- Introduction: Unveiling the Significance of Failure Analysis
- Types of Failures in SolidWorks Simulation
- Common Mistakes Leading to Failures in SolidWorks Simulations
- Failure Analysis Techniques in SolidWorks Simulation
- Case Studies: Real-World Applications of Failure Analysis
- Improving Design Iterations Through Failure Analysis
- Best Practices for Implementing Failure Analysis in SolidWorks Simulation
- Conclusion:
SolidWorks Simulation stands as a pinnacle in the realm of engineering and design, offering a virtual testing ground for creators to scrutinize the intricacies of their designs well before they take physical form. This software doesn't merely stop at providing a digital preview; it goes a step further by incorporating a crucial facet known as failure analysis. This integral component plays a pivotal role in unraveling the potential weak links within a design, presenting engineers and designers with invaluable insights into the structural integrity and performance of their creations. In the subsequent sections, we will navigate through the multifaceted landscape of failure analysis in SolidWorks Simulation, exploring its depth and significance in the context of assignments and projects. If you need help with your SolidWorks assignment, delving into SolidWorks Simulation and its failure analysis component provides valuable insights into effectively analyzing and optimizing designs, empowering students and professionals to excel in their engineering assignments and projects.
Understanding the broader context is key to comprehending why failure analysis is a linchpin in the design process facilitated by SolidWorks Simulation. Imagine the traditional design approach where prototypes were built, tested, and refined iteratively. This methodology, while effective, is both time-consuming and resource-intensive. SolidWorks Simulation, on the other hand, revolutionizes this paradigm by enabling a comprehensive digital examination of designs. However, the true efficiency and reliability of this digital scrutiny lie in the astute application of failure analysis.
Failure analysis serves as a beacon, illuminating potential pitfalls and structural vulnerabilities that might elude even the keenest eye during the design phase. It acts as a proactive measure, preventing unforeseen issues from manifesting in physical prototypes or, worse, in the final product. By identifying weak points early in the design process, engineers gain the ability to rectify and reinforce these aspects, resulting in designs that are not only aesthetically pleasing but also robust and resilient in the face of real-world challenges.
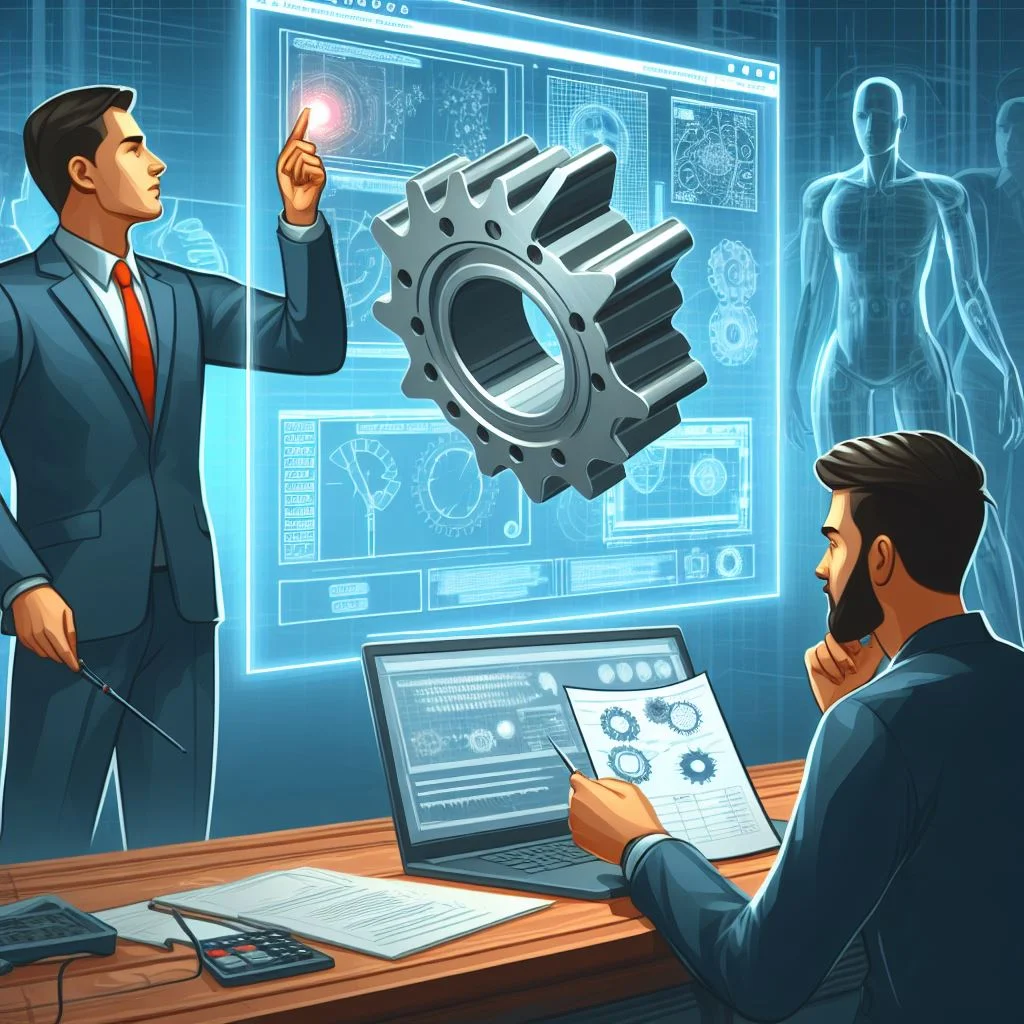
