- Understanding Harvard Engineering Principles
- Overview of Harvard Engineering Principles
- Applying Clarity, Precision, and Thoroughness in SolidWorks Motion Analysis
- Defining Clear Objectives
- Setting Clear Goals for Motion Analysis Assignments
- Importance of a Comprehensive Understanding of Mechanical Systems
- Establishing a Solid Framework
- The Foundation of a Robust Model in SolidWorks Motion Analysis
- Defining Constraints, Materials, and Realistic Forces and Torques
- Systematic Approach to Motion Analysis
- Step-by-Step Procedure for SolidWorks Motion Analysis
- Starting with Basic Kinematic Analysis and Progressing to Dynamic Simulations
- Iterative Analysis and Optimization
- Benefits of Iterative Analysis in SolidWorks Motion Analysis
- Refining Simulations, Adjusting Parameters, and Optimizing Designs
- Documentation and Communication
- The Importance of Clear Documentation in SolidWorks Motion Analysis
- Communicating Assumptions, Inputs, and Results Effectively
- Incorporating Real-world Constraints
- Simulating Real-world Conditions in SolidWorks Motion Analysis
- Considering Friction, Damping, and External Loads as Physical Constraints
- Collaboration and Peer Review
- Embracing Collaboration for Complex Motion Problems
- The Value of Peer Reviews in Catching Errors and Improving Accuracy
- Conclusion
simulate and analyze the motion of mechanical systems. As students and professionals engage in assignments related to SolidWorks Motion Analysis, it becomes essential to adopt effective engineering principles to ensure accurate and insightful results. In this blog, we will explore the application of Harvard Engineering Principles in the context of SolidWorks Motion Analysis assignments.
Engineers often encounter complex challenges when analyzing the motion of mechanical systems, ranging from simple components to intricate assemblies. The precision required in these analyses demands a strategic approach, and this is where Harvard Engineering Principles come into play. By integrating these principles into SolidWorks Motion Analysis assignments, individuals can navigate the intricacies of dynamic systems with heightened clarity and systematic problem-solving.
Harvard Engineering Principles, rooted in clarity, precision, and thoroughness, provide a framework that aligns seamlessly with the objectives of SolidWorks Motion Analysis. This amalgamation ensures not only the accurate representation of motion but also promotes a comprehensive understanding of the underlying engineering dynamics. As we delve into the subsequent sections, we'll unravel the specific ways in which these principles, when applied, can effectively complete your Motion Analysis assignment, enhancing the quality and reliability of motion analysis results.
Understanding Harvard Engineering Principles
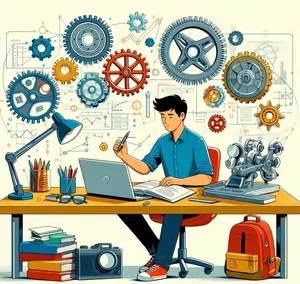
Harvard Engineering Principles serve as a guiding light in the realm of systematic problem-solving. These principles emphasize the need for a meticulous approach, underlining clarity, precision, and thoroughness in every engineering endeavor. In the context of SolidWorks Motion Analysis, understanding Harvard Engineering Principles involves recognizing the importance of these guiding tenets in shaping an analytical mindset.
Harvard's emphasis on precision aligns seamlessly with the demands of motion analysis tasks, where even the slightest deviations can impact the accuracy of results. By dissecting Harvard Engineering Principles and exploring their application within the SolidWorks Motion Analysis framework, we can lay the groundwork for a methodical and insightful engineering analysis.
Overview of Harvard Engineering Principles
Harvard Engineering Principles serve as a guiding light in engineering problem-solving, emphasizing clarity, precision, and thoroughness. These principles, established at the renowned Harvard School of Engineering and Applied Sciences, are foundational to achieving effective solutions. In the context of SolidWorks Motion Analysis, understanding these principles is key to elevating the quality of engineering analyses.
Applying Clarity, Precision, and Thoroughness in SolidWorks Motion Analysis
Applying Harvard Engineering Principles to SolidWorks Motion Analysis involves a meticulous approach. Clarity in defining objectives, precision in modeling mechanical systems, and thoroughness in analysis are paramount. This section will delve into practical strategies for incorporating these principles, ensuring that each step of the motion analysis process aligns with the rigorous standards advocated by Harvard's engineering philosophy.
