- Understanding the Interface: Navigating the SolidWorks Environment
- Command Manager Simplified
- Efficient Property Manager Usage
- Modeling Challenges: Tackling Design and Sketching Issues
- Overcoming Sketching Dilemmas
- Addressing Design Modification Issues
- Assembly Problems: Streamlining Multi-Part Designs
- Managing Component Relationships
- Performance Optimization Techniques
- Simulation and Analysis: Resolving Simulation Roadblocks
- Interpreting Simulation Results
- Troubleshooting Simulation Errors
- Drawing and Documentation: Enhancing Communication Skills
- Dimensioning Best Practices
- Generating Bill of Materials (BOM) Efficiently
- Conclusion
SolidWorks, a formidable 3D computer-aided design (CAD) software, stands as a cornerstone in the realms of design and engineering across diverse industries. Its versatile capabilities make it a go-to tool for architects, engineers, and product designers aiming to transform their imaginative concepts into tangible, three-dimensional realities. However, despite its prominence and functionality, students frequently find themselves navigating a labyrinth of challenges when immersing themselves in the world of SolidWorks.
Learning and effectively utilizing SolidWorks often become a journey of trial and error for students. The software's robust features and intricate interface can be initially overwhelming. The command manager, property manager, and various toolbars create a visual symphony that, at first glance, might seem complex. Navigating through this symphony becomes an art that requires practice and understanding. To ease this initial hurdle, customization becomes the ally of the student. Personalizing the command manager to align with one's workflow preferences and embracing keyboard shortcuts for frequently used tools can significantly enhance the user experience.
Moving beyond the interface challenges, the core of SolidWorks lies in its modeling capabilities. The transition from a conceptual sketch to a tangible 3D model demands a comprehensive understanding of design principles and sketching techniques. Sketching, being the foundation of 3D modeling, requires precision and attention to detail. Ensuring accurate sketch plane selection and employing geometric relations to maintain the integrity of the sketch are pivotal in overcoming initial sketching dilemmas. To solve your 3D Modeling assignment successfully, it is crucial to master these fundamental aspects of SolidWorks.
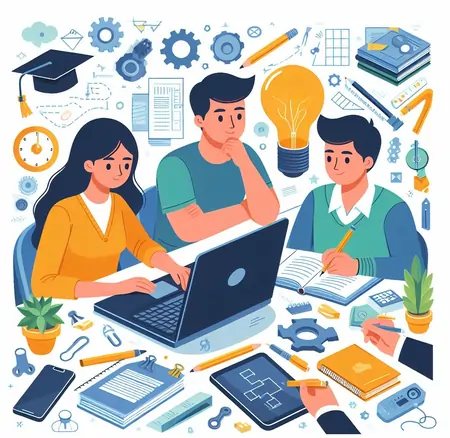
As students progress in their SolidWorks journey, they encounter the complexities of assembly. Managing relationships between multiple components and optimizing performance in large assemblies become crucial skills. The use of mates to define relationships between components and the strategic employment of the "Assembly Visualization" tool can streamline the assembly process. Additionally, addressing performance issues involves simplifying complex assemblies and utilizing configurations to create variations without duplicating data, ensuring a smoother workflow.
SolidWorks extends its utility beyond mere design; it allows students to validate their designs through simulation and analysis. However, understanding and interpreting simulation results pose challenges. The ability to troubleshoot common simulation errors and validate material properties for accurate simulations are skills that students must hone to make the most of this powerful feature.
When it comes to documenting and communicating designs effectively, SolidWorks plays a pivotal role. Creating detailed drawings and generating accurate bills of materials (BOM) are essential communication skills for engineers. Dimensioning, following industry standards, and leveraging tools like the "Fully Define Sketch" are paramount in creating clear and unambiguous drawings. Customizing BOM templates and ensuring accurate part numbering further contribute to effective communication within a design team.
Understanding the Interface: Navigating the SolidWorks Environment
SolidWorks, with its comprehensive set of features, can be a bit daunting for students stepping into the realm of 3D design. The interface, with its various tools and managers, serves as the gateway to unleashing the software's full potential. While it may seem overwhelming at first, mastering the SolidWorks interface is fundamental for a fluid design experience.
