- Understanding Thermal Stress Analysis
- Performing Thermal Stress Analysis in SolidWorks
- Setting Up Thermal Boundary Conditions
- Material Properties and Thermal Conductivity
- Conducting a Thermal Simulation
- Interpreting Thermal Stress Results
- Analyzing Thermal Stress Distribution
- Identifying Critical Points and Design Optimization
- Real-World Applications and Case Studies
- Case Study 1: Automotive Component Design
- Case Study 2: Electronics Enclosure Design
- Tips for Efficient Thermal Stress Analysis in SolidWorks
- Optimizing Mesh for Thermal Simulations
- Utilizing Parametric Studies for Temperature Variations
- Challenges and Limitations
- Addressing Common Challenges in Thermal Stress Analysis
- Understanding the Limitations of Thermal Simulation
- Conclusion
In the realm of mechanical engineering and design, where innovation and precision are paramount, an in-depth comprehension of how materials react to temperature fluctuations is indispensable. The dynamic interplay between materials and temperature lies at the heart of creating structures that stand the test of time and perform reliably under diverse conditions. This blog aims to unravel the intricate world of Thermal Stress Analysis within the context of SolidWorks, providing a comprehensive exploration of its significance, methodologies, and real-world applications. If you need help with your finite element analysis assignment, don't hesitate to reach out for expert support.
Temperature is not merely an environmental factor but a critical force that can significantly impact the structural integrity and performance of engineered components. Understanding how materials respond to thermal variations is akin to wielding a powerful tool in the engineer's arsenal. It allows for the prediction and mitigation of potential issues, ensuring that designs are not only functionally robust but also durable over the long haul.
The field of Thermal Stress Analysis becomes particularly crucial in scenarios where temperature differentials are inherent, such as in the automotive, aerospace, and electronics industries. The ability to simulate and analyze how materials expand, contract, and deform under varying temperatures is indispensable for creating designs that can withstand the rigors of real-world conditions. SolidWorks, a leading software in the realm of computer-aided design and engineering simulations, provides a sophisticated platform for engineers to explore and understand these thermal dynamics.
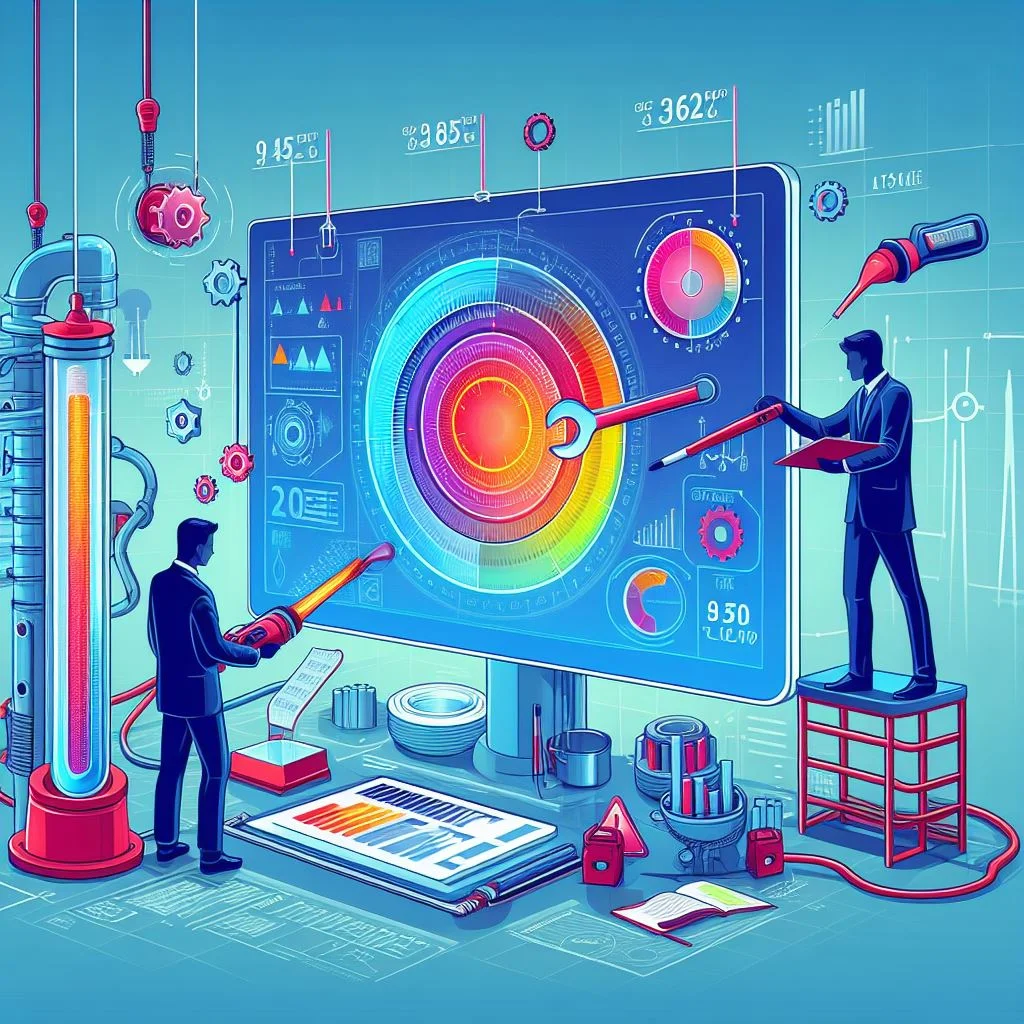
As we embark on this exploration, it's essential to recognize the profound impact that Thermal Stress Analysis can have on the entire design process. It goes beyond theoretical considerations and delves into the practical aspects of ensuring that what is conceptualized on the drawing board translates seamlessly into a physical reality capable of meeting and exceeding expectations. The methodologies employed in Thermal Stress Analysis using SolidWorks are not mere exercises in simulation; they are proactive measures to enhance the reliability and performance of designs.
