- Understanding Buckling Analysis
- Buckling Defined
- Significance of Buckling Analysis
- Finite Element Analysis (FEA) in SolidWorks
- FEA for Buckling Analysis
- Steps in Performing Buckling Analysis in SolidWorks
- Model Creation: Crafting the Foundation for Buckling Analysis
- Applying Boundary Conditions in Buckling Analysis: Ensuring Realistic Simulation
- Material Properties
- Mesh Generation: Optimizing Structural Analysis Precision
- Load Application
- Buckling Analysis Setup
- Solve and Interpret Results
- Importance of Buckling Analysis in Assignments
- Bridging Theory and Practical Application
- Enhancing Problem-Solving Skills
- Real-World Applications and Case Studies
- Automotive Engineering
- Aerospace Engineering
- Challenges and Future Trends in Buckling Analysis
- Challenges in Accuracy
- Future Trends
- Conclusion
Buckling Analysis stands as a cornerstone in the realm of SolidWorks, serving as a linchpin for evaluating the structural stability of diverse engineering designs. This robust computer-aided design (CAD) software empowers engineers and designers to delve deep into the intricate aspects of how structures respond to applied loads, offering invaluable insights into potential failure points. In the dynamic landscape of structural engineering, where the stability and reliability of components are paramount, SolidWorks' Buckling Analysis emerges as an indispensable tool for ensuring the robustness of designs and preventing catastrophic failures. In the context of academic assignments, delving into Buckling Analysis within SolidWorks provides students with a unique opportunity to bridge theoretical knowledge with hands-on practical application, enabling them to complete their Finite Element Analysis assignment. Assignments centered around this critical analysis technique compel students to not only grasp the theoretical underpinnings of structural stability but also to apply this knowledge in a tangible and real-world context. As they navigate the intricacies of modeling, meshing, and interpreting results within the SolidWorks environment, students not only enhance their technical proficiency but also cultivate essential problem-solving skills that will serve them well in their future careers as engineers and designers. The H1 of this blog thus serves as a gateway to a comprehensive exploration of the significance, methodologies, and real-world implications of Buckling Analysis in SolidWorks, making it an invaluable resource for both academics and practitioners alike.
Understanding Buckling Analysis
Understanding buckling analysis is essential in ensuring the structural stability of engineering designs. Buckling refers to the sudden failure of a structure under load, and its analysis involves predicting the critical load at which instability occurs. In the context of SolidWorks, a leading CAD software, buckling analysis is conducted through Finite Element Analysis (FEA). FEA allows engineers to break down complex structures into smaller, more manageable elements, facilitating a detailed simulation of their behavior under varying conditions. By comprehending buckling phenomena, engineers can identify potential failure points, design structures with enhanced stability, and ultimately prevent catastrophic collapses. This understanding serves as a cornerstone in the field of structural engineering, providing a comprehensive insight into how different factors, including material properties, geometry, and applied loads, influence the stability of structures.
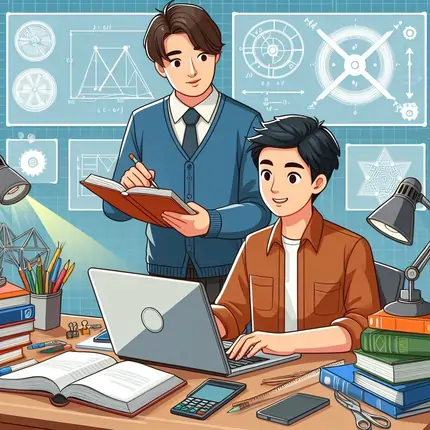
Buckling Defined
Buckling in structural engineering is a phenomenon characterized by the sudden failure of a structure under an applied load, leading to a rapid and often unexpected collapse. This critical instability arises when the structure reaches a threshold load, causing it to deviate from its intended form and lose its ability to bear additional loads. The root causes of buckling are multifaceted, involving a delicate interplay of material properties, geometric imperfections, and external forces. Unlike gradual deformations seen in yielding or plasticity, buckling manifests as a sudden and sometimes catastrophic event, emphasizing the need for a thorough understanding and predictive analysis to ensure structural stability in engineering designs. In the realm of SolidWorks and Finite Element Analysis, the precise identification of potential buckling points is indispensable for engineers seeking to design robust structures capable of withstanding varying loads without compromising safety.
