- Understanding the Basics of SolidWorks Motion Analysis
- Advanced Contact and Friction Modeling in SolidWorks Motion
- Incorporating External Loads and Forces
- Optimization Techniques for Efficient Motion Analysis
- Fine-Tuning Motion Profiles for Realistic Simulations
- Utilizing Sensors for Data-driven Motion Analysis
- Integrating SolidWorks Motion with Other Simulation Tools
- Troubleshooting Common Issues in Motion Analysis
- Case Studies: Real-world Applications of Advanced Motion Analysis
- Conclusion:
SolidWorks Motion Analysis stands as a cornerstone for engineering students, offering a robust platform to simulate and scrutinize the dynamic intricacies of their design creations. It transcends the realm of static models, allowing a comprehensive exploration of how components interact in a dynamic environment. As we venture deeper into the blog, the focus shifts towards unraveling the intricacies of advanced techniques within SolidWorks Motion Analysis, thereby equipping students with invaluable insights to navigate the complexities of this indispensable tool. If you need assistance with your Motion Analysis assignment, this comprehensive exploration of SolidWorks Motion Analysis can provide valuable insights and information to support your understanding and completion of Motion Analysis assignments.
This tool serves as a virtual playground, enabling students to bring their designs to life in a simulated environment. By comprehending the dynamic behavior of their creations, engineers can refine and optimize their designs before physical prototypes are even considered. SolidWorks Motion Analysis offers a nuanced understanding of how forces, loads, and motions influence a design's performance, providing a level of precision that is essential for the modern engineer.
The journey into advanced techniques within SolidWorks Motion Analysis begins with a foundational grasp of its basics. Users must acquaint themselves with the software's capabilities to harness its full potential. This encompasses understanding how to set up motion studies, define mates, and establish the initial conditions that govern the simulation. As students navigate this fundamental terrain, they lay the groundwork for the more intricate aspects of motion analysis.
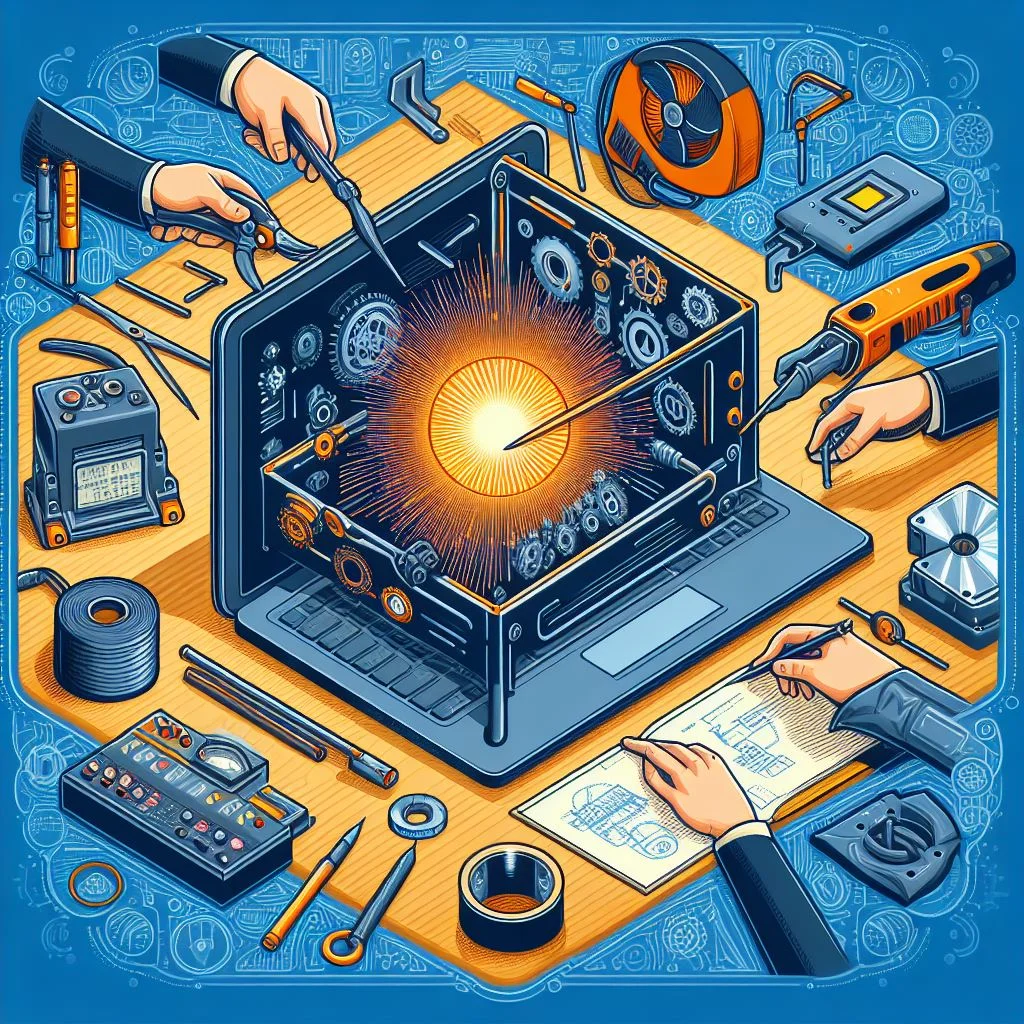
Moving beyond the basics, the exploration of advanced contact and friction modeling becomes paramount. This facet injects a dose of reality into simulations, mirroring the frictional forces and contact interactions present in real-world scenarios. Engineers gain the ability to predict and analyze the behavior of intricate assemblies, ensuring that their designs are not just aesthetically pleasing but also functionally robust.
A pivotal advancement in SolidWorks Motion Analysis involves the incorporation of external loads and forces. By assimilating these dynamic elements into simulations, students can gauge how their designs respond under various conditions. This capability proves instrumental in designing products that withstand the unpredictable forces encountered in the real world, whether it be the impact of external loads or the forces generated by moving components.
