- Understanding Multiphysics Simulation
- Expanding the Understanding:
- The Dynamics of Integration
- Applications Across Industries
- Aerospace Engineering
- Automotive Design
- Electronics and Electromagnetics
- Realizing Complexity in Simplicity
- User-Friendly Interface
- Parametric Optimization
- Case Studies: Multiphysics in Action
- Heat Dissipation in Electronics
- Fluid-Structure Interaction in Mechanical Systems
- Future Trends and Innovations
- AI Integration
- Augmented Reality (AR) for Simulation Visualization
- Conclusion
In the realm of engineering and design, where precision and efficiency reign supreme, mastering the art of simulation stands as a key to unlocking the gateway to innovation. Among the array of tools available, SolidWorks has emerged as a powerhouse in 3D CAD modeling, consistently evolving to meet the ever-growing demands of complex assignments. It is within this dynamic environment that the advent of Multiphysics Simulation has brought about a transformative shift in the way engineers approach problem-solving.
SolidWorks, renowned for its user-friendly interface and robust simulation capabilities, has embraced the concept of Multiphysics Simulation to address the multifaceted challenges that engineers encounter. Unlike traditional simulation methods that often compartmentalize different aspects of a system, Multiphysics Simulation takes a holistic approach by simultaneously considering multiple physical phenomena within a given environment. This not only mirrors real-world scenarios more accurately but also empowers engineers to analyze the intricate interplay between various physics domains.
As engineers strive to push the boundaries of what is possible, SolidWorks Multiphysics Simulation becomes an invaluable asset in their toolkit. It seamlessly integrates a spectrum of physics, encompassing structural mechanics, fluid dynamics, heat transfer, and electromagnetics. This amalgamation of disciplines enables a comprehensive analysis, allowing for a nuanced understanding of how different forces and factors interact within a system. Consequently, engineers can make informed decisions and fine-tune their designs with a level of precision that was previously unattainable.
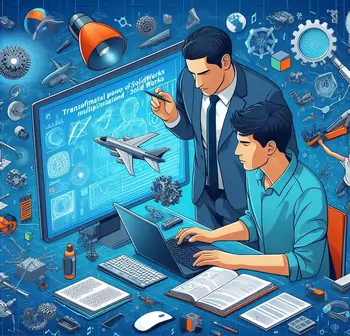
The applications of Multiphysics Simulation in SolidWorks are far-reaching, spanning across diverse industries. In the aerospace sector, where the integrity of components and aerodynamic performance are critical, engineers utilize this simulation technique to optimize designs for enhanced safety and efficiency. Similarly, in the automotive industry, Multiphysics Simulation aids in striking the delicate balance between structural strength, heat dissipation, and aerodynamics, paving the way for the creation of vehicles that are both aesthetically pleasing and technologically advanced.
In the electronics realm, where the miniaturization of components and thermal management are constant challenges, SolidWorks Multiphysics Simulation provides a holistic view of the system. By predicting how heat dissipates within tightly packed electronic components, engineers can devise effective cooling solutions, ensuring optimal performance and reliability.
What sets SolidWorks apart in the realm of Multiphysics Simulation is its commitment to making complex tools accessible. The user-friendly interface allows engineers to seamlessly navigate between different physics modules, adjusting parameters and running simulations with ease. This accessibility plays a crucial role in democratizing simulation tools, enabling engineers of varying expertise levels to harness the power of Multiphysics Simulation.
Moreover, SolidWorks goes beyond mere simulation by offering parametric optimization capabilities. This feature allows engineers to iterate through design variations, automatically adjusting parameters to achieve the best possible outcome. The result is an accelerated product development cycle, significantly reducing time to market and fostering a culture of continuous improvement.
In real-world scenarios, Multiphysics Simulation in SolidWorks unfolds as a game-changer. Consider a situation where electronic components are tightly packed within a confined space. Traditional simulation methods may overlook the intricate interaction between structural mechanics and heat transfer. However, SolidWorks Multiphysics Simulation steps in to predict how heat generated by these components dissipates, empowering engineers to implement strategic cooling solutions and prevent potential overheating issues.