Significance of Buckling Analysis
The significance of buckling analysis in structural engineering cannot be overstated. It serves as a proactive measure to prevent catastrophic failures by providing crucial insights into a structure's stability. By identifying the critical load at which buckling may occur, engineers can design structures with enhanced safety margins, ensuring they can withstand various real-world conditions. This predictive capability is essential in mitigating risks associated with structural instability, especially in applications where human safety and the integrity of the designed system are paramount. The insights gained from buckling analysis empower engineers to make informed decisions during the design phase, ultimately contributing to the creation of robust and reliable structures that meet safety standards and regulatory requirements. In essence, the significance of buckling analysis lies in its ability to bridge theoretical knowledge with practical application, offering a proactive approach to structural design and engineering excellence.
Finite Element Analysis (FEA) in SolidWorks
Finite Element Analysis (FEA) stands as the cornerstone of structural evaluation within the SolidWorks ecosystem. This numerical simulation technique revolutionizes the way engineers analyze and predict the behavior of complex structures. In the realm of SolidWorks, FEA involves the subdivision of intricate designs into smaller, more manageable elements, forming a mesh that mimics the structure's geometry. This method enables a detailed examination of how different parts of a structure respond to varying loads, ultimately aiding in the identification of potential weaknesses. By leveraging FEA in SolidWorks, engineers gain valuable insights into the structural integrity of their designs, ensuring that components can withstand the rigors of real-world applications. The ability to simulate and visualize the effects of loads on a digital prototype enhances the efficiency of the design process and contributes to the overall success of engineering projects.
FEA for Buckling Analysis
Finite Element Analysis (FEA) for buckling analysis is a sophisticated computational technique that has become integral to the field of structural engineering, particularly in the realm of SolidWorks. FEA allows engineers to simulate and analyze the behavior of complex structures under various loading conditions, providing invaluable insights into potential buckling scenarios. By discretizing the structure into finite elements, FEA transforms the intricate mathematical equations governing structural mechanics into a solvable system. This process enables engineers to predict critical loads, identify weak points, and assess the stability of a design. In the context of buckling analysis, FEA in SolidWorks proves to be a powerful tool, offering a comprehensive understanding of how structures respond to applied forces, ultimately aiding in the creation of safer and more robust engineering solutions.
Steps in Performing Buckling Analysis in SolidWorks
Performing buckling analysis in SolidWorks involves a systematic series of steps to ensure accurate predictions of structural stability. The first step is meticulous model creation, where a comprehensive 3D representation of the structure is crafted, incorporating accurate dimensions and material properties. Following this, engineers must carefully apply boundary conditions to mimic real-world constraints and supports. The third step involves specifying the material properties, selecting from a diverse range of options in SolidWorks to closely simulate the behavior of the actual materials. Subsequently, the structure is divided into smaller, manageable elements through mesh generation, striking a balance between accuracy and computational efficiency. The fifth step encompasses the application of external forces by loading the model, simulating the conditions the structure will face. Transitioning to the SolidWorks Simulation module, engineers then set up the buckling analysis, choosing between linear and non-linear options, and inputting relevant parameters. Finally, with all parameters defined, the analysis is initiated, and SolidWorks employs Finite Element Analysis to numerically solve equations, revealing critical loads and buckling modes for a comprehensive understanding of structural stability under different conditions.
Model Creation: Crafting the Foundation for Buckling Analysis
The first step in undertaking a comprehensive buckling analysis in SolidWorks is the meticulous creation of a three-dimensional model. This phase demands precision and attention to detail, as the accuracy of subsequent analyses hinges on the fidelity of the initial model. Engineers and designers must translate their conceptual understanding of the structure into a digital representation within SolidWorks. This involves defining the geometric features, dimensions, and material properties that characterize the physical entity. Whether it's a bridge truss, an automotive component, or an aerospace structure, capturing the essence of the design lays the foundation for a successful buckling analysis. A well-constructed model ensures that the subsequent simulations accurately reflect the real-world behavior of the structure, providing invaluable insights into its stability under various loading conditions.
