- Parametric Design: A Foundation for Innovation
- Assembly Design Mastery: Building Complex Systems
- Surface Modeling: Sculpting Elegance in Design
- Simulation and Analysis: Ensuring Structural Integrity
- Sheet Metal Design: Unfolding Creativity
- 3D Printing Integration: Bringing Designs to Life
- Advanced Rendering: Visualizing the Future
- Conclusion
SolidWorks has emerged as an indispensable companion for engineering students, providing a robust platform that transcends traditional design boundaries. This software not only facilitates precision in design but also serves as a catalyst for fostering innovation within the academic realm. As we delve deeper into the advanced techniques that SolidWorks offers, students can unlock a myriad of possibilities to enrich their projects and gain a profound understanding of the software's expansive capabilities. If you need help with your 3D Modeling assignment, don't hesitate to reach out. I'm here to provide assistance and support to ensure you excel in your studies.
One of the hallmarks of SolidWorks is its ability to empower students with parametric design principles. Unlike conventional design tools, SolidWorks allows users to establish relationships between various components, creating a dynamic framework where modifications can be made effortlessly. This parametric flexibility is invaluable for engineering students, as it enables them to iterate on designs seamlessly, fostering an iterative and creative design process.
Moving beyond the realm of individual components, SolidWorks shines in assembly design, offering students the ability to construct complex systems. Assembling intricate components into a cohesive whole not only mirrors real-world engineering practices but also challenges students to think holistically about their projects. The mastery of assembly design in SolidWorks becomes a gateway for students to tackle projects with multiple interconnected elements, promoting a comprehensive understanding of engineering systems.
Surface modeling is another facet of SolidWorks that adds a layer of sophistication to student projects. While solid modeling forms the foundation, surface modeling allows students to sculpt elegant and intricate shapes, pushing the boundaries of conventional design. This advanced technique opens up avenues for creating aesthetically pleasing designs that blend form and function seamlessly, offering a holistic approach to project development.
Simulation and analysis tools within SolidWorks provide students with a unique opportunity to validate the structural integrity of their designs. By subjecting virtual models to stress analysis, thermal studies, and other simulations, students can ensure that their projects not only meet design specifications but also adhere to real-world performance standards. This integration of simulation into the design process instills a sense of practicality and engineering rigor, preparing students for the challenges they may encounter in their professional careers.
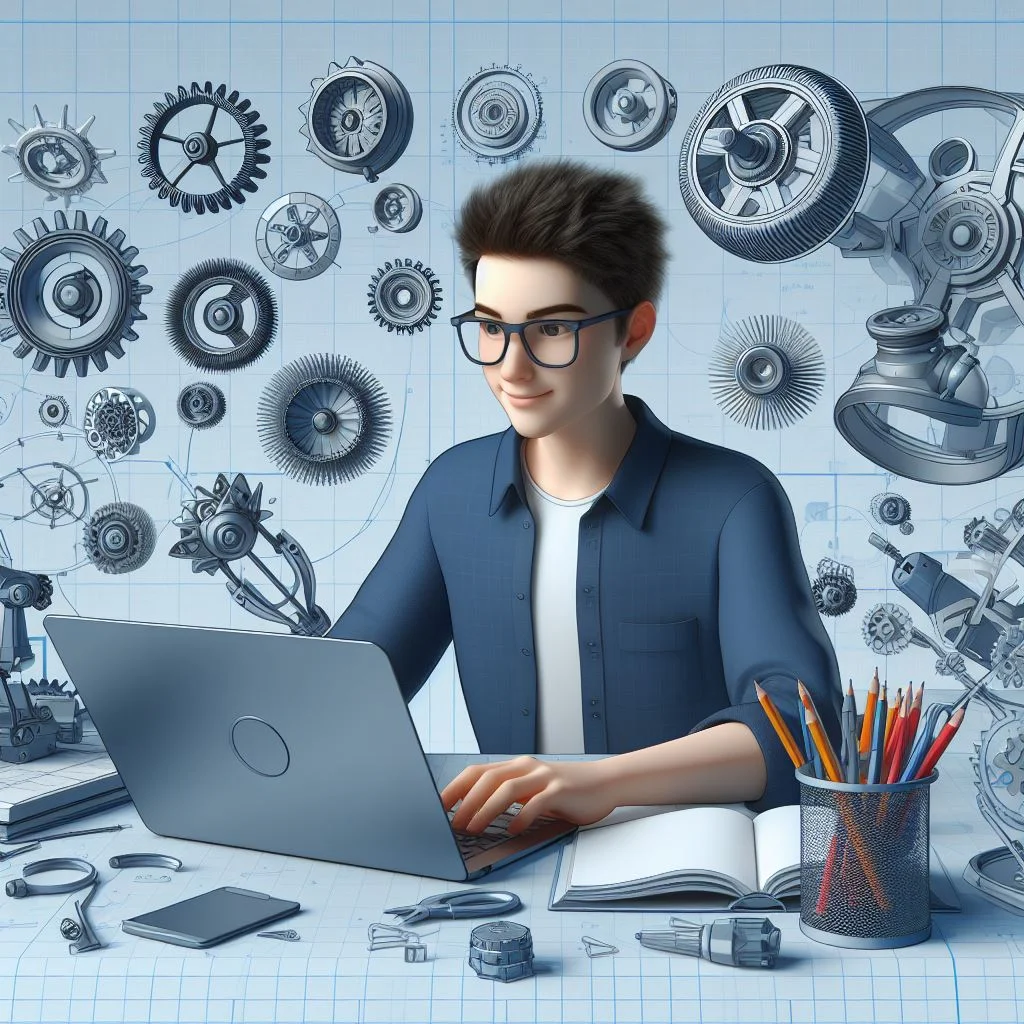