Optimization becomes the next frontier. Advanced users delve into techniques that streamline the simulation process, reducing computation times without compromising accuracy. This efficiency proves crucial when dealing with complex assemblies or when iterating through design variations. A well-optimized motion analysis workflow can significantly enhance productivity, allowing engineers to focus on the finer nuances of design rather than waiting for simulations to conclude.
Fine-tuning motion profiles emerges as an art within SolidWorks Motion Analysis. Engineers seek to achieve simulations that not only replicate real-world scenarios but do so with a level of precision that mirrors the intended dynamic behavior of their designs. This involves meticulous adjustments to motion profiles, ensuring that the simulated motion aligns seamlessly with the envisioned functionality of the product.
In the realm of data-driven insights, sensors take center stage. SolidWorks Motion Analysis allows users to strategically place sensors within the virtual environment, capturing valuable data during simulations. This data-driven approach empowers engineers to make informed decisions based on real-time feedback, paving the way for designs that are not just theoretically sound but practically robust.
As the exploration continues, integration with other simulation tools emerges as a powerful capability. SolidWorks Motion Analysis seamlessly interfaces with structural and thermal analysis tools, providing a comprehensive understanding of how various aspects such as motion, structure, and heat interact. This holistic approach equips engineers with a multifaceted view, essential for creating designs that not only move seamlessly but also endure the structural and thermal challenges encountered in real-world applications.
However, no journey is without its challenges. Troubleshooting common issues in Motion Analysis becomes a skill in itself. Even seasoned users face hurdles, whether it be unexpected behavior in simulations or convergence issues during analysis. Understanding how to identify and address these challenges is crucial for maintaining a smooth and efficient simulation workflow.
The narrative crescendos with real-world case studies that showcase the tangible impact of advanced Motion Analysis techniques. These stories offer a glimpse into how engineers have successfully applied these methods to overcome complex design challenges. From optimizing mechanical components to predicting the performance of intricate assemblies, these case studies serve as a wellspring of inspiration for students looking to apply advanced techniques in their own projects.
Understanding the Basics of SolidWorks Motion Analysis
SolidWorks Motion Analysis is a powerful tool that allows engineering students to simulate and analyze the dynamic behavior of their designs. Before delving into advanced techniques, it's crucial to establish a solid understanding of the basics of SolidWorks Motion Analysis. This foundational knowledge lays the groundwork for a more comprehensive grasp of the software's capabilities.