Applying Boundary Conditions in Buckling Analysis: Ensuring Realistic Simulation
Once the 3D model is meticulously crafted, the next crucial step in performing buckling analysis in SolidWorks is the application of boundary conditions. Think of boundary conditions as the virtual constraints that mimic the real-world environment in which the structure operates. These conditions define how the structure interacts with its surroundings, replicating the constraints and supports that would exist in an actual physical scenario. For accurate and meaningful results, it's essential to thoughtfully impose constraints and supports on the model. This step not only influences the precision of the buckling analysis but also ensures that the simulation aligns with the genuine structural behavior of the design under consideration. Whether it's restraining certain degrees of freedom or allowing specific movements, the accuracy of the entire analysis hinges on the careful application of these boundary conditions, making it a pivotal aspect of the SolidWorks buckling analysis workflow.
Material Properties
Selecting the appropriate material properties is a critical step in conducting buckling analysis within SolidWorks. The behavior of a structure under load is heavily influenced by the physical characteristics of the materials involved. SolidWorks provides users with a diverse range of materials, each characterized by specific properties such as modulus of elasticity, Poisson's ratio, and yield strength. These properties define how a material responds to stress, strain, and deformation, directly impacting the buckling behavior of the structure. Engineers must meticulously choose and input accurate material data to ensure the simulation reflects real-world conditions. The versatility offered by SolidWorks in terms of material selection enables users to analyze structures made from various materials, from metals to polymers, facilitating a comprehensive exploration of buckling phenomena across different engineering applications.
Mesh Generation: Optimizing Structural Analysis Precision
In the realm of buckling analysis in SolidWorks, the process of mesh generation stands as a crucial step in achieving accurate and reliable results. Mesh generation involves dividing the 3D model of a structure into smaller, finite elements, forming a grid that facilitates the numerical simulations essential for analysis. The quality of the mesh profoundly influences the precision of predictions, making it a pivotal consideration in the workflow. A finer mesh, with smaller and more numerous elements, allows for a more detailed representation of the structure but demands increased computational resources. Engineers must strike a balance, selecting a mesh density that ensures accuracy while considering the available computational capacity. SolidWorks empowers users with tools to optimize mesh generation, enabling them to refine the mesh in critical regions and maintain efficiency in computational resources. This meticulous approach to mesh generation ensures that buckling analysis in SolidWorks is not just a simulation but a reliable reflection of the real-world structural behavior.
Load Application
In the buckling analysis journey within SolidWorks, the critical step of load application takes center stage. At this juncture, engineers simulate the external forces that a structure may encounter in its operational environment. SolidWorks provides a versatile platform, allowing users to apply a spectrum of load types, ranging from point loads and distributed loads to pressure loads. The meticulous application of these loads is pivotal for the accuracy of the analysis, as it mirrors the actual conditions the structure is expected to withstand. Engineers must consider the magnitude, direction, and distribution of loads to unveil potential weak points and vulnerabilities in the design. Through the precise orchestration of load application in SolidWorks, engineers can unravel the intricate interplay between applied forces and structural stability, a fundamental aspect in predicting and preventing buckling scenarios.
Buckling Analysis Setup
Once the 3D model is meticulously crafted and boundary conditions are set, the next critical step in the buckling analysis journey within SolidWorks involves configuring the analysis setup. This stage is pivotal as it defines the parameters and conditions under which the simulation will unfold. Users navigate to the SolidWorks Simulation module, where they specify the type of buckling analysis, choosing between linear or non-linear options depending on the structural behavior. Key parameters, such as the type of loading, imperfections, and material properties, are fine-tuned at this juncture. The setup phase also involves defining how the structure interacts with its surroundings and detailing the nuances of geometric imperfections, which can significantly influence the accuracy of the analysis. Through these meticulous configurations, SolidWorks ensures that the subsequent analysis provides valuable insights into the critical loads and potential buckling modes, enabling engineers and designers to make informed decisions about the stability of their structures.
