- Bend Allowance, Bend Deduction, and K-Factor in Sheet Metal Design
- 1. Bend Allowance:
- 2. Bend Deduction:
- 3. K-Factor:
- Inserting Base Flange in SolidWorks for Efficient Sheet Metal Design
- Sheet Metal Tab
- Edge Flange
- Miter Flange
- Hem
- Jog
- Conclusion
Sheet metal design is a fundamental aspect of engineering and manufacturing, and SolidWorks is one of the most powerful tools available to engineers and designers. Understanding the intricacies of sheet metal design is essential for creating products that are not only functional but also cost-effective to manufacture. In this blog, we will explore some key concepts in sheet metal design and demonstrate how to apply them using SolidWorks. If you need help to complete your Sheet Metal assignment, we are here to provide the assistance you require.
Bend Allowance, Bend Deduction, and K-Factor in Sheet Metal Design
Before we delve into the practical aspects of using SolidWorks for sheet metal design, it's crucial to establish a solid foundation by understanding the fundamental concepts of bend allowance, bend deduction, and K-factor. These concepts are at the core of accurate sheet metal design and are essential for ensuring that your final part dimensions align with your design specifications.
1. Bend Allowance:
Definition: Bend allowance is the amount of material you need to add to the total flat pattern length to account for the stretching and deformation that occurs during the bending process. It serves to compensate for the material elongation that takes place on the outer surface of the bend. By considering bend allowance, you ensure that the final bent part will have the correct dimensions and geometry.
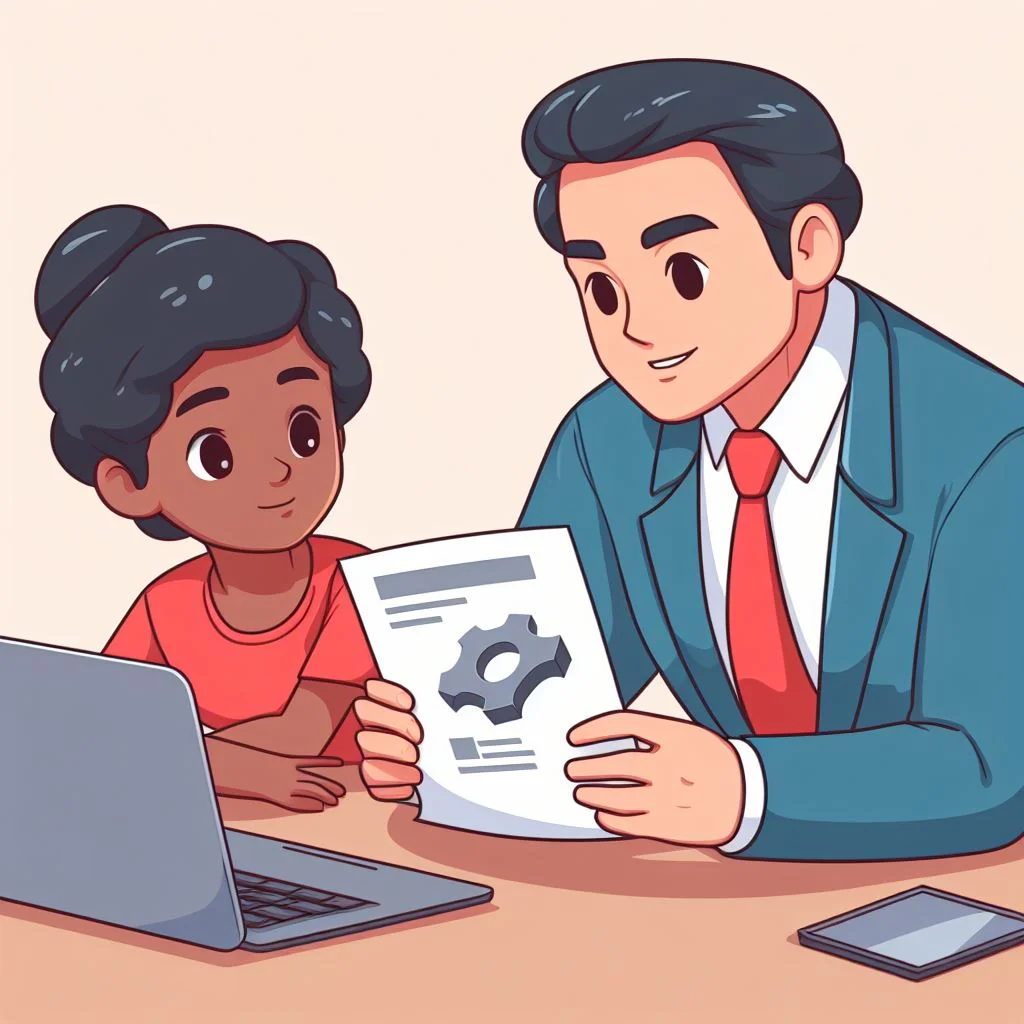
Factors Influencing Bend Allowance: Several factors affect the calculation of bend allowance, making it a crucial parameter in sheet metal design. These factors include:
- Material Thickness: Thicker materials will generally require more bend allowance because they exhibit more stretching during the bending process.