This blog will serve as a beacon, guiding engineers and design enthusiasts through the nuanced terrain of Thermal Stress Analysis. We will unravel the intricacies of setting up thermal boundary conditions, decipher the role of material properties and thermal conductivity, and demystify the process of conducting thermal simulations. Beyond the technicalities, we will delve into the art of interpreting thermal stress results, identifying critical points, and optimizing designs for enhanced resilience.
Moreover, as we navigate through real-world applications and case studies, we will witness the tangible impact of Thermal Stress Analysis on diverse projects. From designing automotive components that endure extreme temperature differentials to creating electronics enclosures that safeguard sensitive equipment, the applications are both varied and impactful.
In essence, this blog is not just a theoretical discourse on Thermal Stress Analysis; it is a practical guide infused with insights and wisdom drawn from real-world scenarios. Whether you are a seasoned engineer looking to refine your skills or a student venturing into the fascinating world of SolidWorks assignments, this exploration promises to be an enlightening journey. So, fasten your seatbelts as we embark on a voyage into the realm where temperature and engineering intricately converge, shaping the future of robust and reliable structures.
Understanding Thermal Stress Analysis
Thermal Stress Analysis serves as a fundamental tool in engineering simulation, particularly in the context of SolidWorks assignments. Within the SolidWorks environment, this analytical process relies heavily on Finite Element Analysis (FEA) to provide insights into the structural behavior of materials subjected to varying temperatures. By leveraging the principles of FEA, engineers can predict not only how materials will deform but also the stresses they will endure in response to different thermal conditions.
The crux of Thermal Stress Analysis lies in its ability to simulate and mimic real-world scenarios, enabling engineers to comprehend the intricate interplay between temperature variations and material response. It acts as a virtual testing ground where designs can be rigorously evaluated before any physical prototype is produced. This predictive capability proves invaluable in identifying potential weak points or areas of concern in a design, ultimately leading to enhanced structural robustness.
The significance of incorporating Thermal Stress Analysis into SolidWorks assignments cannot be overstated. One of its primary roles is the prevention of material failure. By subjecting a design to simulated temperature changes, engineers can identify critical points where excessive thermal stress may lead to structural compromise. This preemptive analysis empowers designers to refine their models, ensuring that the final product can withstand the rigors of real-world thermal conditions.
Moreover, Thermal Stress Analysis plays a pivotal role in optimizing designs for temperature fluctuations. In the dynamic field of engineering, where materials are constantly exposed to varying environmental conditions, the ability to anticipate and address thermal effects is paramount. Whether it's a component in a mechanical system, a structural element in a building, or an intricate part of an electronic device, understanding and mitigating thermal stresses are essential for ensuring longevity and reliability.