Similarly, in mechanical systems involving fluid flow, understanding the interaction between the structure and the fluid is crucial. SolidWorks Multiphysics Simulation aids engineers in analyzing fluid-structure interaction, providing insights that are instrumental in designing components capable of withstanding the forces exerted by fluid flow.
As technology continues to advance, the future of Multiphysics Simulation in SolidWorks holds exciting possibilities. The integration of Artificial Intelligence (AI) is on the horizon, promising enhanced simulation accuracy and efficiency. Additionally, the exploration of Augmented Reality (AR) for simulation visualization hints at a future where engineers can interact with and visualize simulations in real time, ushering in a new era of immersive design experiences. For assistance with your Finite Element Analysis assignment, these advancements in technology offer promising avenues to explore, potentially enhancing your understanding and capabilities in this field.
Understanding Multiphysics Simulation
Before delving into the specifics, let's unravel the concept of Multiphysics Simulation. In essence, it involves the simultaneous simulation of multiple physical phenomena that interact with each other within a given system. SolidWorks, renowned for its robust simulation capabilities, extends its prowess to incorporate various physics domains, fostering a holistic approach to problem-solving.
Expanding the Understanding:
Multiphysics Simulation, at its core, recognizes that real-world systems are rarely governed by a single set of physical principles. The synergy of diverse physics—structural mechanics, fluid dynamics, heat transfer, and electromagnetics—mirrors the complexity inherent in many engineering applications. This approach acknowledges the interconnectedness of different physical phenomena, ensuring that simulations are not siloed but reflective of the intricate interplay between various forces.
SolidWorks, as a stalwart in the realm of engineering software, doesn't merely facilitate the analysis of individual physics components but intertwines them seamlessly. This integration empowers engineers to discern the nuances of how these different aspects influence each other, providing a comprehensive understanding that goes beyond the sum of its parts.
Moreover, this holistic simulation approach aligns with the real-world behavior of complex systems. Whether it's a mechanical component exposed to fluid dynamics or an electronic device generating heat, the ability to simulate the collective impact of these physical factors is indispensable for accurate predictions and effective problem-solving.
The Dynamics of Integration
SolidWorks Multiphysics Simulation transcends the conventional limits of structural analysis, ushering in a new era of simulation capabilities. By seamlessly blending structural mechanics, fluid dynamics, heat transfer, and electromagnetics, SolidWorks establishes a comprehensive simulation environment that mirrors the complexity of real-world scenarios. This integration isn't merely a sum of its parts; it's a symphony of physics working in tandem. Engineers gain the ability to explore the intricate dance between these diverse physical phenomena, leading to a more nuanced and accurate understanding of how various forces and elements interact within a given system. This holistic approach elevates simulation accuracy and empowers engineers to make informed decisions that resonate with the intricacies of practical applications.
Applications Across Industries
Multiphysics Simulation in SolidWorks extends its transformative capabilities across diverse industries, becoming an indispensable tool for engineers grappling with multifaceted challenges. In the realm of Aerospace Engineering, where precision is paramount, SolidWorks enables engineers to conduct intricate simulations, evaluating the structural integrity of components while simultaneously considering fluid dynamics. This holistic approach ensures aircraft designs not only meet safety standards but also optimize performance and fuel efficiency.
In the realm of Automotive Design, where the marriage of aesthetics and functionality is crucial, SolidWorks Multiphysics Simulation plays a pivotal role. Automotive engineers leverage the tool to strike a delicate balance between structural strength, heat dissipation, and aerodynamics. The simulations guide the development of vehicles that not only boast eye-catching designs but also adhere to rigorous performance standards and fuel efficiency targets.
Moving into the domain of Electronics and Electromagnetics, SolidWorks proves its mettle by addressing critical concerns such as electromagnetic interference (EMI) and thermal management. Engineers can delve into the intricate details of circuit designs, predicting potential issues and optimizing electronic components for reliability and longevity.
This adaptability across industries showcases the versatility of Multiphysics Simulation in SolidWorks, positioning it as a cornerstone for innovation in engineering and design. As technology evolves and challenges become more complex, SolidWorks continues to be at the forefront, empowering engineers to push the boundaries of what's possible in their respective fields.
