- Neglecting Proper Planning
- Inaccurate Measurements and Dimensions
- Ignoring Material Selection
- Overlooking Weldment Profiles
- Neglecting Fillet and Chamfer Considerations
- Disregarding Weldment Cut List Updates
- Forgetting to Check for Interferences
- Lack of Revision Control
- Inadequate Knowledge of Weldment Features
- Failure to Seek Guidance and Resources
- Conclusion
SolidWorks stands as a powerhouse in the realm of 3D modeling and design, and its weldment features are pivotal in constructing robust structural frameworks. Yet, amid the vast capabilities of this software, students frequently find themselves grappling with challenges and stumbling upon common mistakes when delving into SolidWorks weldments. In the journey of navigating the intricacies of this tool, it becomes imperative to address these stumbling blocks and equip students with the knowledge to sidestep them effectively. If you need help with your weldment assignment, understanding common challenges and mistakes in SolidWorks weldments is essential for mastering this feature and achieving success in your academic endeavors.
One of the primary challenges that students often face is the oversight of proper planning before embarking on a SolidWorks weldment project. In their eagerness to start modeling, many neglect the crucial step of meticulous planning. This omission can prove detrimental in the later stages of the project, leading to structural issues and design flaws. It is essential to emphasize the significance of comprehensive planning, urging students to identify components, establish connections, and define the structure before diving into the intricate world of SolidWorks weldments.
A closely related pitfall revolves around inaccurate measurements and dimensions. Precision is the cornerstone of successful 3D modeling, and any deviation from accurate measurements can cascade into misalignments and compromise the overall integrity of the design. It is imperative for students to exercise diligence in ensuring that their input values are precise, avoiding costly mistakes that may arise due to inaccuracies in dimensions.
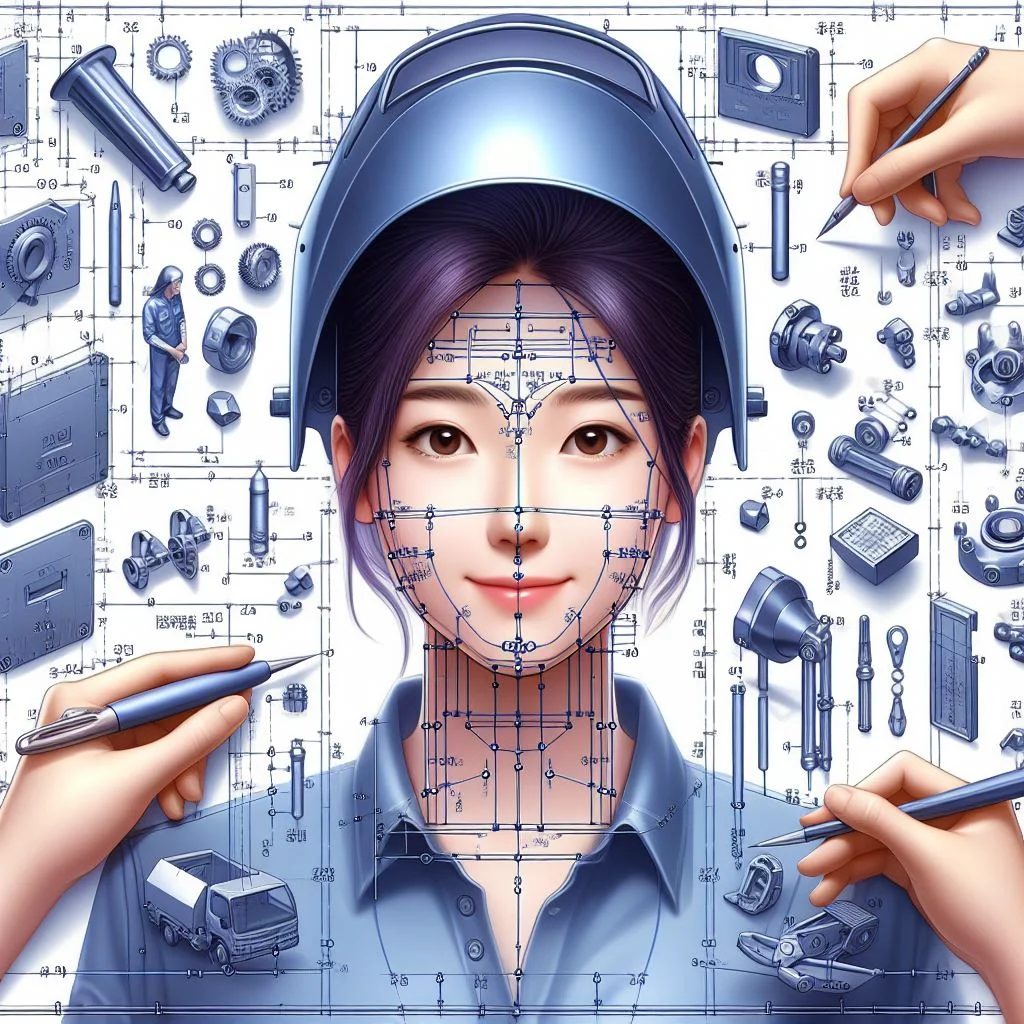
Material selection is another critical aspect that often gets overlooked. The failure to consider material properties can result in structural weaknesses, undermining the very foundation of the SolidWorks weldment. Students must be cognizant of the importance of selecting materials based on project requirements, factoring in considerations such as strength, durability, and compatibility with welding processes.
