- Understanding Stress Analysis in SolidWorks
- What is Stress Analysis?
- Why is Stress Analysis Important?
- Analyzing Stresses in Parts
- Step 1: Create or Import Your Part
- Step 2: Define Materials and Constraints
- Defining Materials
- Setting Constraints
- Step 3: Apply Loads
- Step 4: Create a Mesh
- Generating the Mesh
- Step 5: Run the Analysis
- Running the Analysis
- Step 6: Review Results
- Interpreting Results
- Creating a Mesh for Finite Element Analysis
- Leverage Element Sizing Controls
- Scrutinize Mesh Quality
- Iteratively Refine the Mesh
- Conclusion
SolidWorks, a cornerstone of modern computer-aided design (CAD), is a versatile and indispensable software tool widely embraced by engineers and designers alike. Among its multifaceted capabilities, one that shines brightly is its ability to meticulously analyze stresses in parts subjected to a myriad of loads and seamlessly create a mesh for in-depth finite element analysis (FEA). In this comprehensive blog, we embark on an illuminating journey, delving deeply into the intricate realms of stress analysis and mesh creation within the SolidWorks environment. Our goal is to provide an exhaustive guide that empowers students to not only complete their SolidWorks assignment but also lay a strong foundation for their future endeavors in the dynamic world of engineering.
Understanding Stress Analysis in SolidWorks
Before delving into the practical aspects, it is crucial to grasp the fundamental concepts behind stress analysis and its pivotal role in the engineering domain. Stress analysis serves as the bedrock upon which safe and efficient designs are built, providing engineers with insights into how materials respond to external forces. This understanding not only ensures structural integrity but also aids in the optimization of designs for superior performance, cost-effectiveness, and safety, making it an essential cornerstone of the engineering discipline.
What is Stress Analysis?
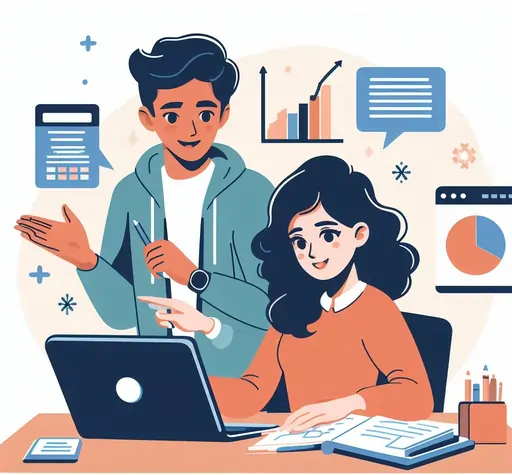
Stress analysis, in essence, is a comprehensive and methodical process that meticulously evaluates how a given part or structure reacts and adapts to external forces or loads. It serves as a virtual voyage into the heart of design resilience, where the aim is to gauge how effectively a structure can withstand the rigors of applied forces while steering clear of catastrophic structural failure. This intricate process involves the intricate dance of simulating the multifaceted impacts of forces and constraints, allowing engineers to not only identify potential weak points but also predict intricate deformation patterns and meticulously pinpoint regions where stress levels reach an unwelcome crescendo within a design.
Why is Stress Analysis Important?
The significance of stress analysis in engineering cannot be overstated, primarily for the following reasons:
- Ensuring Safety: Verifying that a design can withstand expected loads is not merely a professional responsibility but an ethical and moral imperative for engineers and designers alike. The consequences of structural failure can be nothing short of catastrophic, potentially resulting in loss of life, injury, and significant financial and environmental damage. The weight of this responsibility cannot be understated, as it extends beyond the realm of engineering into the broader spectrum of public safety.
- Optimizing Performance: Stress analysis is instrumental in optimizing designs for superior performance. By identifying areas of undue stress, engineers can make informed decisions regarding material selection and structural enhancements.
- Cost-Efficiency: In the realm of engineering projects, cost-effectiveness is paramount. Stress analysis can lead to substantial cost savings by highlighting areas with excessive stress, which can subsequently inform decisions on material usage and manufacturing processes.
Imagine the consequences of a bridge collapsing due to inadequate stress analysis, endangering countless lives and communities. Or consider the implications of a faulty aircraft component, compromising the safety of passengers and crew. In these scenarios and many others, the meticulous practice of comprehensive stress analysis becomes an ethical duty to ensure the well-being and security of the general public.
