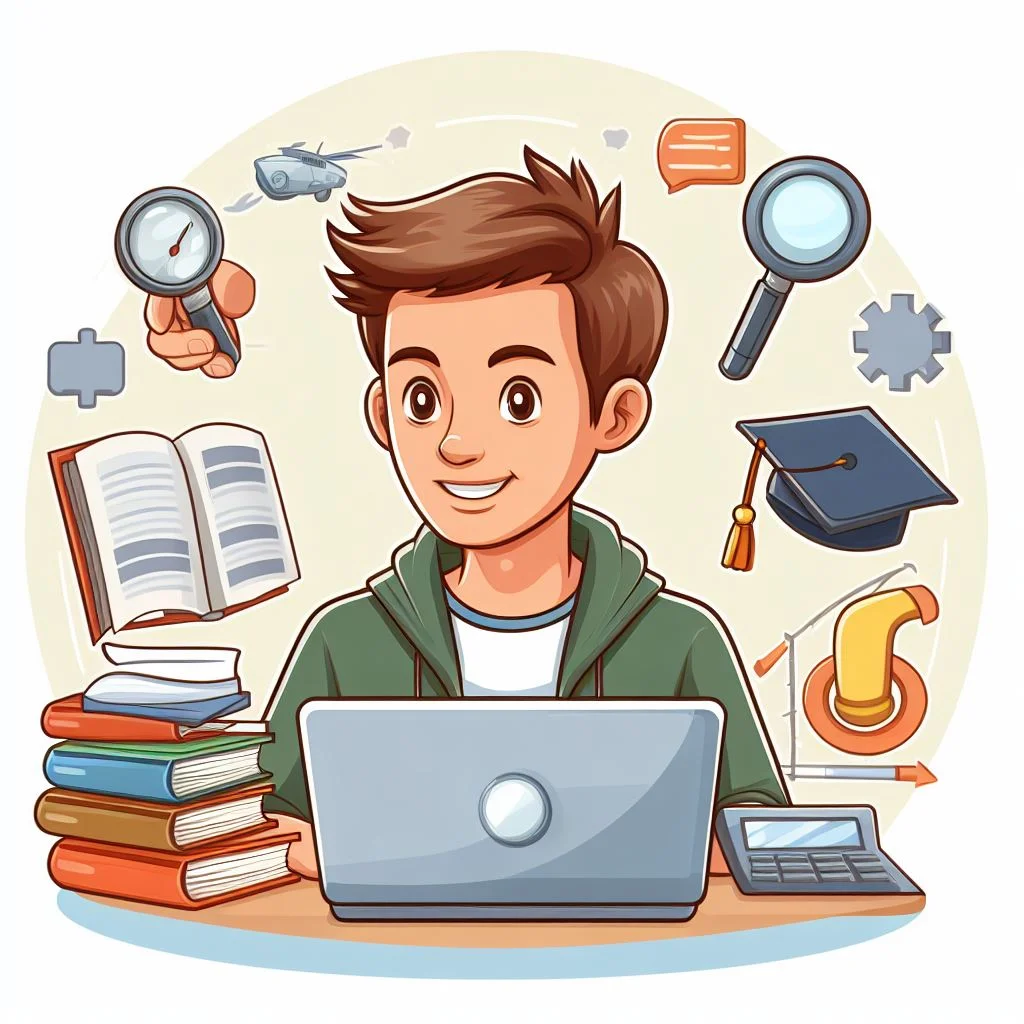
- Single Selection: Single selection is the most straightforward way to choose individual entities within your model. By clicking on a line, edge, face, or body, you select it for editing or manipulation.
- Box Selection: Box selection simplifies the process of selecting multiple entities at once. Click and drag your cursor to draw a rectangular box around the elements you want to select. All entities within the box will be chosen, saving you time and effort.
- Lasso Selection: Lasso selection provides a more freeform approach to selecting entities. You can draw a custom shape around the elements you want to choose. It's especially useful when you need to pick entities that aren't aligned with a rectangular or circular pattern.
- Select All: The "Select All" option, as the name suggests, selects every entity in your model. This is useful when you need to apply a modification or operation to the entire model, such as scaling or rotating the entire assembly.
Advanced Selection Methods
SolidWorks offers more advanced selection techniques that can greatly enhance your modeling efficiency and precision:
- Selection Filters: Selection filters allow you to focus on specific entity types within your model, like faces, edges, vertices, or even components. This is immensely valuable when you're dealing with complex assemblies or intricate models. By filtering your selection, you can avoid inadvertently selecting the wrong entities and ensure you're working on the right parts.
- Selection Sets: Selection sets enable you to save and manage selections for easy access later. This is especially useful when working on large assemblies with many components. You can create sets for commonly used selections and quickly switch between them, reducing the need to reselect items every time you switch tasks.
- Select Other: The "Select Other" tool is handy for selecting entities that may be hidden behind or inside other geometry. It's a time-saving feature that prevents you from needing to hide or suppress parts of your model to access hard-to-reach entities. SolidWorks intelligently detects the entities you might want to select, making it easier to work with complex and layered designs.
- Invert Selection: The "Invert Selection" option is an efficient way to switch your selection from what's chosen to what's unselected and vice versa. This can save you time and clicks when working with complex assemblies, as you don't need to deselect multiple items manually.
Understanding these advanced selection methods and becoming proficient in their use is essential for a productive SolidWorks experience. They streamline your workflow, improve precision, and make working with complex models significantly more manageable.
The Selection Manager in SolidWorks is not merely a tool for picking elements in your 3D model. It's a multifaceted resource that, when used effectively, can greatly enhance your modeling capabilities. By mastering both the basic and advanced selection methods, you'll be well-equipped to tackle intricate design projects with confidence and precision.
