- Evolution of CAD in Sheet Metal Design
- Parametric Design: Shaping the Future
- Integration of Artificial Intelligence
- Cloud-Based Collaboration in Sheet Metal Design
- Sustainable Sheet Metal Design Practices
- Conclusion:
In the ever-evolving landscape of sheet metal design, the integration of Computer-Aided Design (CAD) technologies has been instrumental in shaping the future of fabrication. As manufacturing processes continue to advance, the role of CAD in sheet metal design has become increasingly pivotal. This dynamic field is witnessing a surge in innovation, driven by the relentless pursuit of efficiency, precision, and sustainability. If you need assistance with your sheet metal assignment, don't hesitate to reach out. I'm here to provide support and guidance to ensure your success.
The seamless integration of CAD technologies has revolutionized the way sheet metal components are conceptualized, designed, and brought to life. Gone are the days of relying solely on traditional drafting methods; CAD has ushered in a new era of digital precision and creativity. Designers and engineers now have powerful tools at their disposal, allowing them to create intricate and complex sheet metal designs with unparalleled accuracy.
One of the key trends propelling the field forward is the advent of parametric design. Parametric modeling allows for the creation of intelligent, data-driven designs where changes to one part of the model automatically update related components. This not only expedites the design process but also enhances adaptability, as modifications can be seamlessly incorporated throughout the entire model. The result is a more agile and responsive approach to sheet metal design, capable of meeting the evolving demands of the industry.
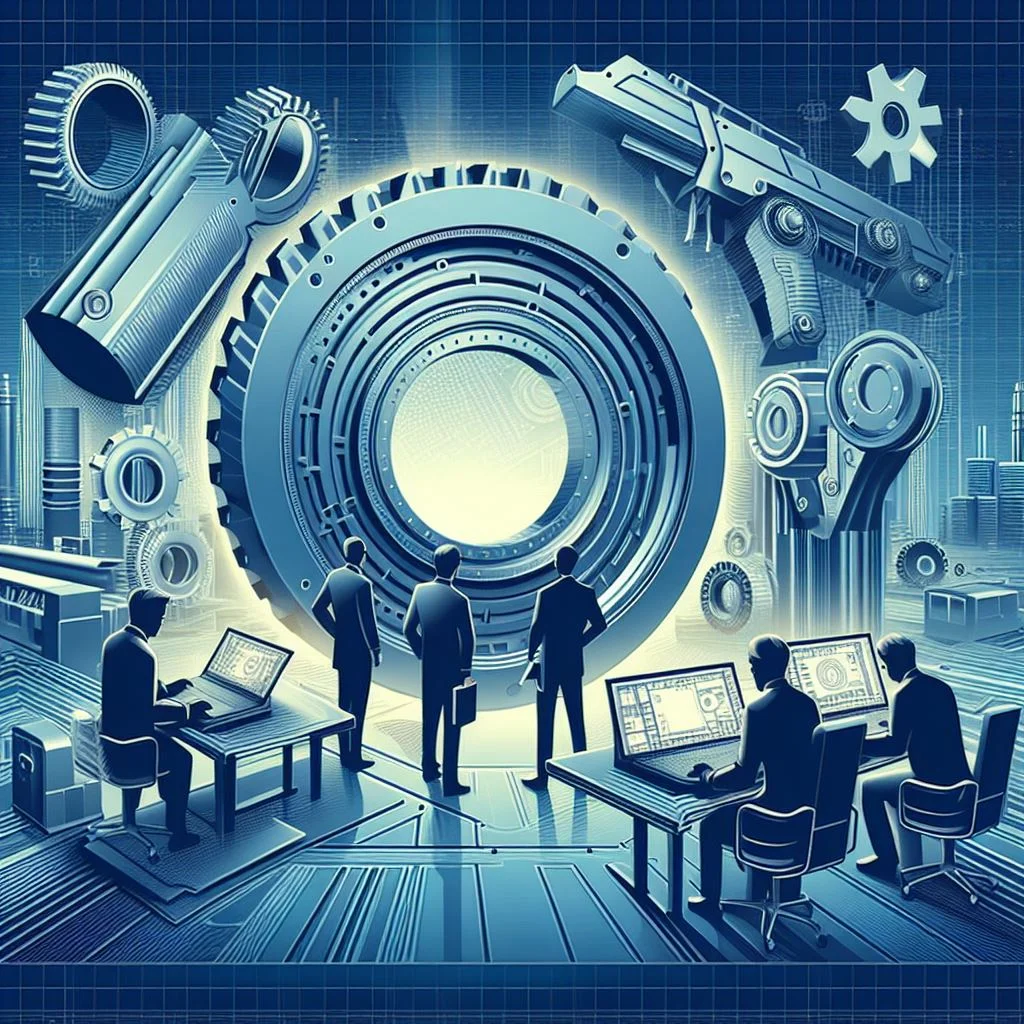
Furthermore, the integration of Artificial Intelligence (AI) has introduced a new dimension to CAD sheet metal design. AI algorithms are increasingly being employed to analyze vast datasets, identify patterns, and optimize designs. This level of intelligent automation not only accelerates the design phase but also contributes to more efficient material usage and cost-effectiveness. As AI continues to evolve, its role in sheet metal design is likely to expand, pushing the boundaries of what is achievable in terms of complexity and innovation.
