- Understanding Fluid Flow Simulation
- Setting Up Fluid Flow Simulation
- Solving Fluid Flow Problems
- Analyzing Results and Extracting Insights
- Applications of Fluid Flow Simulation in Assignments
- Mechanical Engineering Assignments
- Aerospace Engineering Assignments
- Civil Engineering Assignments
- Biomedical Engineering Assignments
- Advantages of Using SolidWorks for Fluid Flow Simulation
- Seamless Integration with CAD Models
- User-Friendly Interface
- Robust Solver Technology
- Extensive Material Database
- Tips for Success in Fluid Flow Simulation with SolidWorks
- Validate Simulations with Experimental Data
- Utilize Adaptive Meshing
- Explore Different Boundary Conditions
- Collaborate and Seek Feedback
- Conclusion
Fluid flow simulation in SolidWorks is a powerful tool that allows engineers and designers to gain valuable insights into the behavior of liquids and gases in their designs. Whether you are working on assignments related to mechanical engineering, aerospace, or any other field that involves fluid dynamics, understanding how to utilize SolidWorks for fluid flow analysis can greatly enhance the quality of your projects. Whether you require assistance with your finite element analysis assignment or simply seek to enhance your proficiency in fluid flow simulation using SolidWorks, mastering this tool is essential for success in various engineering disciplines.
SolidWorks' fluid flow simulation module is a game-changer in the realm of engineering and design. The software enables users to replicate real-world scenarios, providing a virtual environment where fluid dynamics can be studied and analyzed with precision. This capability is particularly beneficial for academic assignments, where theoretical knowledge meets practical application.
As students delve into the intricacies of fluid flow simulation, they open doors to a myriad of possibilities. The ability to simulate and visualize fluid behavior allows for a deeper understanding of how different design parameters impact the overall performance of a system. This insight is invaluable, especially when tackling assignments that require optimization and efficiency improvements.
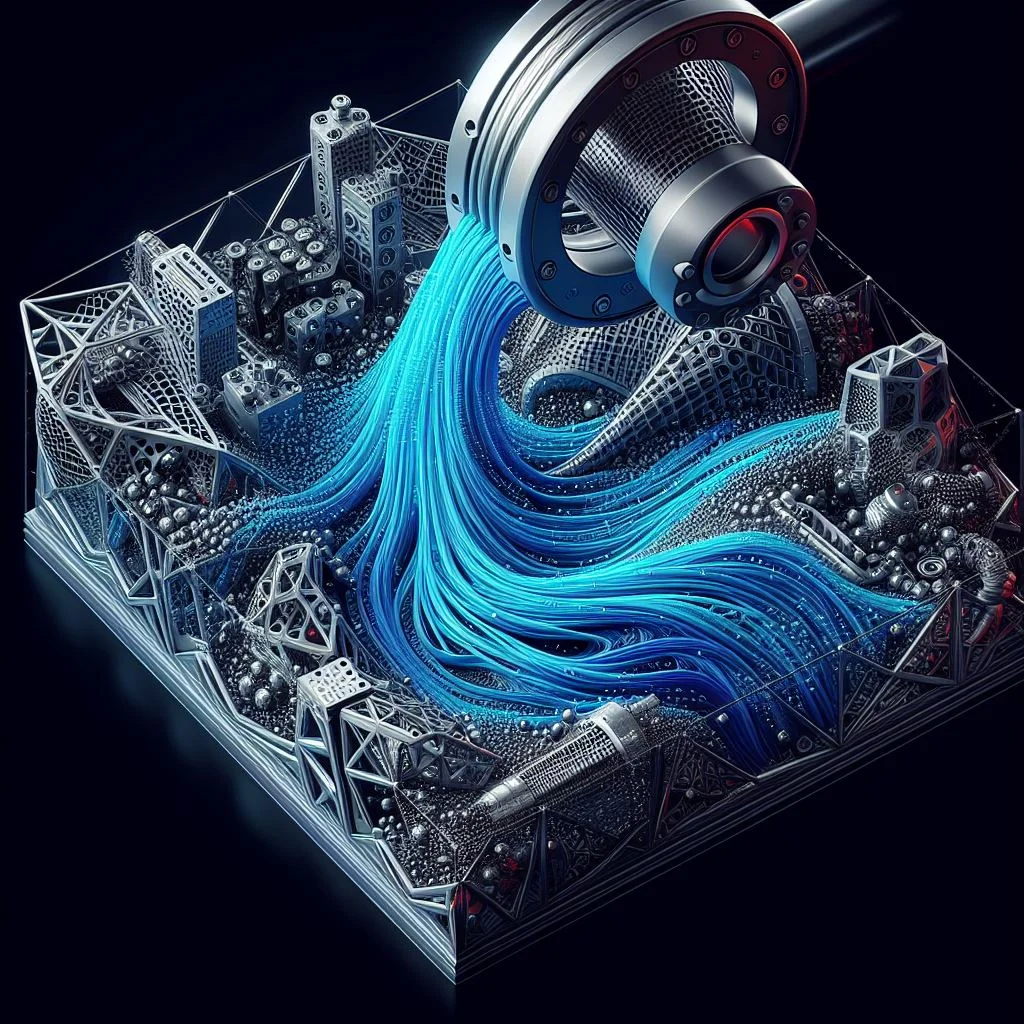
For instance, in mechanical engineering assignments, students may encounter challenges related to pipe systems. SolidWorks' fluid flow simulation facilitates the examination of pressure drops, ensuring that the designed pipe network operates optimally. The software becomes a virtual laboratory where students can experiment with various configurations, gaining a comprehensive understanding of fluid dynamics principles.