Moreover, adhering to rigorous stress analysis protocols not only safeguards lives but also protects against legal liabilities and professional reputational damage. Engineers and designers must bear in mind that their work directly impacts the lives and livelihoods of individuals and society as a whole. Thus, the commitment to robust stress analysis transcends mere professional obligation; it is an ethical mandate rooted in the core principles of safety, responsibility, and the preservation of human well-being.
Having established the importance of stress analysis, let's proceed to explore how this is accomplished effectively using SolidWorks.
Analyzing Stresses in Parts
SolidWorks stands as a beacon of innovation, offering an impressive arsenal of meticulously crafted tools that simplifies the intricate task of analyzing stresses in parts subjected to a wide spectrum of loads. Here, in this comprehensive guide, we embark on an educational journey, providing an all-encompassing, step-by-step roadmap that will illuminate the entire process of performing stress analysis in the most intricate and nuanced detail possible, ensuring that you, as an aspiring engineer or designer, are armed with the knowledge and expertise needed to navigate the complex world of SolidWorks stress analysis with confidence and precision.
Step 1: Create or Import Your Part
The critical initial step in the journey of structural analysis is ensuring that you have a part ready for analysis. In this endeavor, SolidWorks empowers you with versatile modeling tools, offering two distinct paths to your destination. Depending on your project's unique requirements, you can opt to either meticulously construct a part from the ground up, harnessing the full scope of SolidWorks' modeling prowess, or seamlessly import an existing design, effortlessly transitioning it into the realm of analysis. This flexibility serves as a testament to SolidWorks' adaptability, equipping you with the tools necessary to embark on your analytical odyssey with utmost precision and efficiency.
Step 2: Define Materials and Constraints
To ensure a simulation that faithfully replicates real-world conditions, it is absolutely vital to meticulously define the material properties of your part and configure constraints with precision. Materials like steel, aluminum, and plastics each boast unique mechanical characteristics, and SolidWorks relies on this data to conduct its analyses with unparalleled accuracy. This crucial step forms the very foundation upon which your simulation rests, harmonizing the intricacies of materials science with the computational power of SolidWorks to deliver results that mirror the real world with utmost fidelity.
Defining Materials
- To embark on this journey within SolidWorks, start by opening your part, the digital embodiment of your creative vision.
- Within the FeatureManager Design Tree, right-click on the part, invoking the command "Edit Material," a crucial step that sets the foundation for your design's physicality.
- In the ensuing Material dialog, thoughtfully select the material that most closely aligns with your part's composition, a choice that marries your digital model to the physical world, and assign it to your creation, ensuring a harmonious synergy between the digital and tangible realms of engineering.
Setting Constraints
- It's imperative to meticulously identify and model real-world constraints affecting your part's behavior, such as specific points being fixed or pinned, as this mirrors the authentic operating environment.
- To replicate the physical scenario with precision, SolidWorks provides intuitive options like "Fix" or "Pin" within the Simulation study. These essential tools seamlessly apply the identified constraints, ensuring a highly accurate simulation that aligns seamlessly with the actual operating conditions of your design.
Step 3: Apply Loads
The next pivotal step involves applying relevant loads to your part. These loads can encompass forces, pressures, moments, and various parameters, depending on the specific design conditions you aim to replicate. To apply these loads effectively:
- Access the "External Loads" folder within the Simulation study.
- Select the type of load that corresponds to your real-world scenario (e.g., force or pressure).
- Specify the magnitude and direction of the applied load to closely mimic the physical environment.
Step 4: Create a Mesh
Meshing, a critical and intricate element of the process, involves dividing your part into smaller elements, a process akin to tessellating a complex puzzle. In 2D, these elements are typically triangles or quadrilaterals, while in 3D, they manifest as tetrahedra or hexahedra. This meticulous subdivision is a crucial step as it approximates the continuous distribution of stresses across your design. It's worth emphasizing that the quality of your mesh, akin to the precision of pieces in a puzzle, profoundly influences the accuracy, reliability, and fidelity of your analysis. Thus, investing time and care in mesh creation is pivotal to yield dependable engineering insights.
Generating the Mesh
- Within the Simulation study tree, right-click on "Mesh" and select "Create Mesh."
- Choose the type of mesh (e.g., automatic or manual) that aligns with your project requirements.