Delving deeper into the realm of SolidWorks Simulation, it becomes evident that failure analysis is not a singular, monolithic process but rather a nuanced and intricate series of examinations. Material failure, structural failure, and thermal failure are just a few facets of the complex interplay that failure analysis encompasses. Each type of failure offers a unique set of challenges and considerations, demanding a tailored approach in the simulation process.
In the vast landscape of digital design and simulation, it's not uncommon for designers to encounter stumbling blocks that lead to failures in SolidWorks Simulation. These stumbling blocks often stem from common mistakes or oversights, such as inaccuracies in material properties, boundary conditions, or meshing parameters. Acknowledging these common pitfalls is a crucial step towards refining simulation techniques and improving the overall reliability of failure analysis in SolidWorks Simulation.
A comprehensive understanding of failure analysis techniques in SolidWorks Simulation is indispensable for engineers and designers striving to optimize their designs. Stress analysis, for instance, involves evaluating how different forces impact a design, helping to identify areas prone to excessive stress. On the other hand, fatigue analysis delves into the effects of repeated loading on a design, providing insights into potential failure points over time. These techniques, among others, form the toolkit that empowers designers to conduct thorough and insightful failure analyses, paving the way for robust and enduring designs.
Real-world case studies stand as testament to the tangible impact of failure analysis in SolidWorks Simulation. Examining instances where failure analysis played a decisive role in design improvement not only reinforces the importance of this process but also provides invaluable lessons for aspiring engineers. From aerospace components to consumer electronics, the application of failure analysis has a far-reaching influence on the quality and reliability of diverse products.
The iterative nature of design is a hallmark of engineering, and failure analysis in SolidWorks Simulation contributes significantly to this iterative process. By unraveling the intricacies of potential failures, designers can embark on more informed design iterations, minimizing the need for costly and time-consuming physical prototypes. This efficiency not only accelerates the overall design process but also enhances the economic viability of projects.
As with any sophisticated tool, there exist best practices that can amplify the effectiveness of failure analysis in SolidWorks Simulation. Attention to detail in defining material properties, meticulous meshing, and judicious application of boundary conditions are just a few examples. These best practices serve as guiding principles, ensuring that the insights derived from failure analysis are accurate, reliable, and actionable.