In the aerospace domain, where aerodynamics play a crucial role, SolidWorks proves to be an indispensable tool. Fluid flow simulation allows students to study the behavior of air around wings, helping them design more aerodynamically efficient structures. This knowledge is pivotal in creating aircraft that maximize lift while minimizing drag, a fundamental aspect of aerospace engineering.
Moreover, when dealing with assignments involving heat exchangers, SolidWorks' fluid flow simulation comes to the forefront. Students can assess the thermal performance of their designs, identifying areas for improvement and ensuring that heat transfer within the system is optimized. This not only enhances academic learning but also prepares students for real-world challenges in industries where heat exchange is a critical factor.
SolidWorks excels in providing a realistic visualization of fluid flow patterns, making it easier for students to comprehend complex concepts. The visual aspect is a bridge between theoretical knowledge and practical application, allowing students to witness how their designs translate into real-world fluid dynamics scenarios.
The software's capability to conduct parametric studies adds another layer of sophistication to the learning experience. Students can explore multiple design scenarios by adjusting parameters, facilitating a more comprehensive analysis of their assignments. This iterative process of optimization aligns with industry practices, where engineers often need to fine-tune designs for maximum efficiency.
Incorporating fluid flow simulation in SolidWorks into the curriculum enhances the overall educational experience for engineering students. It provides them with a hands-on approach to learning, fostering a deeper understanding of fluid dynamics concepts. The skills acquired through using SolidWorks go beyond the classroom, preparing students for the challenges they will face in their future careers.
Understanding Fluid Flow Simulation
SolidWorks stands out for its comprehensive suite of tools tailored to simulate fluid flow within intricate designs. At the heart of this capability lies computational fluid dynamics (CFD), a sophisticated method for predicting and visualizing fluid behavior. This advanced technology empowers engineers to gain critical insights into how liquids and gases interact within their designs, a fundamental aspect for optimizing performance and efficiency.
With SolidWorks' fluid flow simulation, users can create virtual environments where fluid dynamics unfold realistically. By replicating real-world conditions, the software enables engineers to assess the impact of different factors on fluid behavior, such as pressure, temperature, and velocity. This nuanced understanding aids in making informed design decisions and mitigating potential issues before the physical prototype stage.
Furthermore, SolidWorks provides a user-friendly interface for setting up and conducting fluid flow simulations. Engineers, and students alike, can easily define parameters, boundary conditions, and analyze results seamlessly. This accessibility ensures that the power of fluid flow simulation is harnessed effectively, even by those new to the realm of computational fluid dynamics.
Setting Up Fluid Flow Simulation
The first step in leveraging SolidWorks for fluid flow analysis is setting up the simulation environment. This critical phase involves several key tasks to ensure accurate and meaningful results.
To commence, defining the geometry of the fluid domain is essential. Users can create or import intricate geometries representing the physical components of the system under analysis. Whether it's a complex pipeline network or a straightforward heat exchanger, SolidWorks provides tools to accurately capture the geometry, laying the foundation for a realistic simulation.