Defining Clear Objectives
Clear objectives serve as the cornerstone of any successful SolidWorks Motion Analysis assignment. In the realm of engineering, precision in defining goals is paramount. For SolidWorks Motion Analysis, this involves not only setting specific objectives but also establishing a roadmap for achieving them. Engineers must articulate the purpose of the analysis, whether it's understanding the kinematics of a linkage or assessing the dynamic behavior of a complex mechanism.
A key aspect of defining clear objectives is to ensure alignment with broader project goals and design criteria. This section will delve into the intricacies of setting precise objectives in SolidWorks Motion Analysis assignments, emphasizing the importance of clarity in articulating the goals to drive the simulation process effectively.
Setting Clear Goals for Motion Analysis Assignments
In the realm of SolidWorks Motion Analysis, setting clear objectives is paramount for successful outcomes. Engineers must articulate the specific goals they aim to achieve through the simulation. Whether it's understanding the behavior of a particular mechanism or optimizing the performance of a complex assembly, establishing precise objectives serves as a roadmap for the entire analysis process. This ensures that the focus remains on relevant parameters, contributing to the efficiency and effectiveness of the motion analysis assignment.
Importance of a Comprehensive Understanding of Mechanical Systems
A thorough understanding of the mechanical system under analysis is foundational to the success of SolidWorks Motion Analysis assignments. Beyond merely defining the geometry, engineers must delve into the intricacies of the system's functionality and its interactions. This comprehensive understanding enables the incorporation of accurate constraints and inputs, laying the groundwork for realistic simulations. The Harvard Engineering Principles emphasize the significance of this holistic approach, advocating for precision in modeling and a keen awareness of the mechanical intricacies involved. Through this approach, engineers can extract more meaningful insights from their motion analysis endeavors.
Establishing a Solid Framework
In the realm of SolidWorks Motion Analysis assignments, establishing a solid framework is paramount for accurate simulations. This involves creating a robust model that serves as the foundation for a comprehensive analysis. Engineers must pay meticulous attention to defining constraints, specifying materials, and inputting realistic forces and torques. The intricacies of mechanical systems demand a methodical approach, and a solid framework ensures that the simulated motion aligns with real-world behavior. Harvard Engineering Principles, emphasizing clarity and precision, find resonance in this phase, guiding engineers to lay the groundwork for a reliable motion analysis. As we delve into the subsequent discussions, the significance of this foundational step in achieving accurate and meaningful results will become increasingly evident.
The Foundation of a Robust Model in SolidWorks Motion Analysis
Creating a robust model is the cornerstone of a successful SolidWorks Motion Analysis assignment. A robust model not only accurately represents the physical system but also allows for a more realistic simulation of motion. In this context, Harvard Engineering Principles emphasize the need for precision and thoroughness. Engineers must meticulously define the parameters of the model, considering factors such as geometry, mass properties, and component interactions.
Constructing a robust model involves a detailed understanding of the mechanical system, ensuring that it mirrors the real-world conditions as closely as possible. By adhering to Harvard Engineering Principles, individuals can approach model-building with clarity and a systematic methodology. This section will delve into the critical aspects of constructing a robust model and the application of Harvard Engineering Principles to achieve this goal.
Defining Constraints, Materials, and Realistic Forces and Torques
Beyond the geometry and mass properties, the effectiveness of a SolidWorks Motion Analysis hinges on the accurate definition of constraints, materials, and forces. Harvard Engineering Principles advocate for a meticulous approach to these aspects, emphasizing the importance of real-world accuracy. Constraints should be carefully applied to replicate physical limitations, materials chosen judiciously to mimic actual properties, and forces and torques realistically applied to ensure simulation validity.
By exploring these principles within the context of SolidWorks Motion Analysis assignments, engineers can elevate their understanding of how a robust framework directly impacts the precision and reliability of motion simulations. This section will provide insights into the strategic application of Harvard Engineering Principles when defining constraints, materials, and realistic forces and torques in SolidWorks Motion Analysis.
Systematic Approach to Motion Analysis
Harvard Engineering Principles advocate for a systematic approach to problem-solving, and this holds true in the realm of SolidWorks Motion Analysis. When undertaking assignments related to motion analysis, a systematic approach involves breaking down the complex task into logical steps. This not only facilitates a more organized workflow but also ensures that each aspect of the analysis is thoroughly addressed.