As students delve deeper into SolidWorks weldments, the significance of weldment profiles cannot be overstated. While the software provides a library of standard weldment profiles, students often overlook the efficiency and time-saving benefits these profiles offer. Familiarizing oneself with these profiles and employing them judiciously contributes to a more streamlined and uniform design. Additionally, when custom profiles are inevitable, creating them with precision and attention to detail is paramount.
Fillets and chamfers, often considered minute details, assume a critical role in weldment design. Neglecting the proper sizing of fillets and chamfers can lead to weak joints, compromising the overall stability of the structure. Students need to develop an acute awareness of these elements, ensuring that they are incorporated with the right dimensions to fortify joints and enhance the overall robustness of the design.
Another pitfall lies in the oversight of keeping the weldment cut list updated as the design evolves. Changes to the structure should be accurately reflected in the cut list to avoid confusion and errors during the fabrication stage. Regularly updating the cut list is a simple yet crucial step in maintaining accuracy throughout the design process.
Beyond the design phase, the importance of conducting interference checks cannot be overstated. Overlooking this step may result in clashes or overlaps between components, potentially compromising the functionality and safety of the structure. Incorporating interference checks into the workflow ensures a more thorough and error-free design, minimizing the risk of issues in the manufacturing and assembly stages.
A common oversight in the realm of SolidWorks weldments pertains to the lack of a systematic approach to revision control. Without a robust system in place, changes may go unnoticed, leading to errors in the final product. Utilizing SolidWorks' revision management tools becomes crucial for students to keep track of design modifications, fostering a disciplined and organized workflow.
Furthermore, a recurring mistake lies in the inadequate utilization of the diverse array of weldment features offered by SolidWorks. Each feature serves a specific purpose, yet students may find themselves underutilizing these tools. Mastery of weldment features unlocks the full potential of SolidWorks, allowing students to create more sophisticated and efficient designs. Investing time in understanding these features is a worthwhile endeavor for any aspiring CAD designer.
In the face of challenges, students should embrace a proactive approach and seek guidance from available resources. Online forums, tutorials, and expert advice can provide invaluable insights and solutions to common issues encountered in SolidWorks weldments. Cultivating a learning mindset and leveraging these resources contribute significantly to the development of proficiency in 3D modeling and design.
In conclusion, while SolidWorks remains an invaluable tool for 3D modeling and design, students must navigate through potential pitfalls in weldment projects. By addressing the common mistakes discussed and adopting a disciplined and informed approach, students can elevate their skills and produce more refined, error-free designs. Mastery of SolidWorks weldments is not just a technical skill; it is a journey of continuous learning and improvement, paving the way for success in the field of CAD design.
Neglecting Proper Planning
Before diving into your SolidWorks weldment project, the importance of meticulous planning cannot be overstated. Beyond just the excitement of initiating a design, taking a step back to thoroughly plan is a crucial first phase. Start by identifying all the components required for your weldment. Consider the types of connections needed and how each element will interact within the structure. Define the overall framework with precision, taking into account not only the immediate design goals but also potential future modifications.
A lack of meticulous planning can have far-reaching consequences, extending well beyond the initial stages of your project. Without a clear roadmap, you risk encountering unforeseen challenges during the design process. Inadequate planning may result in structural inconsistencies, misalignments, or even the need for significant rework. These issues can lead to frustration, project delays, and increased workloads.
To avoid these pitfalls, invest time upfront in comprehensive planning. Utilize SolidWorks to create a virtual blueprint of your weldment, carefully considering each element's placement and relationship within the overall structure. This proactive approach will pay off in the long run, contributing to a smoother design process and a final product that meets both your expectations and industry standards. Remember, in the realm of SolidWorks weldments, a well-thought-out plan is the foundation for success.
