- Understanding SolidWorks Motion Analysis
- Case Study 1: Automotive Suspension System Optimization
- Case Study 2: Robotics Arm Dynamics
- Case Study 3: Aerospace Mechanism Simulation
- Case Study 4: Marine Propulsion System Optimization
- Benefits of SolidWorks Motion Analysis for Students
- Conclusion
SolidWorks Motion Analysis is undeniably a game-changer in the field of engineering, offering engineers an unparalleled ability to simulate and meticulously analyze the dynamic behavior of their designs. As technology continues to advance, the demand for comprehensive simulation tools like SolidWorks Motion Analysis is on the rise, making it imperative for students to delve into its real-world applications. Exploring SolidWorks Motion Analysis and its real-world applications is crucial for mastering engineering simulation techniques and enhancing your understanding of dynamic behavior in engineering designs.
In the dynamic realm of engineering, where the performance and reliability of designs are paramount, SolidWorks Motion Analysis emerges as a crucial ally. Its capabilities go beyond static analysis, allowing engineers to comprehend how components interact over time, providing a holistic view of the system's behavior. The significance of such simulation tools cannot be overstated, particularly in industries where precision and efficiency are non-negotiable.
To truly grasp the impact of SolidWorks Motion Analysis, let's embark on a journey through captivating case studies that exemplify its real-world applications. These cases not only showcase the versatility of the tool but also serve as invaluable learning experiences for students aspiring to navigate the complexities of engineering simulation.
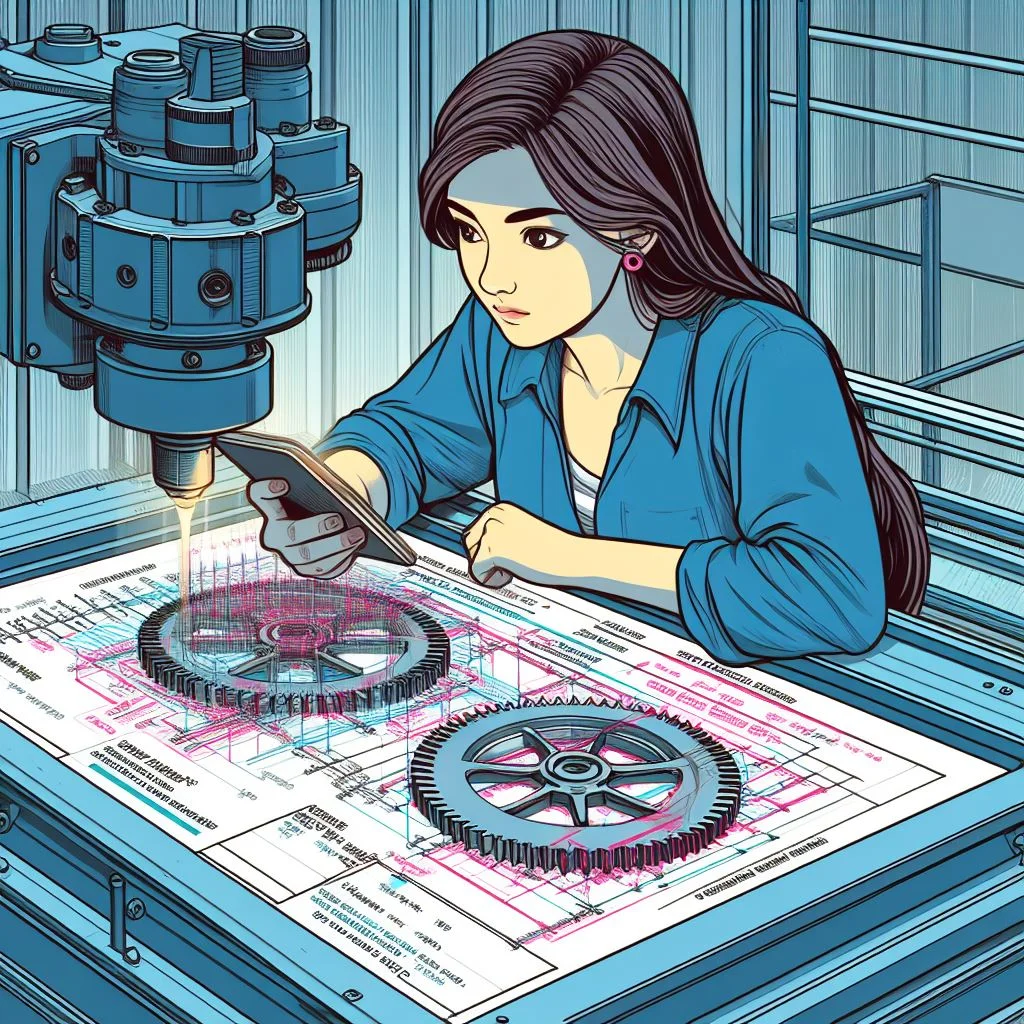
Case Study 1 takes us into the realm of automotive engineering, where the optimization of a sports car's suspension system becomes the focal point. The challenges faced by engineers, such as stability and responsiveness issues, resonate with the intricate nature of real-world design problems. Through SolidWorks Motion Analysis, the virtual tinkering with spring rates, damping coefficients, and linkages mirrors the hands-on adjustments that engineers would make in a physical setting. The results, improved stability, enhanced handling, and superior ride comfort, underscore the transformative potential of SolidWorks Motion Analysis in automotive design.