Understanding the Basics of SolidWorks Motion Analysis is essential for students embarking on their simulation journey. At its core, Motion Analysis allows users to simulate the motion of assemblies, considering factors like time, gravity, and various constraints. The fundamental principles include defining mates, specifying motion drivers, and setting up study properties.
One key aspect to master in the basics is the differentiation between assembly motion and part motion. Understanding how to define and control the motion of individual components within an assembly is paramount for accurate simulations. Students will also explore the significance of mates in constraining motion, ensuring that components move realistically based on real-world constraints.
Additionally, this section will delve into the importance of accurately defining materials, as material properties significantly impact the behavior of components during motion. A thorough grasp of these fundamental aspects forms a solid foundation, equipping students with the knowledge needed to navigate the more advanced features of SolidWorks Motion Analysis with confidence.
Advanced Contact and Friction Modeling in SolidWorks Motion
Enhance your Motion Analysis skills by exploring advanced contact and friction modeling. Learn how to accurately simulate real-world interactions between components, taking your simulations to the next level of realism.
Understanding the intricate nuances of component interactions is paramount in achieving accurate simulations. In advanced contact modeling, SolidWorks allows users to define precise contact areas and simulate the effects of contact forces during motion. This level of detail is crucial for applications where components interact dynamically, such as in assemblies with moving parts or mechanical systems with sliding or rotating elements.
Furthermore, delving into advanced friction modeling adds another layer of realism to your simulations. SolidWorks provides tools to define friction coefficients, allowing you to replicate the effects of frictional forces on moving parts. Mastering these advanced techniques empowers you to create simulations that closely mirror real-world scenarios, providing invaluable insights into the performance and behavior of your designs.
By honing your skills in advanced contact and friction modeling, you elevate your Motion Analysis proficiency, enabling you to tackle complex engineering challenges with greater precision and confidence.
Incorporating External Loads and Forces
Understanding how to incorporate external loads and forces into your SolidWorks Motion Analysis is pivotal for a comprehensive analysis of your designs. By applying dynamic loads, you gain the ability to simulate a variety of real-world scenarios, ensuring your designs can withstand diverse conditions.
In SolidWorks Motion Analysis, external loads and forces can be simulated with precision, allowing you to evaluate the impact of different dynamic factors on your design's performance. Whether it's wind resistance, gravitational forces, or external impacts, the software empowers you to replicate these influences accurately.
This process involves defining the parameters of the external forces, such as magnitude, direction, and duration. SolidWorks Motion Analysis provides a user-friendly interface that simplifies the application of dynamic loads, making it accessible for both novice and experienced users.
By incorporating external loads and forces, you can observe how your design responds to varying conditions, helping you identify potential weaknesses and areas for improvement. This level of analysis goes beyond static considerations, providing a more realistic assessment of your design's behavior in a dynamic environment.
Mastering this aspect of SolidWorks Motion Analysis opens up a world of possibilities for students, allowing them to design and optimize products that can thrive in the face of real-world challenges. As you delve into this advanced technique, you'll gain valuable insights into the dynamic performance of your designs, setting the stage for more robust and resilient engineering solutions.
Optimization Techniques for Efficient Motion Analysis
Optimizing SolidWorks Motion Analysis simulations is crucial for maintaining efficiency in your design process. As projects grow in complexity, the need to streamline workflows, reduce computation times, and achieve precise results becomes paramount.
Efficiency begins with a strategic approach to setting up simulations. One key technique involves simplifying geometry without sacrificing accuracy. By refining the complexity of your models, you not only accelerate computation times but also enhance the overall simulation performance.
Additionally, judiciously selecting appropriate solver settings can significantly impact efficiency. Understanding the intricacies of solver options allows you to tailor settings to the specific requirements of your analysis, striking a balance between accuracy and computational speed.
Parallel processing is another optimization avenue worth exploring. Leveraging the power of multiple processors or cores can dramatically reduce simulation times, especially when dealing with intricate assemblies or extensive motion scenarios.
Furthermore, consider employing advanced meshing techniques. Fine-tuning mesh parameters can enhance the accuracy of results while simultaneously decreasing computation requirements. This delicate balance ensures that your simulations maintain precision without unnecessary computational overhead.