- Bend Radius: The radius of the bending tool used determines how much stretching occurs during bending. Smaller bend radii result in more stretching, necessitating a larger bend allowance.
- Bend Angle: The angle through which the material is bent also plays a role in the amount of stretching. Greater bend angles lead to more elongation.
Importance of Bend Allowance: Bend allowance is essential for achieving precision in sheet metal manufacturing. Without accounting for it, you risk producing parts that are inaccurate and do not meet the specified dimensions. This can lead to rework, increased production costs, and the potential for a product that doesn't fit or function as intended.
SolidWorks and Bend Allowance: In SolidWorks, you can easily and accurately calculate bend allowances. The software considers the material thickness, bend radius, and bend angle to automatically determine the required bend allowance. This feature streamlines the design process, making it more efficient and reducing the likelihood of errors.
2. Bend Deduction:
Definition: In contrast to bend allowance, bend deduction is the amount by which the material is shortened during the bending process. It represents the difference between the initial flat pattern length and the final formed length of the sheet metal. Bend deduction is crucial for accurate sheet metal design and manufacturing, as it helps determine the correct blank length needed for bending.
Calculating Bend Deduction: To calculate bend deduction, you can use the following formula:
Bend Deduction = Initial Flat Pattern Length - Final Formed Length
Importance of Bend Deduction: Understanding bend deduction is essential for accurately predicting the length of material required for a given bend. This ensures that you cut your material to the correct size, preventing waste and reducing production costs.
3. K-Factor:
Definition: The K-factor is a dimensionless factor that relates the bend allowance to the material thickness and the bend radius. It's a vital parameter for calculating bend allowances accurately, as it considers both the material properties and the bending process. The K-factor varies with different materials, tools, and bending methods, making it a crucial component of sheet metal design.
K-Factor Formula: The formula for the K-factor is:
K-Factor = (Internal Radius + Material Thickness) / Internal Radius
Factors Affecting K-Factor: The K-factor is influenced by several variables, including the material type, tooling, and bending process. Different materials have different deformation characteristics, and varying tooling can result in different bend behavior.
SolidWorks and K-Factor: SolidWorks allows you to input the K-factor value that best suits your specific project requirements. By accurately defining the K-factor, you ensure that your sheet metal design is adjusted to the unique properties of the material and the bending tools you intend to use.
Understanding bend allowance, bend deduction, and the K-factor is fundamental for successful sheet metal design. These concepts provide the framework for calculating and accounting for the stretching and deformation that occurs during the bending process, ultimately leading to precise and cost-effective sheet metal components. With the support of SolidWorks, which can automatically calculate these values, you can streamline your sheet metal design process and avoid costly errors, ensuring your final products meet design specifications and manufacturing requirements. Mastering these concepts and using SolidWorks effectively will be invaluable in your journey to becoming a proficient sheet metal designer.
Inserting Base Flange in SolidWorks for Efficient Sheet Metal Design
In SolidWorks, the creation of sheet metal parts begins with the insertion of a base flange. The base flange serves as the foundation for your entire sheet metal design, providing the initial shape that will be bent and formed to create the final part. Let's explore this process in more detail, step by step.
Opening a New Part File and Selecting the Sheet Metal Option:
Begin by opening a new part file in SolidWorks. To work with sheet metal, select the "Sheet Metal" option, which sets the environment for designing and modeling sheet metal components. This environment comes with specialized tools and features tailored to sheet metal design.
Defining Material, Thickness, and Other Parameters:
- Once you've set up the sheet metal environment, the next step is to define the material and thickness of your sheet metal. This information is crucial for accurately modeling the part and for calculating parameters like bend allowances and bend deductions, which we discussed earlier.
- To define the material and thickness, you can either select from a list of predefined materials or input custom values if your material is not on the list. Additionally, you may need to specify other parameters such as the gauge of the material, which could influence how the software interprets your design.
Using the Base Flange/Tab Tool to Create the Initial Shape:
- With the material and thickness defined, you can start creating your base flange. To do this, select the "Base Flange/Tab" tool. This tool allows you to sketch the initial outline of your sheet metal part. You can create this sketch using various methods, including drawing lines, arcs, or using existing sketches or profiles.
