- Understanding SolidWorks: A Primer
- Creating 3D Models with SolidWorks
- Parametric Design: The Power of Flexibility
- Simulation and Analysis in SolidWorks
- Collaborative Design: Bridging the Gap
- Integrating SolidWorks with Other Tools and Systems
- Future Trends: What Lies Ahead for SolidWorks?
- Conclusion:
In the ever-evolving landscape of engineering and design, SolidWorks stands tall as a powerhouse for creating and analyzing intricate mechanical systems. This Computer-Aided Design (CAD) software has become a cornerstone for engineers, providing a robust platform to bring innovative ideas to life. In this comprehensive blog, we delve into the nuances of designing and analyzing mechanical systems with SolidWorks, exploring its features, applications, and the transformative impact it has on the field.
SolidWorks, with its intuitive and user-friendly interface, has redefined the design process, making it accessible to both seasoned engineers and newcomers to the field. The software's parametric design capabilities empower users to capture design intent and make changes easily, fostering a dynamic and iterative approach to creating 3D models. As engineers sketch their initial ideas and refine them through various stages, SolidWorks becomes not just a tool but a collaborator in turning concepts into tangible and functional designs.
One of the standout features of SolidWorks is its parametric design, offering unparalleled flexibility in the design process. This dynamic approach allows engineers to make modifications at any stage without the need to start from scratch. This not only accelerates the design iteration process but also encourages creative exploration, as designers can quickly test different concepts and ideas, refining them until the optimal solution is achieved. The adaptability afforded by parametric design positions SolidWorks as a versatile and indispensable tool in the engineer's toolkit.
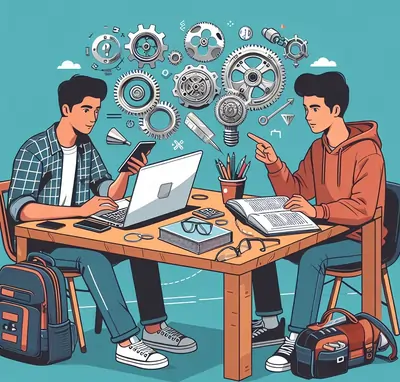
Simulation and analysis are integral components of any mechanical system design, and SolidWorks excels in this domain. The software's simulation capabilities enable engineers to predict and optimize the performance of their designs under various conditions, making it an ideal tool to solve your SolidWorks assignment. By virtually testing the mechanical systems before they are physically built, SolidWorks reduces the need for costly prototypes and ensures that the final product meets the required specifications. The ability to simulate real-world scenarios provides engineers with a comprehensive understanding of how their designs will perform, allowing for informed decision-making throughout the design process.
Collaboration lies at the heart of innovation, and SolidWorks is designed with this principle in mind. The software facilitates seamless teamwork by allowing multiple engineers to work on a project simultaneously. This collaborative design approach not only enhances creativity but also ensures that the collective expertise of a team is leveraged to produce high-quality and thoroughly evaluated designs. SolidWorks transforms the design process from an individual endeavor into a collaborative and synergistic effort, where diverse perspectives contribute to the success of the project.
SolidWorks' integration capabilities further enhance its utility in the engineering landscape. The software seamlessly integrates with a variety of tools and systems, extending its reach into different facets of engineering. Whether connecting with data management systems or interfacing with other design software, SolidWorks adapts to the needs of engineers, creating a cohesive and interconnected design environment. This integration not only streamlines workflows but also allows for a more holistic approach to design, where different aspects of a project are seamlessly woven together.
As engineers continue to push the boundaries of innovation, SolidWorks remains a reliable companion on the journey to shape the future of mechanical design. Its influence is not confined to the present but extends into the exciting possibilities that lie ahead. The integration of artificial intelligence promises to enhance design efficiency, while advancements in virtual reality offer immersive experiences for engineers to interact with their creations. SolidWorks is not merely a tool; it is a dynamic force propelling the world of mechanical design into new dimensions. Its impact is felt in the meticulous details of 3D models, the precision of simulations, and the collaborative synergy of design teams. As the landscape of engineering evolves, SolidWorks stands ready, a steadfast companion on the journey to unlock new frontiers in mechanical design.
Understanding SolidWorks: A Primer
Before delving into the intricacies of designing mechanical systems, it's essential to establish a foundational understanding of SolidWorks. At its core, SolidWorks offers more than just a design tool; it provides an intuitive and user-friendly interface that empowers engineers to navigate the complexities of the software with ease. The learning curve is minimized, allowing both seasoned professionals and aspiring engineers to harness its capabilities efficiently.