In Case Study 2, the spotlight shifts to robotics, a field where precision and speed are paramount. The challenges faced with accuracy and speed in a robotic arm's dynamics find resonance with the day-to-day struggles of engineers in this domain. SolidWorks Motion Analysis steps in as a virtual testing ground, allowing for the optimization of joint movements, reduction of inertia, and refinement of control algorithms. The outcomes, increased accuracy and speed in operations, mirror the tangible improvements that engineers aim to achieve when dealing with real-world robotic systems.
The third case study propels us into the aerospace industry, where the simulation of a complex aerospace mechanism becomes a critical endeavor. The challenges here are multifaceted, ranging from intricate moving parts to the need for reliability under extreme conditions. SolidWorks Motion Analysis facilitates a meticulous examination of the aerospace mechanism's behavior, enabling engineers to identify and address potential issues. The results, a robust and reliable aerospace mechanism, echo the real-world imperative of ensuring the safety and efficiency of aerospace components.
As students navigate these case studies, they gain not just theoretical knowledge but a profound understanding of the practical applications of SolidWorks Motion Analysis. The tool becomes a virtual laboratory, where they can witness the direct impact of their decisions on the performance of complex systems.
In addition to its real-world applicability, SolidWorks Motion Analysis offers students a unique opportunity to hone their problem-solving skills. The complexity of the case studies necessitates a strategic and analytical approach. Students must analyze, iterate, and optimize, mirroring the processes that engineers undertake in their professional journeys.
Moreover, the hands-on experience with SolidWorks Motion Analysis serves as a bridge between academic learning and real-world application. As students engage with the tool, they not only understand the theoretical underpinnings of engineering simulation but also develop a practical skill set that is directly transferable to their future careers.
Understanding SolidWorks Motion Analysis
Understanding SolidWorks Motion Analysis is essential for engineers seeking comprehensive insights into the dynamic behavior of mechanical systems. This robust tool enables users to simulate the intricate movement of assemblies and meticulously assess how individual components interact over time. By offering a virtual environment for testing and analysis, SolidWorks Motion Analysis becomes an indispensable asset in the engineering toolkit.
The predictive capabilities of SolidWorks Motion Analysis play a pivotal role in the design and optimization of mechanical systems. Engineers can explore different scenarios, assessing the impact of various factors on the overall performance of their designs. This not only facilitates the identification of potential issues but also allows for informed decision-making in the early stages of the design process.
Moreover, the tool aids in fine-tuning mechanical systems for optimal functionality. Engineers can adjust parameters such as motion constraints, material properties, and external forces to observe their effects on the system's behavior. This level of precision empowers designers to optimize performance, enhance efficiency, and ensure the reliability of their creations.
SolidWorks Motion Analysis is particularly valuable for simulating dynamic events, such as the motion of machinery, vehicle components, or robotic arms. Engineers can analyze the response of these systems to different inputs, ensuring that they meet performance requirements and safety standards. The tool's ability to provide a detailed understanding of how components move and interact over time contributes significantly to the success of engineering projects.
Case Study 1: Automotive Suspension System Optimization
In this compelling case study, we explore the application of SolidWorks Motion Analysis in optimizing the suspension system of a high-performance sports car. The challenges faced and the subsequent solutions employed shed light on the transformative impact of simulation in the automotive design process.
The initial design of the sports car's suspension system encountered hurdles related to stability and responsiveness. Engineers grappled with the task of enhancing the overall performance of the vehicle, seeking solutions to address these critical issues.
To overcome the challenges, engineers turned to SolidWorks Motion Analysis, leveraging its capabilities to simulate the dynamic behavior of the suspension system. Through virtual experimentation, adjustments to spring rates, damping coefficients, and linkages were meticulously made. The simulation allowed engineers to observe and analyze the system's response under different conditions.
