- Understanding Surface Modeling Basics
- Leveraging Advanced Surfacing Tools
- Mastering Curvature Continuity
- Exploring Advanced Lofting Techniques
- Optimizing Surface Geometry
- Incorporating Organic Shapes
- Conclusion
SolidWorks is indeed a versatile platform renowned for its prowess in 3D modeling and design. Its popularity spans various industries owing to its efficiency and robust features. However, it's in surfacing where SolidWorks truly excels, empowering designers to craft intricate and visually appealing shapes effortlessly. In the following discussion, we'll explore a range of advanced techniques tailored specifically for SolidWorks surfacing assignments, offering insights and practical tips to enhance your proficiency in this critical aspect of 3D modeling. Mastering these advanced techniques will be essential for achieving optimal results in SolidWorks.
Understanding the fundamentals of surface modeling is paramount before delving into more advanced techniques. Surface modeling involves the creation of complex shapes by defining surfaces rather than solid volumes. Mastery of concepts like splines, curves, and boundary surfaces lays a solid foundation for tackling more intricate surfacing challenges.
SolidWorks offers an array of advanced surfacing tools that significantly augment designers' capabilities. Techniques such as lofting, sweeping, and boundary surface creation provide unparalleled flexibility and control over surface geometry. Familiarizing yourself with these tools unlocks a world of possibilities, enabling you to realize your design vision with precision and efficiency.
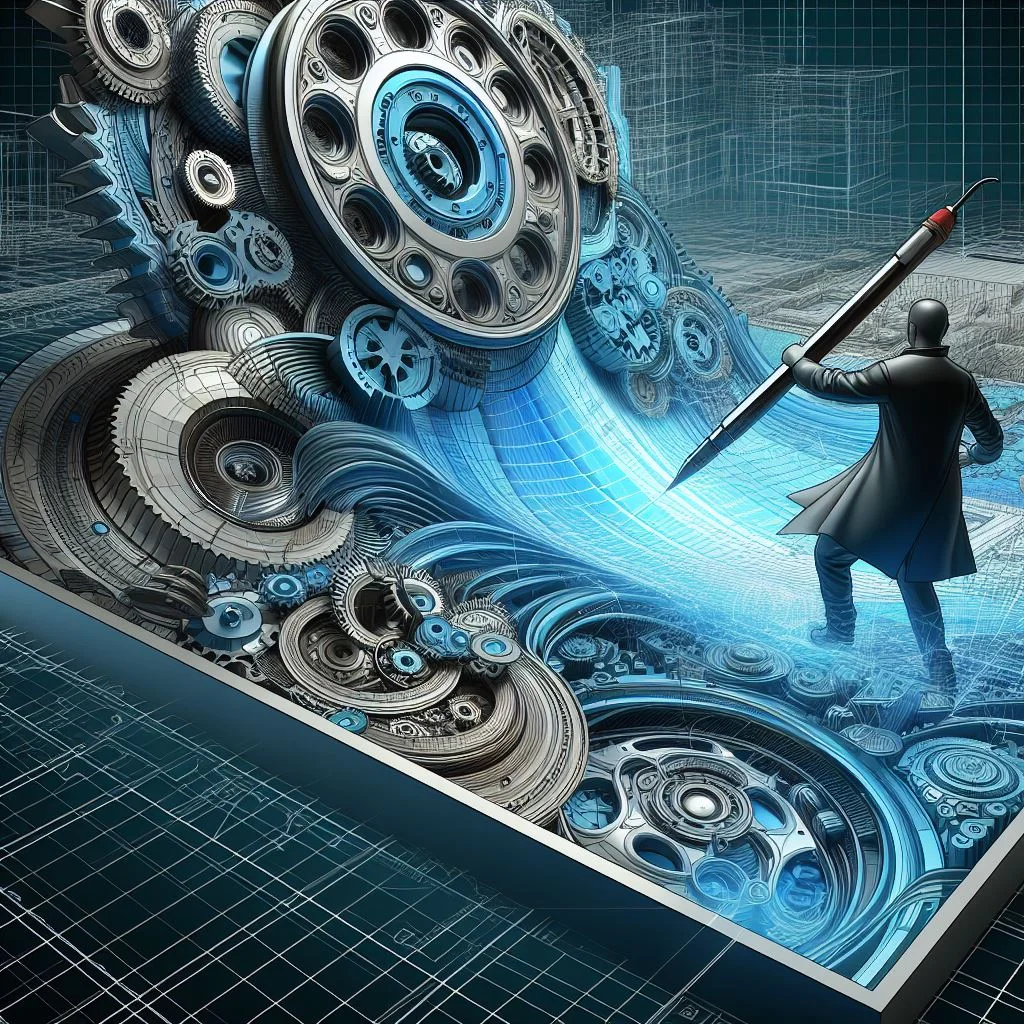
Curvature continuity, often referred to as "G2 continuity," is a critical aspect of surfacing that directly impacts the visual quality and manufacturability of designs. SolidWorks provides robust tools for analyzing and controlling curvature continuity, ensuring that surfaces seamlessly blend into one another, resulting in smooth transitions and professional-grade aesthetics. Mastery of curvature continuity is indispensable for achieving flawless surfaces in your designs.