Sheet metal design, often a critical component of engineering projects, is also a realm where SolidWorks excels. Students can delve into the intricacies of creating precise sheet metal components, understanding the nuances of bending, folding, and unfolding. This advanced technique allows for the creation of intricate and structurally sound sheet metal parts, providing a practical skill set that is highly relevant in various industries.
In the rapidly evolving landscape of modern engineering, the intersection of SolidWorks and 3D printing has become a focal point for innovation. Integrating SolidWorks seamlessly with 3D printing technologies empowers students to translate their virtual designs into tangible prototypes. This not only bridges the gap between the digital and physical realms but also encourages a hands-on approach to learning, promoting a deeper understanding of the entire design and manufacturing process.
Advanced rendering techniques within SolidWorks add a visual dimension to student projects, allowing them to showcase their designs with unparalleled realism. Realistic rendering and animation capabilities enable students to present their projects in a compelling and professional manner, enhancing communication and visualization skills. This emphasis on presentation goes beyond the technical aspects, encouraging students to consider the aesthetic and communicative aspects of their designs.
Collaborative design features in SolidWorks facilitate effective teamwork among students. The ability to work on the same project simultaneously, share design changes, and communicate seamlessly enhances collaborative learning experiences. These features mimic real-world collaborative practices, preparing students for the collaborative nature of engineering projects in professional settings.
Automation through the use of macros is yet another advanced technique that SolidWorks offers. Students can streamline repetitive tasks, saving valuable time and boosting overall project efficiency. By automating routine processes, students can focus more on the creative aspects of their projects, promoting a balance between efficiency and innovation.
The creation of exploded views and animations adds a dynamic element to project presentations. Students can use these features to effectively communicate the design intent to their audience, whether it be classmates, instructors, or industry professionals. This emphasis on clear communication aligns with the practical skills required in the professional world, where the ability to convey design intent is crucial.
Parametric Design: A Foundation for Innovation
SolidWorks, renowned for its versatility in engineering design, empowers students to delve into the realm of parametric design, fostering innovation in project development. Parametric design principles form the backbone of this powerful software, offering a dynamic approach to creating 3D models. By establishing relationships between different components, students can achieve a level of versatility and adaptability that transcends traditional design methodologies.
This flexibility is particularly advantageous when modifications are needed. With parametric design, alterations to one part of the model can seamlessly propagate throughout the entire project, ensuring coherence and efficiency in the design process. This not only streamlines the workflow but also allows students to explore multiple design iterations without starting from scratch each time.