Once the geometry is established, the next step involves specifying the fluid properties. SolidWorks allows users to choose from a wide range of fluids, each with its distinct properties. This flexibility enables students to simulate scenarios with different liquids or gases, enhancing the applicability of the simulation to diverse engineering applications.
Establishing boundary conditions is equally crucial in setting up the simulation. Defining how the fluid interacts with its surroundings, including walls, inlets, and outlets, is vital for the accuracy of the analysis. SolidWorks simplifies this process through an intuitive interface, guiding users in specifying conditions that mimic real-world scenarios.
SolidWorks' user-friendly interface is a boon during these setup tasks. It ensures that even those new to fluid flow simulation can navigate the process seamlessly. Simultaneously, its advanced features cater to the needs of experienced professionals, providing a versatile platform that accommodates a spectrum of users with varying levels of expertise. The accessibility of SolidWorks in this phase makes it a powerful tool for both academic assignments and real-world engineering challenges.
Solving Fluid Flow Problems
Once the simulation setup is complete, SolidWorks delves into the intricate task of solving fluid flow problems using advanced numerical methods. The software employs a discretization approach, breaking down the fluid domain into a mesh of elements. This mesh serves as the foundation for solving the governing equations of fluid dynamics, enabling SolidWorks to analyze and predict fluid behavior with remarkable precision.
The numerical solution process involves solving for fluid properties at each element within the mesh. SolidWorks iteratively refines this solution until it converges to a stable and accurate outcome. This iterative refinement is a crucial aspect of ensuring the reliability of the simulation results. Through each iteration, the software fine-tunes the calculations, taking into account the complex interactions between fluid elements and the boundaries of the simulated system.
This methodical approach not only enhances the accuracy of the results but also allows users to gain deeper insights into the nuances of fluid flow within their designs. By comprehensively addressing the governing equations through numerical methods, SolidWorks provides engineers and students alike with a robust platform for tackling a diverse range of fluid flow problems in academic assignments and real-world applications.
Analyzing Results and Extracting Insights
The real power of fluid flow simulation in SolidWorks lies in the ability to analyze the results and extract meaningful insights. Engineers can visualize velocity profiles, pressure distributions, and other key parameters to understand how fluids interact with their designs. This information is crucial for making informed decisions and optimizing the performance of engineering systems.
Furthermore, SolidWorks offers post-processing tools that allow users to delve deeper into the simulation results. Engineers can generate detailed reports, charts, and graphs, aiding in the interpretation of complex data. This level of post-processing capability is invaluable in academic assignments where a comprehensive analysis of fluid behavior is required.
By scrutinizing the simulation results, students can gain a deeper understanding of the impact of design changes on fluid dynamics. For instance, altering the geometry of a pipe or adjusting flow rates can have profound effects on pressure distribution and velocity within a system. The ability to extract insights from simulation results equips students with the skills to make informed design decisions that enhance the efficiency and functionality of their engineering projects.
Applications of Fluid Flow Simulation in Assignments
Fluid flow simulation in SolidWorks finds applications in a wide range of engineering assignments. Let's explore how this powerful tool can be utilized in different fields:
One notable application is in the design and analysis of hydraulic systems. Engineering assignments often require students to develop hydraulic systems for various purposes, such as heavy machinery or industrial processes. SolidWorks' fluid flow simulation allows them to model and simulate the behavior of hydraulic fluids within these systems. This includes assessing pressure distribution, identifying potential leakage points, and optimizing the overall performance of the hydraulic system.
In the realm of environmental engineering, fluid flow simulation proves crucial for analyzing water and air pollution dispersion. Students tasked with environmental impact assessments can leverage SolidWorks to simulate the dispersion patterns of pollutants in bodies of water or the atmosphere. This aids in understanding the potential environmental consequences of different scenarios, enabling informed decision-making in the design and planning of industrial facilities.
Additionally, SolidWorks' fluid flow simulation is invaluable in assignments related to biomedical engineering. Students working on the design of medical devices, such as blood flow through artificial organs or drug delivery systems, can use the software to model and analyze fluid behavior. This ensures that their designs meet stringent safety and efficacy standards, contributing to advancements in medical technology.
Mechanical Engineering Assignments
In mechanical engineering, understanding fluid behavior is essential for designing efficient cooling systems, hydraulic components, and ventilation systems. SolidWorks' fluid flow simulation capabilities allow engineers to optimize the performance of these systems, ensuring they meet design specifications and operate reliably.
