- Unveiling the Power of SolidWorks in Sheet Metal Design
- Understanding Sheet Metal Fundamentals in SolidWorks
- Leveraging Parametric Design for Flexibility
- Mastering the Art of Flat Pattern and Unfold in SolidWorks
- Optimizing Design for Manufacturing (DFM) in SolidWorks
- Advanced Feature Techniques for Complex Sheet Metal Designs
- Harnessing the Power of Design Tables and Configurations
- Integrating Simulation for Optimal Sheet Metal Performance
- Conclusion:
In the realm of 3D CAD design, SolidWorks stands out as a powerful tool, especially in the domain of sheet metal design. Its widespread adoption across industries is a testament to its versatility and efficiency. SolidWorks provides a comprehensive suite of features that caters specifically to the intricacies of sheet metal design, making it an indispensable tool for engineers and designers.
Whether you're a seasoned SolidWorks user, well-versed in its capabilities, or just starting out on your design journey, the quest for uncovering the secrets to streamline your sheet metal design process is a common goal. The allure lies in the promise of heightened efficiency and productivity, allowing users to navigate the complexities of sheet metal design with finesse and precision.
As we embark on this exploration, envision SolidWorks as your virtual workshop, where every tool and feature is a brushstroke on the canvas of your design. It's not merely a software but a creative space where your ideas take shape and transform into tangible, manufacturable designs. The following sections will act as guides, unveiling expert tips and techniques that have the potential to transform your proficiency in mastering the art of sheet metal design within the SolidWorks environment.
SolidWorks, with its intuitive interface and robust parametric modeling capabilities, provides a seamless transition from conceptualization to realization. For seasoned users, it offers a familiar yet constantly evolving landscape, while newcomers find a user-friendly environment that encourages experimentation and learning.
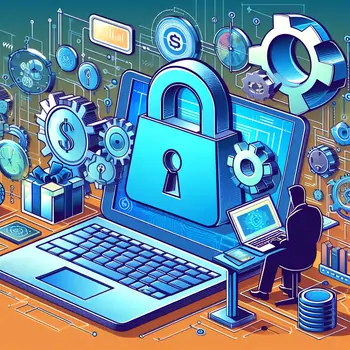
The beauty of SolidWorks lies in its ability to embrace complexity without sacrificing user-friendliness. Its features are designed with precision, allowing for intricate detailing while maintaining an accessible platform for designers of all levels. From creating basic sheet metal components to handling complex geometries, SolidWorks remains a reliable companion, adapting to the diverse needs of its users.
Moreover, the software's commitment to parametric design empowers users to create flexible sheet metal designs. This means that changes and iterations are not only possible but can be implemented with ease. Such flexibility is a game-changer, particularly in industries where design modifications are a routine part of the process.
The transition from 3D models to flat patterns is a critical juncture in sheet metal design. SolidWorks facilitates this transition seamlessly, offering tools like the unfold feature that simplifies the process. As you delve into the intricacies of creating accurate flat patterns, you'll discover the precision with which SolidWorks handles this aspect, ensuring that what you design in 3D is faithfully represented in the flattened version.
Furthermore, the art of sheet metal design extends beyond the virtual realm, requiring a deep understanding of real-world manufacturing constraints. SolidWorks aids in this endeavor by providing tools for Design for Manufacturing (DFM). These tools allow designers to optimize their creations for efficient and cost-effective production. The integration of DFM principles into the design process ensures that your creations are not only aesthetically pleasing but also practical and economically viable. To complete your Sheet Metal Design assignment successfully, it is crucial to apply these principles and leverage the capabilities of SolidWorks for a well-rounded approach.
Unveiling the Power of SolidWorks in Sheet Metal Design
SolidWorks has long been revered for its versatility in creating intricate sheet metal designs. Its widespread adoption in industries ranging from aerospace to automotive is a testament to its robust capabilities. What sets SolidWorks apart is its intuitive user interface, empowering designers of all levels to bring their sheet metal concepts to life with ease.
At the core of SolidWorks' appeal lies its comprehensive suite of sheet metal design tools. The software seamlessly integrates parametric modeling, allowing designers to create dynamic and flexible designs. This parametric approach means that changes made in one part of the model automatically propagate throughout the entire design, ensuring coherence and consistency. This feature proves invaluable in the iterative nature of sheet metal design, where adjustments and refinements are the norm.