- Define mesh parameters, encompassing element size and shape controls, to strike a balance between accuracy and computational efficiency.
- Execute the mesh generation process by clicking "Generate."
Step 5: Run the Analysis
Once the meticulous preparatory steps are successfully completed, it's time to set the analysis in motion, a pivotal moment where SolidWorks deploys its computational prowess. Utilizing finite element analysis, the software adeptly solves the intricate mathematical equations that govern your part's behavior under the precisely specified conditions. This transformative process yields not just data but actionable insights, akin to a lighthouse guiding your decisions, crucial for making informed, data-driven choices that shape the future of your design and engineering endeavors.
Running the Analysis
- As you delve into the intricate world of simulation, navigate to the Simulation study tree, where you've meticulously fine-tuned your simulation parameters, ensuring every boundary condition aligns perfectly with your design's real-world demands.
- Now, as you stand on the precipice of discovery, right-click on "Run," and with a sense of anticipation, select "Run." This simple action unleashes the formidable power of SolidWorks, setting it in motion to compute, analyze, and finally, derive insightful results that will illuminate the structural integrity of your design.
Step 6: Review Results
Following the successful completion of the analysis, a wealth of data and visualizations eagerly awaits your exploration, poised to offer a comprehensive understanding of your part's behavior under the applied loads. SolidWorks presents an array of visual representations, including vivid stress distribution maps, intricate displacement patterns, and critical safety factor analyses, all meticulously crafted to illuminate the inner workings of your design and provide unparalleled insights into its structural performance.
Interpreting Results
- Stress Distribution: Capitalize on color plots to visualize regions with varying stress levels. Typically, red signifies high stress, while blue denotes areas with minimal stress, providing a vivid visual indicator of potential vulnerabilities.
- Displacement: Scrutinize how your part deforms under the influence of applied loads. This information is instrumental in assessing whether your design adheres to deformation tolerances.
- Safety Factor: The safety factor serves as a paramount indicator of design robustness. A safety factor greater than 1 signifies that your design can safely withstand the applied loads, while values lower than 1 suggest potential structural issues.
Creating a Mesh for Finite Element Analysis
Meshing, often regarded as the bedrock of finite element analysis, warrants a deeper exploration of its nuanced intricacies. Attaining an optimal mesh is pivotal for accurate results, and here, we delve into advanced tips to enhance your meshing skills in SolidWorks. These insights will empower you to craft meshes that not only meet but exceed the standards of precision and reliability expected in professional engineering practices, ensuring your simulations stand as beacons of excellence in the industry.
Leverage Element Sizing Controls
Element size controls empower you to specify element sizes in different regions of your part. This granular control allows you to employ a finer mesh in areas where high stress gradients are expected, while employing a coarser mesh in regions where precision is not as critical. This strategic approach optimizes computation time and resource utilization.
Scrutinize Mesh Quality
SolidWorks equips users with a robust suite of tools to meticulously assess and enhance mesh quality. It is imperative to maintain the integrity of your mesh by vigilantly scrutinizing for any signs of distorted elements, as their presence can potentially introduce inaccuracies that undermine the reliability of your analysis. Make judicious use of the "Mesh Quality" plot, a valuable resource that allows you to pinpoint elements requiring adjustments, thus ensuring the precision and trustworthiness of your simulation results.
Iteratively Refine the Mesh
In scenarios where your analysis is not converging, results appear unstable, or precision is paramount, consider adopting an iterative approach to mesh refinement. This strategy entails meticulously reducing element sizes in critical regions or strategically implementing adaptive meshing techniques to further enhance analysis accuracy and ensure your simulations deliver results of the highest quality and reliability demanded by the most exacting professional engineering standards.
Conclusion
The art of analyzing stresses in parts under varying loads and skillfully creating a mesh is an indispensable skill set for aspiring engineers and designers navigating the world of SolidWorks. By diligently following the comprehensive steps outlined in this blog, students can lay a sturdy foundation in stress analysis and meshing techniques. Armed with these capabilities, they can approach SolidWorks assignments with confidence and precision. Mastery in this domain is cultivated through practice and exploration of diverse design scenarios. Fortunately, SolidWorks offers a wealth of resources and tutorials to further enrich one's knowledge and skills in this field. As students embark on their engineering journeys, they are encouraged to tap into these resources to foster growth and innovation in the realm of CAD and FEA.