Solve and Interpret Results
Once the pre-processing steps are completed, SolidWorks initiates the computational process to solve the mathematical equations derived from the finite element mesh. This step involves complex numerical algorithms that simulate the structural response to the applied loads. As the solver iterates through the calculations, it gradually converges towards a solution, predicting critical loads and buckling modes. Upon completion of the analysis, the obtained results need careful interpretation. Engineers and designers must scrutinize the data to understand the structural behavior under various conditions, identifying potential weak points and areas prone to buckling. SolidWorks provides intuitive visualization tools, including color-coded contour plots and deformation animations, aiding in the comprehensive interpretation of results. This step is crucial for making informed design decisions, ensuring structural stability, and refining the model if necessary. The ability to effectively solve and interpret results distinguishes a robust buckling analysis in SolidWorks, providing valuable insights for optimizing designs and ensuring structural integrity.
Importance of Buckling Analysis in Assignments
In the realm of engineering assignments, incorporating buckling analysis holds paramount importance for several reasons. Firstly, it serves as a practical application of theoretical knowledge, allowing students to witness the direct impact of structural stability considerations on designs within the SolidWorks environment. As budding engineers, the ability to seamlessly transition from textbook principles to real-world applications is a skill that sets a strong foundation for their future careers. Additionally, assignments featuring buckling analysis contribute significantly to the development of critical thinking and problem-solving skills. Students are challenged to apply engineering concepts to analyze structures under various conditions, fostering a deep understanding of the intricacies involved in ensuring stability. By integrating buckling analysis into assignments, educational institutions not only enhance the academic experience but also empower students to approach engineering challenges with a holistic and practical mindset.
Bridging Theory and Practical Application
Buckling analysis in SolidWorks serves as a vital link between theoretical knowledge and practical application in the realm of structural engineering. While textbooks and lectures provide a foundational understanding of engineering principles, incorporating buckling analysis into SolidWorks assignments empowers students to translate theoretical concepts into tangible designs. This bridge allows them to witness firsthand how variations in material properties, geometric configurations, and applied loads influence the stability of structures. By grappling with real-world scenarios in a virtual environment, students develop a holistic understanding of the interplay between theory and practice, cultivating the problem-solving skills essential for success in the dynamic field of structural engineering. In essence, the inclusion of buckling analysis in SolidWorks assignments transforms theoretical insights into actionable engineering solutions, preparing students for the challenges they will encounter in their professional endeavors.
Enhancing Problem-Solving Skills
Engaging in SolidWorks assignments that incorporate buckling analysis goes beyond the realm of software proficiency; it serves as a catalyst for enhancing problem-solving skills among engineering students. As students grapple with the complexities of predicting structural stability, they are compelled to synthesize theoretical knowledge with practical applications. The multifaceted nature of buckling analysis demands a thoughtful consideration of various factors, pushing students to think critically and creatively. Whether it involves choosing the right material properties, configuring boundary conditions, or interpreting simulation results, each step in the process contributes to the development of a robust problem-solving mindset. This skill set is invaluable, extending far beyond the confines of SolidWorks, as it equips future engineers with the ability to tackle real-world challenges and devise innovative solutions in the dynamic field of structural engineering.
Real-World Applications and Case Studies
In the realm of real-world engineering, the application of buckling analysis in SolidWorks extends far beyond theoretical exercises. One compelling case study lies in the field of automotive engineering, where the stability of chassis and frames is paramount. SolidWorks' buckling analysis allows engineers to predict potential failure points and optimize designs for enhanced safety. Similarly, in aerospace engineering, the analysis becomes indispensable for crafting robust components like wings and fuselage structures. The aviation industry relies on SolidWorks to simulate various loading conditions, ensuring that aircraft can withstand the forces encountered during flight. These real-world applications underscore the significance of buckling analysis in SolidWorks, demonstrating its vital role in designing structures that endure the rigors of diverse and challenging environments.
Automotive Engineering
In the realm of automotive engineering, buckling analysis emerges as a fundamental tool that shapes the design and safety of vehicles. The intricate interplay of forces and materials within an automobile demands a meticulous understanding of structural stability. Buckling analysis in SolidWorks proves indispensable in this field, offering engineers the capability to scrutinize and optimize critical components such as chassis and frames. By simulating various loading scenarios, automotive engineers can predict potential points of instability and, in turn, refine designs to enhance overall safety and performance. The application of buckling analysis in SolidWorks not only ensures compliance with rigorous safety standards but also fosters innovation in the pursuit of creating vehicles that not only excel in performance but also prioritize the safety of occupants on the road.