Furthermore, SolidWorks excels in providing a virtual environment for designers to visualize their sheet metal creations. The 3D modeling capabilities enable a realistic representation of the final product, facilitating better decision-making during the design phase. Designers can simulate how the sheet metal will bend, fold, and interact with other components, leading to more informed design choices.
The software's robustness extends to its ability to generate accurate flat patterns from 3D models. SolidWorks effortlessly unfolds complex geometries, producing precise flat patterns that serve as the blueprint for fabrication. This functionality not only accelerates the design-to-production timeline but also minimizes material wastage by optimizing layouts for cutting and manufacturing processes.
In essence, SolidWorks stands as a pillar in the realm of sheet metal design, offering a harmonious blend of user-friendly interfaces and powerful functionalities. As we embark on this journey to uncover the secrets that enhance SolidWorks' prowess in sheet metal design, it's essential to appreciate the software's foundational strengths that make it the preferred choice for designers worldwide.
Understanding Sheet Metal Fundamentals in SolidWorks
SolidWorks has long been revered for its versatility in creating intricate sheet metal designs. The software's widespread adoption among engineers and designers can be attributed to its robust set of features tailored specifically for sheet metal applications. With SolidWorks, users gain access to a comprehensive suite of tools that streamline the entire design process, from conceptualization to production.
One standout feature is SolidWorks' intuitive parametric design capabilities, allowing users to create flexible and adaptable sheet metal designs effortlessly. The software's parametric modeling empowers designers to make real-time changes, explore design variations, and optimize their creations with unparalleled ease. This flexibility ensures that sheet metal designs can evolve seamlessly in response to project requirements or design modifications, enhancing the overall efficiency of the design workflow.
Moreover, SolidWorks excels in the critical aspect of transitioning from 3D models to flat patterns. The software's sophisticated algorithms for bend allowance and K-factor calculations ensure a high level of accuracy in flat pattern development. Designers can confidently utilize the unfold feature, knowing that SolidWorks will generate precise representations of sheet metal components, laying the groundwork for error-free manufacturing processes.
SolidWorks' prowess extends beyond basic functionalities, incorporating advanced features such as Lofted Bend and Swept Flange. These features empower designers to tackle complex geometries and achieve intricate sheet metal forms, expanding the possibilities for creative and innovative designs. As we delve deeper into the following sections, these features will be explored in detail, unlocking their full potential for optimizing sheet metal design.
In essence, SolidWorks serves as a comprehensive toolbox for sheet metal designers, offering a range of features that cater to both fundamental requirements and advanced design challenges. As we journey through the secrets and expert tips in the subsequent sections, this robust foundation provided by SolidWorks becomes the cornerstone for elevating your sheet metal design skills to new heights.
Leveraging Parametric Design for Flexibility
One of SolidWorks' notable strengths lies in its parametric design capabilities, making it a standout choice for sheet metal design. Parametric modeling allows designers to create designs that are not only detailed and precise but also inherently flexible. This flexibility is a game-changer in the ever-evolving landscape of product development.
In the dynamic world of sheet metal design, changes and iterations are not uncommon. Here, SolidWorks' parametric prowess truly shines. Designers can establish relationships between different elements in their models, creating a web of interconnected parameters. This means that a single tweak in one part of the design can propagate changes throughout the entire model, ensuring consistency and accuracy.
Imagine a scenario where a client requests modifications to the dimensions of a sheet metal component. Without parametric design, this could entail hours of painstaking adjustments and potential errors. However, with SolidWorks' parametric capabilities, designers can swiftly adapt to such changes by simply adjusting the relevant parameters. This not only expedites the design process but also significantly reduces the likelihood of errors, fostering a more efficient and reliable workflow.
Furthermore, the parametric approach in SolidWorks extends beyond dimensions; it encompasses material properties, features, and relationships, providing a comprehensive foundation for a flexible design ecosystem. As a result, designers can experiment with various iterations and design alternatives without the fear of compromising the integrity of the entire model.
In essence, SolidWorks' parametric design is not just a feature; it's a philosophy that empowers designers to navigate the complexities of sheet metal design with agility and precision. By mastering this aspect of SolidWorks, designers can truly unlock a new level of adaptability, making them well-equipped to tackle the dynamic challenges of modern sheet metal design projects.
Mastering the Art of Flat Pattern and Unfold in SolidWorks
Efficiently transitioning from intricate 3D models to precise flat patterns is a critical skill in the realm of sheet metal design within SolidWorks. This process is indispensable for fabricators and manufacturers who need clear and accurate templates to cut and shape sheet metal components. In the SolidWorks environment, mastering the art of creating flat patterns and effectively utilizing the unfold feature is a game-changer for designers seeking precision and efficiency.
