- Understanding the Basics of SolidWorks
- 1. Familiarizing Yourself with the SolidWorks Interface
- 2. Exploring the Essential Tools and Features
- Converting 2D Sketches into 3D Models
- 1. Creating a Base Sketch
- 2. Utilizing Extrusion and Revolve Features
- 3. Incorporating Sweeps and Lofts for Complex Designs
- Applying Constraints and Dimensions for Accurate Models
- 1. Defining Geometric Constraints
- 2. Adding Dimensions to Ensure Precision and Repeatability
- Refining Your 3D Models for Realistic Representation
- 1. Adding Fillets and Chamfers for Smooth Edges
- 2. Applying Material and Texture
- Validating and Documenting Your 3D Designs
- 1. Performing Analysis and Simulation Tests
- 2. Creating Technical Drawings and Documentation
- Conclusion
SolidWorks is a robust CAD program used extensively across many fields for the creation of high-quality 3D models. Students need to be proficient in translating 2D ideas into precise and believable 3D designs as part of their SolidWorks homework. The purpose of this blog is to help you do well on your SolidWorks assignments by discussing the steps involved in moving ideas from the 2D to the 3D world.
Understanding the Basics of SolidWorks
If you want to be productive with SolidWorks, you need to know the program's fundamentals. The best way to get around in SolidWorks is to know your way around the menus, toolbars, and windows. Converting ideas from 2D to 3D is facilitated by becoming familiar with the fundamental features and tools in SolidWorks, such as sketching, creating basic shapes, and working with assemblies. Once you've mastered the fundamentals, you'll be able to make the most of SolidWorks' features and increase your output on projects.
1. Familiarizing Yourself with the SolidWorks Interface
Learning the ins and outs of SolidWorks' user interface is a must for new users. You can access the various menus, toolbars, and windows that make up the interface in order to use its many functions and features. Learn your way around the SolidWorks interface so you can complete your assignments successfully. The Command Manager, FeatureManager Design Tree, PropertyManager, and Task Pane are all important parts of the design process, so take the time to learn how to use them.
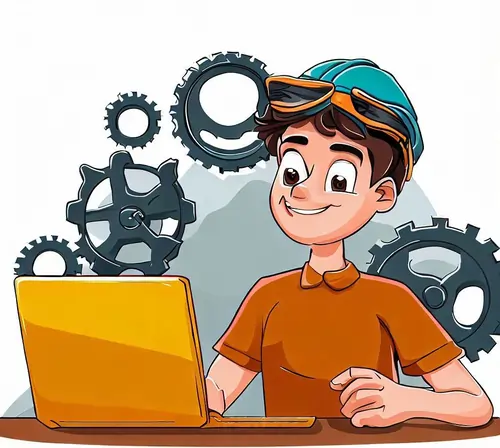
2. Exploring the Essential Tools and Features
You can make complex 3D models with the help of SolidWorks' many features and tools. Understanding and making good use of the necessary tools is crucial for making the transition from 2D to 3D. As a first step, familiarize yourself with SolidWorks' sketching tools, which allow you to quickly and easily create 2D shapes out of lines, arcs, and other geometry. Get some experience with the Line, Circle, and Rectangle tools by sketching various shapes.
You can use tools like Extrude, Revolve, and Cut-Extrude to turn your 2D sketches into 3D models once you have your design in mind. You can use the Extrude tool to push or pull your sketch in the third dimension to add or remove volume, and the Revolve tool to create rotational symmetry by rotating your sketch around an axis. These elements are crucial for developing functional 3D models from your 2D designs.
Converting 2D Sketches into 3D Models
Creating a 3D model from a 2D sketch is a fundamental operation in SolidWorks. Making a detailed sketch of your design is the first step in developing the 3D model. By utilizing tools like extrude and revolve, you can add depth and movement to your sketches in the third dimension. Intricate shapes and transitions can be made with the help of sweeps and lofts, which are best used in more complex designs. Learning to translate 2D sketches into 3D models is a key skill that will allow you to fully realize your design potential.