In essence, Thermal Stress Analysis in SolidWorks adds a layer of precision to the engineering process. It transcends mere theoretical considerations, providing tangible insights that can be applied to refine designs, enhance performance, and ensure the longevity and reliability of engineering solutions. The integration of Thermal Stress Analysis into SolidWorks assignments thus stands as a cornerstone in the pursuit of robust and resilient engineering designs.
Performing Thermal Stress Analysis in SolidWorks
Performing Thermal Stress Analysis in SolidWorks involves a meticulous process that goes beyond simply defining thermal boundary conditions. Once you've set up these conditions, the next crucial step is meshing, where the geometry is discretized into small elements for analysis. In SolidWorks, meshing is a pivotal aspect of simulation accuracy, as it directly influences the fidelity of your results.
Choosing an appropriate mesh size and type is essential. A fine mesh captures intricate details but demands more computational resources, while a coarse mesh reduces computational demands but might overlook subtle changes. Striking the right balance is key for an efficient and accurate analysis. SolidWorks provides various meshing options, including automatic and manual methods, allowing users to tailor their approach based on the specific requirements of the simulation.
Furthermore, the software offers the flexibility to refine the mesh in critical regions, ensuring a detailed examination where needed most. Understanding the intricacies of meshing in SolidWorks empowers engineers to optimize simulations, obtaining results that strike the right balance between accuracy and computational efficiency.
In addition to meshing, SolidWorks enables users to define material properties and thermal conductivity accurately, contributing to the precision of thermal simulations. By mastering these simulation techniques, engineers can confidently navigate the complexities of Thermal Stress Analysis and enhance the reliability of their designs.
Setting Up Thermal Boundary Conditions
Learn the step-by-step process of defining thermal boundary conditions in SolidWorks. This section will guide you through specifying temperatures, heat sources, and thermal loads to accurately simulate real-world thermal scenarios.
SolidWorks provides a user-friendly interface for setting up thermal boundary conditions. Begin by identifying the regions of your model that will be subjected to thermal loading. Specify the initial temperature conditions and any external heat sources. Whether you're dealing with conduction, convection, or radiation, SolidWorks offers a range of tools to accurately model these phenomena.
Understanding thermal boundary conditions is crucial for capturing the intricacies of heat transfer within your design. This knowledge empowers engineers to create simulations that closely mimic the actual operating conditions, resulting in more precise and reliable analyses.
Material Properties and Thermal Conductivity
Understand the role of material properties and thermal conductivity in Thermal Stress Analysis. Discover how SolidWorks allows you to assign accurate material data and optimize your simulations for enhanced accuracy.
The success of any thermal analysis hinges on the accurate representation of material properties. In SolidWorks, you have the flexibility to assign specific thermal properties to different materials within your model. This includes thermal conductivity, specific heat, and density. By incorporating precise material data, you ensure that your simulations mirror real-world conditions, allowing for more informed decision-making in the design process.
Optimizing for thermal conductivity is particularly crucial in scenarios where heat transfer plays a significant role. SolidWorks empowers engineers to explore various materials and their thermal characteristics, facilitating the selection of the most suitable materials for applications with specific thermal requirements.
Conducting a Thermal Simulation
A hands-on guide to running a thermal simulation in SolidWorks. Explore the simulation settings, solver options, and result interpretation. Gain insights into visualizing temperature distributions and identifying potential areas of concern.
Once thermal boundary conditions and material properties are set, the next step is to run the thermal simulation. SolidWorks provides a comprehensive set of simulation settings, allowing users to customize the analysis based on their specific requirements. Choose appropriate solver options to ensure accuracy and efficiency throughout the simulation process.
As the simulation progresses, SolidWorks generates detailed results, including temperature distributions across the model. Visualization tools enable engineers to identify hotspots, cold zones, and areas experiencing thermal stress. This insight is invaluable for making informed design decisions, optimizing the model, and ensuring it meets thermal performance criteria.
Interpreting Thermal Stress Results
In the realm of interpreting thermal stress results, it is essential to delve deeper into the intricacies of von Mises stress and its implications for design integrity. Beyond merely identifying stress concentrations, engineers must analyze the spatial distribution of thermal stresses to pinpoint critical regions in a model. These critical points often serve as indicators of potential structural vulnerabilities under varying temperature conditions.