Cloud-based collaboration tools have also become indispensable in the realm of CAD sheet metal design. Design teams are no longer bound by geographical constraints, as cloud platforms facilitate real-time collaboration and communication. This has significantly streamlined the exchange of ideas and feedback, resulting in more cohesive and well-coordinated design processes. The ability to access design files and collaborate remotely has become a cornerstone of modern sheet metal design workflows.
Sustainability is another critical aspect gaining prominence in CAD sheet metal design. Designers are increasingly mindful of the environmental impact of their creations and are leveraging CAD technologies to develop sustainable solutions. The ability to simulate and analyze the environmental footprint of sheet metal designs enables the identification of eco-friendly alternatives, ultimately contributing to a more sustainable future for the manufacturing industry.
In addition to these advancements, the incorporation of advanced simulation techniques has become a game-changer in the field. Virtual testing and simulations enable designers to evaluate the performance of sheet metal components under various conditions without the need for physical prototypes. This not only reduces the time and resources required for testing but also minimizes the likelihood of errors, ensuring that the final product meets the highest standards of quality and reliability.
As we navigate the future of sheet metal design, the synergy between CAD technologies and emerging trends continues to redefine the industry. The adoption of 3D printing has opened up new possibilities in fabrication, allowing for the creation of intricate and customized sheet metal components. Additive manufacturing processes driven by CAD designs offer unparalleled flexibility and efficiency in producing complex geometries that were once challenging to achieve through traditional methods.
Augmented Reality (AR) is making its mark in sheet metal assembly processes. By overlaying digital information onto the physical assembly environment, AR technologies enhance precision and reduce errors during fabrication and assembly stages. This integration of digital information into the real-world context ensures that sheet metal components fit seamlessly into the larger assembly, minimizing rework and optimizing the entire production process.
However, the journey towards the future of sheet metal design is not without its challenges. The rapid pace of technological advancements requires professionals in the field to continually update their skills and stay abreast of the latest trends. Additionally, the increased complexity introduced by advanced technologies necessitates a thorough understanding of their implications on design, fabrication, and assembly processes.
Evolution of CAD in Sheet Metal Design
The evolution of CAD in sheet metal design is a fascinating journey that spans several decades, marked by significant milestones and transformative technological advancements. In its early days, Computer-Aided Design emerged as a revolutionary concept, challenging traditional manual drafting methods. The advent of CAD brought about a paradigm shift, introducing a digital platform that allowed designers to create, modify, and analyze sheet metal designs with unprecedented precision.
As technology advanced, CAD systems evolved from rudimentary two-dimensional representations to sophisticated three-dimensional modeling environments. This transition empowered designers to visualize and manipulate sheet metal components in a more realistic and immersive manner. The introduction of parametric design further enhanced CAD capabilities, enabling designers to establish relationships between various geometric elements. This breakthrough allowed for dynamic changes in the design, facilitating greater flexibility and adaptability.
Over the years, CAD in sheet metal design has played a pivotal role in streamlining the entire design process. From conceptualization to prototyping, CAD tools have become indispensable in ensuring accuracy and efficiency. Key milestones include the integration of feature-based modeling, which enabled the creation of complex sheet metal structures with ease.
Technological advancements such as direct modeling and synchronous technology have further refined the design process by providing real-time editing capabilities. These innovations empower designers to make instant modifications, reducing design cycle times and enhancing overall productivity.
