- Introduction to Frequency Response Analysis
- Importance in System Dynamics
- Performing Frequency Response Analysis in SolidWorks
- Applications in Structural Analysis
- Enhancing Mechanical Vibrations Analysis
- System Optimization and Design Iterations
- Common Challenges and Troubleshooting Tips
- Case Studies: Real-World Applications
- Future Trends in Frequency Response Analysis with SolidWorks
- Conclusion
SolidWorks stands as an indispensable pillar in the vast landscape of engineering design, offering a treasure trove of capabilities for comprehending and dissecting intricate systems. Among the myriad techniques within its arsenal, one that stands out as essential for both aspiring engineers and seasoned professionals is Frequency Response Analysis. This blog aims to navigate through the complexities of Frequency Response Analysis within the SolidWorks framework, shedding light on its applications, benefits, and transformative potential in the realm of help with your SolidWorks assignment. Whether you're a student seeking guidance or a professional looking to enhance your skills, understanding Frequency Response Analysis in SolidWorks can significantly impact your ability to analyze and optimize engineering systems.
In the realm of engineering, SolidWorks serves as a linchpin, enabling designers to venture into the intricacies of complex systems with unprecedented ease. The software's versatility is evident in its ability to cater to a diverse range of engineering needs, providing a comprehensive platform for designing, simulating, and analyzing various components and systems. Within this expansive toolkit, Frequency Response Analysis emerges as a critical technique, acting as a beacon for those seeking deeper insights into the behavior of dynamic systems.
Frequency Response Analysis, at its core, is a method for understanding how a system responds to different frequencies of input. For engineers and designers working on SolidWorks, this translates to a profound understanding of how a design will behave under various conditions. It's not just a tool for analysis; it's a key that unlocks the door to optimizing designs for optimal performance.
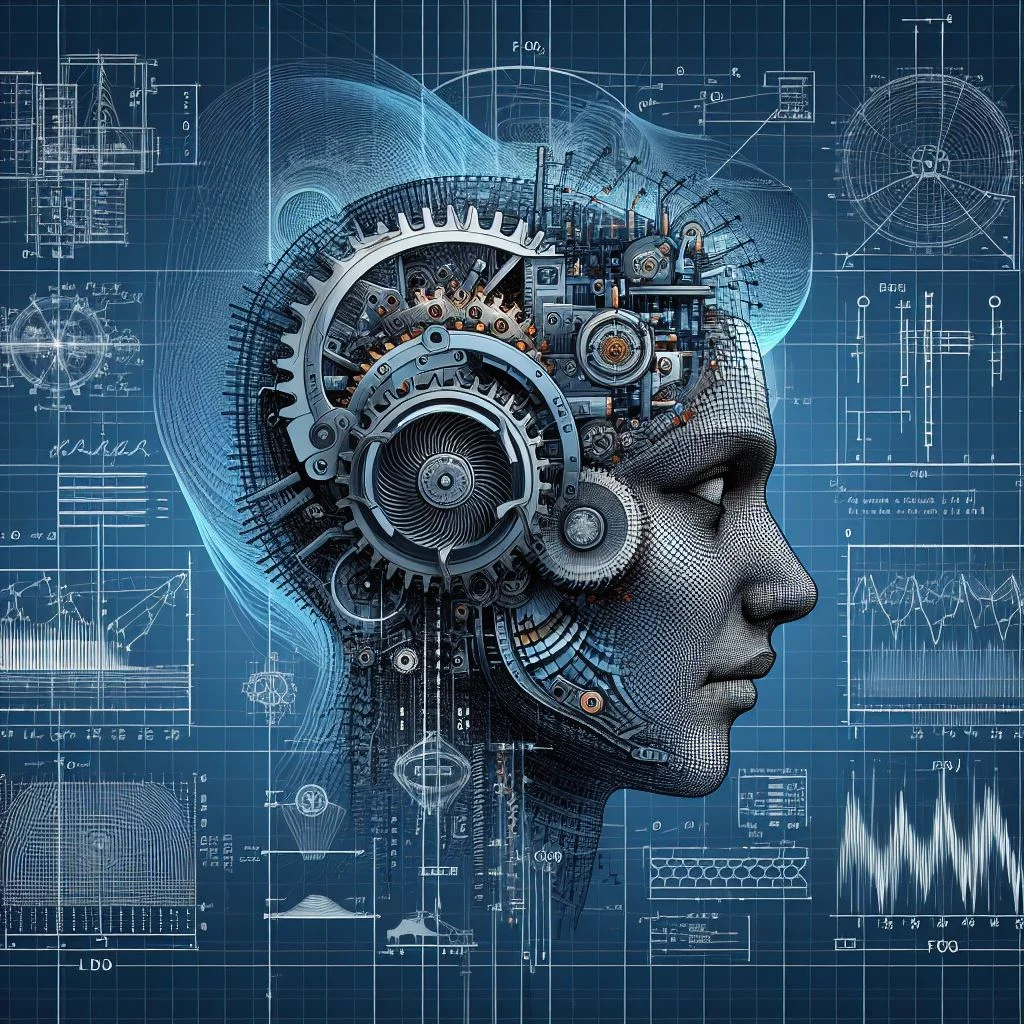
The applications of Frequency Response Analysis in SolidWorks are diverse and impactful. From unraveling the intricacies of system dynamics to fine-tuning structural designs, this technique plays a pivotal role in shaping the way engineers approach their projects. In the context of structural analysis, SolidWorks becomes a virtual laboratory, allowing users to examine the behavior of structures under different frequencies and loads. This insight is invaluable in identifying potential weaknesses, optimizing material usage, and ensuring the structural integrity of designs.
Mechanical vibrations, an inherent aspect of many engineering systems, can be thoroughly explored and understood through Frequency Response Analysis in SolidWorks. Engineers gain the ability to not only visualize but also quantify the vibrations within a design. This knowledge proves instrumental in mitigating potential issues related to resonance and unwanted vibrations, ultimately leading to more robust and reliable designs.