The key to SolidWorks' prowess lies in its parametric design capabilities. This feature enables engineers to create models that are not only visually impressive but also adaptable to changes. The parametric nature of SolidWorks means that modifications can be made seamlessly, without the need to start from scratch. This flexibility in design is a game-changer, as it accommodates the iterative nature of the design process, fostering creativity and innovation.
As engineers embark on the journey of designing mechanical systems, SolidWorks serves as a guiding light. The software streamlines the design process, from the initial stages of sketching ideas to the meticulous detailing of 3D models. The user-friendly interface, coupled with parametric design, creates a symbiotic relationship that enhances the efficiency of the design workflow.
In essence, SolidWorks isn't just a tool; it's a gateway to a world where design is not bound by limitations. It's a platform where ideas take shape, evolve, and adapt, ultimately materializing into tangible and functional mechanical systems. The understanding of SolidWorks goes beyond the technical aspects – it embodies a philosophy that champions innovation, collaboration, and the relentless pursuit of engineering excellence. As we navigate the depths of designing with SolidWorks, we embark on a journey that transcends the ordinary, propelling us into a realm where possibilities are limitless, and the future of mechanical design is shaped with precision and creativity.
Creating 3D Models with SolidWorks
SolidWorks, a cornerstone in modern engineering, serves as a dynamic platform that empowers engineers to translate abstract concepts into tangible 3D models. The process of crafting these intricate representations is a captivating journey, starting with the inception of ideas and progressing through a series of meticulous steps.
At the heart of SolidWorks' prowess lies its user-friendly interface, providing engineers with an intuitive canvas to sketch their initial ideas. This phase is akin to an artist's sketchpad, where concepts take shape and form, laying the groundwork for the detailed 3D models that will follow. The software's versatility in accommodating various design approaches ensures that the creative process is not constrained but rather flourishes in an environment that encourages experimentation.
Moving beyond conceptualization, engineers embark on a step-by-step process, breathing life into their ideas. SolidWorks facilitates the transition from 2D sketches to three-dimensional wonders, allowing for the incorporation of intricate details and dimensions. Each component and feature is meticulously crafted, contributing to the overall richness of the model. The software's parametric design capabilities shine at this stage, offering the flexibility to make dynamic changes and refinements, ensuring that the evolving design aligns with the engineer's vision.
In the realm of creating 3D models with SolidWorks, precision is paramount. The software's tools and features provide engineers with the means to achieve the desired level of accuracy, ensuring that the virtual representation mirrors the intricacies of the intended mechanical system. As the design takes shape, SolidWorks becomes more than just a tool; it transforms into a partner in the creative process, guiding engineers through the nuanced art of turning imagination into reality. The result is not just a 3D model; it is a testament to the fusion of innovation, skill, and the boundless possibilities that SolidWorks unlocks for engineers in their quest to redefine mechanical design.
Parametric Design: The Power of Flexibility
In the realm of SolidWorks, the spotlight shines brightly on its distinctive feature—parametric design. This facet unveils an unprecedented level of flexibility in making design modifications, setting SolidWorks apart as a champion of efficiency and creativity in the world of mechanical design.
Parametric modeling within SolidWorks stands as a testament to the software's commitment to empowering engineers throughout the design process. This capability allows for dynamic changes to be seamlessly integrated into the design without the need to initiate the entire process anew. Gone are the days of scrapping entire projects due to minor adjustments; parametric design ensures that modifications can be made swiftly and precisely, preserving the integrity of the overall project.
Engineers find themselves liberated by the power of parametric design, as it encourages a fluid and iterative approach to the creative process. The ability to refine and fine-tune designs without the constraints of rigid starting points fosters an environment where ideas can evolve organically. This flexibility not only saves time but also stimulates innovation, as engineers can experiment with different iterations of their designs, pushing the boundaries of what is possible.
In essence, parametric design within SolidWorks is not just a feature; it is a philosophy that embraces the dynamic nature of the design process. It exemplifies the software's commitment to providing a platform that adapts to the evolving needs of engineers, allowing them to navigate the intricacies of design with unparalleled ease. As we continue our journey through the world of SolidWorks, the significance of parametric design becomes increasingly apparent, weaving itself into the very fabric of a design culture that values efficiency, adaptability, and, above all, boundless creativity.
Simulation and Analysis in SolidWorks
Simulation is undeniably a critical aspect of mechanical system design, and SolidWorks emerges as a stalwart ally in this realm. As engineers embark on the intricate journey of creating mechanical systems, the software's simulation capabilities become a guiding light. SolidWorks provides a virtual testing ground, allowing engineers to predict and optimize the performance of their designs with unparalleled precision before any physical prototype is constructed.