Aerospace Engineering
In the aerospace industry, precision is not just a requirement; it's a non-negotiable imperative. SolidWorks Multiphysics Simulation plays a pivotal role in meeting this demand. Engineers harness its capabilities to meticulously evaluate the structural integrity of components, ensuring that every part can withstand the extreme conditions inherent in aerospace applications. Moreover, SolidWorks enables a detailed analysis of fluid dynamics around aircraft surfaces, a critical aspect of aerodynamic performance. This level of simulation precision empowers aerospace engineers to optimize designs, pushing the boundaries of performance and safety in an industry where the margin for error is virtually nonexistent.
Automotive Design
Automotive engineers face a perpetual challenge in achieving the delicate balance between structural strength, heat dissipation, and aerodynamics. SolidWorks Multiphysics Simulation emerges as a reliable ally in navigating this complex terrain. By enabling a comprehensive examination of these interconnected factors, SolidWorks facilitates the creation of vehicles that transcend mere aesthetics. The simulations delve into the intricacies of structural integrity, ensuring the vehicle's robustness, while also addressing heat dissipation and aerodynamic efficiency. The result is a synergy of form and function, where vehicles not only look impressive but also operate with unparalleled efficiency on the road.
Electronics and Electromagnetics
In the realm of electronics, where reliability is paramount, SolidWorks Multiphysics Simulation takes center stage. Electronic components are not immune to challenges such as electromagnetic interference (EMI) and thermal management issues. SolidWorks provides a sophisticated platform for engineers to foresee and address these potential pitfalls. The simulations enable a proactive approach, ensuring the reliability and longevity of electronic components. By identifying and mitigating issues related to EMI and thermal management, SolidWorks empowers designers to create electronic systems that not only meet but exceed the stringent standards of reliability demanded by modern technology.
Realizing Complexity in Simplicity
Realizing Complexity in Simplicity is a hallmark of SolidWorks Multiphysics Simulation, where the software's user-friendly interface plays a pivotal role. The intuitive design ensures that engineers, regardless of their expertise level, can navigate seamlessly through the various physics modules. This accessibility fosters collaboration within diverse engineering teams, enabling professionals from different backgrounds to contribute their insights to the simulation process.
SolidWorks further simplifies the complexity through its parametric optimization capabilities. This feature allows engineers to explore a multitude of design variations effortlessly. By automating the adjustment of parameters, the software streamlines the iterative process of refining designs. This not only accelerates the product development cycle but also empowers engineers to achieve optimal solutions efficiently.
The parametric optimization feature in SolidWorks Multiphysics Simulation serves as a virtual playground for engineers, allowing them to experiment with different design scenarios and fine-tune parameters in real-time. This interactive and iterative approach not only enhances the overall efficiency of the design process but also encourages innovation by providing engineers with the flexibility to explore creative solutions to complex problems.
User-Friendly Interface
In the realm of Multiphysics Simulation, SolidWorks takes pride in ensuring that complexity does not equate to convoluted processes. One of the standout features is its user-friendly interface, which serves as a beacon for engineers navigating the intricate world of simulation. The intuitive design allows users to seamlessly transition between different physics modules, offering a smooth and accessible experience. This simplicity is not a compromise but a strategic choice, democratizing simulation tools and making them accessible to engineers with varying levels of expertise.
Beyond the interface, SolidWorks Multiphysics Simulation embraces parametric optimization, adding another layer of simplicity to the complexity of simulation. Engineers can effortlessly iterate through design variations, with the software automatically adjusting parameters to find the optimal solution. This dynamic approach accelerates the product development cycle, enabling engineers to fine-tune designs swiftly and efficiently.
Parametric Optimization
In the dynamic landscape of engineering, SolidWorks Multiphysics Simulation is not confined to mere analysis; it goes a step further by facilitating parametric optimization. This transformative capability empowers engineers to navigate through diverse design variations effortlessly. Through an automated process, parameters are dynamically adjusted to ascertain the optimal outcome, ensuring that the final design aligns perfectly with predefined performance criteria.
This iterative approach to parametric optimization becomes a game-changer in the product development cycle. By streamlining the design refinement process, engineers can significantly reduce the time to market for their innovations. The ability to swiftly iterate and fine-tune design parameters enables teams to achieve optimal solutions efficiently, fostering a more agile and responsive product development environment.