As users navigate through the process of performing Frequency Response Analysis in SolidWorks, a step-by-step journey unfolds. The software provides a user-friendly interface, guiding engineers through the setup of models and the execution of analyses. Interpreting results becomes a seamless task, with visualizations and data that offer deep insights into the dynamic behavior of the system under scrutiny.
The real power of Frequency Response Analysis in SolidWorks lies in its ability to foster a culture of optimization and design iteration. Armed with the data obtained through analysis, engineers can iteratively refine and enhance their designs. This iterative approach is a hallmark of effective engineering, ensuring that each design iteration is a step closer to perfection. SolidWorks becomes not just a design tool but a partner in the creative process, facilitating a dynamic and responsive approach to engineering challenges.
Despite its myriad benefits, Frequency Response Analysis, like any analytical tool, comes with its set of challenges. SolidWorks users may encounter issues during the analysis process, ranging from convergence problems to unexpected results. However, the blog doesn't just stop at extolling the virtues of Frequency Response Analysis; it dives into the common challenges users might face and provides practical troubleshooting tips. This holistic approach ensures that engineers are not just equipped with knowledge but also armed with the tools to navigate potential roadblocks.
As the exploration of Frequency Response Analysis unfolds, the blog delves into real-world applications through compelling case studies. These studies serve as tangible examples of how this analytical technique has been instrumental in solving complex engineering problems across diverse industries. From aerospace to automotive, the adaptability of Frequency Response Analysis in SolidWorks shines through, showcasing its relevance in a multitude of scenarios.
Looking forward, the blog glimpses into the future trends of Frequency Response Analysis within the SolidWorks ecosystem. As technology evolves, so do the tools at the disposal of engineers. The blog discusses emerging trends and advancements, providing readers with a glimpse into what the future holds for this indispensable analytical technique.
Introduction to Frequency Response Analysis
In the realm of engineering design, Frequency Response Analysis stands as a pivotal technique, offering profound insights into the dynamic behavior of systems. As we embark on the journey of understanding this indispensable tool within the context of SolidWorks assignments, it is imperative to grasp the fundamentals.
Frequency Response Analysis is essentially a method employed to assess how a system responds to varying frequencies of input signals. In the context of SolidWorks assignments, this technique becomes paramount for engineers and students alike. It serves as the key to unraveling the intricate relationship between a system's dynamics and its response to external stimuli. By probing the frequency domain, engineers gain a comprehensive understanding of how a system behaves under different conditions.