To delve deeper into this aspect of sheet metal design, it's essential to understand how SolidWorks handles the transition from 3D models to flat patterns. The software provides a dedicated feature known as the "Flat Pattern" feature, which essentially unfolds the 3D model, presenting it in a two-dimensional layout. However, to truly master this process, designers must go beyond the basic application of the Flat Pattern feature.
Advanced techniques involve ensuring that the flat patterns accurately represent the physical characteristics of the sheet metal, accounting for factors such as material thickness, bend allowances, and K-factors. SolidWorks offers customization options within the Flat Pattern feature, allowing designers to tweak parameters and optimize the flat pattern for specific manufacturing requirements.
Moreover, the Unfold feature in SolidWorks provides additional flexibility in working with complex designs. Designers can strategically unfold selected bends or features, offering a more controlled approach to creating accurate flat patterns. Understanding when and how to leverage the Unfold feature can significantly enhance the efficiency of the sheet metal design process.
In essence, mastering the art of flat patterns and utilizing the unfold feature in SolidWorks involves a nuanced understanding of the software's capabilities, coupled with a keen awareness of the intricacies of sheet metal behavior. By incorporating these advanced techniques, designers can ensure that their flat patterns not only meet manufacturing requirements but also contribute to a streamlined and error-free fabrication process.
Optimizing Design for Manufacturing (DFM) in SolidWorks
Optimizing your sheet metal designs for manufacturing in SolidWorks goes beyond creating aesthetically pleasing models. It involves a strategic approach to enhance the manufacturability of your components, minimizing costs and potential hurdles in the production phase. To achieve this, consider the following expert strategies.
Begin by closely collaborating with manufacturing teams during the design phase. Establishing clear communication channels ensures that design specifications align seamlessly with the capabilities of the manufacturing processes. SolidWorks facilitates this collaboration by allowing real-time sharing of design data, fostering a collaborative environment that promotes efficiency and accuracy.
Furthermore, take advantage of SolidWorks' Design for Manufacturing (DFM) tools. These tools help identify potential manufacturing issues early in the design process, allowing you to make informed decisions that prevent costly errors downstream. Evaluate factors such as material selection, bend radii, and tolerances to align with the capabilities of the chosen manufacturing processes, whether it's laser cutting, stamping, or CNC machining.
Consider implementing standard components where possible. SolidWorks provides an extensive library of standard sheet metal components that comply with industry norms. By utilizing these standardized elements, you not only expedite the design process but also enhance compatibility with manufacturing processes, reducing the need for custom tooling and minimizing production costs.
Additionally, leverage SolidWorks' Costing tool to estimate the manufacturing expenses associated with your sheet metal design. This feature provides valuable insights into the cost breakdown, allowing you to identify areas for potential cost savings without compromising on quality or functionality.
Advanced Feature Techniques for Complex Sheet Metal Designs
In the realm of sheet metal design within SolidWorks, the software's robust features open up avenues for tackling the most intricate and complex geometries with finesse. Among these advanced techniques, the Lofted Bend and Swept Flange features stand out as invaluable tools for designers seeking to push the boundaries of their sheet metal projects.
The Lofted Bend feature in SolidWorks allows designers to create smooth and seamless transitions between complex shapes in their sheet metal designs. By lofting between two or more sketches, users can generate intricate surfaces that seamlessly blend into one another, providing a high degree of flexibility in shaping complex components. This feature proves especially useful when dealing with designs that require a gradual change in geometry, such as curved surfaces or tapered sections.
On the other hand, the Swept Flange feature empowers designers to extrude a profile along a sketched path, creating intricate flanges and complex structures. This feature is particularly beneficial when dealing with designs that demand unique and varied cross-sectional profiles along a specified trajectory. By leveraging the Swept Flange tool, designers can achieve precision and creativity in shaping their sheet metal components, adding an extra layer of sophistication to their projects.
Mastering these advanced features not only enhances the aesthetic appeal of your sheet metal designs but also contributes to the overall functionality and manufacturability of the components. As you incorporate Lofted Bend and Swept Flange into your SolidWorks repertoire, you'll find yourself better equipped to meet the demands of complex sheet metal projects, pushing the boundaries of what's achievable in the world of 3D CAD design.