Introduction: Unveiling the Significance of Failure Analysis
In the intricate world of engineering and design, where precision and performance are paramount, the role of failure analysis cannot be overstated. Failure analysis in SolidWorks Simulation is a critical step in the design process, serving as the vigilant guardian that identifies vulnerabilities and weak points within a virtual model before it takes physical form. This analytical approach contributes significantly to the creation of designs that stand resilient in the face of real-world challenges.
As designers embark on the journey of creating intricate structures and components, the ability to foresee potential failures becomes a linchpin in the pursuit of robust and efficient designs. Failure analysis acts as a preemptive strike against unforeseen issues, providing invaluable insights into the behavior of a design under various conditions. By simulating and scrutinizing potential failure scenarios, engineers gain a comprehensive understanding of the strengths and weaknesses inherent in their creations.
Moreover, failure analysis is not merely a corrective measure but an empowering tool for innovation. It fosters a proactive mindset, encouraging designers to iterate and refine their models iteratively. In doing so, the design process transforms into a dynamic, learning-driven cycle, where each analysis informs subsequent improvements, ultimately leading to designs that exceed expectations in terms of reliability and performance. In essence, failure analysis serves as the compass guiding designers towards the creation of designs that not only meet specifications but also thrive in the real-world environments they are destined to inhabit.
Types of Failures in SolidWorks Simulation
In SolidWorks Simulation, understanding the diverse range of failures is paramount to creating designs that withstand real-world conditions. Material failure is a critical aspect, focusing on how materials respond under different loads and environmental factors. Engineers need to consider factors like yield strength, ultimate strength, and fatigue life to predict and prevent material failures effectively.
Structural failure is another facet that demands close attention during simulation. It involves analyzing how components or structures may collapse under different loads or external forces. Identifying weak points, stress concentrations, and potential points of failure helps engineers reinforce these areas to enhance the overall structural integrity of the design.
Additionally, thermal failure analysis is essential for systems exposed to varying temperatures. SolidWorks Simulation allows engineers to predict how heat is dissipated or accumulated within a design, preventing thermal stress, expansion issues, and overheating. By considering material properties and thermal boundary conditions, designers can optimize thermal performance and mitigate potential failures related to excessive heat.
The synergy of these failure types highlights the comprehensive nature of SolidWorks Simulation. Material, structural, and thermal analyses collectively provide engineers with a holistic understanding of a design's behavior, enabling them to address weaknesses effectively and create robust solutions for a myriad of applications.
Common Mistakes Leading to Failures in SolidWorks Simulations
In the intricate world of SolidWorks Simulations, designers often find themselves grappling with common mistakes that can lead to failures in their analyses. One prevalent error is neglecting accurate material properties, a fundamental oversight that can significantly impact simulation results. Designers must meticulously input precise material data to ensure simulations reflect real-world behavior.
Another stumbling block is overlooking the importance of boundary conditions. Failure to define boundary conditions accurately can result in misleading simulation outcomes. Engineers must pay close attention to constraints, loads, and supports to mirror actual operating conditions, thus enhancing the accuracy of the analysis.
Inadequate meshing is yet another pitfall that designers encounter. Insufficient mesh refinement can compromise the accuracy of stress distribution and lead to inaccurate predictions of failure points. It is crucial to strike a balance between computational efficiency and mesh refinement to obtain reliable simulation results.
Moreover, ignoring geometric imperfections and simplifying complex geometries can introduce inaccuracies. Designers must ensure that the simulated model accurately represents the intricacies of the actual design, accounting for variations and irregularities.
Additionally, overlooking the impact of manufacturing processes on material properties can result in flawed simulations. Understanding how manufacturing influences material behavior is essential for realistic analyses.
To circumvent these pitfalls, designers must approach SolidWorks Simulations with a meticulous mindset, validating inputs, refining meshes, and ensuring the fidelity of the simulated model to the real-world counterpart. By addressing these common mistakes head-on, engineers can elevate the reliability and accuracy of SolidWorks Simulations, ultimately steering clear of potential failures in their analyses.