Today, CAD in sheet metal design stands at the forefront of innovation, with cloud-based collaboration, artificial intelligence, and advanced simulation techniques reshaping the landscape. The journey from humble beginnings to the present day reflects the relentless pursuit of excellence and efficiency in sheet metal design facilitated by CAD technologies.
Parametric Design: Shaping the Future
Parametric design has emerged as a transformative force in the realm of sheet metal fabrication, revolutionizing the way engineers and designers approach their craft. At its core, parametric modeling is a design approach that involves the use of parameters or variables to create dynamic and flexible models. This methodology brings a profound shift in the traditional design process, allowing for unparalleled flexibility and adaptability in sheet metal design.
In the context of sheet metal fabrication, parametric design enables engineers to make dynamic changes and adjustments to their models with ease. This newfound flexibility is a game-changer, especially in industries where precision and customization are paramount. Engineers can modify parameters such as dimensions, angles, and shapes, and the entire design adapts accordingly. This not only accelerates the design process but also facilitates rapid prototyping and iteration.
One of the key advantages of parametric modeling in sheet metal design is its ability to handle complex geometries effortlessly. Engineers can create intricate and sophisticated designs, knowing that any modifications can be seamlessly incorporated into the model. This dynamic approach enhances design flexibility, enabling manufacturers to respond quickly to changes in specifications or market demands.
Moreover, parametric design fosters a more efficient and collaborative design process. Teams can work concurrently on different aspects of a project, knowing that modifications made by one team member will seamlessly integrate with the overall design. This collaborative aspect of parametric modeling contributes to shorter design cycles and, ultimately, faster time-to-market for sheet metal products.
Integration of Artificial Intelligence
In the realm of CAD sheet metal design, the integration of Artificial Intelligence (AI) marks a significant leap forward. AI algorithms play a pivotal role in automating various aspects of the design process, ushering in a new era of intelligent automation. One key contribution of AI in sheet metal design is its ability to optimize designs dynamically. By analyzing vast datasets and considering multiple design parameters, AI algorithms can generate optimized designs that meet specified criteria, such as structural integrity, material efficiency, and manufacturing constraints.
Moreover, AI brings efficiency to the forefront by streamlining workflows and reducing manual intervention. Design iterations that traditionally took significant time and effort can now be accomplished swiftly, thanks to the computational prowess of AI. This not only accelerates the design phase but also allows engineers to explore a multitude of design options in a shorter timeframe, fostering innovation.
The intelligent automation facilitated by AI extends beyond design optimization. AI algorithms can learn from historical design data, identifying patterns and trends that humans might overlook. This capability enhances the decision-making process, aiding designers in making informed choices based on a wealth of data.
In essence, the integration of AI in CAD sheet metal design is a transformative force, bringing efficiency, optimization, and innovative problem-solving to the forefront. As AI continues to evolve, its impact on the sheet metal fabrication industry is poised to grow, unlocking new possibilities and shaping the future of design processes.
Cloud-Based Collaboration in Sheet Metal Design
The advent of cloud-based collaboration tools has revolutionized the landscape of sheet metal design, fostering a new era of seamless communication and collaboration among geographically dispersed teams. In the realm of sheet metal design, where precision and coordination are paramount, these platforms offer a myriad of benefits that significantly enhance the overall design process.
One of the primary advantages is the real-time collaboration capabilities that cloud-based tools provide. Design teams spread across different locations can work concurrently on a project, making instant updates and modifications visible to all members. This real-time collaboration eliminates delays caused by traditional file-sharing methods, ensuring that all team members are on the same page throughout the design phase.
Furthermore, cloud-based collaboration facilitates effective version control. Design iterations and modifications are tracked automatically, preventing the confusion that can arise from multiple versions of a design circulating among team members. This not only streamlines the collaborative process but also enhances overall project efficiency.
In addition to real-time collaboration and version control, cloud-based tools enhance accessibility. Team members can access the design files and project data from anywhere with an internet connection. This accessibility is particularly beneficial in a globalized industry, allowing international teams to collaborate seamlessly without the constraints of time zones or physical proximity.
Moreover, these collaboration tools often come equipped with communication features such as chat and comment threads directly integrated into the design environment. This ensures that discussions and feedback on specific design elements are consolidated within the platform, promoting a more organized and efficient communication flow.