Moreover, the color-coded stress contour plots provided by SolidWorks offer a visual representation of stress levels throughout the model. Engineers can use these plots to identify zones experiencing high thermal stress, enabling targeted interventions for design optimization. By understanding how materials respond to temperature changes, one can make informed decisions about material selection, geometry adjustments, or the addition of structural reinforcements.
Furthermore, interpreting thermal stress results involves considering the time-dependent aspects of temperature effects. SolidWorks allows for transient thermal analysis, enabling engineers to observe how stresses evolve over time. This capability is particularly valuable in scenarios where temperature fluctuations occur dynamically, such as in electronic devices subjected to varying operational loads.
Analyzing Thermal Stress Distribution
Dive into the post-simulation analysis phase. After running a Thermal Stress Analysis in SolidWorks, the next crucial step is interpreting the results. One key parameter to focus on is the von Mises stress, a scalar value that represents the combined effect of all the stresses in a material. Understand how to dissect this stress distribution map, identifying regions of high and low stress. Gain insights into the relationship between material properties, temperature variations, and stress concentrations, allowing for a nuanced understanding of how your model responds to thermal challenges.
In addition to von Mises stress, explore other stress components such as normal and shear stresses. This multifaceted analysis provides a comprehensive view of how different stress types manifest in your design under varying temperature conditions.
Identifying Critical Points and Design Optimization
With a clearer understanding of stress distribution, move on to identifying critical points in your design where thermal stress is most pronounced. These are the areas that demand special attention to prevent potential failure or deformation. SolidWorks offers tools to highlight these critical regions, enabling you to pinpoint vulnerabilities.
Once critical points are identified, embark on the journey of design optimization. Explore strategies to mitigate excessive thermal stress, such as modifying material properties, adjusting geometry, or refining the overall design. Through iterative optimization, enhance the structural integrity of your model, ensuring it can withstand the thermal challenges it may encounter in real-world applications.
In essence, the process of interpreting thermal stress results and optimizing designs is a dynamic and iterative one. By delving into these aspects of Thermal Stress Analysis in SolidWorks, you gain the ability to not only identify potential issues but also implement effective solutions, resulting in designs that are robust and resilient in the face of temperature-induced stresses.
Real-World Applications and Case Studies
In addition to the previously discussed case studies, exploring further real-world applications of Thermal Stress Analysis in SolidWorks unveils its versatile utility across various industries. Consider the realm of aerospace engineering, where components of aircraft and spacecraft undergo extreme temperature differentials during ascent, descent, and exposure to atmospheric conditions. Thermal Stress Analysis in SolidWorks proves instrumental in designing aerospace structures that can withstand these temperature variations, ensuring the safety and reliability of the vehicles.
Moreover, the renewable energy sector stands as another testament to the significance of Thermal Stress Analysis. In the design of solar panels, wind turbine components, and geothermal installations, understanding how materials respond to temperature fluctuations is critical for long-term performance. SolidWorks simulations aid engineers in optimizing the structural integrity of renewable energy systems, contributing to the sustainability and efficiency of these crucial technologies.
By delving into additional case studies across diverse industries, engineers can glean insights into the adaptability of Thermal Stress Analysis in SolidWorks. These applications underscore the methodology's universal relevance and emphasize its pivotal role in shaping the future of engineering across various disciplines.
Case Study 1: Automotive Component Design
Explore a real-world case study where Thermal Stress Analysis in SolidWorks played a pivotal role in designing a reliable automotive component. The project involved developing a critical component for a high-performance automobile, subject to extreme temperature differentials during operation. The challenges faced included ensuring the part's durability under rapid temperature changes, potential thermal expansion, and the need for weight optimization.
To address these challenges, engineers employed SolidWorks for a detailed Thermal Stress Analysis. The simulation helped identify potential weak points susceptible to thermal stresses, allowing for strategic reinforcement. By iteratively refining the design based on simulation results, the team achieved a robust and thermally resilient automotive component. The impact was significant – not only did it meet stringent performance requirements, but it also contributed to the overall efficiency and reliability of the vehicle.