The beauty of SolidWorks' simulation lies in its ability to replicate real-world conditions, offering a comprehensive understanding of how a mechanical system will behave under various scenarios. Engineers can subject their designs to simulated stresses, forces, and environmental factors, gaining insights that go beyond theoretical expectations. This virtual experimentation not only saves valuable time and resources but also empowers engineers to make informed decisions early in the design process.
Optimization becomes a tangible reality through SolidWorks' simulation features. By identifying potential weaknesses or areas for improvement in the virtual realm, engineers can refine their designs iteratively, ensuring that the final product is robust and resilient. This predictive approach to performance evaluation minimizes the need for costly physical prototypes, fostering a more efficient and cost-effective design cycle.
In essence, SolidWorks transforms the traditional paradigm of "design and test" by introducing a powerful "simulate and refine" methodology. The software not only aids engineers in anticipating challenges but also provides the tools to proactively address them. As the engineering landscape continues to demand innovation and efficiency, SolidWorks' simulation capabilities become not just a feature but a cornerstone for success in designing mechanical systems that stand the test of reality.
Collaborative Design: Bridging the Gap
SolidWorks transcends the realm of solitary design, finding its strength in the collaborative synergy it fosters. It stands as a testament to the power of teamwork in the world of mechanical design. The software's architecture is built to facilitate seamless collaboration, providing a virtual space where multiple engineers can converge, contribute, and collectively shape the trajectory of a design project.
In this collaborative ecosystem, engineers find themselves breaking free from the confines of sequential workflows. No longer bound by the limitations of working in isolation, they can concurrently contribute to the design process. This concurrent collaboration not only accelerates the pace of development but also brings a diversity of perspectives into play. Each engineer becomes a crucial piece of the puzzle, contributing their unique insights and expertise to the collective pool of knowledge.
The result is not just a sum of individual efforts but a synergistic creation that reflects the collective intelligence of the design team. SolidWorks acts as a virtual workshop where ideas are shared, refined, and seamlessly integrated into the evolving design. The software's real-time collaboration features transcend geographical boundaries, allowing teams to work together irrespective of their physical locations.
This collaborative ethos extends beyond mere efficiency; it becomes a breeding ground for innovation. The interchange of ideas sparks creativity, and the collective problem-solving mindset becomes a driving force behind overcoming challenges. SolidWorks, in this context, becomes more than a tool; it transforms into a platform that nurtures a culture of shared success, where the achievements of the team eclipse individual contributions.
As we navigate the collaborative landscape of SolidWorks, it becomes evident that the software not only bridges the gap between engineers but also bridges the gap between imagination and realization. It transforms the design process from a solitary endeavor into a collective journey, where each keystroke and modification is a step forward, not just for an individual, but for the entire team working in harmony. SolidWorks, in its essence, is not just a tool for designing mechanical systems; it is a catalyst for the collaborative spirit that propels innovation and excellence in engineering.
Integrating SolidWorks with Other Tools and Systems
SolidWorks seamlessly integrates with a myriad of tools and systems, transforming it into a versatile powerhouse that extends its reach across diverse engineering landscapes. The compatibility of SolidWorks with various third-party applications enhances its capabilities and elevates its functionality to meet the evolving needs of engineers.
By exploring the integration possibilities, engineers can streamline their workflows and achieve heightened efficiency in their design processes. The connectivity of SolidWorks with tools such as data management systems, analysis software, and even manufacturing solutions creates a unified ecosystem where information flows seamlessly. This integration not only saves time but also reduces the likelihood of errors that can occur when transferring data between different platforms.
Furthermore, SolidWorks' compatibility with Computer-Aided Engineering (CAE) tools enables engineers to conduct advanced simulations and analyses, pushing the boundaries of what can be achieved in the virtual realm. This synergy between SolidWorks and complementary tools empowers engineers to tackle complex challenges with a comprehensive and integrated approach.
As we navigate the intricate landscape of modern engineering, the ability to integrate SolidWorks with various tools becomes a strategic advantage. It not only optimizes the design process but also ensures that the final product is a result of a cohesive and collaborative effort. The marriage of SolidWorks with a diverse array of tools exemplifies its adaptability, reinforcing its position as a cornerstone in the ever-expanding toolkit of today's innovative engineers.
Best Practices for Efficient Design Workflow
Efficiency is the heartbeat of successful engineering, and SolidWorks pulsates with a myriad of features dedicated to streamlining the design workflow. Navigating through the expansive toolbox of SolidWorks reveals a treasure trove of best practices that propel the design process towards unprecedented levels of smoothness and productivity.