Lastly, take advantage of SolidWorks Motion Analysis features such as result plotting and data exporting. By selectively extracting and analyzing critical data points, you can focus on the most relevant aspects of your simulation, avoiding information overload and expediting the decision-making process.
Fine-Tuning Motion Profiles for Realistic Simulations
Achieving realistic simulations goes beyond mastering the basics of SolidWorks Motion Analysis; it demands a nuanced understanding of how to fine-tune motion profiles. This process is critical in ensuring that your simulations faithfully mirror the intended dynamic behavior of your designs.
To begin with, meticulous attention to detail is paramount. Precision in defining motion profiles sets the stage for simulations that closely mimic real-world scenarios. Understand the intricacies of motion types, whether it's linear, rotary, or a combination, and delve into the nuances of specifying velocity and acceleration profiles. This precision is akin to an artist carefully crafting each stroke on a canvas – it defines the essence of the final masterpiece.
Advanced users often leverage mathematical functions and equations to precisely control motion profiles. This approach provides a level of sophistication that goes beyond basic simulations, allowing for a more accurate representation of the dynamic forces at play in your designs. Consider incorporating trigonometric functions or custom equations to capture complex motion patterns that generic profiles might overlook.
Moreover, SolidWorks offers features such as parametric studies and optimization tools, empowering users to iteratively refine motion profiles. This iterative approach enables you to explore a range of scenarios, fine-tuning parameters until the simulation aligns seamlessly with your design expectations.
Utilizing Sensors for Data-driven Motion Analysis
Sensors stand as indispensable tools in SolidWorks Motion Analysis, acting as the bridge between virtual simulations and real-world data. These devices play a crucial role in capturing and interpreting essential information, enabling engineers to make informed design decisions. Understanding how to effectively utilize sensors within SolidWorks Motion Analysis opens up a realm of possibilities for students seeking a deeper understanding of dynamic behavior in their designs.
Incorporating sensors into your simulations provides a wealth of data, ranging from velocity and acceleration to contact forces and beyond. By strategically placing sensors within your assembly, you can gather precise measurements at critical points, offering a comprehensive view of the entire system's behavior. This data-driven approach empowers engineers to validate their designs against real-world scenarios, ensuring accuracy and reliability in their simulations.
Furthermore, SolidWorks offers a variety of sensor types, each serving a specific purpose. Whether it's displacement sensors tracking the movement of components or force sensors measuring the impact of external forces, understanding the nuances of these sensor types enhances the depth and accuracy of your Motion Analysis.
By mastering the art of sensor utilization, students can harness the full potential of SolidWorks Motion Analysis. This data-driven approach not only refines the accuracy of simulations but also equips engineers with the insights needed to optimize designs, troubleshoot issues, and ultimately create more robust and efficient engineering solutions.
Integrating SolidWorks Motion with Other Simulation Tools
Expand your capabilities by integrating SolidWorks Motion with other simulation tools. This synergy allows for a comprehensive analysis of your designs' performance, offering valuable insights that go beyond the scope of Motion Analysis alone.
Combining SolidWorks Motion with structural analysis tools opens up new dimensions in understanding the mechanical behavior of your assemblies. By seamlessly integrating Motion Analysis with tools like SolidWorks Simulation, you can evaluate how forces and motion interact, ensuring that your designs not only move correctly but also withstand the physical stresses they may encounter in real-world scenarios. This integrated approach provides a holistic understanding of the dynamic and structural aspects of your designs, paving the way for more robust and reliable products.
Moreover, the integration with thermal analysis tools adds another layer of sophistication. By assessing how motion influences heat dissipation and thermal stress, engineers can make informed decisions about material selection and cooling strategies. This comprehensive analysis is vital in industries where temperature variations can significantly impact the performance and lifespan of a product.
Troubleshooting Common Issues in Motion Analysis
Even seasoned SolidWorks users, with their depth of experience, can encounter challenges during the Motion Analysis process. Troubleshooting these common issues is crucial to maintaining a smooth and error-free simulation process.
One frequent challenge involves inaccurate results stemming from improper constraints. Ensure that all components are correctly constrained, paying close attention to joints, mates, and contact conditions. This meticulous approach will help eliminate unexpected movements and ensure your simulation aligns with real-world expectations.