SolidWorks, with its commitment to user-centric design and innovation, places the power of parametric optimization in the hands of engineers. The simplicity and effectiveness of this feature underscore SolidWorks' dedication to not just meeting industry standards but surpassing them, allowing engineering teams to push the boundaries of what is possible in the realm of product design and development.
Case Studies: Multiphysics in Action
Embarking on a journey through real-world applications, Multiphysics Simulation in SolidWorks becomes more tangible when examined through case studies. These practical scenarios exemplify the versatility and efficacy of integrating multiple physics in complex assignments.
Consider the realm of heat dissipation in electronics, a critical concern in modern electronic devices. Multiphysics Simulation facilitates a comprehensive analysis, predicting how heat generated by tightly packed components dissipates within confined spaces. Engineers can then strategically implement cooling solutions, preventing overheating and ensuring optimal performance and longevity of electronic systems. This capability is particularly invaluable in the fast-paced electronics industry, where efficiency and reliability are paramount.
In mechanical systems involving fluid flow, the interaction between the structure and the fluid is a key consideration. Multiphysics Simulation in SolidWorks enables engineers to delve into fluid-structure interaction, a critical aspect in the design of mechanical components. By understanding how the structure responds to forces exerted by fluid flow, engineers can optimize designs to withstand these dynamic forces, ensuring the durability and efficiency of mechanical systems.
These case studies underscore the transformative power of Multiphysics Simulation, illustrating how it goes beyond theoretical analysis to drive tangible improvements in real-world applications. SolidWorks continues to empower engineers with tools that not only simulate but also inform and guide the design process, fostering innovation and efficiency across diverse industries.
Heat Dissipation in Electronics
Imagine a scenario where electronic components are tightly packed within a confined space, such as in modern electronic devices or intricate circuitry. In such environments, the generation of heat is inevitable due to the continuous operation of electronic components. SolidWorks Multiphysics Simulation proves invaluable in predicting how this heat dissipates throughout the system. Engineers can gain insights into temperature distributions and identify potential hotspots. Armed with this information, they can implement strategic cooling solutions, whether through innovative heat sink designs, improved ventilation, or other thermal management techniques. This proactive approach not only prevents overheating issues but also ensures optimal performance and longevity of electronic components.
Fluid-Structure Interaction in Mechanical Systems
In the realm of mechanical systems where fluid flow plays a pivotal role, understanding the intricate interaction between the structure and the fluid is of paramount importance. SolidWorks Multiphysics Simulation excels in analyzing fluid-structure interaction, providing engineers with a comprehensive understanding of how mechanical components respond to fluid forces. This capability is instrumental in designing components that can withstand the dynamic forces exerted by fluid flow, be it in pipelines, pumps, or other fluid-carrying systems. By simulating and optimizing these interactions, engineers can fine-tune designs to enhance structural integrity, reduce wear and tear, and ultimately improve the overall efficiency and reliability of mechanical systems.
Future Trends and Innovations
As we gaze into the future of engineering simulation, it becomes apparent that SolidWorks Multiphysics is poised to embrace transformative trends and innovations. One such trend is the integration of Artificial Intelligence (AI) into the simulation workflow. AI has the potential to elevate simulation accuracy and efficiency by learning from vast datasets and optimizing parameters dynamically. SolidWorks, being a pioneer in the field, is actively exploring ways to harness AI capabilities, enabling engineers to achieve even more precise and rapid simulations.
Another groundbreaking avenue on the horizon is the integration of Augmented Reality (AR) for simulation visualization. Imagine engineers donning AR devices to interact with and visualize simulations in real-time, fostering a deeper understanding of complex dynamics. SolidWorks recognizes the potential of AR and is at the forefront of developing applications that bring simulations to life in immersive ways. This convergence of simulation and AR not only enhances the user experience but also opens up new possibilities for collaborative design and decision-making.
In this era of rapid technological advancement, SolidWorks continues to be a vanguard, adapting to and driving the evolution of engineering simulation. The synergy of AI and AR with Multiphysics Simulation holds the promise of a future where engineers can not only simulate complex scenarios with unprecedented accuracy but also experience and manipulate these simulations in ways that were once confined to the realm of science fiction. The journey towards these futuristic innovations underscores SolidWorks' commitment to shaping the next frontier of engineering excellence.