The optimized suspension system yielded significant improvements, not only in the vehicle's stability but also in its handling and ride comfort. The virtual adjustments made through SolidWorks Motion Analysis translated into real-world enhancements, showcasing the tool's efficacy in refining automotive designs. The sports car now demonstrated superior performance characteristics, a testament to the power of simulation in achieving optimal engineering solutions.
This case study serves as a poignant example of how SolidWorks Motion Analysis can play a crucial role in the iterative design process of complex systems, offering engineers valuable insights before physical prototypes are even built. It underscores the importance of simulation in achieving superior performance, efficiency, and comfort in automotive engineering.
Case Study 2: Robotics Arm Dynamics
In this case study, the focus was on employing SolidWorks Motion Analysis to gain insights into the dynamics of a robotic arm and subsequently improve its performance. The initial challenges were centered around the need to enhance the robotic arm's precision and reduce the time required to execute specific tasks.
Engineers utilized SolidWorks Motion Analysis to simulate the intricate movements of the robotic arm. This involved a comprehensive analysis of its behavior under varying conditions, allowing for a detailed examination of joint movements, inertia reduction, and the fine-tuning of control algorithms.
The results of this simulation were impactful. The optimized robotic arm displayed a marked improvement in both accuracy and speed during its operations. The precision achieved through the analysis and adjustments made using SolidWorks Motion Analysis translated into enhanced efficiency for the robotic system.
This case study serves as a testament to the instrumental role that SolidWorks Motion Analysis can play in refining and optimizing the performance of robotic systems. The ability to simulate and analyze complex movements not only leads to improved functionality but also contributes to the overall advancement of automation technology.
By leveraging SolidWorks Motion Analysis, engineers can fine-tune the design and operation of robotic arms, ensuring they meet the high standards of accuracy and efficiency demanded by modern industrial applications. This case study underscores the practical application of simulation tools in addressing real-world challenges and driving innovation in the field of robotics.
Case Study 3: Aerospace Mechanism Simulation
This case study sheds light on the practical application of SolidWorks Motion Analysis in the simulation of a sophisticated aerospace mechanism. The aerospace industry demands precision and reliability, making motion analysis a critical aspect of the design process.
Engineers faced substantial challenges in ensuring the reliability of the aerospace mechanism, which comprised intricate moving parts. The design had to withstand not only high-speed maneuvers but also extreme temperatures associated with various operational conditions.
SolidWorks Motion Analysis emerged as the go-to solution for addressing these challenges. Engineers conducted a meticulous motion analysis using the software, allowing them to simulate the behavior of the aerospace mechanism in a spectrum of scenarios. This in-depth analysis enabled the identification of potential issues and shortcomings in the design.
The simulation process in SolidWorks went beyond a simple visual representation. It involved a detailed examination of how each component within the aerospace mechanism interacted with others under different conditions. This comprehensive understanding was instrumental in making informed decisions to optimize the system for optimal performance.
The results of the simulation were nothing short of remarkable. The aerospace mechanism, post-adjustments based on SolidWorks Motion Analysis insights, demonstrated robustness and reliability under diverse operating conditions. The software not only identified potential issues but also provided a platform for engineers to fine-tune the design, ensuring the safety and efficiency of the aerospace component.
This case study stands as a testament to the pivotal role SolidWorks Motion Analysis can play in the aerospace industry, where precision and reliability are paramount. By leveraging simulation tools, engineers can refine designs to meet the stringent requirements of high-performance aerospace applications, ultimately contributing to the advancement of aviation technology.
Case Study 4: Marine Propulsion System Optimization
In this additional case study, we explore the application of SolidWorks Motion Analysis in optimizing the propulsion system of a marine vessel. The challenges encountered and the solutions derived provide a comprehensive view of the software's versatility in diverse engineering applications.
The marine propulsion system initially grappled with challenges related to efficiency and fuel consumption. The objective was to improve the overall performance of the vessel by addressing these crucial factors.
SolidWorks Motion Analysis was employed to simulate the marine propulsion system's dynamics, allowing engineers to delve into the intricacies of its operation. Virtual adjustments were made to parameters such as propeller pitch, blade design, and engine power to optimize the system's performance.
The optimized propulsion system showcased remarkable improvements in efficiency, leading to reduced fuel consumption and enhanced maneuverability. SolidWorks Motion Analysis proved instrumental in fine-tuning the complex interplay of components, resulting in a more environmentally friendly and cost-effective marine propulsion solution.