The significance of this analysis becomes even more pronounced when considering the intricacies of SolidWorks designs. SolidWorks, being a versatile design software, empowers engineers to model and simulate complex systems. Frequency Response Analysis becomes a linchpin in this process, allowing designers to predict and optimize the performance of their creations.
This introductory exploration sets the foundation for a deeper dive into the mechanics of Frequency Response Analysis in the subsequent sections. It acts as a gateway, emphasizing the critical role this analysis plays in deciphering and enhancing the behavior of systems in the SolidWorks environment.
Importance in System Dynamics
Importance in System Dynamics: Unraveling the connection between system dynamics and Frequency Response Analysis is pivotal in gaining a profound understanding of how engineering designs interact with their environment. In the dynamic realm of engineering, systems are in constant motion and subject to varying external forces. SolidWorks emerges as an invaluable ally in this scenario, offering a platform that goes beyond static analysis.
SolidWorks, through its sophisticated tools and features, allows engineers to visualize and analyze the behavior of dynamic systems with precision. Unlike static analysis, which assumes a constant state, system dynamics involve elements in motion, responding to changing conditions. Frequency Response Analysis becomes the lens through which engineers can observe these dynamic behaviors, providing insights into how structures and mechanisms respond to different frequencies of input.
By employing SolidWorks for Frequency Response Analysis, engineers can simulate and assess the performance of their designs under dynamic conditions. This capability is particularly crucial in fields where structures are subjected to vibrations, oscillations, or any form of dynamic loading. Whether it's a suspension system absorbing road vibrations or a machinery component experiencing periodic forces, understanding and optimizing for dynamic behavior is essential.
SolidWorks not only aids in identifying potential issues related to system dynamics but also enables engineers to make informed design decisions for enhanced performance and durability. The ability to visualize and analyze dynamic behavior ensures that the final design is not only structurally sound under static conditions but also resilient in the face of real-world dynamic forces. In essence, SolidWorks empowers engineers to create designs that are not just static entities but living, dynamic systems capable of thriving in diverse operating conditions.
Performing Frequency Response Analysis in SolidWorks
Performing Frequency Response Analysis in SolidWorks involves a systematic approach, beginning with the crucial step of setting up the model. Start by defining the geometry, material properties, and boundary conditions within the SolidWorks environment. This initial stage is pivotal, as it lays the foundation for accurate and meaningful results.
Once the model is set up, the next step is to define the excitation. SolidWorks provides a range of options for applying excitations, including force, displacement, and acceleration. Choosing the appropriate type of excitation is essential to simulate real-world conditions accurately. Engineers must carefully consider the nature of the system under analysis and select the most relevant excitation method.
After defining the excitation, the system's response is simulated over a range of frequencies. SolidWorks enables users to specify the frequency range and resolution of the analysis. This flexibility is invaluable, allowing for a detailed examination of how the system behaves across different frequency components.
Interpreting the results is the final and crucial stage of Frequency Response Analysis. SolidWorks generates graphical outputs, including frequency response curves and mode shapes, providing insights into the dynamic behavior of the system. Engineers must carefully analyze these outputs to identify resonance frequencies, mode shapes, and potential areas of concern.
Applications in Structural Analysis
Frequency Response Analysis proves to be an invaluable tool when applied to structural analysis within SolidWorks. By scrutinizing the dynamic behavior of structures under varying frequencies, engineers can gain profound insights into the integrity and performance of designs. The applications extend across a spectrum of industries, from civil engineering to aerospace, where structural stability is of utmost importance.
In the realm of civil engineering, Frequency Response Analysis aids in the assessment of buildings and bridges. By subjecting these structures to varying frequencies, engineers can identify potential weaknesses or vulnerabilities that might not be evident in static analyses. This dynamic approach provides a more comprehensive understanding of how structures respond to external forces, enabling the optimization of designs for enhanced safety and longevity.
Similarly, in the aerospace industry, where weight and structural integrity are critical factors, Frequency Response Analysis becomes a game-changer. Engineers can analyze the response of aircraft components to vibrations and oscillations, ensuring that the structure remains resilient under diverse operating conditions. This not only enhances the safety of aerospace systems but also contributes to the overall efficiency and performance of the aircraft.