1. Creating a Base Sketch
Developing a preliminary sketch is the first step in developing a final 3D model from your 2D ideas. The building blocks of your 3D model start with a simple sketch. Make sure the dimensions and proportions of your design are correct in the initial sketch you create. Create the lines, arcs, circles, and other shapes integral to your design using the provided sketching tools.
Geometric constraints must be applied to sketch entities in order to preserve the intended connections between them. Sketch elements' locations and behaviors can be specified with the aid of constraints. In SolidWorks homework help, you can choose from several different kinds of constraints, including coincident, parallel, perpendicular, and concentric, to name a few. If you use constraints, your sketch won't break if you change some of the design's parameters.
2. Utilizing Extrusion and Revolve Features
Developing a three-dimensional model begins with a rough sketch. Extrude and Revolve are just two of the robust tools available in SolidWorks for turning 2D sketches into finished 3D models.
Using the Extrude tool, you can make a solid object by extending or slicing your sketch along the normal direction. The height and depth of your 3D model can be adjusted by adjusting the extrusion distance and direction. Using this function, you can easily make cubes, cylinders, and rectangular blocks, all of which are prismatic shapes.
Similarly, the Revolve function spins your sketch's profile around an arbitrary axis, producing mirror images. Shapes like spheres, cones, and more can be generated by adjusting the angle of rotation and defining the axis of revolution.
3. Incorporating Sweeps and Lofts for Complex Designs
In addition to standard 3D modelings operations like extrusion and revolution, SolidWorks also includes more sophisticated tools like sweeps and lofts.
Using a 2D sketch and a path or guide curve, you can make any shape you like with the Sweep tool. It is possible to create complex designs with a variety of cross-sections by utilizing multiple sketch profiles and path options.
Using the Loft tool, you can make seamless transitions between several 2D profiles. SolidWorks allows users to create intricate organic shapes by defining a series of cross-sectional profiles and guide curves.
With these sophisticated tools at your disposal, you can easily transform complex 2D ideas into visually compelling 3D models.
Applying Constraints and Dimensions for Accurate Models
The accuracy and precision of your SolidWorks 3D models rely heavily on the application of constraints and dimensions. Geometric constraints ensure that entities in a sketch continue to behave as intended when combined. Including dimensions gives your models a solid structure by which you can define lengths, widths, and heights. Modifications and design changes are made easier with these constraints and dimensions in place. You can make sure your 3D models are accurate by learning how to properly apply constraints and dimensions.
1. Defining Geometric Constraints
The geometric relationships between sketch entities must be preserved with great care when translating 2D ideas into 3D models. SolidWorks provides a number of geometric constraints that can be used to accomplish this.
Sketch entities' dimensions, locations, and rotations can all be managed with the help of geometric constraints. The coincident constraint guarantees that two points or entities are in the same place, and the parallel constraint makes sure that two lines or edges are always the same distance apart. If you use these restrictions wisely, you can make flexible 3D models that look and behave just like your 2D sketch.
2. Adding Dimensions to Ensure Precision and Repeatability
Add dimensions that define specific sizes and measurements to your 3D models to ensure their accuracy and repeatability. You can specify lengths, angles, and other important parameters with the help of SolidWorks' extensive set of dimensioning tools.
The addition of dimensions provides a firm foundation for your plan. Dimensions allow you to regulate the overall size, particular features, and connections between various parts. Not only do these measurements guarantee precision, but they also make improvements and alterations to the design much simpler down the road. Smart dimensioning tools can automatically detect geometric relationships and suggest appropriate dimensions, which is why they should be considered when adding dimensions. Workflow acceleration and error prevention are both greatly improved by this function.
Refining Your 3D Models for Realistic Representation
Improving the detail of your SolidWorks 3D models is crucial for producing an accurate rendering of your designs. Smoothing out your models' sharp edges and transitions with fillets and chamfers improves their visual appeal and usability. By simulating their physical properties and adding visual depth, materials, and textures bring your models to life. You can make designs that are both aesthetically pleasing and faithful representations of the real world if you focus on these aspects. Improving the quality of your designs and increasing their overall impact is possible through the use of refined 3D models.