Failure Analysis Techniques in SolidWorks Simulation
In the realm of SolidWorks Simulation, failure analysis techniques are pivotal for ensuring the reliability and robustness of designs. One primary technique employed is stress analysis, which involves evaluating how various forces and loads affect the structural integrity of a component. SolidWorks Simulation allows engineers to simulate and visualize stress distributions across a design, helping identify areas prone to failure under specific conditions.
Furthermore, fatigue analysis is another crucial aspect of failure analysis in SolidWorks Simulation. It focuses on understanding how repetitive loading or cyclic stresses can lead to material fatigue and eventual failure over time. By subjecting a design to simulated cyclic loading, engineers can predict the lifespan of a component and make informed decisions to enhance its durability.
SolidWorks Simulation offers a comprehensive suite of tools for failure analysis, allowing users to explore different failure modes such as buckling, deformation, and thermal issues. With advanced simulation capabilities, designers can gain valuable insights into potential failure scenarios and iteratively refine their designs to mitigate risks.
In essence, these techniques empower engineers to proactively address weak points in their designs, fostering a more efficient and reliable product development process. Through stress and fatigue analysis in SolidWorks Simulation, designers can optimize their designs, ultimately delivering solutions that not only meet performance requirements but also exceed expectations in terms of durability and longevity.
Case Studies: Real-World Applications of Failure Analysis
Examining real-world examples where failure analysis in SolidWorks Simulation played a crucial role in improving designs and preventing catastrophic failures provides valuable insights into the practical application of simulation techniques. In the aerospace industry, for instance, failure analysis has been instrumental in identifying potential weak points in aircraft components. By subjecting designs to rigorous simulation tests, engineers can detect stress concentrations, material weaknesses, and other critical issues that may compromise the structural integrity of the aircraft.
Similarly, in the automotive sector, failure analysis has proven essential in enhancing vehicle safety and performance. Through SolidWorks Simulation, automotive engineers can simulate various scenarios, such as crash tests or extreme operating conditions, to identify areas of concern in a vehicle's design. This proactive approach allows for the implementation of design modifications aimed at strengthening critical components and ensuring compliance with safety standards.
Moreover, failure analysis has found its place in the medical device industry, where the reliability of equipment is paramount. Simulation tools enable designers to predict potential failures in medical devices, ensuring that they meet stringent regulatory requirements and operate flawlessly in real-world scenarios. By studying these case studies, both students and professionals gain a deeper understanding of how failure analysis in SolidWorks Simulation can have a transformative impact on diverse industries, fostering innovation and reliability in engineering practices.
Improving Design Iterations Through Failure Analysis
In the realm of design engineering, the process of refining and iterating upon initial designs is a fundamental aspect of creating products that meet high standards of performance and reliability. Failure analysis in SolidWorks Simulation plays a pivotal role in this iterative journey by providing valuable insights that guide the improvement of design iterations. By identifying potential weak points and stress concentrations through simulation, engineers gain a deeper understanding of how their designs behave under various conditions.
This enhanced understanding allows for targeted adjustments and refinements during the design iteration phase. Engineers can fine-tune parameters, materials, and geometries with the specific goal of addressing weaknesses highlighted in the failure analysis. Consequently, this informed approach significantly reduces the reliance on physical prototypes, which can be both expensive and time-consuming to produce.
The beauty of incorporating failure analysis into the design iteration process lies in its ability to act as a virtual testing ground. Rather than relying solely on trial and error with physical prototypes, engineers can simulate a wide range of scenarios to predict potential failure modes and make proactive design decisions. This not only accelerates the design cycle but also minimizes the likelihood of costly errors that may arise during the physical testing phase.
In essence, failure analysis in SolidWorks Simulation transforms the design iteration process into a more efficient and cost-effective endeavor, ultimately contributing to the creation of robust and high-performing products.
Best Practices for Implementing Failure Analysis in SolidWorks Simulation
In the realm of SolidWorks Simulation, implementing failure analysis successfully requires a thoughtful and strategic approach. To ensure a seamless integration of failure analysis into SolidWorks Simulation projects, engineers and designers should adhere to a set of best practices.