- It's essential to be precise at this stage, as the accuracy of your sketch will directly affect the final shape and dimensions of your sheet metal part. Keep in mind the concepts of bend allowance and bend deduction we discussed earlier, as they play a crucial role in determining how your part will behave during the bending process.
Specifying Dimensions, Bend Parameters, and Relief Options:
- After creating the initial shape of your sheet metal part, it's time to specify the dimensions and other parameters. You can define things like the overall length, width, and height of your part. Additionally, you'll need to specify the bend parameters, including the bend radius, bend angle, and the direction of the bend (inside or outside).
- The relief options are also critical at this stage. Relief cuts or openings are introduced to compensate for the material deformation during bending, preventing wrinkles or warping. You can select various relief options such as rectangular, circular, or obround shapes, depending on your design requirements.
SolidWorks offers real-time feedback, providing a visual representation of your part as you adjust these parameters. This feature enables you to make on-the-fly modifications, ensuring your design aligns with your project specifications.
Moving On to Additional Features:
- Once the base flange is in place, you can proceed to add additional features to your sheet metal design. These features can include edge flanges, hems, tabs, jogs, and miter flanges, all of which contribute to the functionality, rigidity, and assembly of your sheet metal part.
- The base flange serves as the starting point for building a more complex sheet metal component. SolidWorks makes it easy to incorporate these additional features, providing a comprehensive set of tools to simplify the process.
In conclusion, the base flange is a foundational element in sheet metal design using SolidWorks. It provides the initial shape and structure from which your sheet metal part will be formed. By following the steps mentioned above, you can efficiently create the base flange, define crucial parameters, and prepare the foundation for more intricate sheet metal features, ultimately leading to a well-structured and accurately designed sheet metal part. SolidWorks' user-friendly interface and specialized sheet metal design environment make the entire process intuitive and streamlined for both beginners and experienced users.
Sheet Metal Tab
Tabs are used to reinforce edges and corners of sheet metal parts. SolidWorks provides a dedicated feature called Sheet Metal Tab to create these reinforcing elements easily.
To insert a sheet metal tab:
- Select the desired edges or corners of your sheet metal part.
- Specify the tab's dimensions and other parameters.
- SolidWorks will create the tab and include it in the flat pattern.
Edge Flange
Edge flanges are used to extend the edges of a sheet metal part, providing rigidity and facilitating connections with other components. SolidWorks allows you to create edge flanges with precision and ease.
To insert an edge flange:
- Select the edge you want to extend.
- Specify the dimensions, bend parameters, and relief options.
- SolidWorks will create the edge flange and include it in the flat pattern.
Miter Flange
Miter flanges are used to connect two perpendicular edges of a sheet metal part, often at a 45-degree angle. They are essential for creating complex sheet metal assemblies. SolidWorks provides tools to create miter flanges with accuracy.
To insert a miter flange:
- Select the two perpendicular edges you want to connect.
- Specify the dimensions and bend parameters.
- SolidWorks will create the miter flange and include it in the flat pattern.
Hem
A hem is a folded edge that not only adds rigidity to a sheet metal part but also provides safety by eliminating sharp edges. SolidWorks simplifies the process of adding hems to your designs.
To insert a hem:
- Select the edge you want to hem.
- Specify the dimensions and bend parameters.
- SolidWorks will create the hem and include it in the flat pattern.
Jog
Jogs are small extensions or notches made in the sheet metal to accommodate fasteners or other components. SolidWorks offers an easy way to add jogs to your designs.
To insert a jog:
- Select the edge where you want to create the jog.
- Specify the dimensions and position of the jog.
- SolidWorks will create the jog and include it in the flat pattern.
Conclusion
SolidWorks is a powerful tool for sheet metal design, offering a wide range of features and tools to create accurate and manufacturable parts. Understanding fundamental concepts like bend allowance, bend deduction, and K-factor is crucial for successful sheet metal design. By mastering tools like base flange, sheet metal tab, edge flange, miter flange, hem, and jog, you can efficiently design complex sheet metal parts for various applications.
In this blog, we've provided an overview of these concepts and demonstrated how to use SolidWorks to apply them in your designs. Whether you're a student learning the ropes of sheet metal design or a professional looking to enhance your skills, SolidWorks and these fundamental concepts will be your allies in creating efficient and cost-effective sheet metal components.
So, the next time you embark on a sheet metal design project, remember to leverage SolidWorks and these essential principles to ensure your designs are not only functional but also optimized for manufacturing. Happy designing!