- Understanding SolidWorks Simulation
- Key Components of Structural Analysis
- Material Selection and Properties
- Boundary Conditions and Constraints
- Meshing Techniques for Accurate Results
- Importance of Mesh Density
- Localized Mesh Refinement
- Analyzing Results and Interpretation
- Post-Processing Tools
- Extracting Maximum Value from Simulation Data
- Real-world Applications and Case Studies
- Case Study: Optimizing a Truss Structure
- Integrating Simulation into the Design Process
- Conclusion
Structural analysis, a cornerstone of engineering design, is a discipline that holds paramount importance in guaranteeing the resilience of components and structures against a myriad of loads and environmental conditions. As the engineering landscape continues to evolve, so does the methodology employed for ensuring the structural integrity of designs. The emergence of cutting-edge simulation tools, exemplified by SolidWorks Simulation, has revolutionized the approach engineers take toward design validation. This transformative technology empowers engineers to conduct comprehensive virtual testing, enabling meticulous scrutiny of their designs well before the commencement of the manufacturing phase. If you need help with your finite element analysis assignment, consider this acknowledgment of the role of simulation tools in structural analysis as a valuable resource, providing insights into the application of advanced technologies like SolidWorks Simulation in the realm of engineering design and assisting you in mastering the challenges of your finite element analysis assignments.
The bedrock of SolidWorks Simulation lies in its ability to create a virtual prototype of a design, offering a dynamic platform for engineers to subject their creations to a wide array of simulated conditions. This not only expedites the design validation process but also significantly mitigates the risks associated with unforeseen structural deficiencies that may manifest during real-world applications. By simulating various loads, forces, and environmental factors, engineers can glean valuable insights into the behavior of their designs, ultimately fine-tuning and optimizing them for optimal performance and reliability.
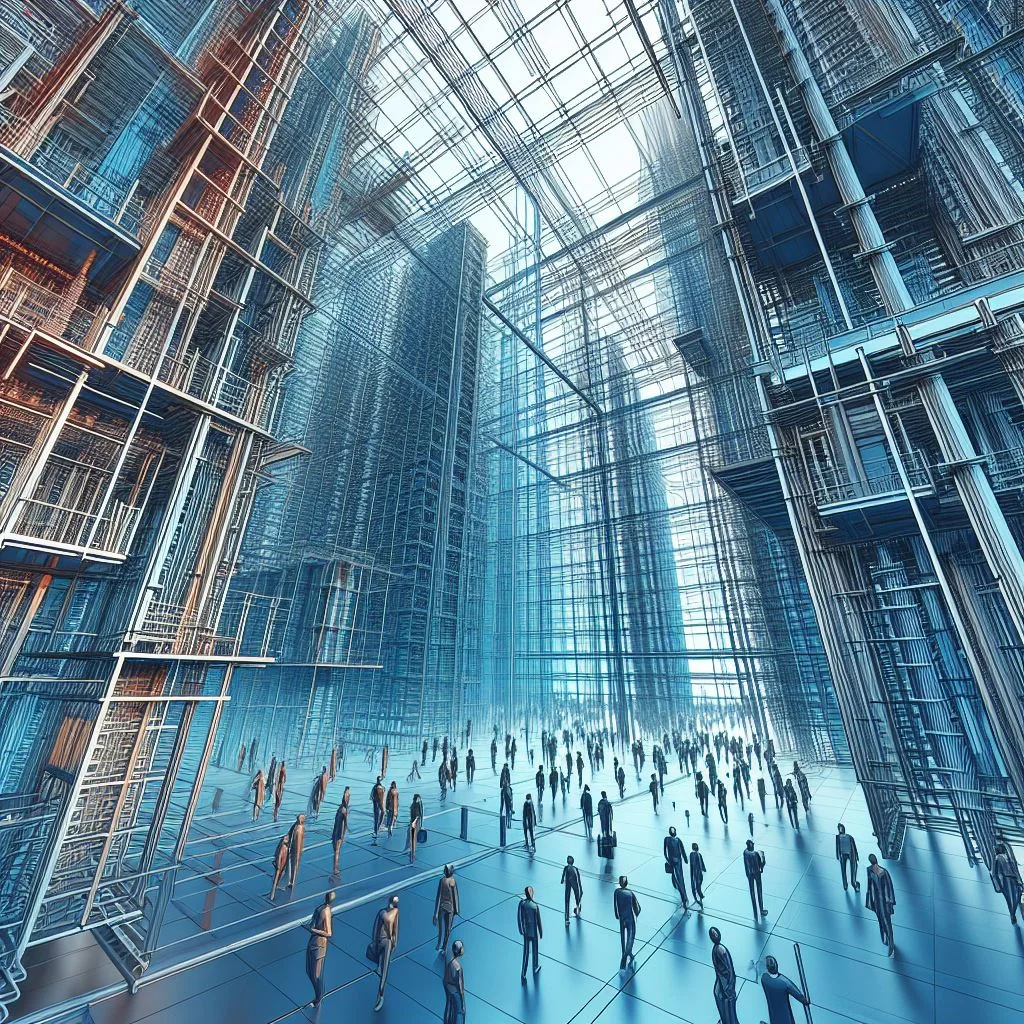
In the context of this blog, we embark on a comprehensive exploration of the intricate world of structural analysis through the lens of SolidWorks Simulation. Our journey takes us beyond the theoretical underpinnings and into the practical realm, shedding light on techniques that are not only applicable to academic assignments but also find resonance in the dynamic landscape of real-world engineering applications.