To begin with, the Command Manager stands as a command hub, offering a plethora of tools neatly categorized for easy access. Customizing this manager to align with your workflow can significantly enhance efficiency. Consider assigning keyboard shortcuts to frequently used tools, providing swift access and reducing the reliance on menu navigation.
The Property Manager is another cornerstone of the SolidWorks interface, providing contextual options based on the selected feature. Understanding how to efficiently use this manager can streamline the design process. Right-clicking on features for context-sensitive options adds a layer of convenience, allowing for quick edits without delving deep into menus.
Navigating SolidWorks seamlessly involves a blend of customization and familiarity. As you delve into projects, experimenting with different interface layouts and adapting it to your unique workflow will gradually transform the initially overwhelming interface into a tool that amplifies your design capabilities. Embrace the learning curve, and soon the SolidWorks interface will become your canvas for turning imagination into precision.
Command Manager Simplified
Mastering the SolidWorks interface is a pivotal step in a student's journey. To streamline your workflow, consider customizing the Command Manager. This allows you to arrange tools based on your preferences, ensuring quick access to frequently used commands. Additionally, harness the power of keyboard shortcuts for a more efficient design process. By mapping shortcuts to commonly used tools, you can significantly reduce the time spent navigating menus, enhancing your overall productivity within the software.
Efficient Property Manager Usage
The Property Manager in SolidWorks is a versatile tool for making swift edits to your design. To navigate it effectively, hone the skill of seamlessly moving between its tabs for specific modifications. Mastering context-sensitive right-click options provides an additional layer of efficiency. By right-clicking on entities, features, or the graphics area, you unlock a toolbox of quick actions tailored to the context, empowering you to make edits without unnecessary navigation. This dexterity in property manager usage proves invaluable in maintaining a fluid and uninterrupted design flow.
Modeling Challenges: Tackling Design and Sketching Issues
Creating 3D models involves intricate design and sketching, where students encounter hurdles in transforming abstract concepts into tangible, well-structured models. One prevalent issue revolves around maintaining sketch integrity throughout the design process. To overcome this, it's crucial for students to meticulously select the appropriate sketch plane and utilize geometric relations effectively. By ensuring accurate sketch plane selection and employing geometric relations, students can lay a solid foundation for their models, minimizing the risk of errors and inconsistencies.
Another key challenge lies in addressing design modification issues. As students progress through the design stages, they often need to make adjustments to their models. The "Rollback Bar" proves to be a valuable tool in this scenario, allowing users to revisit and modify specific features without disrupting the entire design sequence. Understanding the implications of design changes on related features is equally important, ensuring that modifications seamlessly integrate into the overall model without causing unintended consequences.
In essence, by mastering these sketching and design principles, students can navigate the intricacies of SolidWorks modeling with confidence and precision. These foundational skills not only contribute to the creation of accurate and aesthetically pleasing 3D models but also serve as a cornerstone for advanced design and engineering endeavors.
Overcoming Sketching Dilemmas
Sketching is the foundation of any SolidWorks design, and accuracy in sketching is paramount. To overcome sketching dilemmas, students should pay meticulous attention to sketch plane selection. Ensuring the correct sketch plane is chosen lays the groundwork for a solid design. Additionally, utilizing geometric relations is key to maintaining sketch integrity. Employing constraints like parallel, perpendicular, and concentric ensures that the sketch behaves as intended, minimizing unexpected distortions and simplifying the overall design process.
Addressing Design Modification Issues
The design process is iterative, and modifications are inevitable. To facilitate design changes seamlessly, students can make effective use of the "Rollback Bar." This feature allows users to roll back the model's history, making it easier to identify and modify specific features. Understanding the implications of design changes on related features is equally important. Modifying one feature may affect others in the design.
Assembly Problems: Streamlining Multi-Part Designs
Working with assemblies introduces a new set of challenges, especially when dealing with multiple components. Assemblies, while powerful for representing complex structures, can become intricate to manage. One significant issue that students often encounter is the delicate task of maintaining relationships between components.
Ensuring that every part fits seamlessly into the assembly and moves as intended is critical. One effective solution is to meticulously define and manage component relationships through mates. Mates serve as the virtual connections between parts, dictating their relative positions, angles, and alignments. By using mates judiciously, students can create a stable assembly that accurately reflects their design intent.