1. Adding Fillets and Chamfers for Smooth Edges
By rounding off corners and transitions with fillets and chamfers, you can improve the look and usability of your 3D models. Both fillets and chamfers are used to soften sharp corners.
You can make your design more attractive and easier to manufacture and use by adding chamfers and fillets. Your 3D models will last longer and be easier to assemble thanks to these design choices that reduce the likelihood of stress concentrations.
Fillets and chamfers can be easily added to your models with the help of SolidWorks' convenient tools. The level of smoothness and aesthetic appeal can be adjusted by adjusting the size, position, and type of fillet or chamfer.
2. Applying Material and Texture
Using a variety of materials and textures, your 3D models can take on a more lifelike appearance. Metals, plastics, and composites are just some of the many available pre-defined materials in SolidWorks' extensive library. The material's properties can be altered to meet the user's precise needs.
Assigning materials to various parts or surfaces allows you to see how they react to light and other factors in a virtual environment. As a result, you can check the form and function of your design before actually making it.
In addition, you can improve the realism of your models by giving them matte, glossy, or textured finishes in SolidWorks. Including textures in your design is a great way to give it depth and appeal to more people.
Validating and Documenting Your 3D Designs
It is essential to validate and document your 3D designs before proceeding with manufacturing or assembly. You can ensure the functionality and durability of your designs by conducting analysis and simulation tests with the help of SolidWorks' tools. Making technical drawings and documentation gives you a clear and detailed representation of your models, complete with measurements, comments, and instructions for building. When your 3D designs have been verified and documented, you will have the assurance to share your ideas and develop working prototypes.
1. Performing Analysis and Simulation Tests
The performance and behavior of your 3D designs should be verified with the help of analysis and simulation tools in SolidWorks before you commit to a final version. Strength, motion, fluid flow, and thermal behavior are just some of the things that can be examined with these devices.
By putting your models through these checks, you can find and fix any performance or structural issues before they go into production. In terms of analysis and simulation, SolidWorks offers a wide variety of tools, such as Finite Element Analysis (FEA), Computational Fluid Dynamics (CFD), and Motion Analysis.
You can make better choices, fine-tune your models, and make sure they meet the required performance criteria by analyzing and simulating your 3D designs.
2. Creating Technical Drawings and Documentation
Creating precise technical drawings and documentation is crucial for effectively communicating your design and easing manufacturing or assembly. SolidWorks includes everything you need to make 2D drawings complete with dimensions, annotations, and other information.
Your 3D models can be accurately depicted in technical drawings with the help of detailed views, section cuts, and assembly drawings. The manufacturing procedures, assembly guidelines, and quality assurance all make use of these drawings.
With SolidWorks, you can easily create supporting documentation for your designs, like a bill of materials (BOM), exploded views, and more. Your 3D models will be successfully translated into physical objects with the help of the information provided in these documents, which is essential for production, procurement, and assembly.
You can guarantee the success of your 3D designs in the real world by producing thorough technical drawings and documentation.
It takes time and effort to become proficient in SolidWorks' process of transforming 2D ideas into 3D models. You can succeed in your SolidWorks classes and acquire valuable skills for a future career in engineering and design if you follow the steps outlined, make use of the necessary tools and features, apply constraints and dimensions accurately, and refine your models for realistic representation.
Conclusion
SolidWorks assignments often require translating ideas from two dimensions to three. If you follow the instructions and learn the techniques, you can make 3D models that look and function like the real thing. For a polished final product, it's important to focus on the little things, like making sure your constraints and dimensions are accurate. You can succeed in your SolidWorks classes and acquire the skills necessary for a prosperous professional life in the engineering and design fields with hard work and perseverance.
Please don't hesitate to contact us at SolidWorksAssignmentHelp.com if you ever find yourself in need of further assistance with your SolidWorks homework. As you work to improve your SolidWorks skills, we're here to help. Have fun creating!