Furthermore, SolidWorks provides a robust set of parametric tools, allowing users to define and control parameters such as dimensions, angles, and relationships between geometric elements. This level of control empowers students to fine-tune their designs with precision, creating models that are not only visually appealing but also functionally optimized.
As students delve deeper into parametric design, they gain a holistic understanding of how different elements within a project interact. This knowledge becomes invaluable as they progress in their engineering education and enter professional practice, where the ability to create adaptive and responsive designs is a sought-after skill. In essence, mastering parametric design in SolidWorks opens a gateway to a new dimension of creativity and innovation, setting the stage for successful and forward-thinking engineering projects.
Assembly Design Mastery: Building Complex Systems
Delve into the intricacies of assembly design in SolidWorks, where the art of seamlessly bringing together individual components transforms into building complex systems that mirror real-world applications. Assembly design is not merely about combining parts; it's about orchestrating a symphony of elements that work in harmony to achieve a greater purpose.
In SolidWorks, understanding the nuances of assembly design involves more than just placing components in a virtual space. It requires a deep appreciation for the relationships between parts, the dynamics of movement, and the consideration of real-world constraints. As you embark on the journey of creating complex systems, SolidWorks provides a sophisticated platform where your designs evolve from conceptual ideas to tangible, functional representations.
Consider the importance of clearances, tolerances, and the interaction of moving parts within your assembly. SolidWorks offers advanced features like interference detection and motion analysis, allowing you to identify and resolve issues before the virtual model transitions into the physical realm. This not only enhances the accuracy of your designs but also serves as a valuable learning experience for aspiring engineers.
Furthermore, SolidWorks empowers you to simulate and visualize the behavior of your assembled components under various conditions. Dive into the simulation tools to analyze how forces and loads affect your system, ensuring that it not only functions but excels in the face of real-world challenges.
As you navigate the assembly design process, remember that attention to detail is paramount. SolidWorks enables you to document your assemblies comprehensively, creating a valuable resource for future reference and collaboration. By mastering assembly design, you not only build complex systems virtually but also lay the foundation for efficient and effective real-world applications. Your projects cease to be mere collections of parts; they become intricate systems designed to make a meaningful impact in the world of engineering.
Surface Modeling: Sculpting Elegance in Design
Surface modeling in SolidWorks opens up a realm of possibilities for designers seeking to infuse elegance and sophistication into their projects. Moving beyond the constraints of traditional solid modeling, surface modeling allows you to sculpt sleek and aesthetically pleasing surfaces that mimic real-world objects with precision.
By mastering surface modeling techniques, you gain the ability to create complex and organic shapes that may be challenging to achieve using traditional methods. SolidWorks provides a set of powerful tools that enable you to manipulate curves and surfaces, allowing you to craft designs that seamlessly blend form and function.
One key advantage of surface modeling lies in its applicability to industries where aesthetics play a crucial role, such as automotive and consumer product design. Whether you're designing a futuristic car body or a cutting-edge consumer gadget, surface modeling empowers you to achieve the smooth and visually appealing curves that define modern design trends.
Furthermore, understanding the intricacies of surface modeling enhances your ability to optimize designs for manufacturing processes like injection molding. This is particularly important when working on projects where both form and function are critical, as surface modeling allows you to refine shapes for optimal production efficiency.
In essence, delving into the world of surface modeling in SolidWorks is not just about creating visually stunning designs; it's about elevating the overall quality and manufacturability of your projects. It's a skill that adds finesse and artistry to your engineering toolbox, enabling you to turn conceptual ideas into tangible works of functional elegance.
Simulation and Analysis: Ensuring Structural Integrity
Simulation and analysis are integral components of the design process, playing a crucial role in ensuring the structural integrity of your projects. SolidWorks Simulation empowers students to go beyond the visual aspects of design and delve into the virtual testing realm. Through stress analysis, you can assess how various forces impact your model, identifying potential weak points and areas that require reinforcement.
Moreover, SolidWorks Simulation extends its capabilities to thermal studies, allowing you to understand how heat influences your design. Whether you're working on a device susceptible to temperature changes or optimizing the efficiency of a thermal system, this tool provides valuable insights. Thermal analysis aids in preventing overheating issues and optimizing material selection for enhanced performance.