Aerospace Engineering Assignments
Aerospace engineers rely on fluid flow simulation to analyze the aerodynamics of aircraft, spacecraft, and other aerospace components. SolidWorks enables engineers to study the airflow around wings, fuselages, and propulsion systems, contributing to the development of more aerodynamically efficient and fuel-efficient vehicles.
Civil Engineering Assignments
In civil engineering, fluid flow simulation is used to analyze water and wastewater systems, stormwater drainage, and environmental flows. SolidWorks helps engineers design sustainable and resilient infrastructure by simulating the behavior of fluids in pipes, channels, and other components.
Biomedical Engineering Assignments
Biomedical engineers utilize fluid flow simulation to study blood flow, drug delivery systems, and respiratory mechanics. SolidWorks' capabilities enable the optimization of medical devices, ensuring they operate safely and effectively within the human body.
Advantages of Using SolidWorks for Fluid Flow Simulation
SolidWorks stands out as a preferred tool for fluid flow simulations due to its array of advantages, catering to the diverse needs of engineers and designers alike. One notable advantage is the user-friendly interface, providing a seamless experience for both beginners and seasoned professionals. The intuitive nature of SolidWorks ensures that users can quickly adapt to the fluid flow simulation module, reducing the learning curve associated with complex simulation software.
Another key advantage lies in the extensive material database integrated into SolidWorks. This feature allows users to accurately define the properties of fluids, ensuring realistic simulation results. Whether dealing with water, oil, or air, SolidWorks provides a comprehensive selection of materials, contributing to the accuracy and reliability of fluid flow analyses.
SolidWorks' robust solver technology is a game-changer in fluid flow simulations. The software employs state-of-the-art algorithms to solve complex fluid dynamics equations, delivering precise and efficient results. This advanced solver capability enables engineers and students to explore intricate scenarios, from turbulent flows to transient behaviors, expanding the scope of their analyses.
Moreover, the parametric study capabilities of SolidWorks empower users to conduct systematic analyses by varying multiple parameters. This proves invaluable in engineering assignments, where students can explore different design iterations and optimize their solutions based on specific criteria. The ability to assess the impact of various factors on fluid behavior enhances the depth and quality of assignments, fostering a more comprehensive understanding of fluid dynamics.
Seamless Integration with CAD Models
One standout feature of SolidWorks is its seamless integration between CAD modeling and fluid flow simulation. Engineers can directly utilize their existing 3D CAD models, eliminating the cumbersome process of data transfer or model reconstruction. This integration not only saves time but also ensures that the simulation is closely aligned with the actual design, providing a more accurate representation of fluid behavior in real-world scenarios.
User-Friendly Interface
SolidWorks boasts an intuitive and user-friendly interface, making it accessible to both beginners and experienced users alike. The software's guided workflows and interactive tools contribute to a streamlined simulation process. This user-centric approach enhances the learning curve for students, allowing them to focus more on understanding fluid dynamics concepts rather than grappling with complex software interfaces.
Robust Solver Technology
SolidWorks employs advanced solver technology, guaranteeing accurate and efficient fluid flow simulations. The software's capabilities extend to handling complex geometries, transient simulations, and multiphase flows. This ensures that engineering students can trust the results of their simulations, providing a solid foundation for making informed design decisions.
Extensive Material Database
With an extensive material database, SolidWorks equips users with the ability to easily assign properties to fluids. This feature simplifies the setup process for simulations, allowing students to concentrate on the core aspects of fluid behavior analysis. The availability of a comprehensive material database ensures that simulations mirror real-world conditions, contributing to the overall reliability of the results.
Tips for Success in Fluid Flow Simulation with SolidWorks
To achieve optimal results in fluid flow simulation, consider the following tips:
Understanding the intricacies of fluid flow simulation in SolidWorks is the first step toward successful analysis. Begin by thoroughly familiarizing yourself with the software's interface, tools, and simulation setup. SolidWorks provides a user-friendly environment, and a solid foundation in its usage is crucial for accurate simulations.
When setting up simulations, pay meticulous attention to the boundary conditions. Accurate representation of real-world scenarios ensures that the simulation results align with practical outcomes. Assigning appropriate material properties and defining realistic constraints contribute to the reliability of the simulation.