Inaccurate Measurements and Dimensions
Precision is paramount in the realm of 3D modeling, particularly when dealing with SolidWorks weldments. The accuracy of your measurements and dimensions significantly influences the success of your entire design. Even minor discrepancies in these foundational elements can lead to misalignments and structural issues that may compromise the integrity of the final product. To safeguard against such pitfalls, it is imperative to diligently ensure that your measurements are exact and your dimensions are spot-on.
Taking the extra step to double-check your input values can be a game-changer in preventing costly mistakes down the line. This meticulous approach not only minimizes the chances of errors but also contributes to a smoother design process. Moreover, it instills confidence in the precision of your work, a quality that is indispensable in the field of engineering and design.
In the dynamic landscape of SolidWorks weldments, where precision is synonymous with quality, practitioners must embrace a mindset that values accuracy in every aspect of their work. This commitment to precision will not only elevate the overall quality of designs but also cultivate a skill set that is highly sought after in the competitive world of 3D modeling and engineering.
Ignoring Material Selection
Selecting the right materials is an integral aspect of SolidWorks weldment design, and it goes beyond mere aesthetic considerations. The choice of materials directly impacts the structural integrity, durability, and overall performance of your design. Failure to meticulously consider material properties can result in significant consequences, including structural weaknesses and compromised integrity.
When embarking on a SolidWorks weldment project, it is imperative to conduct thorough research to understand the unique properties of various materials. Different projects may demand specific characteristics such as tensile strength, hardness, or corrosion resistance. A critical consideration is also the environmental conditions to which the final product will be exposed. Whether it's a load-bearing structure subject to heavy forces or a component facing extreme temperatures, the selected materials must align with the project's requirements.
Incorporating the wrong materials or neglecting to account for their properties can lead to premature wear and tear, reduced load-bearing capacity, and even catastrophic failure. To avoid such pitfalls, make informed decisions based on a comprehensive understanding of material science and its application in SolidWorks weldments. Your design's success hinges on the meticulous selection of materials that not only meet aesthetic preferences but also align with the functional demands of the project.
Overlooking Weldment Profiles
SolidWorks simplifies the design process by offering a comprehensive library of standard weldment profiles. However, it's not uncommon for students to underestimate the significance of these pre-defined profiles. These standard profiles serve as a valuable resource, streamlining the design workflow and contributing to the overall efficiency of the project. By utilizing these profiles, students can save considerable time that would otherwise be spent on creating custom shapes from scratch.
Familiarizing yourself with the available weldment profiles is a fundamental step in leveraging SolidWorks effectively. These profiles cover a wide range of structural shapes and sizes, from simple beams to complex sections. They are designed to meet industry standards, ensuring that your structures adhere to recognized specifications. Neglecting these standard profiles not only leads to a loss of efficiency but also increases the likelihood of errors in the design process.
Moreover, while standard profiles are convenient, there will be instances where custom shapes are necessary to meet specific project requirements. In such cases, it's imperative to approach the creation of custom profiles with precision and meticulous attention to detail. Accurate dimensions and proper geometric considerations are essential to avoid discrepancies in the final design. By striking a balance between utilizing standard profiles and creating custom ones when needed, students can achieve a harmonious blend of efficiency and customization in their SolidWorks weldment projects.
Neglecting Fillet and Chamfer Considerations
Fillets and chamfers play a critical role in weldment design, contributing significantly to the overall strength and stability of the structure. Neglecting these elements can lead to weakened joints and compromise the integrity of the entire design. It's crucial to understand that fillets and chamfers are not mere aesthetic details but serve a functional purpose in distributing stress and preventing stress concentrations.
When fillet and chamfer considerations are overlooked, joints may become vulnerable to excessive loads, increasing the risk of failure. Proper sizing and placement of fillets and chamfers distribute stress more evenly throughout the weldment, preventing stress concentrations that could lead to fractures or deformations. Engineers and students alike should recognize the importance of these features in enhancing the durability and reliability of their designs.
Additionally, inadequate fillet and chamfer dimensions can impact the manufacturability of the structure. Welding processes may face challenges with improper joint configurations, leading to difficulties in fabrication and compromising the overall quality of the weldment. Therefore, meticulous attention to fillet and chamfer details is not only vital for design robustness but also for facilitating a smooth manufacturing process. By being mindful of these crucial elements, designers can ensure a well-executed and structurally sound weldment that meets both design and manufacturing requirements.