Real-world examples abound, showcasing how Frequency Response Analysis in SolidWorks has been instrumental in optimizing structures for various applications. From skyscrapers to aircraft wings, this analytical tool empowers engineers to design with confidence, knowing that the structural integrity has been thoroughly assessed and refined for optimal performance.
Enhancing Mechanical Vibrations Analysis
In the realm of engineering design, delving into the study of mechanical vibrations is a crucial aspect, and SolidWorks takes the lead in facilitating a comprehensive analysis through Frequency Response Analysis (FRA). By employing FRA in SolidWorks, engineers can gain a profound understanding of how mechanical systems respond to varying frequencies, unraveling a wealth of insights that contribute to the improvement of designs and the mitigation of potential issues.
SolidWorks' prowess in enhancing mechanical vibrations analysis lies in its ability to accurately simulate and visualize the dynamic behavior of structures under varying vibrational conditions. Engineers can explore different scenarios, allowing them to identify critical frequencies, resonances, and modes of vibration that might lead to structural fatigue or performance issues. This in-depth analysis proves invaluable in refining designs, ensuring that mechanical components operate within safe and efficient parameters.
System Optimization and Design Iterations
Frequency Response Analysis in SolidWorks extends beyond the realm of understanding system behavior; it serves as a catalyst for system optimization and design iterations. SolidWorks, with its robust capabilities, empowers engineers to go beyond the initial analysis and fine-tune designs for optimal performance.
Once the frequency response data is obtained, engineers can embark on a journey of refinement. This involves tweaking parameters, adjusting variables, and making design modifications based on the insights gained from the analysis. SolidWorks provides a seamless platform for these iterations, allowing engineers to observe real-time changes in the frequency response and understand how adjustments impact the overall system dynamics.
The iterative process facilitated by SolidWorks is a game-changer in the field of engineering design. Engineers can explore a spectrum of design possibilities, ensuring that the final product not only meets but exceeds performance expectations. This approach is particularly valuable in industries where precision and efficiency are paramount, such as aerospace, automotive, and structural engineering.
Moreover, the integration of optimization tools within SolidWorks streamlines the iterative process. Engineers can leverage optimization algorithms to automatically explore design alternatives, further accelerating the path to an optimized solution. This synthesis of analysis and optimization within SolidWorks transforms the traditional design workflow, fostering innovation and pushing the boundaries of what is achievable in engineering projects.
Common Challenges and Troubleshooting Tips
In the dynamic realm of Frequency Response Analysis within SolidWorks, practitioners often encounter challenges that can potentially impede the seamless progress of their analyses. One common hurdle is the complexity of models, where intricate designs can lead to longer computation times and resource-intensive simulations. To address this, users can consider simplifying the geometry or utilizing SolidWorks Simulation tools strategically to optimize the analysis without compromising accuracy.
Another frequent challenge lies in the proper selection of boundary conditions and constraints, as inaccuracies in these inputs can yield misleading results. Users are advised to conduct thorough reviews of their setups, ensuring that constraints are accurately applied, and boundary conditions mimic real-world scenarios effectively. Utilizing SolidWorks' simulation validation tools can assist in verifying the correctness of these inputs.
Additionally, convergence issues may arise during the analysis, impacting the reliability of results. Understanding the convergence criteria within SolidWorks and adjusting settings accordingly can mitigate these challenges, ensuring accurate and dependable outcomes. It's crucial for users to familiarize themselves with the software's convergence controls and make informed adjustments based on the specifics of their simulations.
Moreover, interpreting and extracting meaningful insights from the obtained frequency response data can pose a challenge. SolidWorks provides post-processing tools and visualization options, but users must possess a nuanced understanding of these features to extract valuable information effectively. Engaging with tutorials and seeking assistance from the SolidWorks community can enhance proficiency in post-processing techniques.
Case Studies: Real-World Applications
In delving into the practical application of Frequency Response Analysis in SolidWorks, exploring real-world case studies unveils its transformative impact on engineering problem-solving. These case studies serve as compelling narratives, illustrating how the nuanced insights derived from Frequency Response Analysis have proven instrumental in resolving complex challenges across diverse industries.
One notable case study involves the aerospace sector, where engineers employed SolidWorks for Frequency Response Analysis to optimize the structural integrity of aircraft components. By understanding the dynamic behavior of critical elements under varying conditions, they were able to refine designs, ensuring optimal performance and safety.