One of the key focal points in this exploration is the role of material selection and the nuanced understanding of material properties. SolidWorks Simulation facilitates a meticulous delineation of material characteristics, considering factors such as elasticity, thermal expansion, and density. This precise calibration ensures that the virtual representation of the material behaves in a manner consistent with its real-world counterpart, laying the groundwork for accurate and reliable simulations.
As we venture deeper into the nuances of structural analysis, the spotlight shifts to the critical aspect of establishing boundary conditions and constraints. In the virtual realm of SolidWorks Simulation, engineers are bestowed with the capability to emulate a spectrum of constraints ranging from fixed supports to rollers and applied forces. The judicious selection and accurate definition of these boundary conditions are pivotal, as they play a decisive role in mimicking real-world scenarios, a prerequisite for a simulation that mirrors the authentic structural behavior of a design.
Meshing, an indispensable facet of structural analysis, assumes a central position in our exploration. The process of meshing involves subdividing the geometric representation of a structure into smaller elements to facilitate analysis. Striking a delicate balance in mesh density is paramount—too coarse a mesh may compromise accuracy, while an overly fine mesh can escalate computational costs. Our discourse will delve into strategies for achieving an optimal mesh density and shed light on the benefits of localized mesh refinement in areas of particular structural significance.
The subsequent segments of this blog will unravel the complexities of post-processing tools available within SolidWorks Simulation. These tools provide engineers with a suite of options for interpreting simulation results effectively. From contour plots illustrating stress distribution to animations elucidating structural deformations, these post-processing capabilities empower engineers to glean actionable insights from simulation data. Moreover, we will navigate through methodologies for extracting maximum value from simulation results, equipping engineers with the prowess to identify critical areas, assess safety margins, and make informed design decisions.
In an effort to bridge theory with practical application, this blog will culminate in real-world case studies, offering a tangible demonstration of the prowess of SolidWorks Simulation. A specific case study will unfold, detailing the optimization of a truss structure through an iterative process of design modification and simulation analysis. By dissecting this real-world example, readers will gain a profound understanding of how simulation can be seamlessly integrated into the design process, leading to enhanced structural performance and efficiency.
Understanding SolidWorks Simulation
Before we delve into the techniques, let's take a closer look at SolidWorks Simulation. This finite element analysis (FEA) tool is seamlessly integrated into the SolidWorks CAD software, empowering engineers to simulate and analyze the behavior of their designs under diverse conditions. SolidWorks Simulation serves as a virtual testing ground, mimicking real-world scenarios and providing invaluable insights into the structural aspects of a design.
SolidWorks Simulation excels in capturing the complexities of structural behavior, offering a comprehensive analysis of stress, strain, and deformation. Engineers can explore how different materials respond to varying loads, enabling them to make informed decisions during the design phase. This understanding is paramount for optimizing designs and ensuring that structures can withstand the demands they will face in practical applications.
