- Understanding Weldment Analysis
- Importance of Simulation in Weldment Analysis
- Ensuring Structural Integrity
- Cost-Effective Prototyping
- Benefits of Simulation in Welding Technology
- Risk Mitigation
- Performance Optimization
- Applications of Simulation in Welding
- Thermal Analysis
- Stress and Strain Analysis
- Fatigue Analysis
- Case Studies: Real-World Applications
- Aerospace Industry
- Automotive Engineering
- Overcoming Challenges in Weldment Analysis Simulation
- Material Properties
- Software Selection
- Conclusion
Welding, a fundamental process across diverse industries, forms the backbone of structural integrity in various applications. Whether it's the construction of towering skyscrapers, the assembly of intricate machinery, or the fabrication of essential components in aerospace engineering, welding plays a pivotal role in creating robust and durable structures.
In this dynamic landscape, the need for precision and reliability in welded structures cannot be overstated. As students embark on their journey into the world of welding, understanding the complexities of weldment analysis becomes paramount. This blog seeks to provide a holistic introduction to the integration of simulation in weldment analysis, shedding light on its profound significance, multifaceted benefits, and wide-ranging applications within the realm of welding technology. If you need assistance with your weldment assignment, don't hesitate to reach out for expert support.
Weldment analysis, at its core, involves a meticulous examination of how welded structures respond to various conditions. Traditional approaches often rely on physical prototypes and testing, but the advent of simulation has revolutionized this process. Simulation, in the context of weldment analysis, refers to the virtual prototyping of welding scenarios, allowing students to predict, analyze, and optimize the structural integrity of weldments before physical implementation.
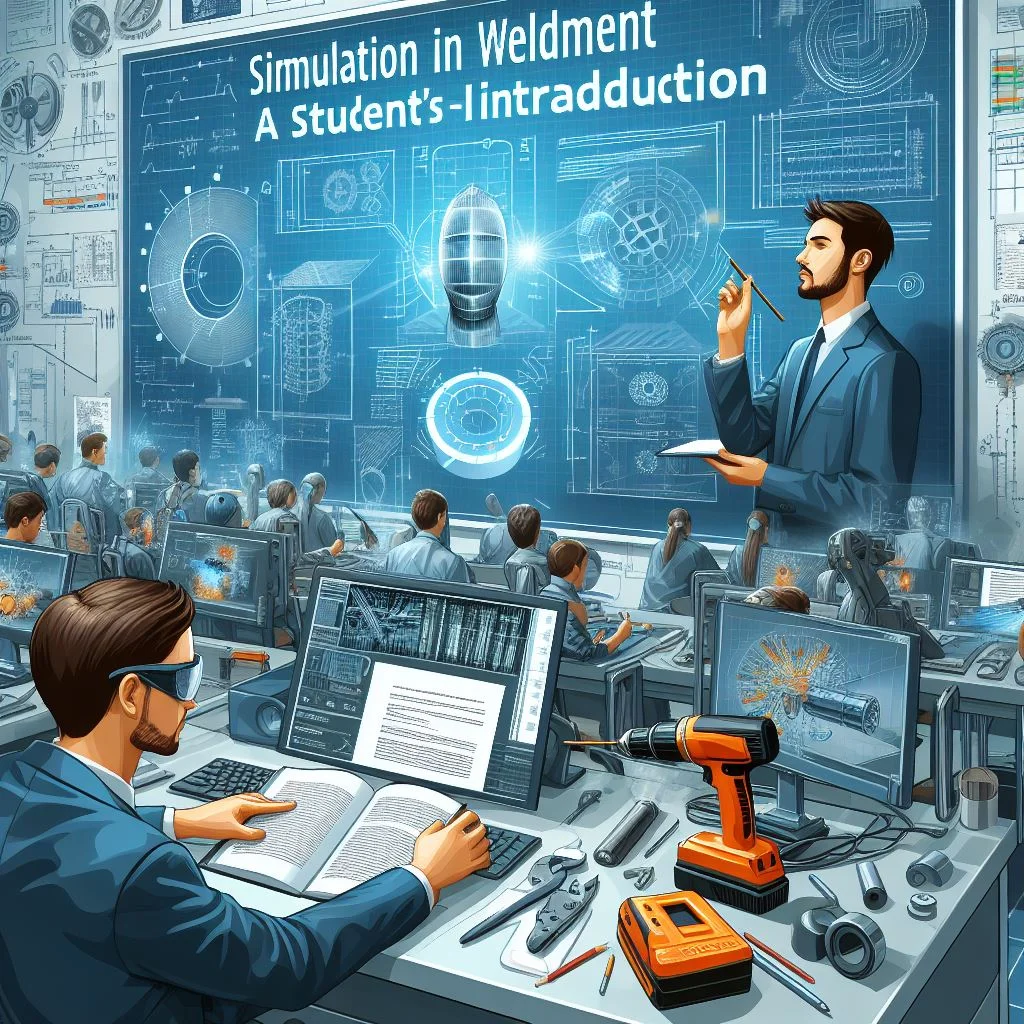
The significance of simulation in weldment analysis lies in its ability to provide a comprehensive understanding of the intricate dynamics involved in welding processes. Students can explore and experiment with different variables, gaining insights into how factors like heat distribution, stress, and strain impact the overall performance of welded structures. This virtual experimentation not only enhances learning but also contributes to the development of more resilient and efficient welding practices.