One of the keystones of efficiency lies in the judicious use of keyboard shortcuts. SolidWorks empowers users to execute commands swiftly, reducing the time spent navigating menus and enhancing the overall speed of the design process. With a shortcut for almost every function, engineers can seamlessly transition from one task to another, maintaining a fluidity that is essential in the dynamic world of mechanical design.
Design libraries within SolidWorks serve as reservoirs of pre-built components and templates. Leveraging these libraries expedites the design phase, eliminating the need to recreate commonly used elements. This not only saves time but also ensures consistency across projects. Engineers can effortlessly access a repository of standardized parts, assemblies, and even entire design templates, fostering a standardized approach that enhances collaboration and reduces the likelihood of errors.
Furthermore, the use of templates in SolidWorks acts as a force multiplier for design efficiency. Creating standardized templates for different projects establishes a cohesive starting point, allowing engineers to dive directly into the unique aspects of each design without the need for repetitive groundwork. This templated approach not only accelerates the initial stages of design but also maintains a level of uniformity in documentation and presentation.
In the realm of efficiency, SolidWorks extends beyond the digital canvas, providing tools and features that empower engineers to work smarter, not harder. The amalgamation of keyboard shortcuts, design libraries, and templates orchestrates a symphony of efficiency, ensuring that the design workflow is not only optimized but also tailored to the unique preferences and requirements of each engineer. SolidWorks stands as a testament to the principle that in the world of design, efficiency is not just a luxury but an indispensable asset that propels innovation forward.
Future Trends: What Lies Ahead for SolidWorks?
Looking ahead, the trajectory of SolidWorks is aligned with the cutting edge of technological advancements in the field of Computer-Aided Design (CAD). As the broader landscape of engineering continues its rapid evolution, SolidWorks is poised to embrace future trends that promise to redefine the way mechanical systems are designed and analyzed.
One of the most anticipated developments on the horizon for SolidWorks is the seamless integration of artificial intelligence (AI). This revolutionary incorporation holds the potential to elevate design processes to unprecedented levels of efficiency and precision. AI algorithms can analyze vast datasets, identify patterns, and provide intelligent insights, empowering engineers with a deeper understanding of their designs and streamlining decision-making processes. The synergy between human ingenuity and machine intelligence is expected to usher in a new era of design capabilities.
Furthermore, SolidWorks is poised to capitalize on the advancements in virtual reality (VR) technology. Enhanced virtual reality experiences within the SolidWorks environment will enable engineers to immerse themselves in their designs, offering a level of interaction and understanding that transcends traditional 3D modeling. Engineers will have the ability to walk through their creations, assess spatial relationships, and make real-time adjustments, fostering a more intuitive and immersive design process.
Conclusion:
In the ever-evolving realm of mechanical design, SolidWorks stands as a beacon of innovation and efficiency, guiding engineers through the intricate process of creating and analyzing mechanical systems. As we conclude our exploration of SolidWorks, it becomes evident that this CAD software has transcended the conventional boundaries of design, becoming a catalyst for transformative advancements in engineering.
SolidWorks, with its user-friendly interface and parametric design capabilities, has redefined the way engineers bring their ideas to life. The journey from conceptualization to a detailed 3D model is not just a series of steps but a dynamic process that encourages creativity and adaptability. The power of parametric design, allowing engineers to make swift modifications without compromising the integrity of the entire project, has revolutionized the landscape of design iteration.
Simulation and analysis form the backbone of any mechanical system, and SolidWorks emerges as a formidable tool in this arena. Engineers can now predict and optimize the performance of their designs, reducing the need for costly physical prototypes and accelerating the development cycle. The software's ability to simulate real-world conditions provides a level of confidence in the design that is unparalleled, ensuring that the final product meets and exceeds expectations.
Collaborative design takes center stage in SolidWorks, fostering teamwork and collective problem-solving. The ability for multiple engineers to work simultaneously on a project, contributing their expertise in real-time, has broken down the barriers of traditional design workflows. This collaborative spirit not only enhances creativity but also results in more robust and thoroughly evaluated designs.
The integration capabilities of SolidWorks amplify its impact, allowing engineers to seamlessly connect with other tools and systems. This interoperability extends the software's reach into various industries, making it a versatile companion for engineers working in diverse fields. From aerospace to automotive, SolidWorks is leaving an indelible mark on the design landscape.
As we look to the future, SolidWorks continues to evolve, embracing new technologies and trends. The integration of artificial intelligence promises to enhance design efficiency, while advancements in virtual reality offer immersive experiences for engineers to interact with their creations. The journey with SolidWorks is not just a snapshot of the present; it is a glimpse into the exciting possibilities that lie ahead for mechanical design.