In the context of SolidWorks Motion Analysis assignments, adopting a systematic approach begins with a meticulous examination of the system's kinematics. Engineers must carefully define the relationships between components, specifying constraints and degrees of freedom. This foundational step lays the groundwork for subsequent dynamic simulations.
Following the kinematic analysis, engineers can progress to dynamic simulations, introducing forces, torques, and external influences. This step-by-step progression aligns with the systematic problem-solving advocated by Harvard Engineering Principles, fostering a methodical exploration of the mechanical system's behavior.
A systematic approach not only enhances the accuracy of results but also facilitates troubleshooting and optimization. By methodically addressing each element of the motion analysis process, engineers can uncover insights, refine their models, and achieve a more comprehensive understanding of the system's behavior. This section will further elaborate on the benefits and nuances of adopting a systematic approach in SolidWorks Motion Analysis assignments.
Step-by-Step Procedure for SolidWorks Motion Analysis
In the realm of SolidWorks Motion Analysis, a systematic approach is paramount for achieving precise and reliable results. A step-by-step procedure ensures that each phase of the analysis is meticulously addressed. Commencing with a clear definition of the problem at hand, engineers can then progress to establishing constraints, defining materials, and specifying forces and torques. This structured procedure not only streamlines the simulation setup but also facilitates a comprehensive understanding of the mechanical system's behavior throughout the motion.
Starting with Basic Kinematic Analysis and Progressing to Dynamic Simulations
A fundamental aspect of Harvard Engineering Principles is the progression from simplicity to complexity. Applying this principle to SolidWorks Motion Analysis, engineers begin by conducting a basic kinematic analysis. This initial phase lays the groundwork, focusing on the study of motion without considering forces. Subsequently, the analysis evolves to dynamic simulations, introducing forces and torques to replicate real-world conditions. This staged approach allows for a more in-depth exploration of the mechanical system's behavior, ensuring a thorough examination of both kinematics and dynamics for a comprehensive motion analysis.
Iterative Analysis and Optimization
Iterative analysis and optimization constitute a pivotal phase in SolidWorks Motion Analysis assignments. Engineers embark on this journey to refine simulations, fine-tune parameters, and optimize designs for superior performance. The iterative process, a cornerstone of Harvard Engineering Principles, aligns seamlessly with this stage, promoting continuous improvement.
Within the realm of SolidWorks Motion Analysis, engineers often encounter multifaceted challenges that necessitate refining the initial simulation based on preliminary results. This iterative approach enables a dynamic exploration of design variations, contributing to a more robust and optimized solution. By adjusting parameters and systematically evaluating the impact on motion dynamics, engineers can fine-tune their models and achieve outcomes that align more closely with real-world scenarios. This iterative methodology not only enhances the accuracy of results but also instills a sense of adaptability and resilience in the face of evolving engineering challenges. As we delve deeper into this section, we will uncover the nuances of iterative analysis and optimization, emphasizing its integral role in achieving superior outcomes in SolidWorks Motion Analysis assignments.
Benefits of Iterative Analysis in SolidWorks Motion Analysis
Iterative analysis plays a pivotal role in SolidWorks Motion Analysis, offering a range of benefits. Firstly, it allows engineers to progressively refine their simulations by identifying and rectifying inaccuracies. This iterative process enhances the accuracy of results, ensuring a closer alignment with real-world scenarios. Moreover, it facilitates a deeper exploration of various design alternatives, enabling engineers to gain valuable insights into the dynamic behavior of mechanical systems. Iterative analysis also contributes to a more robust understanding of the impact of different parameters on the overall motion, laying the groundwork for informed decision-making in engineering assignments.
Refining Simulations, Adjusting Parameters, and Optimizing Designs
Refining simulations, adjusting parameters, and optimizing designs are integral steps in the SolidWorks Motion Analysis workflow. Engineers engage in a meticulous process of fine-tuning simulation settings to achieve results that accurately reflect the behavior of the studied system. Adjusting parameters, such as material properties or contact conditions, allows for a nuanced exploration of design variations. This not only enhances the overall accuracy of the analysis but also empowers engineers to optimize their designs for improved performance. The iterative nature of this refinement process ensures that the final simulation output is not only reliable but also aligns closely with the intended engineering objectives.