Disregarding Weldment Cut List Updates
As your SolidWorks weldment project progresses, maintaining an up-to-date cut list becomes increasingly crucial. A regularly updated cut list serves as a comprehensive inventory of components, their specifications, and any modifications made during the design process. Neglecting this critical step can result in confusion and errors during fabrication.
An outdated cut list may lead to discrepancies between the digital model and the physical structure being manufactured. This misalignment can cause delays, additional costs, and compromise the overall quality of the final product. Fabricators rely on accurate cut lists to precisely cut and assemble components, ensuring the integrity of the weldment.
Furthermore, an updated cut list is invaluable for project documentation and communication. When collaborating with team members or external partners, having a synchronized cut list enhances clarity and reduces the likelihood of misunderstandings. It acts as a reliable reference point, facilitating efficient communication throughout the fabrication process.
In essence, keeping your cut list current is not just a procedural formality; it is a strategic practice that directly impacts the success of your SolidWorks weldment project. By prioritizing the regular updating of the cut list, you not only streamline the manufacturing process but also contribute to the overall accuracy, efficiency, and success of your design endeavors.
Forgetting to Check for Interferences
Interferences within a SolidWorks weldment design can have significant consequences, underscoring the importance of thorough interference checks. These checks go beyond merely identifying clashes or overlaps between components; they serve as a critical safeguard for both the functionality and safety of the entire structure.
When interferences are overlooked, the consequences can be far-reaching. Misaligned or overlapping components can compromise the structural integrity of the weldment, leading to potential failure during real-world applications. Moreover, such oversights may result in manufacturing challenges, causing delays and increased costs.
To ensure the robustness of your SolidWorks weldment, make interference checks a routine part of your design process. This involves scrutinizing the entire assembly for any areas where components intersect or interfere with one another. SolidWorks provides tools and features to streamline this process, allowing designers to visualize and rectify interferences effectively.
Additionally, these checks become particularly crucial when modifications or updates are made to the weldment design. As the project evolves, revisiting interference checks helps maintain the accuracy of the model, preventing any unintended consequences stemming from alterations made during the design process.
In conclusion, vigilance in performing interference checks is paramount for any SolidWorks weldment project. By prioritizing this step, designers can mitigate risks, ensure structural soundness, and contribute to the overall success of the fabrication and implementation phases.
Lack of Revision Control
Maintaining a systematic approach to revisions is paramount in any design project, and the consequences of neglecting proper revision control cannot be overstated. When changes go unnoticed, the risk of introducing errors into the final product significantly increases. This lack of oversight can have far-reaching implications, not only compromising the structural integrity of the design but also potentially causing delays in the manufacturing process.
To mitigate these risks, students should actively utilize SolidWorks' robust revision management tools. These tools provide a structured framework for tracking and documenting design modifications throughout the entire project lifecycle. By assigning clear revision labels and dates, designers can easily trace the evolution of their SolidWorks weldment, ensuring that every change is recorded and accounted for.
Effective revision control serves as a safeguard against versioning issues and helps maintain consistency in collaboration. When multiple team members are involved in a project, the risk of confusion and miscommunication is inherent. SolidWorks' revision management tools offer a centralized platform for teams to coordinate changes, reducing the likelihood of discrepancies and ensuring that everyone is working with the most up-to-date information.
Inadequate Knowledge of Weldment Features
SolidWorks provides a diverse array of weldment features, each tailored to serve specific purposes in 3D modeling and design. Unfortunately, students frequently underutilize these valuable features, unknowingly limiting the capabilities of their SolidWorks projects. It is crucial for aspiring designers to invest time in comprehending and mastering the various weldment tools available.
Understanding weldment features allows for the creation of more intricate and sophisticated designs. For instance, SolidWorks offers a comprehensive library of standard weldment profiles that can significantly expedite the design process and ensure uniformity. Moreover, the software enables the creation of custom profiles, empowering designers to address unique project requirements with precision.
Beyond profiles, SolidWorks weldment tools encompass a range of capabilities, including structural member design, frame generation, and the incorporation of weld beads. Familiarizing oneself with these features not only enhances design efficiency but also opens up possibilities for more innovative and structurally sound creations.
To unlock the full potential of SolidWorks, students should explore the intricacies of weldment features through tutorials, practice, and hands-on projects. By doing so, they can transform their designs, making them not just visually appealing but also robust and functional. Embracing the depth of SolidWorks weldment features is a crucial step towards becoming a proficient and versatile CAD designer.
Failure to Seek Guidance and Resources
When faced with challenges in SolidWorks weldment design, reaching out for guidance and utilizing available resources is a pivotal step in overcoming obstacles and refining your skills. The realm of 3D modeling and design is dynamic, and the learning process is continuous. Hence, students should adopt a proactive approach by tapping into various channels for support and insights.