The benefits of incorporating simulation into welding technology are multifaceted. Firstly, it serves as a proactive measure to ensure structural integrity. By virtually dissecting welding scenarios, students can identify potential weak points and areas of concern, allowing for preemptive adjustments and improvements in design.
Additionally, simulation in weldment analysis proves to be a cost-effective approach, particularly in educational settings. The traditional method of relying solely on physical prototypes can be time-consuming and resource intensive. Simulation mitigates these challenges by offering a virtual platform for experimentation, reducing the need for extensive physical prototyping and associated costs.
As students delve into the world of welding simulation, they discover its applications spanning various aspects of welding technology. Thermal analysis, a crucial component, enables them to grasp the intricate distribution of heat during welding processes, unraveling the mysteries of temperature's influence on material properties.
Stress and strain analysis, another key application, allows students to virtually subject welded structures to different loads, unveiling potential weak points and areas prone to deformation. Furthermore, fatigue analysis in simulation simulates the effects of prolonged stress, aiding in predicting the lifespan of weldments in real-world conditions.
Real-world case studies highlight the practical applications of simulation in welding technology. In the aerospace industry, where components endure extreme conditions, simulation ensures the structural integrity of welded structures. Similarly, in automotive engineering, simulation contributes to the optimization of weight and performance, aligning with the industry's demand for efficiency.
Navigating the terrain of weldment analysis simulation is not without its challenges. Students encounter complexities in dealing with diverse material properties commonly used in welding. Accurate representation of material data becomes paramount in ensuring the fidelity of simulation results.
Moreover, the selection of appropriate simulation software becomes a critical consideration. Factors such as accuracy, ease of use, and compatibility with other design tools come into play. Guiding students through these challenges becomes an integral part of their educational journey, preparing them for the intricacies of the real-world application of welding simulation.
Understanding Weldment Analysis
Weldment analysis is a multifaceted process that involves scrutinizing the structural performance of welded components under diverse conditions. This analytical approach utilizes cutting-edge simulation tools to predict and optimize the structural integrity of weldments, offering a virtual testing ground for students. By leveraging these simulation tools, students can gain valuable insights into the complex interactions between materials, welding processes, and environmental factors.
A key aspect of understanding weldment analysis is appreciating its role in assessing how various welding scenarios impact the overall structural stability. It goes beyond the traditional realm of hands-on testing, providing a digital platform for students to explore different welding parameters, materials, and configurations. This virtual experimentation allows for a nuanced understanding of how weldments respond to thermal variations, stress, and other critical factors, providing a holistic view that is often challenging to achieve through physical prototyping alone.
Moreover, weldment analysis simulation aids students in comprehending the intricacies of heat distribution during welding processes. This knowledge is crucial for predicting potential weak points and optimizing designs to withstand varying temperatures, ensuring the longevity and reliability of welded structures. As students delve into the world of weldment analysis, they embark on a journey of discovery where theoretical knowledge converges with practical applications, laying the foundation for a comprehensive understanding of welding technology.
Importance of Simulation in Weldment Analysis
Simulation plays a pivotal role in the realm of weldment analysis due to its profound importance in ensuring the structural integrity of welded structures. One of the primary aspects where simulation shines is in its ability to predict and address potential weak points within a design. By subjecting virtual weldments to various conditions, students can identify vulnerable areas that might be prone to failure under real-world circumstances. This predictive capability empowers students to refine their designs, implement necessary reinforcements, and ultimately create weldments that can withstand the rigors of practical applications.