Aerospace Engineering
Aerospace engineering is a multidisciplinary field that encompasses the design, development, and production of aircraft and spacecraft. As a branch of engineering, aerospace engineering combines elements of mechanical, electrical, and materials engineering to create vehicles that can operate efficiently within the Earth's atmosphere or in outer space. Aerospace engineers tackle challenges related to aerodynamics, propulsion systems, avionics, and structural design, all with the goal of achieving optimal performance and safety. This field plays a crucial role in advancing technology for both civilian and military applications, contributing to the development of cutting-edge aircraft, spacecraft, and satellite systems. Aerospace engineers strive to push the boundaries of what is possible, exploring innovations that redefine the capabilities of human flight and space exploration. Whether designing next-generation aircraft or contributing to the exploration of distant planets, aerospace engineering stands at the forefront of technological advancement, driving progress in the realms of transportation, communication, and scientific discovery.
Challenges and Future Trends in Buckling Analysis
The realm of buckling analysis in SolidWorks, while immensely powerful, is not without its challenges. One notable challenge lies in achieving absolute accuracy, especially when dealing with material non-linearity and intricate geometries. The complex interplay of factors influencing buckling behavior introduces uncertainties that engineers must navigate. As we look toward the future, however, exciting trends and advancements offer promise. The integration of simulation technologies with machine learning and artificial intelligence holds the potential to significantly enhance the accuracy and efficiency of buckling analysis. These innovations may enable SolidWorks to adapt and overcome current challenges, providing engineers with more reliable predictions and streamlined design processes. The evolving landscape of technology suggests a future where buckling analysis becomes even more sophisticated, empowering engineers to tackle intricate structural stability issues with greater confidence and precision.
Challenges in Accuracy
While buckling analysis in SolidWorks through Finite Element Analysis (FEA) has significantly advanced structural engineering, challenges persist in achieving absolute accuracy. Material non-linearity, intricate geometries, and the dynamic nature of real-world scenarios pose complexities that may impact the precision of predictions. Engineers often grapple with the trade-off between computational efficiency and result accuracy, emphasizing the need for continuous refinement in simulation techniques.
Future Trends
Looking ahead, the future of buckling analysis in SolidWorks holds exciting prospects. The integration of advanced technologies, including machine learning and artificial intelligence, is expected to address existing challenges. These innovations can empower the software to adapt and learn from a vast array of simulations, improving its ability to predict buckling behavior accurately. Additionally, developments in hardware capabilities may lead to faster computation times, making intricate analyses more accessible and efficient. As SolidWorks continues to evolve, embracing these future trends will likely redefine the landscape of buckling analysis, offering engineers more reliable insights into structural stability and design optimization.
Conclusion
In conclusion, delving into the realm of buckling analysis in SolidWorks unveils a realm of possibilities for structural engineers and designers. Through the lens of Finite Element Analysis (FEA), the software empowers users to dissect complex structures, foresee potential failure points, and optimize designs for maximum stability. The ability to predict and prevent buckling is not merely a theoretical exercise but a practical necessity in ensuring the longevity and safety of diverse engineering projects. SolidWorks, with its robust simulation capabilities, serves as a gateway for students and professionals alike to bridge the gap between theoretical knowledge and hands-on application, fostering a deeper understanding of structural stability.
As the field of engineering continues to advance, the integration of buckling analysis into SolidWorks assignments not only enriches educational experiences but also propels innovation in real-world applications. The importance of this analysis extends beyond academic exercises, finding its place in industries such as automotive and aerospace engineering, where structural integrity is paramount. Embracing the challenges and exploring future trends in buckling analysis positions engineers to not only meet current demands but to anticipate and overcome challenges on the horizon, shaping a future where structural stability is at the core of every design endeavor. In the dynamic landscape of engineering, SolidWorks stands as a reliable ally, empowering professionals to create structures that withstand the test of time and external forces.