In essence, SolidWorks Simulation goes beyond traditional design approaches by allowing engineers to virtually test and refine their concepts. This not only accelerates the design iteration process but also significantly contributes to achieving a higher level of precision and reliability in engineering projects. Now, let's move on to explore the key components of structural analysis using SolidWorks Simulation.
Key Components of Structural Analysis
Structural analysis involves several critical components that collectively contribute to the comprehensive evaluation of a design's integrity and performance. One fundamental aspect is the meticulous selection and characterization of materials. Engineers must carefully consider factors such as elasticity, thermal expansion, and density to accurately represent how materials behave under varying conditions. SolidWorks Simulation facilitates this process by allowing precise definition of material properties.
Another crucial element in structural analysis is the establishment of boundary conditions and constraints. These conditions emulate the real-world scenarios in which a structure operates. Whether it be fixed supports, rollers, or applied forces, SolidWorks Simulation enables engineers to precisely define these conditions, ensuring the virtual testing environment closely mirrors the expected conditions during the operational life of the structure.
These key components, material selection, and boundary condition definition, lay the groundwork for an effective structural analysis. They serve as the building blocks for creating a virtual model that accurately represents the physical reality, setting the stage for further analysis and optimization. In the subsequent sections, we will explore additional techniques and considerations, emphasizing their significance in both assignments and real-world engineering applications.
Material Selection and Properties
One of the fundamental aspects of structural analysis is selecting the appropriate materials for a design. SolidWorks Simulation enables users to define material properties accurately, considering factors such as elasticity, thermal expansion, and density. This ensures a realistic representation of how materials behave under different loading conditions.
Selecting the right material is akin to laying the foundation for a sturdy structure. Engineers must carefully evaluate the mechanical properties of materials, such as tensile strength and Young's modulus, to accurately simulate their behavior under various stressors. SolidWorks Simulation's material library facilitates this process by providing a comprehensive database of materials with predefined properties. Engineers can also customize material properties to reflect real-world scenarios accurately.
Understanding the thermal behavior of materials is equally crucial, especially in applications where temperature variations play a significant role. SolidWorks Simulation allows for the incorporation of thermal expansion coefficients, ensuring simulations consider the effects of temperature changes on material dimensions.
In assignments, demonstrating a thorough understanding of material selection and properties not only showcases engineering expertise but also lays the groundwork for successful structural simulations.
Boundary Conditions and Constraints
Setting up realistic boundary conditions is essential for obtaining accurate simulation results. Whether it's fixed supports, rollers, or applied forces, SolidWorks Simulation allows engineers to define these conditions precisely. We'll explore how to choose the right constraints to mimic real-world scenarios, ensuring the simulation mirrors actual structural behavior.
Choosing the Right Constraints: The accuracy of a structural simulation heavily relies on defining appropriate boundary conditions. Engineers need to carefully consider how a structure interacts with its surroundings. For instance, in civil engineering applications, understanding how a building connects to its foundation is crucial. SolidWorks Simulation provides a range of constraint options, including fixed geometry, rollers for allowing rotational movement, and prescribed displacements to simulate specific structural interactions.
Imitating Real-world Scenarios: In the realm of structural analysis, authenticity is key. Simulating actual conditions, such as how a bridge is anchored to its abutments or how a car frame interfaces with its suspension system, requires a thoughtful selection of boundary conditions. SolidWorks Simulation empowers engineers to replicate these scenarios with precision, allowing for a more accurate prediction of a structure's behavior under different loads.
By exploring the intricacies of boundary conditions and constraints in SolidWorks Simulation, engineers can enhance the reliability of their simulations and gain valuable insights into the real-world performance of their designs.
Meshing Techniques for Accurate Results
Meshing is a critical aspect of structural analysis using SolidWorks Simulation, influencing the accuracy and efficiency of simulation results. Achieving an optimal mesh density is essential, striking a balance between accuracy and computational resources. Too coarse a mesh may oversimplify the representation of the structure, leading to inaccurate results, while an excessively fine mesh can strain computational resources without providing proportional benefits.
In the realm of meshing techniques, SolidWorks Simulation offers engineers the flexibility to refine meshes locally. This capability is particularly advantageous when certain regions of a structure demand more detailed analysis due to high stress concentrations or complex geometries. By employing localized mesh refinement strategically, engineers can enhance the precision of their simulations without unnecessarily burdening the computational load.