One fundamental practice is to begin with a comprehensive understanding of the design's intended function and the potential stressors it may encounter. This proactive approach allows for the identification of critical areas prone to failure, guiding the simulation focus towards those specific points. Furthermore, establishing clear objectives for the analysis, such as identifying failure modes, understanding failure mechanisms, and optimizing designs accordingly, provides a roadmap for a more targeted and effective simulation process.
Collaboration and communication are key components of successful failure analysis implementation. Teams should encourage open discussions among members, drawing on the diverse expertise within the group. This collective knowledge can unveil insights that might be overlooked by an individual, fostering a more robust and comprehensive analysis.
Incorporating realistic boundary conditions and loads is another critical aspect. Simulation results are only as accurate as the inputs provided, and ensuring that they closely mirror real-world conditions is paramount. This involves a thorough examination of the operational environment, considering factors like temperature, pressure, and external forces that might impact the design.
Regular validation of simulation results against empirical data or physical testing helps in refining the simulation model and improving its predictive accuracy. Iterative refinement based on real-world feedback is a hallmark of successful implementation, ensuring that the simulation model aligns closely with the actual performance of the designed system.
By embracing these best practices, engineers and designers can elevate the effectiveness of failure analysis in SolidWorks Simulation, resulting in more reliable and optimized designs that withstand the challenges of the real-world applications.
Conclusion:
In conclusion, the process of failure analysis in SolidWorks Simulation stands as a linchpin in the realm of design engineering. Through the exploration of the intricacies involved in identifying weak points and potential failures, it becomes evident that failure analysis is not merely a troubleshooting exercise but a proactive strategy for creating designs that withstand real-world challenges.
One of the paramount takeaways from our discussion is the holistic approach that failure analysis encourages. By considering various aspects such as material properties, structural integrity, and thermal behavior, engineers gain a comprehensive understanding of their designs. This multifaceted insight empowers them to make informed decisions during the design phase, ultimately contributing to the creation of resilient and high-performing products.
Moreover, the real-world applicability of failure analysis cannot be overstated. Case studies have shown that failure analysis in SolidWorks Simulation has played a pivotal role in industries ranging from aerospace to automotive. In these scenarios, failure analysis has not only averted potential disasters but has also driven innovation by prompting design improvements and optimizations. Learning from these real-world examples, designers and engineers can draw inspiration for their own projects, understanding the transformative impact that failure analysis can have on the overall design process.
Furthermore, the iterative nature of design is greatly enhanced through the insights gained from failure analysis. Instead of relying solely on trial and error or physical prototypes, designers can leverage simulation data to refine and optimize their designs at an accelerated pace. This iterative loop not only saves time and resources but also leads to designs that are thoroughly vetted and more likely to meet or exceed performance expectations.
Emphasizing the role of failure analysis in the creation of resilient designs is crucial in the context of SolidWorks Simulation. As a predictive tool, SolidWorks Simulation allows designers to foresee potential challenges and weaknesses in their designs early on. This foresight is invaluable, as it enables preemptive adjustments and improvements, ensuring that the final product is not only functional but also durable and reliable.
In essence, failure analysis in SolidWorks Simulation is a proactive strategy that transforms the design process from a reactive endeavor into a foresighted, deliberate, and innovative one. The power lies in the ability to predict, analyze, and mitigate potential failures, thereby fortifying designs against unforeseen challenges. It is a tool that empowers designers to push the boundaries of what is possible, fostering a culture of continuous improvement and excellence in the field of engineering.
As we wrap up our exploration of failure analysis in SolidWorks Simulation, it is evident that this process is not merely a checkbox in the design workflow; rather, it is a mindset that champions resilience, innovation, and excellence. By integrating failure analysis seamlessly into the design process, engineers can elevate their creations to new heights, creating products that not only meet specifications but exceed expectations in the dynamic and demanding landscape of engineering.