Harnessing the Power of Design Tables and Configurations
Incorporating design tables and configurations into your SolidWorks sheet metal design workflow is a game-changer, offering a seamless way to manage multiple iterations with efficiency and precision. Design tables serve as dynamic spreadsheets within SolidWorks, allowing you to control dimensions, features, and configurations in a centralized manner.
As you delve into the realm of design tables, start by understanding their structure. Each row in the table represents a unique configuration, and each column corresponds to a parameter or dimension you want to control. By populating the cells with values, you can swiftly create and modify configurations without the need to manually adjust each feature.
One of the key advantages of design tables is their ability to enhance collaboration. For instance, if your sheet metal design project involves a team, design tables provide a structured approach for multiple contributors to input their respective dimensions and parameters. This collaborative environment fosters effective communication, ensuring that everyone is on the same page and reducing the chances of errors or discrepancies in the design process.
Furthermore, the configurability offered by design tables enables you to explore various design alternatives effortlessly. By simply changing values in the table, you can generate multiple iterations of your sheet metal design, allowing for quick comparisons and evaluations. This iterative approach not only saves time but also facilitates a more thorough exploration of design possibilities, ultimately leading to optimized and refined outcomes.
Integrating Simulation for Optimal Sheet Metal Performance
Integrating simulation into your sheet metal design process is a game-changer that goes beyond mere visual representation. SolidWorks Simulation, a robust feature within the SolidWorks suite, empowers designers to delve into the realm of virtual testing, providing invaluable insights into the structural integrity and performance of their sheet metal designs.
SolidWorks Simulation allows for a comprehensive analysis of your sheet metal components, considering factors like stress distribution, deformation, and material behavior under various loading conditions. By virtually subjecting your design to real-world forces and environmental factors, you gain a deeper understanding of how it will perform in the physical realm. This insight is invaluable for ensuring that your sheet metal creations not only meet design specifications but also withstand the rigors of their intended applications.
Furthermore, SolidWorks Simulation enables iterative testing and refinement without the need for physical prototypes. This not only accelerates the design process but also significantly reduces costs associated with trial and error. Designers can experiment with different configurations, materials, and dimensions, fine-tuning their sheet metal designs to achieve optimal performance while minimizing material usage and weight.
Beyond structural analysis, SolidWorks Simulation extends its capabilities to thermal analysis, allowing designers to assess how sheet metal components respond to temperature variations. This is particularly crucial in applications where thermal stability is a critical factor, such as electronics enclosures or components exposed to extreme temperature conditions.
Conclusion:
In conclusion, as we bring our journey through the hidden gems of SolidWorks for sheet metal design to a close, you're now equipped with a treasure trove of insights that can propel your skills to unprecedented levels. By putting these expert tips into action, you'll witness a transformative shift in your sheet metal design process—efficiency, accuracy, and overall enjoyment will become the hallmarks of your workflow.
Implementing these SolidWorks secrets is not merely a matter of enhancing your technical prowess; it's a strategic move that can positively impact your entire design ecosystem. Picture a scenario where your iterations are smoother, your designs seamlessly adapt to changes, and the entire manufacturing process unfolds with precision. This isn't just an aspiration; it's the reality you're now poised to create.
As you navigate the intricate landscape of sheet metal design, remember that these secrets are not meant to be confined to the virtual realm of your CAD software. They are tools of empowerment, meant to be wielded in the real-world context of manufacturing and production. Your newfound ability to optimize designs for manufacturability will not only save costs but also foster a collaborative environment where your designs seamlessly translate into tangible, high-quality products.
Moreover, the integration of simulation into your design process is a game-changer. The assurance of structural integrity and performance reliability provides a level of confidence that extends beyond the digital realm. It translates into designs that not only look good on the screen but also function flawlessly in the physical realm—a testament to the power and precision of SolidWorks.
As you embark on this enhanced sheet metal design journey, keep in mind that the joy of creating extends beyond the technical aspects. SolidWorks becomes a canvas for your creativity, and each design iteration is an opportunity to push the boundaries of what's possible. The once-daunting complexities of intricate geometries become a playground for innovation, and you, the designer, are at the helm, orchestrating a symphony of form and function.
In essence, the SolidWorks secrets you've uncovered are keys to unlocking a realm of possibilities. They're not just tips; they're invitations to explore, experiment, and evolve. So, go forth with confidence, armed with the knowledge that your sheet metal designs are not just functional—they're a testament to your mastery of SolidWorks and your commitment to pushing the boundaries of what's achievable in the world of 3D CAD. The journey doesn't end here; it evolves with each design, each project, and each realization of what's possible with SolidWorks at your fingertips.