Consider a scenario where a component within a larger assembly experiences varying stress levels. Through localized mesh refinement, engineers can focus computational resources on these critical areas, ensuring that the simulation captures the nuances of stress distribution accurately. This technique not only aids in assignments where specific aspects of a design require closer examination but also proves invaluable in real-world applications, where localized stress concentrations can significantly impact structural integrity.
Importance of Mesh Density
Mesh density is a pivotal factor in the accuracy of structural analysis using SolidWorks Simulation. The process of meshing involves breaking down the geometric structure into smaller elements for analysis. Striking the right balance in mesh density is crucial: a mesh that is too coarse may lead to imprecise results, while an overly fine mesh can impose a significant computational burden.
Achieving an optimal mesh density involves thoughtful consideration of both accuracy and computational efficiency. In this section, we'll delve into strategies for determining the appropriate mesh density for different types of structures. By understanding the intricacies of meshing, engineers can enhance the reliability of their simulation results and gain a more nuanced understanding of structural behavior.
Localized Mesh Refinement
Certain areas within a structure may endure higher stress concentrations than others. To address this, SolidWorks Simulation provides a powerful tool: localized mesh refinement. This feature allows engineers to focus on specific critical regions, enabling a more detailed analysis without the need to increase the overall mesh density uniformly.
In assignments where specific aspects of a design demand closer scrutiny, localized mesh refinement proves particularly advantageous. This technique empowers engineers to refine the simulation precisely where it matters most, ensuring a more accurate representation of the structural response in critical areas. We'll explore the practical application of localized mesh refinement and how it enhances the overall effectiveness of structural analysis using SolidWorks Simulation.
Analyzing Results and Interpretation
Once the structural analysis simulation is executed, engineers are presented with a wealth of data that requires careful interpretation. SolidWorks Simulation offers a variety of post-processing tools to make sense of the simulation results. These tools provide a visual representation of how the structure responds to different loads, offering insights into stress distribution, deformation patterns, and other critical factors.
One essential aspect of post-processing is the utilization of contour plots. These graphical representations allow engineers to visualize stress concentrations and identify areas where the structure may be vulnerable. By carefully examining these contour plots, designers can pinpoint regions that require further attention or modification to enhance the overall structural performance.
In addition to contour plots, animations play a crucial role in result interpretation. Animated simulations demonstrate the deformation of the structure under applied loads, offering a dynamic perspective on how different components respond to various forces. This visual representation aids in identifying potential weak points, assessing the overall stability, and validating the structural integrity of the design.
Furthermore, engineers can extract numerical data from the simulation results, allowing for a quantitative analysis of factors such as maximum stress, displacement, and safety margins. This data-driven approach empowers designers to make informed decisions, ensuring that the structural elements not only meet safety standards but also optimize material usage and overall design efficiency.
In the subsequent sections, we will explore techniques for extracting maximum value from simulation data and showcase their application in real-world scenarios. This knowledge not only enhances the effectiveness of structural analysis for assignments but also serves as a valuable tool in the broader spectrum of engineering design and optimization.
Post-Processing Tools
SolidWorks Simulation offers a suite of post-processing tools designed to enhance engineers' ability to interpret simulation results effectively. These tools go beyond simple numerical outputs, providing visualizations that aid in understanding how a structure responds to applied loads. Engineers can utilize contour plots illustrating stress and displacement distributions, as well as dynamic animations that showcase deformation under various conditions. This section will delve into the practical applications of these post-processing tools, demonstrating how they contribute to a comprehensive analysis of structural behavior.
Extracting Maximum Value from Simulation Data
Simulation results contain a wealth of information, and extracting maximum value from this data is paramount. In this section, we will explore techniques for a thorough analysis, including the identification of critical areas within a design, assessing safety margins, and making informed decisions based on simulation outcomes. These skills are not only crucial for academic assignments but also directly applicable to real-world engineering practices, ensuring that engineers can leverage simulation data to optimize designs and enhance overall structural performance.
Real-world Applications and Case Studies
As we delve into the practical applications of SolidWorks Simulation, it becomes evident that the software extends beyond theoretical concepts, finding a crucial place in real-world engineering scenarios. One compelling case study that showcases the power of this simulation tool involves the optimization of a truss structure.