In the automotive industry, SolidWorks facilitated Frequency Response Analysis in the quest for enhanced vehicle suspension systems. Engineers utilized this technique to fine-tune the dynamic response of suspensions, resulting in improved ride comfort, stability, and overall vehicle performance. Real-world testing validated the effectiveness of the analysis, leading to the implementation of optimized suspension designs in production.
Additionally, the energy sector leveraged SolidWorks for Frequency Response Analysis in the development of efficient wind turbine systems. Engineers gained invaluable insights into the vibrational characteristics of turbine components, enabling them to mitigate structural fatigue and enhance overall reliability. This application underscores how Frequency Response Analysis contributes to sustainable energy solutions by optimizing the performance and longevity of critical infrastructure.
Future Trends in Frequency Response Analysis with SolidWorks
As we look into the future of Frequency Response Analysis (FRA) within the SolidWorks ecosystem, a wave of advancements and trends promises to reshape the landscape of engineering analysis. One notable trend revolves around the integration of artificial intelligence (AI) and machine learning (ML) algorithms into FRA processes. SolidWorks is increasingly incorporating smart algorithms that can predict system behaviors more accurately, reducing the need for extensive manual intervention.
Additionally, the future of FRA in SolidWorks is likely to witness enhanced compatibility with virtual reality (VR) and augmented reality (AR) technologies. Engineers and designers can expect a more immersive and intuitive analysis experience, allowing them to interact with complex system dynamics in a three-dimensional space. This shift towards immersive technologies not only enhances the visualization of results but also streamlines the decision-making process during the design phase.
Furthermore, the advent of cloud computing is set to revolutionize how FRA simulations are conducted. SolidWorks is anticipated to leverage cloud-based solutions, enabling faster processing times and the ability to handle larger and more intricate simulations. This not only boosts efficiency but also ensures that engineers can seamlessly collaborate on projects irrespective of geographical boundaries.
Conclusion
In conclusion, delving into the realm of Frequency Response Analysis within SolidWorks reveals a host of invaluable insights and benefits for engineering professionals and students alike. The key takeaways from this exploration highlight the transformative potential of integrating Frequency Response Analysis into SolidWorks assignments.
Understanding system dynamics becomes more than a theoretical exercise; it becomes a practical application that enhances the design and analysis process. The ability to visualize and comprehend how a system behaves under varying frequencies is a game-changer. It empowers engineers to make informed decisions, optimize designs, and troubleshoot potential issues before they manifest in the real world.
The benefits of incorporating Frequency Response Analysis into SolidWorks workflows are multifaceted. It offers a deeper understanding of structural dynamics, paving the way for more robust and efficient designs. Mechanical vibrations, a critical consideration in many engineering applications, can be studied and mitigated effectively, leading to enhanced performance and longevity of components.
Moreover, the iterative nature of design is streamlined through Frequency Response Analysis. Engineers can now iterate designs with precision, fine-tuning parameters based on frequency response data. This iterative process not only improves the overall efficiency of designs but also accelerates the product development cycle.
The significance of Frequency Response Analysis is particularly evident in structural analysis, where the tool enables engineers to identify potential weak points and optimize structures accordingly. This proactive approach minimizes the likelihood of structural failures, enhancing the safety and reliability of engineering projects.
As we reflect on the importance of integrating Frequency Response Analysis into SolidWorks assignments, it becomes evident that it goes beyond meeting academic requirements. It's about equipping future engineers with a skill set that directly translates into real-world problem-solving. The tool becomes an extension of the engineer's thought process, enabling them to anticipate challenges and devise innovative solutions.
In the professional landscape, the ability to conduct Frequency Response Analysis using SolidWorks becomes a sought-after skill. Employers value professionals who not only understand theoretical concepts but can also apply them practically to improve designs and address complex engineering issues. Mastery of this tool opens up new avenues for career growth and positions engineers as valuable assets in their respective industries.
In a rapidly evolving technological landscape, the future of Frequency Response Analysis in SolidWorks holds immense promise. As industries continue to push boundaries and demand more sophisticated engineering solutions, the role of this analysis tool will only become more pivotal. The integration of artificial intelligence, simulation advancements, and collaborative platforms within SolidWorks is expected to further enhance the capabilities of Frequency Response Analysis, making it an indispensable part of the engineer's toolkit.