In addition to stress and thermal studies, SolidWorks Simulation offers a spectrum of simulation tools. Students can explore modal analysis to understand the natural frequencies of their designs, ensuring they avoid resonance issues. Dynamic analysis allows for the study of how external forces impact the behavior of your project over time.
By integrating these simulation tools into your workflow, you not only validate the structural robustness of your designs but also gain a comprehensive understanding of how they will perform in real-world scenarios. This knowledge is invaluable, ensuring that your projects not only meet but exceed the standards set by industry and engineering principles. SolidWorks Simulation opens the door to a deeper level of design validation, empowering students to create projects that stand the test of both simulation and reality.
Sheet Metal Design: Unfolding Creativity
Sheet metal design in SolidWorks is a versatile skill that opens up a world of possibilities for innovative project designs. As you delve into this aspect of the software, you'll find a plethora of tools and techniques at your disposal, allowing you to create intricate and precise sheet metal components.
SolidWorks provides a dedicated set of features for sheet metal design, allowing users to model and unfold complex geometries with ease. The ability to define bend allowances, create flanges, and generate flat patterns is crucial for designing components that are manufacturable in the real world.
One of the key advantages of sheet metal design in SolidWorks is the seamless integration with manufacturing processes. As you unfold your creativity onto the virtual canvas, the software ensures that your designs are not just visually appealing but also practical for fabrication. Understanding how to leverage the parametric capabilities of SolidWorks in sheet metal design allows for quick adjustments and iterations, streamlining the design process.
Moreover, SolidWorks enables users to simulate the bending and forming processes, providing insights into potential challenges and allowing for preemptive problem-solving. This simulation-driven approach enhances the accuracy of your designs, ensuring that the final product meets the desired specifications.
Beyond the technical aspects, sheet metal design in SolidWorks encourages a holistic approach to creativity. It prompts users to consider not only the form and function of their designs but also the feasibility of fabrication and assembly. This comprehensive perspective fosters a deeper understanding of the entire product development lifecycle, a valuable skill for any aspiring engineer.
In conclusion, sheet metal design in SolidWorks is a powerful tool for unfolding creativity in student projects. By mastering the intricacies of this feature, students can push the boundaries of what is possible, creating designs that are not only visually stunning but also practical and manufacturable in the real world. Whether you're crafting complex enclosures or designing streamlined components, SolidWorks' sheet metal capabilities empower you to bring your creative visions to life.
3D Printing Integration: Bringing Designs to Life
In today's fast-evolving technological landscape, 3D printing has emerged as a revolutionary tool in the realm of product development and design. SolidWorks, with its versatile capabilities, seamlessly integrates with 3D printing technologies, allowing designers to transition effortlessly from virtual models to tangible prototypes.
Understanding the intricacies of this integration is pivotal for students seeking to elevate their projects. When venturing into the world of 3D printing with SolidWorks, it's essential to consider various design aspects and adhere to best practices to ensure the successful translation of virtual concepts into physical reality.
Consideration of materials is a fundamental aspect of 3D printing integration. SolidWorks provides a comprehensive range of material options, each with its unique properties. Students must grasp the characteristics of different materials and select the most suitable ones for their specific projects. Whether it's plastics for rapid prototyping or metal for functional parts, the choice of material significantly influences the final outcome.
Moreover, understanding the limitations and capabilities of the chosen 3D printing technology is crucial. SolidWorks supports various file formats compatible with most 3D printers, but students need to be aware of size constraints, resolution settings, and other technical specifications to ensure a smooth printing process. This awareness empowers them to make informed decisions during the design phase, minimizing errors and optimizing the printing workflow.
As students delve into 3D printing integration with SolidWorks, they should explore advanced features such as support structures and infill patterns. Support structures are essential for printing overhanging features, preventing deformities in the final product. Infill patterns, on the other hand, determine the internal structure of the printed object, balancing material usage with structural integrity.
Furthermore, mastering SolidWorks' assembly features becomes imperative when designing projects intended for 3D printing. Ensuring that individual components fit together seamlessly and considering assembly constraints are vital steps in the process. This meticulous approach not only enhances the printing outcome but also reduces post-printing adjustments.