Moreover, the cost-effectiveness of simulation cannot be overstated. Traditional methods of prototyping involve the fabrication of physical models for testing, a process that consumes both time and resources. Simulation allows students to virtually prototype weldments, reducing the need for expensive and time-consuming physical iterations. This not only accelerates the design process but also makes it more accessible for educational institutions with limited budgets. The ability to explore multiple design iterations virtually, tweaking parameters and analyzing outcomes, contributes significantly to the efficiency and affordability of the overall learning process. In essence, simulation in weldment analysis acts as a powerful tool for fortifying structures against potential risks while simultaneously streamlining the design and prototyping phases.
Ensuring Structural Integrity
Simulation allows for a virtual exploration of various welding scenarios, enabling students to analyze potential weak points and optimize designs for maximum structural integrity. In the intricate world of welding, understanding how different materials respond to various welding conditions is paramount. Simulation tools provide a dynamic platform for students to study and analyze the impact of welding parameters on the structural integrity of weldments.
With virtual models, students can simulate diverse welding techniques, such as arc welding or gas metal arc welding, and observe how each method influences the structural properties of the welded joint. This hands-on virtual experience not only enhances their understanding of welding processes but also equips them with the knowledge to identify potential challenges and weaknesses in a controlled environment.
Cost-Effective Prototyping
By simulating weldments, students can reduce the need for physical prototypes, saving time and resources. This cost-effective approach is invaluable in educational settings and real-world applications. Traditional prototyping can be time-consuming and resource-intensive, often requiring multiple iterations before achieving the desired outcome. Simulation technology streamlines this process, allowing students to virtually test and refine their designs before moving to the physical prototype stage.
This not only accelerates the product development cycle but also minimizes material wastage associated with trial and error. Students can experiment with different welding parameters, materials, and joint configurations in a virtual environment, gaining valuable insights without the need for extensive material resources. As a result, the learning curve is shortened, and students are better equipped to approach real-world welding challenges with confidence and efficiency.
Benefits of Simulation in Welding Technology
Simulation in welding technology offers a myriad of advantages that extend beyond the virtual realm. One significant benefit is the enhancement of students' problem-solving skills. By engaging in simulated scenarios, students develop a deep understanding of the complexities involved in welding processes. They learn to troubleshoot issues, optimize parameters, and make informed decisions to achieve optimal results.
Furthermore, simulation fosters a sense of innovation and creativity among students. As they experiment with different welding configurations and parameters in a virtual environment, they are encouraged to think outside the conventional boundaries. This not only stimulates their intellectual curiosity but also prepares them to face the challenges of the ever-evolving field of welding technology.
Moreover, the real-time feedback provided by simulation tools empowers students to iterate and refine their designs rapidly. This iterative process is invaluable in the learning journey, allowing students to witness the immediate impact of their decisions on the performance and integrity of weldments. It instills a sense of accountability and precision in their approach, traits that are highly desirable in professional welding practices.
Risk Mitigation
Simulation helps students identify and mitigate potential risks associated with welding processes, ensuring safer and more reliable structural outcomes. In the world of welding, understanding and managing risks are paramount. Simulation tools allow students to virtually foresee potential issues such as weld defects, material weaknesses, and thermal distortions. By simulating various scenarios, students gain insights into how different parameters affect the overall safety of a welded structure. This proactive approach to risk mitigation not only enhances the learning experience but also instills a mindset of safety consciousness that is crucial in real-world welding applications.
Performance Optimization
Optimizing weldment designs through simulation leads to improved performance, efficiency, and durability. Students can experiment with different parameters to achieve the best results. Simulation empowers students to fine-tune their designs by virtually testing and tweaking various factors, such as welding parameters, material choices, and joint configurations. Through this iterative process, students can optimize the performance of welded structures, ensuring they meet or exceed desired specifications. This hands-on experience in performance optimization prepares students for the challenges they may encounter in their future careers, where efficiency and durability are essential considerations in welding technology.
Applications of Simulation in Welding
Simulations in welding extend their utility across various industries, each benefiting from the nuanced insights they provide. In the realm of thermal analysis, simulations allow students to delve into the intricate details of how heat is distributed during welding processes. This knowledge proves invaluable, particularly in understanding the thermal effects on material properties, helping students make informed decisions about welding parameters and techniques.