2. Multiple Body Concepts
In SolidWorks, a part or assembly can consist of multiple bodies. This is a powerful feature that allows you to create complex designs efficiently. Understanding how to work with multiple bodies is essential, especially when dealing with intricate assemblies or multi-part designs. Here's what you need to know:
Creating Multiple Bodies
Creating multiple bodies within a single part file is the first step in utilizing this powerful feature. Here's how to do it:
- Start with a Base Feature: Begin by defining your base feature, which serves as the initial body for your part. This base feature could be an extrusion, revolve, or any other feature that defines the fundamental shape of your part.
- Add New Bodies: After establishing the base feature, you can add new bodies using various features such as extrusions, cuts, lofts, sweeps, and more. Each new feature you create can generate additional bodies within the same part. These bodies can be completely separate or interconnected, depending on your design requirements.
- Define Materials: It's important to understand that each body can have its own material properties. You can specify whether the bodies share the same material or have unique materials. This is especially useful in scenarios where different components of your design are made of different materials, as it allows for accurate mass properties calculations and material assignment.
Creating multiple bodies in a single part file offers tremendous flexibility. It simplifies the management of complex designs and makes it easier to modify and analyze individual components within your model.
Editing Multiple Bodies
Once you have multiple bodies in your part, you may need to make changes to individual bodies. This could involve applying different features, materials, or appearances to different parts of your model. Here's how to edit multiple bodies:
- Isolate and Select: To edit a specific body, you need to isolate it from the others. You can do this by hiding or suppressing the bodies you don't want to edit, leaving only the desired body visible. Then, select the body you want to modify.
- Edit Features: You can now make changes to the selected body. This could involve adding or modifying features like fillets, chamfers, cuts, or anything else that's part of your design. The changes you make will only affect the currently selected body.
- Repeat as Needed: To edit other bodies within the same part, repeat the process by selecting and isolating the body you want to modify. This allows you to fine-tune each component of your design separately.
Editing multiple bodies within a single part file is a powerful capability that streamlines the design process and simplifies the management of complex parts or assemblies. It ensures that each component of your design is precisely tailored to its specific requirements.
Using the Combine Tool
The Combine tool in SolidWorks is a versatile feature that allows you to perform various operations on multiple bodies within a part or assembly. These operations include adding, subtracting, and intersecting bodies. Here's how to use it:
- Access the Combine Tool: To use the Combine tool, go to the "Insert" menu and select "Features." Then, choose "Combine." This opens the Combine tool dialog box.
- Select Bodies: In the Combine tool dialog, select the bodies you want to combine. You can choose the operation you want to perform (add, subtract, or intersect) and specify the target body.
- Review the Result: Once you've applied the Combine tool, SolidWorks will perform the selected operation on the chosen bodies, creating a new body as a result. This new body represents the outcome of the operation you specified.
The Combine tool is particularly valuable when working with assemblies or creating complex shapes. For example, you can use it to add components together to represent an assembly, subtract material to create voids, or intersect bodies to find the shared space between components.
Understanding how to work with multiple bodies in SolidWorks is vital for tackling complex design projects. By creating, editing, and combining bodies, you can efficiently manage and modify your 3D models, making the software a versatile tool for handling intricate assemblies and multi-part designs. Mastering these concepts empowers you to bring your innovative ideas to life with precision and efficiency.
3. Creating References: Points, Axes, and Coordinates
Precise modeling in SolidWorks often relies on creating and utilizing reference geometry. Points, axes, and coordinates are fundamental references that can help you accurately position and relate different components within your 3D model.
Creating Reference Points
Reference points are essential for marking specific locations in your model. To create them:
- Go to the Reference Geometry dropdown menu and select "Point."
- Place the point where you need it in your model.
Reference points can serve as anchor points, making it easier to position and align other features.
Generating Reference Axes
Axes help define direction and orientation within your model. To create reference axes:
- Go to the Reference Geometry dropdown menu and select "Axis."
- Select two reference points, and the axis will pass through them.
Reference axes are useful for creating rotational features or establishing symmetry.
Working with Coordinates
Coordinates are a more advanced reference system in SolidWorks, allowing you to precisely position and align components. They are often used when importing models or for complex assemblies. Here's how to use them:
- Define your coordinate system by selecting three points that determine its origin and orientation.
- Once your coordinate system is established, you can easily position parts or features using the defined coordinates.
4. Creating Curves
Curves are the building blocks of many 3D models. SolidWorks offers a variety of tools to create curves, each with its specific use case. Let's explore some of the most common curve creation tools:
Split Curve
The Split Curve tool allows you to divide a curve into segments. This is useful for creating different features or modifying existing ones.
Project Curve
The Project Curve tool is used to project an existing curve onto a surface or plane. This is handy for creating new curves based on the contours of an existing model.
Composite Curve
A Composite Curve is a combination of multiple curves, allowing you to create complex shapes or paths for your models. This is particularly useful in surface modeling.
Curve Through Points
Curve Through Points enables you to create a curve that passes through specific points. It's excellent for defining precise paths for features like sweeps and lofts.
Helix and Spiral
Helix and Spiral are specialized curve creation tools. Helix is used to create 3D helical curves, while Spiral generates curves that follow a twisting path. These are invaluable for creating thread profiles, springs, or any design with a helical component.
Conclusion
Mastering SolidWorks is a rewarding journey, and understanding the essentials of geometry selection, working with multiple bodies, creating reference geometry, and generating curves is paramount to your success. Whether you're a student working on assignments or a professional designing intricate models, the knowledge and skills covered in this blog will undoubtedly elevate your SolidWorks proficiency. So, roll up your sleeves, open SolidWorks, and start creating amazing 3D models with confidence and precision.