Documentation and Communication
Clear documentation and effective communication are pivotal aspects of any engineering endeavor, and SolidWorks Motion Analysis assignments are no exception. In the realm of motion analysis, meticulous documentation serves as a record of assumptions, inputs, methodologies, and results, ensuring a transparent and reproducible process.
Thorough documentation not only aids in personal understanding but also facilitates collaboration by providing a roadmap for others who may review or build upon the analysis. It acts as a comprehensive guide, enabling fellow engineers, researchers, or instructors to grasp the intricacies of the SolidWorks Motion Analysis undertaken. This emphasis on documentation aligns seamlessly with the Harvard Engineering Principles, promoting clarity and precision in conveying complex engineering analyses. In the subsequent sections, we will delve into the nuances of effective documentation and communication within the context of SolidWorks Motion Analysis assignments.
The Importance of Clear Documentation in SolidWorks Motion Analysis
Clear documentation in SolidWorks Motion Analysis is a cornerstone for ensuring transparency and repeatability in engineering analyses. Documenting the entire process, including the setup, boundary conditions, and key parameters, not only provides a record for future reference but also enables colleagues to replicate and validate the results. This practice aligns with Harvard Engineering Principles, emphasizing the need for precision and clarity in every engineering endeavor. Thorough documentation serves as a valuable resource for troubleshooting, peer review, and continuous improvement in the simulation process.
Communicating Assumptions, Inputs, and Results Effectively
Effective communication is pivotal in conveying the nuances of SolidWorks Motion Analysis. Clearly articulating assumptions made during the simulation, input parameters chosen, and the resultant outcomes is crucial for fostering collaboration and understanding. Harvard Engineering Principles highlight the significance of communication in engineering solutions, emphasizing that insights gained from motion analysis are most impactful when shared with clarity. By adhering to these principles, professionals and students can enhance their ability to articulate complex engineering concepts, facilitating better collaboration and knowledge dissemination within the engineering community.
Incorporating Real-world Constraints
The realm of SolidWorks Motion Analysis extends beyond theoretical simulations, emphasizing the need to incorporate real-world constraints for a more authentic representation of mechanical behavior. In this phase of the analysis, engineers delve into the intricacies of physical constraints such as friction, damping, and external loads, mirroring the challenges encountered in actual operating environments.
Understanding and integrating these real-world constraints not only enhances the accuracy of SolidWorks Motion Analysis but also ensures that the simulated results align closely with the performance expectations of the physical system. This section explores the significance of incorporating these constraints and sheds light on how it contributes to the overall fidelity and practicality of motion analysis assignments.
Simulating Real-world Conditions in SolidWorks Motion Analysis
SolidWorks Motion Analysis excels in its ability to replicate real-world conditions, providing engineers with a dynamic platform for exploring mechanical systems. To simulate real-world conditions effectively, it's crucial to meticulously incorporate parameters such as friction, damping, and external loads. Friction, a fundamental force in mechanical interactions, influences the accuracy of motion analysis. By accounting for different friction coefficients, engineers can enhance the fidelity of simulations. Similarly, incorporating damping characteristics ensures a more realistic representation of system behavior, particularly in scenarios involving oscillations or vibrations. External loads, such as applied forces or torques, introduce dynamic challenges that further enrich the simulation, mirroring the complexities encountered in actual mechanical systems.
Considering Friction, Damping, and External Loads as Physical Constraints
Friction, damping, and external loads serve as inherent physical constraints in mechanical systems. In SolidWorks Motion Analysis, acknowledging and integrating these constraints is pivotal for an accurate representation of real-world scenarios. Frictional forces, arising from surface interactions, impact the motion and energy balance within a system. A nuanced understanding of frictional effects enables engineers to refine simulations and predict behavior more precisely. Damping, associated with energy dissipation, becomes crucial in scenarios where mechanical systems exhibit oscillations or vibrations. By incorporating damping as a physical constraint, engineers can replicate scenarios closer to reality. Additionally, factoring in external loads, whether gravitational forces or applied torques, completes the picture, allowing for a holistic analysis that considers all relevant physical constraints in SolidWorks Motion Analysis assignments.
Collaboration and Peer Review
In the realm of SolidWorks Motion Analysis assignments, collaboration and peer review emerge as integral components for ensuring the accuracy and validity of the results. Engineering challenges, especially those involving dynamic systems, often benefit from diverse perspectives and collective problem-solving. Collaborative efforts bring together the strengths of individuals, allowing for a more comprehensive examination of the motion analysis process.