AI Integration
As Artificial Intelligence continues to shape the future of engineering, the convergence of AI and Multiphysics Simulation holds immense promise. SolidWorks, known for its unwavering commitment to innovation, is at the forefront of this transformative journey. The integration of AI into Multiphysics Simulation is poised to revolutionize the way engineers approach complex assignments.
In this symbiotic relationship, AI brings its predictive prowess and adaptive learning capabilities to enhance simulation accuracy and efficiency. Imagine a scenario where AI algorithms analyze simulation data in real-time, identifying patterns and optimizing parameters autonomously. This synergy between AI and Multiphysics Simulation not only expedites the design process but also unveils novel insights, pushing the boundaries of what is achievable in engineering simulation.
Augmented Reality (AR) for Simulation Visualization
In tandem with AI integration, SolidWorks is actively exploring the integration of Augmented Reality (AR) into Multiphysics Simulation. This venture into AR applications unveils a new dimension of visualization and interaction for engineers.
The marriage of Augmented Reality and Multiphysics Simulation allows engineers to step into a virtual world where simulations come to life in real-time. This immersive experience transcends traditional two-dimensional representations, offering engineers the ability to interact with and manipulate simulations in a three-dimensional space. It not only enhances the understanding of complex physics but also facilitates collaboration among multidisciplinary teams, fostering a shared and enriched simulation experience.
As SolidWorks pioneers this integration, the future of engineering simulation promises to be not just accurate and efficient but also visually captivating and collaborative, laying the groundwork for the next era of innovation.
Conclusion
In conclusion, the incorporation of Multiphysics Simulation into SolidWorks marks a significant milestone in the dynamic world of engineering simulation. The seamless integration of multiple physics domains within the SolidWorks platform not only addresses the immediate challenges faced by engineers but also propels the entire field into a realm of unparalleled possibilities.
The real strength of SolidWorks Multiphysics Simulation lies in its ability to empower engineers to navigate through the intricacies of assignments previously deemed too complex. The traditional boundaries of simulation are surpassed as structural mechanics, fluid dynamics, heat transfer, and electromagnetics converge harmoniously. This convergence enables a more holistic understanding of the behavior of systems in the real world, where multiple physical phenomena often interact concurrently.
The versatility of SolidWorks Multiphysics Simulation finds application across diverse industries, adding value to engineering processes in ways that were once considered unattainable. In the aerospace sector, for instance, engineers can scrutinize not only the structural integrity of components but also the fluid dynamics surrounding aircraft surfaces. This comprehensive analysis translates into safer, more efficient designs.
Similarly, automotive engineers benefit from the integration of SolidWorks Multiphysics Simulation in balancing the interplay of structural strength, heat dissipation, and aerodynamics. The result is a harmonious blend of form and function, creating vehicles that not only exude aesthetic appeal but also deliver optimal performance.
In the realm of electronics, where thermal management and electromagnetic interference pose constant challenges, SolidWorks Multiphysics Simulation emerges as a guiding light. Engineers can proactively address these challenges, ensuring the reliability and longevity of electronic components.
What sets SolidWorks apart is its commitment to simplifying complexity. The user-friendly interface facilitates a seamless transition between different physics modules, allowing engineers to adjust parameters and run simulations effortlessly. This accessibility democratizes the use of simulation tools, enabling engineering teams to embrace the power of Multiphysics Simulation.
Moreover, the parametric optimization feature in SolidWorks Multiphysics Simulation is a game-changer. Engineers can iterate through design variations, automatically adjusting parameters to achieve optimal outcomes. This iterative process not only accelerates the product development cycle but also fosters a culture of continuous improvement within engineering teams.
In essence, SolidWorks Multiphysics Simulation is not merely a tool; it is a catalyst for innovation. As the engineering landscape continues to evolve, the integration of Artificial Intelligence (AI) into Multiphysics Simulation is poised to be the next frontier. SolidWorks, with its forward-looking approach, is well-positioned to lead the way in harnessing the potential of AI to further enhance simulation accuracy and efficiency.