Consider a scenario where a design team is tasked with creating an efficient and robust truss for a bridge. By leveraging SolidWorks Simulation, engineers can simulate various loading conditions, assess stress distribution, and iterate on the design for optimal performance. This iterative process involves making adjustments to the truss geometry, material properties, or support conditions, followed by running simulations to evaluate the impact of these changes.
Through this iterative cycle, the design team can identify the most effective configuration that minimizes stress concentrations and ensures the truss's overall stability. SolidWorks Simulation not only aids in reaching an optimized solution but also provides valuable insights into the structural behavior under different scenarios, allowing engineers to make informed decisions.
This case study highlights the practicality of SolidWorks Simulation in addressing complex engineering challenges, offering a glimpse into how virtual testing can significantly streamline the design process and contribute to the creation of structurally sound and efficient solutions.
Case Study: Optimizing a Truss Structure
To illustrate the practical application of SolidWorks Simulation, let's dive into a comprehensive case study that revolves around optimizing a truss structure. In this scenario, we encounter a truss designed for a specific load-bearing purpose. The iterative process begins with making intentional design changes to the truss configuration. SolidWorks Simulation enables engineers to run simulations that assess how these alterations impact the structural behavior.
Through multiple simulation iterations, engineers gain valuable insights into stress distribution, potential weak points, and areas of improvement. This hands-on example serves as a powerful illustration of how simulation tools facilitate a data-driven approach to design optimization. By refining the truss structure based on simulation results, engineers can achieve not only enhanced structural performance but also a more efficient and cost-effective design.
Integrating Simulation into the Design Process
In this final section, we delve into the pivotal role of integrating SolidWorks Simulation into the overall design process. Starting simulation activities in the early stages of design allows engineers to foresee and address potential issues before advancing to the manufacturing phase. This proactive approach serves as a preventive measure, saving both time and resources by mitigating the risk of discovering flaws in the final product.
By seamlessly integrating simulation into the design workflow, engineers can refine their designs iteratively, ensuring that the end result aligns with performance expectations. This section highlights the proactive and predictive nature of utilizing SolidWorks Simulation, contributing to the creation of more robust, reliable, and efficient designs. The ability to anticipate challenges early on fosters a culture of continuous improvement in the engineering design process.
Conclusion
In conclusion, SolidWorks Simulation emerges as a cornerstone in the arsenal of tools available to engineers, revolutionizing the landscape of structural analysis. This software doesn't merely offer a suite of features; it provides a dynamic platform for engineers to embark on a journey of comprehensive validation and optimization. The techniques explored in this blog, ranging from meticulous material selection to intricate meshing strategies and nuanced result interpretation, collectively form a holistic approach that extends its applicability from academic assignments to the complex tapestry of real-world engineering projects.
The significance of mastering these techniques cannot be overstated. In the realm of material selection, engineers are equipped not only with the ability to choose materials based on standard properties but also to fine-tune these properties to mirror the intricacies of real-world scenarios accurately. This attention to detail ensures that the virtual prototypes generated by SolidWorks Simulation align closely with the behavior of physical counterparts, instilling confidence in the design process.
As we venture into the realm of meshing strategies, the emphasis is on achieving that delicate balance between accuracy and computational efficiency. The ability to adapt mesh density, coupled with localized refinement where needed, showcases the software's sophistication. This adaptability not only enhances the precision of structural analyses but also underscores the practicality of SolidWorks Simulation in addressing complex engineering challenges.
Result interpretation is the culmination of the simulation process, and SolidWorks Simulation doesn't disappoint in this regard. The post-processing tools available allow engineers to dissect and understand the intricacies of simulated behavior, paving the way for informed decision-making. This analytical prowess is not confined to the digital realm; it permeates the fabric of tangible engineering outcomes, directly influencing the success and reliability of projects.
In essence, the mastery of SolidWorks Simulation's capabilities isn't just a technical proficiency; it's a strategic advantage. Engineers wielding this tool aren't merely validating designs; they are sculptors of structural resilience and architects of optimal performance. The ripple effect of this mastery is felt across the entire spectrum of engineering projects, contributing fundamentally to their triumphs and the overarching success of the professionals behind them. SolidWorks Simulation stands not just as software but as a catalyst for engineering excellence, enabling designs to transcend the digital realm and manifest as robust, real-world solutions.