Engaging in peer reviews further enhances the quality of SolidWorks Motion Analysis assignments. A fresh set of eyes can catch potential errors, offer alternative insights, and contribute to refining the overall analysis. Through collaborative endeavors and peer feedback, engineers and students not only validate their findings but also cultivate a culture of continuous improvement, aligning with the principles of precision and thoroughness advocated by Harvard Engineering Principles. This collaborative approach fosters a dynamic learning environment where knowledge and expertise converge to elevate the standards of motion analysis within the SolidWorks framework.
Embracing Collaboration for Complex Motion Problems
Collaboration is paramount when tackling intricate motion problems within SolidWorks assignments. Engaging in collective problem-solving brings together diverse perspectives, each contributing valuable insights. Engineers collaborating on SolidWorks Motion Analysis assignments can pool their expertise, share ideas, and collectively address challenges. This collaborative approach not only fosters creativity but also accelerates the resolution of complex motion problems. By embracing collaboration, individuals can tap into a wealth of collective knowledge, ensuring a more robust and innovative solution to intricate motion challenges.
The Value of Peer Reviews in Catching Errors and Improving Accuracy
Peer reviews play a pivotal role in refining SolidWorks Motion Analysis assignments by providing an additional layer of scrutiny. Engaging colleagues to review the simulation setup, assumptions, and results helps catch potential errors that might have been overlooked. This iterative process ensures the accuracy and reliability of the analysis. The value of constructive feedback from peers cannot be overstated; it not only identifies errors but also offers alternative perspectives and suggestions for improvement. Through meticulous peer reviews, engineers can enhance the accuracy of their SolidWorks Motion Analysis assignments, contributing to a more rigorous and dependable final outcome.
Conclusion
Incorporating Harvard Engineering Principles into SolidWorks Motion Analysis assignments can significantly enhance the quality and reliability of results. These principles act as guiding lights, ensuring that engineers and students approach motion analysis with a holistic and strategic mindset. The emphasis on clear objectives ensures that the goals of the analysis are well-defined, providing a roadmap for a more focused and purposeful study.
Establishing a solid framework becomes the cornerstone of a successful SolidWorks Motion Analysis assignment. This involves meticulous attention to detail in defining constraints, specifying materials, and accurately inputting forces and torques. A robust model serves as the foundation for precise simulations, allowing for a deeper understanding of the mechanical system under study.
The systematic approach recommended by Harvard Engineering Principles encourages individuals to break down the motion analysis process into manageable steps. Starting with basic kinematic analysis before delving into dynamic simulations ensures a thorough understanding of the system's behavior at each stage. This step-by-step methodology not only enhances accuracy but also facilitates a more efficient problem-solving process.
The principles of iteration and optimization further contribute to the refinement of SolidWorks Motion Analysis assignments. Engineers and students are urged to embrace the idea of continuous improvement, refining simulations based on initial results, adjusting parameters, and optimizing designs for better performance. This iterative process not only enhances the accuracy of the analysis but also encourages a mindset of perpetual learning and enhancement.
Documentation and communication, as highlighted by Harvard Engineering Principles, play a crucial role in ensuring the transparency and reproducibility of SolidWorks Motion Analysis. Thorough documentation of assumptions, inputs, and results allows for a comprehensive review and understanding of the analysis process. Effective communication further facilitates knowledge transfer, enabling others to build upon the work and contribute to the collective understanding of motion analysis principles.
Collaboration and peer review, the final aspects of Harvard Engineering Principles discussed in this blog, underscore the importance of collective wisdom. Engaging in collaborative efforts for solving complex motion problems leverages diverse perspectives and accelerates the problem-solving process. Peer reviews provide a valuable checkpoint, catching errors, offering alternative viewpoints, and ultimately improving the accuracy and reliability of the analysis.
As you embark on your next SolidWorks Motion Analysis assignment, remember to apply these principles. By doing so, you will not only unlock the full potential of SolidWorks Motion Analysis but also contribute to a culture of excellence and continuous improvement within the realm of engineering analysis. These principles transcend individual assignments, shaping a mindset that seeks to optimize, refine, and advance motion analysis techniques for a more comprehensive and insightful engineering analysis.