Sustainable Sheet Metal Design Practices
The global shift towards sustainable practices has undeniably influenced various industries, and sheet metal design is no exception. In recent years, there has been a growing emphasis on incorporating eco-friendly principles into the fabrication process. This heightened awareness has led to the integration of sustainable sheet metal design practices, supported and enhanced by advanced Computer-Aided Design (CAD) technologies.
As the demand for environmentally conscious solutions continues to rise, CAD plays a crucial role in facilitating the creation of sheet metal designs that align with sustainability goals. CAD tools enable designers to optimize material usage, reduce waste, and enhance overall efficiency in the production process. Through parametric modeling and simulation techniques, designers can analyze the environmental impact of different design iterations, making informed decisions that prioritize sustainability.
Moreover, CAD technologies empower designers to explore alternative materials and manufacturing methods that have a lower environmental footprint. By simulating and visualizing the life cycle of sheet metal products, designers can identify areas for improvement and implement changes that contribute to a more sustainable end product.
In essence, the marriage of CAD and sustainable sheet metal design practices not only addresses current environmental concerns but also sets the stage for a future where the entire industry embraces eco-conscious approaches. This synergy allows for innovative solutions that not only meet functional and aesthetic requirements but also adhere to the principles of responsible and sustainable design. As we continue to navigate the evolving landscape of sheet metal fabrication, the integration of CAD technologies remains pivotal in fostering a greener and more sustainable future for the industry.
Conclusion:
In conclusion, the rapidly evolving landscape of sheet metal design is undoubtedly shaped by the pivotal role of Computer-Aided Design (CAD). As we navigate the future of sheet metal fabrication, several key takeaways emerge, underscoring the transformative impact of CAD technologies on the industry.
One of the primary takeaways is the unprecedented flexibility afforded by parametric design. The ability to make dynamic changes to designs and easily adapt to evolving project requirements is a game-changer. This flexibility not only enhances creativity but also streamlines the design process, allowing for greater efficiency and responsiveness to client needs. As CAD tools continue to advance, parametric design is poised to become even more integral to the sheet metal design process.
Artificial Intelligence (AI) stands out as another driving force behind the future of sheet metal design. AI algorithms contribute to intelligent automation, optimizing designs based on historical data and predictive analytics. This not only accelerates the design process but also minimizes errors, resulting in more accurate and cost-effective fabrication. As AI continues to evolve, its integration into CAD for sheet metal design promises even greater strides in efficiency and innovation.
Cloud-based collaboration tools play a crucial role in breaking down geographical barriers and fostering seamless teamwork. The future of sheet metal design will likely see an increased reliance on these platforms, enabling design teams to collaborate in real-time, share ideas, and collectively contribute to the success of projects. The accessibility and ease of collaboration offered by cloud-based tools are set to redefine the dynamics of teamwork in the sheet metal design realm.
Sustainability emerges as a key consideration for the future of sheet metal design. CAD technologies play a vital role in creating environmentally-friendly designs by optimizing material usage and minimizing waste. As the industry continues to prioritize sustainable practices, CAD will be at the forefront, driving innovations that align with eco-friendly principles.
The advent of advanced simulation techniques within CAD further solidifies its importance in sheet metal design. Virtual testing and simulations not only enhance design accuracy but also reduce the need for physical prototypes, saving both time and resources. This trend towards more efficient and precise simulation tools is expected to continue, revolutionizing how sheet metal designs are validated and refined.
3D printing, coupled with CAD advancements, is ushering in a new era in sheet metal fabrication. The ability to translate intricate designs into physical objects through additive manufacturing processes opens up possibilities for complex and customized sheet metal components. This technology is likely to play an increasingly integral role in prototyping and small-scale production, offering a level of detail and customization previously unattainable.
Augmented Reality (AR) is set to revolutionize the assembly processes in sheet metal fabrication. By overlaying digital information onto the physical environment, AR enhances precision during assembly, reducing errors and improving overall efficiency. The integration of AR into CAD for sheet metal design is a step towards creating more intuitive and error-proof assembly processes.
As we look ahead, the challenges of integrating these emerging technologies into sheet metal design are apparent. However, with challenges come opportunities for growth and innovation. Staying informed about the latest advancements in CAD for sheet metal design and actively adapting to the evolving landscape will be crucial for professionals in the field.