Case Study 2: Electronics Enclosure Design
Delve into a case study highlighting the importance of Thermal Stress Analysis in the design of electronics enclosures. In this scenario, the challenge was to create an enclosure for sensitive electronic components subjected to varying operating temperatures. Thermal management was crucial to prevent overheating and ensure the longevity of the electronics.
SolidWorks simulations played a crucial role in this case study by providing insights into temperature distribution within the enclosure. By accurately modeling heat dissipation and thermal conductivity, engineers were able to optimize the selection of materials and design features. This resulted in an electronics enclosure that effectively mitigated thermal stresses, extended the lifespan of electronic components, and enhanced the overall reliability of the electronic system.
These real-world case studies underscore the practical applications of Thermal Stress Analysis in SolidWorks, demonstrating its instrumental role in overcoming challenges and achieving optimal design solutions.
Tips for Efficient Thermal Stress Analysis in SolidWorks
Optimizing the mesh is just the starting point for efficient Thermal Stress Analysis in SolidWorks. Beyond mesh refinement, consider employing adaptive meshing techniques to focus computational resources on areas experiencing significant temperature gradients or stress concentrations. SolidWorks provides advanced mesh controls that allow you to selectively refine the mesh based on specific criteria, ensuring a fine balance between simulation accuracy and computational efficiency.
Furthermore, leverage the power of parallel processing and distributed computing if your simulations demand higher computational resources. SolidWorks offers parallel processing capabilities, enabling you to significantly reduce simulation run times by distributing the workload across multiple processors or cores.
In addition to mesh optimization and parallel processing, utilize SolidWorks Simulation features such as submodeling to zoom in on critical regions of interest. Submodeling allows for more detailed analysis of specific areas without the need to simulate the entire model, offering a pragmatic approach to refining and validating the results in key regions.
By incorporating these advanced strategies into your Thermal Stress Analysis workflow, you can enhance the efficiency and precision of your simulations, ensuring that your SolidWorks assignments reflect real-world scenarios with the utmost accuracy.
Optimizing Mesh for Thermal Simulations
Uncover the importance of mesh optimization in thermal simulations. Learn how to strike the right balance between accuracy and computational efficiency to obtain reliable results in a timely manner.
Efficient meshing is a critical aspect of Thermal Stress Analysis in SolidWorks. A well-optimized mesh ensures that the simulation accurately captures the behavior of the model under varying temperature conditions. By carefully selecting the mesh size and refining it where necessary, engineers can achieve a balance that prevents overly coarse results without sacrificing computational efficiency.
In the context of thermal simulations, a fine mesh is often required in areas with high thermal gradients or stress concentrations. This targeted refinement allows for a more accurate representation of temperature distribution and stress intensity. Conversely, using a coarse mesh in less critical regions can significantly reduce computation time without compromising overall accuracy.
Remember, the key is to understand the specific requirements of your simulation and tailor the mesh accordingly. SolidWorks provides tools for mesh refinement and control, empowering users to optimize their simulations for both accuracy and efficiency.
Utilizing Parametric Studies for Temperature Variations
Explore the benefits of parametric studies in Thermal Stress Analysis. Understand how varying temperature conditions and observing their effects can lead to more robust and adaptable designs.
Parametric studies offer a powerful approach to investigating the influence of temperature variations on your SolidWorks models. By systematically altering temperature parameters and observing the resulting changes in stress distribution, engineers can gain valuable insights into the behavior of their designs under different thermal scenarios.
This method allows for the exploration of a wide range of temperature conditions without the need for manual adjustments at each step. SolidWorks facilitates parametric studies, enabling users to define multiple scenarios and automatically analyze the thermal stress response for each set of conditions.
Through parametric studies, engineers can identify the critical temperature ranges where the design may be prone to failure or excessive stress. This information is invaluable for making informed decisions during the design optimization process. By incorporating the findings from parametric studies, you can create more resilient and adaptable designs that withstand diverse thermal challenges.
Challenges and Limitations
Addressing Common Challenges in Thermal Stress Analysis is an integral aspect of ensuring the reliability and accuracy of simulation results. One common challenge engineers encounter is the issue of convergence during simulations. Convergence problems may arise when the solution fails to reach a stable state, affecting the accuracy of the results. To overcome this challenge, careful consideration of mesh refinement, solver settings, and boundary conditions is essential.