Additionally, the "Assembly Visualization" tool proves invaluable for gaining a comprehensive overview of the assembly structure. This tool enables users to evaluate the mass, volume, and quantity of components, aiding in the identification of bottlenecks or components that may require simplification for optimal performance.
By mastering these assembly management techniques, students can streamline their multi-part designs, ensuring efficient workflows and robust representations of intricate engineering assemblies. This approach not only enhances the design process but also lays the foundation for successful collaboration and effective communication within a team of engineers or stakeholders.
Managing Component Relationships
Successfully managing component relationships is crucial for a well-organized assembly. Using mates effectively is not just about placing components in the right position but ensuring they interact seamlessly. Mates define how parts move, rotate, and relate to each other. For instance, when creating an assembly, applying coincident and concentric mates accurately aligns components, establishing a strong foundation for the entire design. It's essential to understand the various mate types available in SolidWorks and apply them judiciously to achieve the desired results.
Additionally, the "Assembly Visualization" tool emerges as a powerful ally in gaining a comprehensive overview of your assembly. This tool provides a visual representation of the assembly's structure, making it easier to identify relationships, spot errors, and optimize the arrangement of components. By color-coding components based on criteria such as mass or custom properties, Assembly Visualization enhances efficiency in managing complex assemblies.
Performance Optimization Techniques
Optimizing the performance of assemblies is a common concern, especially when dealing with intricate designs. Simplifying complex assemblies is a key strategy to improve responsiveness and speed during modeling. This involves removing unnecessary details or creating simplified representations of parts, reducing computational load without compromising the overall design integrity.
Furthermore, utilizing configurations proves invaluable in managing variations without duplicating data. By creating different configurations for parts or assemblies, you can explore design alternatives without creating multiple files. Configurations allow for quick comparisons and facilitate the development of parametric designs, enhancing flexibility in adapting to changing project requirements. These performance optimization techniques not only streamline the design process but also contribute to a more efficient and responsive SolidWorks experience.
Simulation and Analysis: Resolving Simulation Roadblocks
SolidWorks Simulation is a powerful tool that empowers students to virtually test and analyze their designs, providing valuable insights into their structural and dynamic behavior. Despite its robust capabilities, students may encounter roadblocks that can impede the simulation and analysis process.
One common challenge is understanding and interpreting simulation results accurately. It is essential for students to delve into the intricacies of result interpretation, recognizing key indicators that reflect the structural integrity and performance of their designs. The "Trend Tracker" tool can be particularly beneficial in visualizing and comparing design changes across multiple iterations, aiding in the refinement of models.
Additionally, troubleshooting simulation errors is a crucial skill for students working with SolidWorks Simulation. Errors can range from meshing problems to convergence issues, and knowing how to identify and resolve these issues is paramount. Verifying material properties is another essential step, ensuring that the simulation accurately reflects the real-world behavior of materials used in the design.
By mastering the nuances of simulation and analysis, students not only enhance their problem-solving skills but also gain a deeper understanding of how their designs will perform in real-world scenarios. This proficiency is invaluable in the field of engineering, where accurate simulations play a pivotal role in ensuring the success and reliability of designs.
Interpreting Simulation Results
Interpreting simulation results is a critical aspect of utilizing SolidWorks effectively for design validation. To master result interpretation, students should delve into the details provided by the simulation reports. Understanding stress distributions, displacement patterns, and factor of safety values allows for a comprehensive analysis of the model's behavior under different conditions. Additionally, exploring the "Trend Tracker" feature enhances the analytical process by visually representing design changes over multiple iterations. This tool provides insights into how alterations impact the overall performance, enabling students to refine and optimize their designs with precision.
Troubleshooting Simulation Errors
Simulation errors can be stumbling blocks in the design validation process. It's essential for students to develop a keen understanding of common errors and their resolutions. Whether it's mesh-related issues, boundary condition conflicts, or convergence problems, a systematic approach to troubleshooting is crucial. Validating material properties is another key aspect to ensure accurate simulations. Confirming that material data is correctly assigned to components helps in achieving reliable and realistic results. By addressing these aspects, students can navigate through simulation challenges, ensuring their analyses are not only accurate but also reflective of real-world scenarios.