Moving beyond thermal considerations, stress and strain analysis through simulation grants students the ability to virtually explore the impact of mechanical forces on welded structures. This aspect is critical for identifying potential weak points and designing weldments that can withstand the stresses they may encounter in real-world applications.
Fatigue analysis, another crucial application, enables students to simulate the long-term performance of welded structures. By subjecting virtual weldments to repeated loading and unloading cycles, students can predict the fatigue life of a structure, ensuring its durability over an extended period.
These applications find practical relevance in industries such as aerospace and automotive engineering. In the aerospace sector, simulations contribute significantly to ensuring the structural integrity of components exposed to extreme conditions. Likewise, in automotive engineering, simulations aid in optimizing welded structures, striking a balance between performance, safety, and weight considerations.
Simulations, therefore, serve as a virtual laboratory for students, allowing them to explore and analyze diverse scenarios in welding, ultimately preparing them for the challenges they may encounter in their future careers.
Thermal Analysis
Explore how heat is distributed during welding processes, allowing students to understand the impact of temperature on material properties.
Enhancing Understanding through Thermal Analysis
In the realm of welding, thermal analysis becomes a crucial tool for students to comprehend the intricate dance of heat during the welding process. As students delve into the simulation of thermal dynamics, they gain insights into how different materials respond to varying temperatures. This exploration aids in predicting and mitigating potential issues such as thermal distortion, changes in material properties, and the formation of undesirable microstructures. By navigating the virtual landscape of thermal analysis, students acquire a profound understanding of how heat influences the overall integrity of welded structures.
Stress and Strain Analysis
Simulate the effects of stress and strain on welded structures, providing insights into potential weak points and deformation.
Unveiling Structural Responses through Stress and Strain Analysis
In the intricate tapestry of welded structures, stress and strain act as silent architects, shaping the final form and function. Simulation in stress and strain analysis empowers students to unravel these invisible forces, offering a virtual playground to assess how materials respond under different loads. By subjecting weldments to simulated stress scenarios, students gain valuable insights into potential weak points, deformation patterns, and the overall structural behavior. This hands-on experience in the virtual realm prepares students to optimize designs, ensuring welded structures can withstand the real-world forces they may encounter.
Fatigue Analysis
Examine the long-term performance of weldments by simulating fatigue conditions, helping students predict the lifespan of structures.
Predicting Endurance: The Essence of Fatigue Analysis
In the journey towards robust and enduring welded structures, fatigue analysis emerges as a beacon guiding students through the challenges of long-term performance. Through simulation, students can subject weldments to cyclical loading, mimicking the real-world conditions that structures often face. This process allows students to predict and understand the cumulative damage that occurs over time, providing valuable insights into the fatigue life of welded components. Armed with this knowledge, students can make informed decisions in design and material selection, contributing to the creation of welded structures that stand the test of time.
Case Studies: Real-World Applications
Explore how simulation plays a pivotal role in ensuring the structural integrity of aerospace components subjected to extreme conditions. For instance, in the aerospace industry, where safety and reliability are paramount, simulation allows engineers to analyze the effects of high temperatures, varying pressures, and dynamic forces on welded structures. By virtually testing different scenarios, they can optimize designs to withstand the harsh conditions of space travel and aeronautical operations.
Similarly, in the realm of automotive engineering, simulation contributes significantly to the optimization of welded structures. Consider the challenges faced in designing vehicles that must balance performance, safety, and fuel efficiency. Through simulation, students can delve into the complexities of welding applications in the automotive industry, gaining insights into how different welding techniques and materials impact the overall performance and safety of vehicles. This virtual exploration helps engineers refine designs, minimize weight, and maximize structural strength, ultimately influencing the development of more fuel-efficient and safer automobiles.
Aerospace Industry
Discover how simulation plays a pivotal role in ensuring the structural integrity of aerospace components subjected to extreme conditions.
In the aerospace industry, where precision and reliability are non-negotiable, simulation emerges as a game-changer. The ability to virtually test and analyze weldments under extreme conditions, such as high temperatures, pressure differentials, and dynamic loads, is paramount. Aerospace engineers utilize simulation tools to predict how different materials will perform in these harsh environments, ensuring that welded structures can withstand the rigors of space travel and varying atmospheric conditions. This not only enhances safety but also contributes to the development of lightweight yet robust components, a critical factor in aerospace design.