Meshing is a critical aspect of fluid flow simulation. Opt for a mesh refinement strategy that balances accuracy and computational efficiency. A refined mesh in areas of complex flow and crucial features provides more accurate results without compromising simulation speed.
Iterative refinement is key. Run preliminary simulations to identify potential issues and refine your setup accordingly. This iterative process allows for continuous improvement and ensures that the final simulation accurately represents the intended fluid behavior.
Utilize post-processing tools in SolidWorks to extract meaningful insights from simulation results. Visualization of flow trajectories, pressure contours, and velocity vectors aids in the interpretation of complex fluid dynamics. SolidWorks offers powerful post-processing capabilities that enhance the understanding of simulation outcomes.
Collaborate and seek guidance from peers and mentors. Fluid flow simulation can be intricate, and sharing insights with others in the field fosters a collaborative learning environment. Discussing challenges, strategies, and best practices enhances your proficiency in using SolidWorks for fluid flow analysis.
By incorporating these tips into your approach, you'll enhance the accuracy and reliability of fluid flow simulations in SolidWorks, setting the stage for success in your academic assignments and future engineering endeavors.
Validate Simulations with Experimental Data
Whenever possible, validate your simulations with experimental data. This helps ensure the accuracy of your results and builds confidence in the simulation outcomes. This iterative validation process enhances the reliability of your fluid flow analysis, aligning theoretical predictions with real-world observations.
Utilize Adaptive Meshing
Take advantage of SolidWorks' adaptive meshing capabilities. This feature refines the mesh in areas of interest, providing more accurate results without unnecessarily increasing computational costs. Adaptive meshing optimizes the simulation process, allowing for a balance between accuracy and computational efficiency.
Explore Different Boundary Conditions
Experiment with different boundary conditions to understand how changes in inputs affect fluid behavior. This iterative process can lead to insights that drive design improvements. By exploring various boundary conditions, students gain a comprehensive understanding of the factors influencing fluid dynamics, enriching their problem-solving skills.
Collaborate and Seek Feedback
Collaborate with colleagues and seek feedback on your simulation setup and results. Multiple perspectives can uncover overlooked details and contribute to the overall success of your fluid flow analysis. Engaging in collaborative efforts fosters a dynamic learning environment, where diverse insights enhance the quality of simulation outcomes.
Conclusion
Fluid flow simulation in SolidWorks is undoubtedly a valuable tool that transcends traditional mechanical design. As we conclude our exploration of this powerful feature, it becomes evident that engineers and designers, working on assignments spanning diverse disciplines, can greatly benefit from its capabilities.
The comprehensive nature of SolidWorks in simulating fluid behavior provides users with a nuanced understanding of their designs. Whether tackling assignments related to pipe systems, heat exchangers, or aerofoil studies, the software's ability to analyze and visualize fluid dynamics is unparalleled. This not only enhances the quality of academic submissions but also lays the foundation for practical problem-solving skills that are crucial in the professional realm.
Moreover, by incorporating fluid flow simulation into assignments, students are exposed to real-world scenarios, preparing them for the challenges they may encounter in their future careers. The optimization capabilities of SolidWorks allow users to refine their designs based on specific parameters, fostering a mindset of continuous improvement and efficiency.
One of the key takeaways from utilizing SolidWorks for fluid flow simulation is the realistic visualization it offers. The software bridges the gap between theoretical concepts and practical applications by providing users with a visual representation of fluid flow patterns. This realistic approach not only aids in comprehension but also instills a deeper appreciation for the complexities of fluid dynamics.
In the realm of academic assignments, SolidWorks proves to be an indispensable tool for optimizing pipe systems. Students can analyze pressure drops, ensuring the efficiency and cost-effectiveness of fluid transportation networks. The software's application in heat exchanger analysis is equally significant, allowing students to evaluate and enhance thermal performance in their assignments.
For aerofoil studies, SolidWorks becomes a virtual laboratory where students can unravel the mysteries of aerodynamics. The insights gained from fluid flow simulation contribute to the design of efficient wings, ensuring optimal lift and performance in aerospace-related assignments.
As we reflect on the importance of fluid flow simulation in engineering education, it becomes clear that it goes beyond theoretical learning. SolidWorks becomes a catalyst for transforming theoretical knowledge into practical skills, preparing students for the dynamic challenges of the engineering world. The inclusion of this simulation tool in the curriculum not only enhances academic excellence but also nurtures a mindset of innovation and adaptability.