Drawing and Documentation: Enhancing Communication Skills
The ability to create detailed and accurate drawings is crucial for effective communication in engineering. Let's explore solutions for common challenges in drawing and documentation.
Students often encounter difficulties in presenting their designs clearly on paper or in digital formats. One common issue revolves around dimensioning practices. It's essential to adhere to industry-standard dimensioning practices to ensure that the drawings convey accurate information. By following these practices, students can eliminate ambiguity and enhance the overall clarity of their designs.
Furthermore, the "Fully Define Sketch" tool proves invaluable in addressing sketch-related challenges. This tool assists in avoiding ambiguous sketches by automatically adding the necessary dimensions and geometric constraints. By incorporating these solutions into their drawing and documentation practices, students can significantly improve their communication skills in the field of engineering.
Dimensioning Best Practices
Proper dimensioning is paramount for conveying design intent accurately. By adhering to industry-standard practices, students can enhance the clarity of their drawings. Precision is achieved by carefully placing dimensions, avoiding clutter, and ensuring consistency throughout the design. Additionally, utilizing the "Fully Define Sketch" tool proves instrumental in eliminating ambiguity in sketches. This tool automatically adds dimensions and geometric constraints, leaving no room for interpretation. Embracing these dimensioning best practices not only fosters effective communication but also streamlines the manufacturing process by providing clear instructions for production.
Generating Bill of Materials (BOM) Efficiently
Efficient BOM generation is vital for project management and production workflows. To tailor BOMs to specific project requirements, students should explore template customization. This involves selecting relevant properties, organizing information logically, and presenting it in a format that aligns with project specifications. Furthermore, meticulous attention to accurate part numbering and naming conventions ensures seamless collaboration and reduces errors in the manufacturing process. Mastering the art of generating BOMs efficiently contributes to overall project success and facilitates a smoother transition from design to production.
Conclusion
In conclusion, navigating the intricate landscape of SolidWorks is undoubtedly a journey filled with challenges, but armed with the right knowledge and strategies, students can transform these obstacles into stepping stones toward mastering the art of 3D design. The multifaceted interface, with its command and property managers, may seem daunting initially, but by customizing the command manager and leveraging keyboard shortcuts, students can tailor their workspace to suit their workflow, fostering a more intuitive and efficient design process.
As students venture into the realm of modeling, sketching issues often surface. Precision in sketching is paramount, and mastering sketch plane selection and the use of geometric relations ensures the integrity of their designs. When modifications are required, the "Rollback Bar" becomes a valuable ally, offering a visual timeline of design changes and facilitating seamless adjustments.
Assemblies introduce a new layer of complexity, demanding a keen understanding of component relationships and performance optimization techniques. Mates play a pivotal role in defining these relationships, while the "Assembly Visualization" tool provides a comprehensive overview of the entire assembly. Performance optimization, achieved through simplifying complex assemblies and utilizing configurations, ensures a smooth design experience even in intricate multi-part projects.
SolidWorks Simulation empowers students to validate their designs virtually, but interpreting simulation results and troubleshooting errors can be challenging. The "Trend Tracker" becomes a valuable aid in visualizing design changes over iterations, enhancing the iterative process. Furthermore, a thorough understanding of common simulation errors and meticulous validation of material properties contribute to accurate and reliable simulations.
Effective communication in engineering hinges on proficient drawing and documentation skills. Adhering to dimensioning best practices and utilizing tools like the "Fully Define Sketch" feature ensures clarity and precision in drawings. Generating Bill of Materials (BOM) efficiently, with customized templates and adherence to naming conventions, further enhances the communicative power of design documentation.
In essence, the journey through SolidWorks troubleshooting unveils not only the technical aspects of the software but also the iterative and problem-solving nature of the design process itself. Each challenge presents an opportunity for growth, pushing students to think critically, analyze results, and refine their designs. The solutions provided here serve as a roadmap, guiding students through the intricacies of SolidWorks and empowering them to overcome challenges with confidence. As they continue on their design endeavors, these newfound skills will undoubtedly contribute to their success in the dynamic and innovative world of 3D design and engineering.