Automotive Engineering
Explore how simulation contributes to the optimization of welded structures in the automotive industry, balancing performance and weight considerations.
In the realm of automotive engineering, where the pursuit of efficiency and performance is relentless, simulation becomes an indispensable ally. Weldments in vehicles must endure diverse challenges, including constant vibrations, varying temperatures, and stringent safety requirements. Simulation allows automotive engineers to fine-tune the design of welded structures, finding the delicate balance between performance and weight considerations. By virtually testing different welding configurations, materials, and joining techniques, engineers can optimize the overall structural integrity of vehicles. This not only enhances safety but also contributes to fuel efficiency and overall performance, a crucial aspect in the ever-evolving automotive landscape.
Overcoming Challenges in Weldment Analysis Simulation
Successfully navigating the realm of weldment analysis simulation involves addressing various challenges inherent to the process. One significant hurdle lies in accurately representing material properties within the simulation environment. Different materials exhibit unique behaviors under the stress and heat of welding, and ensuring that the simulation reflects these nuances is crucial. This challenge emphasizes the importance of comprehensive material data, highlighting the need for students to access and incorporate precise information into their simulations.
Another critical aspect is the selection of appropriate simulation software. The market offers a plethora of tools, each with its strengths and weaknesses. Students must carefully consider factors such as the software's accuracy, user-friendliness, and compatibility with other design tools. The learning curve associated with mastering simulation software can be steep, but with the right guidance and hands-on experience, students can overcome this challenge and harness the full potential of simulation in weldment analysis.
Material Properties
Addressing the complexities of simulating different materials commonly used in welding is a critical aspect of weldment analysis. The simulation process heavily relies on accurate material data to provide realistic results. Each material exhibits unique thermal conductivity, melting points, and structural properties that directly impact the welding process. Students must be aware of the challenges associated with obtaining precise material data and the consequences of using inaccurate information in simulations. By emphasizing the importance of accurate material properties, this ensures that simulations accurately reflect real-world welding scenarios, contributing to more reliable and insightful analyses.
Software Selection
Guiding students in choosing the right simulation software is crucial for a successful weldment analysis. The selection process involves evaluating various factors, including accuracy, ease of use, and compatibility with other design tools. Students need to be aware of the diverse software options available, each with its unique features and capabilities. Emphasizing the importance of aligning software capabilities with specific analysis requirements helps students make informed decisions.
The choice of simulation software significantly influences the depth and accuracy of the analysis. Factors such as the ability to handle non-linearities, support for multi-physics simulations, and integration with CAD tools should be considered. Additionally, students should explore user interfaces and documentation to ensure a smooth learning curve. By providing guidance on software selection, educators empower students to navigate the evolving landscape of simulation tools, preparing them for the challenges they may encounter in their academic and professional journeys.
Conclusion
In conclusion, the role of simulation in weldment analysis holds significant importance for students embarking on a journey in the field of welding technology. As technology continues to advance, the integration of simulation tools becomes increasingly pivotal for fostering a deeper understanding of the complexities associated with welded structures.
By comprehending the importance of simulation, students gain a holistic perspective on the intricate dynamics involved in welding processes. The ability to virtually assess and predict the behavior of weldments empowers students to identify potential challenges early in the design phase. This proactive approach not only enhances their problem-solving skills but also instills a sense of confidence in their ability to address real-world issues in welding applications.
Moreover, the benefits of simulation extend beyond the academic realm, reaching into the practical aspects of the welding industry. The cost-effective nature of virtual prototyping through simulation allows students to explore a myriad of design variations without the need for extensive physical prototypes. This not only saves resources but also encourages a culture of innovation and experimentation within the academic environment.
As students delve into the applications of simulation in welding, they gain insights into industries such as aerospace and automotive engineering. These sectors heavily rely on simulation to ensure the structural integrity of welded components under extreme conditions. The knowledge gained through such case studies not only broadens the students' perspectives but also prepares them for the diverse challenges they may encounter in their professional careers.
In essence, a thorough understanding of simulation in weldment analysis equips students with the tools they need to contribute meaningfully to the development of robust and reliable welded structures. As they enter the workforce, their proficiency in utilizing simulation techniques positions them as valuable assets in industries where precision, efficiency, and safety are paramount.