This case study exemplifies how SolidWorks Motion Analysis extends its applicability beyond land-based vehicles, demonstrating its effectiveness in marine engineering. By providing a virtual environment for experimentation, engineers can refine designs with precision, ensuring optimal performance in real-world maritime conditions. The success achieved in this marine propulsion optimization reaffirms the software's role as a valuable asset in the continuous pursuit of engineering excellence.
Benefits of SolidWorks Motion Analysis for Students
SolidWorks Motion Analysis case studies offer students a tangible bridge between theoretical knowledge and real-world applications, fostering a profound understanding of how engineering simulation operates in practical scenarios. This exposure equips students with a pragmatic skill set that extends far beyond the boundaries of theoretical concepts, laying the groundwork for the challenges they will encounter in their professional journeys.
Engagement with these case studies acts as a crucible for the development of students' critical thinking and problem-solving abilities. As they navigate through the intricacies of simulated scenarios, students learn to dissect complex engineering problems, identifying pivotal parameters that impact the performance of mechanical systems. This process cultivates a mindset where students not only grasp the theoretical aspects but also acquire the ability to make judicious decisions aimed at optimizing designs for real-world applications.
The hands-on experience gained through working with SolidWorks Motion Analysis in a classroom setting is pivotal for students transitioning from academic studies to professional roles. Interacting with industry-standard simulation software provides a unique opportunity for students to familiarize themselves with the tools and methodologies widely employed in the engineering sector. This practical experience not only hones their technical proficiency but also instills a level of confidence that proves invaluable as they step into the dynamic realm of engineering practice.
In essence, the benefits derived from SolidWorks Motion Analysis for students extend beyond the confines of traditional learning. These case studies become a conduit for transforming theoretical knowledge into practical acumen, nurturing problem-solving skills, and offering hands-on experience that acts as a launchpad for their future careers in the field of engineering.
Conclusion
In conclusion, SolidWorks Motion Analysis stands as a pivotal tool that not only facilitates a comprehensive understanding of engineering simulation but also bridges the gap between theoretical knowledge and practical application. The case studies examined in this exploration highlight the tool's versatility and significant impact across diverse industries, unraveling valuable insights for budding engineers embarking on their professional journeys.
Through these real-world applications, students gain a profound insight into the intricacies of design optimization, system dynamics, and performance enhancement. The automotive suspension system optimization case study underscored how SolidWorks Motion Analysis can tackle challenges related to stability and responsiveness, ultimately contributing to improved vehicle performance. Similarly, the exploration of robotics arm dynamics showcased the tool's efficacy in refining precision and speed in robotic operations, addressing critical aspects of automation and control.
The aerospace mechanism simulation delved into the complex realm of aviation, demonstrating how SolidWorks Motion Analysis ensures reliability under varying conditions, ranging from high-speed maneuvers to extreme temperatures. These case studies collectively emphasize the adaptability of SolidWorks Motion Analysis across different engineering domains, instilling in students a holistic perspective on the tool's applicability.
Moreover, the benefits extended to students extend beyond mere theoretical comprehension. Engaging with SolidWorks Motion Analysis case studies fosters enhanced problem-solving skills as students grapple with real-world engineering challenges. The practical application of theoretical knowledge becomes evident as they learn to dissect complex problems, identify key parameters, and iteratively optimize designs. This process not only hones their analytical abilities but also prepares them for the multifaceted challenges awaiting them in professional settings.
Furthermore, the hands-on experience gained through interaction with SolidWorks Motion Analysis in a classroom environment is invaluable. Students are provided with a platform to familiarize themselves with industry-standard simulation software, empowering them to transition seamlessly from academic settings to real-world engineering scenarios. This experiential learning approach ensures that students not only comprehend the theoretical underpinnings of engineering simulation but also acquire the skills necessary to navigate the complexities of their future roles.
In essence, SolidWorks Motion Analysis becomes a conduit for students to bridge the gap between academia and industry. It is not just a software tool but a gateway to a deeper understanding of the practical applications of engineering principles. The tool's ability to simulate and analyze dynamic behaviors in diverse contexts equips students with a skill set that is not only relevant but also highly sought after in the professional landscape.
As we conclude this exploration, it is evident that SolidWorks Motion Analysis serves as a guiding beacon for students, illuminating the path towards a more nuanced understanding of engineering dynamics. The case studies and the insights gained from practical applications empower students to become adept problem solvers and critical thinkers, ready to make significant contributions to the ever-evolving field of engineering. SolidWorks Motion Analysis is not just a software tool; it is a catalyst for the transformation of aspiring engineers into proficient professionals, poised to shape the future of engineering innovation.