Advanced Rendering: Visualizing the Future
Enhance the visual appeal of your projects with advanced rendering techniques, opening up a world of possibilities to captivate your audience. As you delve into the intricacies of realistic rendering and animation, you'll find that these tools are more than just visual enhancements—they are powerful storytelling instruments that bring your designs to life.
In the realm of advanced rendering, photorealism becomes the ultimate goal. SolidWorks provides a myriad of tools and settings that allow you to simulate real-world lighting conditions, materials, and environments. By mastering these features, you can create visuals that closely resemble the final product, making it easier for stakeholders to envision the end result.
Moreover, animation adds an extra layer of dynamism to your projects. Through SolidWorks animation tools, you can create walkthroughs, assembly animations, and motion studies, providing a holistic view of your design. This not only aids in project presentations but also serves as a valuable tool for design validation and user training.
Imagine presenting a project where every nut, bolt, and component moves seamlessly, demonstrating functionality and design intent. Advanced rendering and animation enable you to tell a compelling story about your project, making it more accessible and engaging for a diverse audience.
As you navigate the world of advanced rendering, consider experimenting with different materials, lighting setups, and environments. The ability to create realistic reflections, shadows, and textures adds depth and authenticity to your visualizations. SolidWorks empowers you to control every aspect of the rendering process, ensuring that your designs are not just technically sound but visually stunning.
Conclusion
In conclusion, embracing advanced techniques in SolidWorks for student projects opens up a realm of possibilities, transforming the way engineering concepts are conceived, designed, and presented. As we've explored parametric design, assembly mastery, surface modeling, simulation and analysis, sheet metal design, 3D printing integration, advanced rendering, collaborative design, automation with macros, and the art of exploded views and animations, it becomes evident that SolidWorks is not merely a software but a gateway to innovation and creativity.
These advanced techniques empower students to think beyond the basics, encouraging them to push the boundaries of what is conventionally possible. Parametric design, for instance, instills a sense of flexibility and adaptability in projects, allowing for swift modifications and adjustments. This not only mirrors real-world engineering scenarios but also fosters a mindset of continuous improvement.
Assembly design mastery takes students on a journey of creating intricate systems, teaching them the importance of each component's role in the larger mechanism. It promotes a holistic understanding of the design process, emphasizing the need for seamless integration and efficient collaboration among team members.
Surface modeling, with its focus on aesthetics and precision, introduces an element of artistry into engineering. By mastering this aspect, students can add an extra layer of sophistication to their projects, making them visually appealing and market-ready.
The incorporation of simulation and analysis tools ensures that student projects not only look good on paper but also meet the rigorous standards of structural integrity. This knowledge is invaluable in the professional world, where robust and reliable designs are non-negotiable.
Sheet metal design opens up avenues for creativity, challenging students to think in three dimensions. The ability to unfold designs and create intricate sheet metal components adds a practical and hands-on dimension to their learning experience.
The seamless integration of SolidWorks with 3D printing technologies bridges the gap between the virtual and physical worlds. Students can witness their designs come to life, gaining insights into the practical considerations of manufacturing and prototyping.
Advanced rendering techniques elevate the visual communication of projects, making them more compelling and market-ready. These skills not only enhance project presentations but also contribute to the creation of impressive portfolios that can set students apart in the competitive job market.
Collaborative design features in SolidWorks emphasize the importance of teamwork, a crucial skill in the professional engineering landscape. The ability to work efficiently with team members on the same project fosters a sense of camaraderie and collective achievement.
Automation with macros, a tool often underutilized, empowers students to work smarter, not harder. By automating repetitive tasks, they can devote more time to the creative and strategic aspects of their projects, ultimately improving overall project efficiency.
Finally, the art of exploded views and animations is a storytelling tool that goes beyond technicalities. It allows students to communicate their design intent effectively, ensuring that stakeholders, whether they are team members, instructors, or potential clients, grasp the essence of the project.
In essence, mastering these advanced techniques in SolidWorks not only enhances technical proficiency but also cultivates a mindset of innovation and adaptability. As students apply these skills in their projects, they are not just learning software; they are preparing for a future where creativity, collaboration, and cutting-edge design are the keys to success. SolidWorks becomes a catalyst for their growth, transforming students into forward-thinking engineers ready to tackle the challenges of tomorrow's world.