Additionally, complex geometries can pose a significant hurdle in Thermal Stress Analysis. Intricate shapes and intricate assemblies may lead to increased computation times and potential inaccuracies in results. Engineers must employ effective meshing strategies and consider simplifying complex geometries where possible without compromising the overall integrity of the simulation.
Understanding the Limitations of Thermal Simulation is crucial for practitioners. While Thermal Stress Analysis in SolidWorks provides valuable insights, it's essential to acknowledge its limitations. For instance, the assumption of linear material behavior and neglecting phase changes may impact the accuracy of results in scenarios involving extreme temperatures. Engineers should be mindful of these limitations and, when necessary, complement thermal simulations with other analysis techniques for a more comprehensive understanding of the system's behavior. Embracing these challenges and limitations as opportunities for improvement ultimately leads to more robust and reliable engineering solutions.
Addressing Common Challenges in Thermal Stress Analysis
Navigate through challenges commonly encountered during Thermal Stress Analysis in SolidWorks. From convergence issues to dealing with intricate geometries, engineers often face hurdles that require strategic solutions. Convergence issues may arise when the simulation struggles to reach a stable solution, affecting result accuracy. To overcome this, refining mesh settings, adjusting solver parameters, and ensuring proper material assignments are crucial steps.
Additionally, when dealing with complex geometries, ensuring a well-defined mesh becomes paramount. Employing local mesh controls and refining mesh in critical areas can enhance simulation accuracy, enabling a more precise evaluation of thermal stresses.
Understanding the Limitations of Thermal Simulation
While Thermal Stress Analysis in SolidWorks provides invaluable insights, it's essential to recognize its limitations. Simulations assume certain conditions and may not fully capture real-world complexities. High-temperature gradients, non-linear material behavior, and transient thermal effects can pose challenges. In such cases, engineers should consider complementary analyses or alternative simulation methods, such as coupled thermal-mechanical simulations, to ensure a more comprehensive understanding of the system's behavior.
Conclusion
In conclusion, the journey through the intricacies of Thermal Stress Analysis in SolidWorks assignments has illuminated the paramount importance of this simulation technique in the realm of mechanical engineering. By delving into the behavior of materials under varying temperature conditions, engineers gain a profound understanding of how structures respond to thermal stresses. This knowledge serves as a cornerstone for designing robust and reliable components, ensuring that they withstand the rigors of real-world applications.
The significance of Thermal Stress Analysis lies not only in its ability to predict and mitigate potential failures but also in its role as a guiding force for optimized design. As we've explored the nuances of setting up thermal boundary conditions, understanding material properties, and conducting simulations, it becomes evident that SolidWorks offers a powerful platform for engineers to fine-tune their designs for optimal performance in diverse thermal environments.
The key takeaway from this exploration is the empowerment of engineers to make informed decisions throughout the design process. Armed with the ability to analyze thermal stress distribution, identify critical points, and optimize designs accordingly, professionals can create structures that not only meet functional requirements but also excel in longevity and reliability.
Encouraging readers to apply the knowledge gained from this guide is more than a suggestion; it is an invitation to elevate engineering skills to new heights. The insights shared here provide a foundation for continuous learning and improvement. As you embark on your SolidWorks assignments, consider the nuances of thermal stress and the impact of temperature variations on your designs. Implement the strategies outlined in this guide to enhance the resilience of your components, ensuring they perform admirably under a spectrum of thermal conditions.
Remember, the true value of knowledge lies in its application. Whether you're working on automotive components, electronics enclosures, or any other engineering endeavor, integrating Thermal Stress Analysis into your SolidWorks workflow can be a game-changer. Embrace the challenges, learn from the simulations, and refine your designs iteratively.
In essence, this exploration into Thermal Stress Analysis serves as a catalyst for continuous improvement and innovation in engineering design. By embracing the insights shared here, you not only navigate the challenges posed by temperature-induced stresses but also contribute to the creation of structures that stand the test of time. Here's to a future of resilient designs and engineering excellence!
This comprehensive guide equips you with the knowledge and skills needed to excel in Thermal Stress Analysis within the SolidWorks environment. By understanding temperature effects on materials and structures, you can elevate your engineering designs to new heights. Stay tuned for more insightful content from SolidWorkAssignmentHelp.com!