One valuable resource for SolidWorks enthusiasts is online forums. These platforms serve as virtual communities where individuals share their experiences, ask questions, and offer solutions. Engaging in these forums allows students to connect with a broader community of users, including seasoned professionals and peers who may have encountered similar challenges. The exchange of ideas and troubleshooting tips can be immensely beneficial in navigating through complexities in weldment design.
In addition to online forums, tutorials are another indispensable tool for expanding one's knowledge base. SolidWorks provides a plethora of official tutorials covering various aspects of the software, including weldments. These tutorials offer step-by-step guidance, practical demonstrations, and hands-on exercises. Following these tutorials not only enhances your understanding of SolidWorks weldments but also provides a structured learning path to follow at your own pace.
Expert advice is a gem in the learning process. Seeking guidance from professionals who have extensive experience in SolidWorks and weldment design can offer personalized insights and solutions tailored to specific challenges. Many seasoned designers are willing to share their knowledge and mentor aspiring individuals. Connecting with experts through networking events, online platforms, or even reaching out directly can open doors to invaluable guidance that accelerates your learning curve.
Moreover, staying updated with the latest developments in SolidWorks and CAD design is essential. Regularly checking for software updates, attending webinars, and participating in industry events can keep you informed about new features, tools, and best practices. SolidWorks often introduces enhancements to its weldment capabilities, and staying abreast of these changes ensures that you are leveraging the full potential of the software in your designs.
It's crucial to recognize that learning is an ongoing process, and a proactive mindset is key to success. Embrace challenges as opportunities to grow and refine your skills. Experiment with different design approaches, and don't be afraid to make mistakes – they are an integral part of the learning journey.
Additionally, consider forming study groups or collaborative projects with fellow students. Collective brainstorming and problem-solving can offer fresh perspectives and creative solutions. Engaging in collaborative efforts not only enhances your understanding of SolidWorks weldments but also fosters a supportive learning environment.
Conclusion
In conclusion, mastering SolidWorks weldments is a journey that demands attention to detail, dedication, and a commitment to continuous learning. By addressing the common pitfalls discussed in this blog, students can significantly enhance their proficiency in using SolidWorks for weldment design projects.
As you navigate the intricacies of SolidWorks weldments, remember the importance of careful planning. Taking the time to plan your project thoroughly can prevent many errors down the line. Accurate measurements and dimensions are the backbone of any successful 3D modeling endeavor, so ensure you double-check your inputs to maintain precision in your designs.
The significance of material selection cannot be overstated. It directly influences the structural integrity of your weldment, so choose materials based on the specific requirements of your project. Additionally, familiarize yourself with the standard weldment profiles provided by SolidWorks, as they can significantly streamline your design process and ensure consistency.
Fillets and chamfers, often overlooked, play a critical role in weldment design. Properly sized fillets and chamfers are essential for creating robust joints and maintaining the overall stability of your structure. Likewise, keeping your weldment cut list updated throughout the design process is vital for accurate fabrication and assembly.
Performing interference checks regularly cannot be emphasized enough. Identifying and resolving interferences early in the design phase prevents costly errors during manufacturing. Moreover, establishing a solid revision control system is essential for managing changes effectively and avoiding confusion in the later stages of your project.
Understanding and fully utilizing SolidWorks' array of weldment features is key to unlocking the software's potential. Each feature serves a specific purpose, and having a comprehensive understanding of them allows for more efficient and creative design solutions. Invest time in learning about weldment tools, and experiment with different features to broaden your skill set.
While striving for proficiency, it's crucial not to forget the importance of seeking guidance and utilizing available resources. Online forums, tutorials, and expert advice can provide valuable insights and solutions to challenges you may encounter. Embrace a proactive approach to learning and leverage the collective knowledge of the SolidWorks community.
Expanding on the conclusion, remember that becoming an adept SolidWorks user is an ongoing process. It's not just about avoiding mistakes but also about continuously refining your skills. Stay curious, explore advanced features, and challenge yourself with complex projects to push your capabilities further.
In your journey to master SolidWorks weldments, don't underestimate the power of hands-on experience. Practice, experimentation, and perseverance are fundamental aspects of the learning process. Each project, regardless of its size, contributes to your growth as a proficient CAD designer.
In essence, this blog has aimed to shed light on the common pitfalls in SolidWorks weldments and provide practical guidance for avoiding them. By embracing a comprehensive approach to design, being attentive to details, and remaining open to continuous improvement, students can navigate their SolidWorks weldment projects with confidence and precision. Happy designing!