Additionally, inadequate mesh settings can lead to simulation inaccuracies. Troubleshoot this by refining your mesh, striking a balance between accuracy and computational efficiency. Adjusting mesh parameters such as size and density can significantly impact the reliability of your results.
Another common stumbling block is the misapplication of forces and loads. Verify that all external forces are accurately applied, considering direction, magnitude, and location. This careful examination can prevent misinterpretation of simulation outcomes caused by improperly defined inputs.
Furthermore, numerical instability may arise, causing simulations to diverge unexpectedly. Troubleshoot this issue by refining the time step settings and ensuring that your model's physical properties are well-defined. Adjusting solver options can also contribute to stabilizing the simulation, allowing for more reliable results.
Case Studies: Real-world Applications of Advanced Motion Analysis
Delving into real-world applications unveils the transformative impact of advanced Motion Analysis techniques on solving intricate engineering challenges. Consider a scenario where a robotics company sought to optimize the movement of a robotic arm in a manufacturing setting. By employing advanced Motion Analysis, they were able to simulate and refine the arm's motion profile, significantly reducing cycle times and enhancing overall efficiency. This not only saved valuable production time but also led to increased throughput and cost savings.
In another instance, an automotive design team faced the complex task of improving vehicle suspension for optimal ride comfort and handling. Through advanced Motion Analysis, they simulated various suspension configurations, analyzing the dynamic response under different driving conditions. The insights gained enabled the team to fine-tune the suspension design, resulting in a smoother ride and improved vehicle performance.
These case studies showcase how advanced Motion Analysis goes beyond theoretical simulations, providing tangible solutions to real-world engineering problems. Students can draw inspiration from these success stories, understanding the practical applications of the techniques they learn in academic settings. Aspiring engineers can adapt these methodologies to their own projects, leveraging the power of advanced Motion Analysis to overcome challenges and innovate in their respective fields.
Conclusion:
In conclusion, mastering SolidWorks Motion Analysis is not just a technical skill but a gateway to unlocking the full potential of engineering designs. Throughout this blog, we have explored a myriad of advanced techniques that go beyond the basics, providing students with a comprehensive toolkit for dynamic simulation and analysis.
One key takeaway is the importance of a solid foundation in the basics of SolidWorks Motion Analysis. Understanding the fundamentals is crucial before delving into more intricate techniques. From the initiation of simulations to the incorporation of external forces and optimization processes, a thorough grasp of the basics forms the cornerstone of successful motion analysis.
As we explored advanced contact and friction modeling, the significance of realistic simulations came to the forefront. Accurately simulating real-world interactions between components is not just about achieving aesthetic motion; it is about obtaining precise data that informs design decisions. This emphasis on realism extends to the fine-tuning of motion profiles, where students learn to control the minutiae of movement for a true representation of their designs' dynamic behavior.
Optimization techniques, as discussed, are essential for efficient motion analysis. Striking a balance between accuracy and computation time is an art that aspiring engineers must master. This blog has provided insights into streamlining workflows and reducing computation times without compromising the precision of results, ensuring a more efficient and productive simulation process.
The incorporation of external loads and forces, along with the utilization of sensors, further enriches the Motion Analysis experience. By delving into these advanced features, students gain a more profound understanding of how their designs respond to dynamic conditions, paving the way for data-driven insights that influence design improvements.
Integration with other simulation tools is another key aspect covered in this exploration. By combining SolidWorks Motion Analysis with structural or thermal analysis tools, students can achieve a holistic understanding of their designs' performance. This interdisciplinary approach not only enhances the depth of analysis but also mirrors real-world engineering scenarios where multiple factors influence a design's behavior.
Troubleshooting common issues is an inevitable part of the learning curve. As students encounter challenges, they are encouraged to view them as opportunities for growth. The ability to troubleshoot not only enhances technical skills but also fosters resilience, a vital trait in the ever-evolving field of engineering.
The real-world case studies presented serve as inspiration for students. Witnessing how advanced Motion Analysis techniques have been instrumental in solving complex engineering problems reinforces the practical application of these skills. These case studies exemplify the transformative impact that mastering SolidWorks Motion Analysis can have on engineering projects.