Advanced lofting techniques offer a sophisticated approach to creating complex shapes by defining a series of cross-sections and guiding curves. In challenging surfacing assignments, traditional lofting methods may prove inadequate. SolidWorks addresses this limitation by offering advanced lofting options such as guide curves and curvature control, empowering designers to tackle even the most intricate design requirements with confidence and precision.
Optimizing surface geometry is crucial for ensuring the manufacturability and structural integrity of final designs. SolidWorks equips designers with powerful tools for analyzing and optimizing surface geometry, allowing for the identification and resolution of potential issues such as surface irregularities or sharp transitions. By optimizing surface geometry, designers can create designs that not only look visually appealing but also function flawlessly in real-world applications.
Organic shapes, inspired by nature or biological forms, are increasingly prevalent in modern design projects. SolidWorks excels in creating organic shapes through techniques such as freeform modeling and surface sculpting. By incorporating these advanced techniques into surfacing assignments, designers can unleash their creativity and produce captivating designs that push the boundaries of traditional CAD modeling.
Understanding Surface Modeling Basics
Before delving into advanced techniques, establishing a solid understanding of surface modeling fundamentals in SolidWorks is paramount. Surface modeling diverges from conventional solid modeling by focusing on the creation and manipulation of surfaces rather than solid volumes. This distinction is critical as it underpins the entire process of crafting intricate designs with finesse and precision.
Central to grasping surface modeling basics are key concepts such as splines, curves, and boundary surfaces. Splines serve as fundamental building blocks, allowing designers to define smooth and flowing shapes that form the basis of complex surface geometries. Mastery of spline manipulation enables designers to sculpt surfaces with unparalleled flexibility, ensuring that every contour and curve aligns seamlessly with the intended design vision.
Moreover, understanding curves in SolidWorks is essential for controlling the trajectory and shape of surfaces. By leveraging curve tools, designers can precisely define the path along which surfaces will be created, facilitating the creation of intricate and precise designs. Whether utilizing sketches, reference geometry, or imported curves, the ability to manipulate curves empowers designers to craft surfaces with unparalleled accuracy and control.
Furthermore, boundary surfaces play a pivotal role in surface modeling, serving as the framework upon which complex shapes are built. By defining boundary surfaces between specified curves or edges, designers can seamlessly blend disparate elements into cohesive and harmonious designs. Mastery of boundary surface creation is foundational, as it enables designers to bridge the gap between concept and reality, bringing their design visions to life with precision and clarity.
Leveraging Advanced Surfacing Tools
SolidWorks provides a comprehensive set of advanced surfacing tools that empower designers to navigate intricate design landscapes with confidence and finesse. Among these tools, lofting, sweeping, and boundary surface creation stand out as pillars of versatility and control. Lofting, for instance, facilitates the creation of complex shapes by interpolating between two or more profiles along a specified path. By defining cross-sections and guide curves, designers can seamlessly blend surfaces to achieve organic and intricate shapes that meet exacting design requirements.
Similarly, sweeping in SolidWorks enables designers to extrude a profile along a defined path, offering unparalleled flexibility in shaping intricate geometries. Whether it's creating sweeping curves or intricate contours, this tool allows for precise control over surface geometry, empowering designers to bring their visions to life with unparalleled accuracy.
Boundary surface creation is another invaluable tool in the SolidWorks arsenal, offering a streamlined approach to creating complex surfaces by defining boundary conditions between multiple curves or surfaces. This technique is particularly useful for achieving smooth transitions and complex surface blends, essential for projects requiring high aesthetic standards and functional integrity.
Mastering these advanced surfacing tools in SolidWorks opens up a world of possibilities for designers, enabling them to tackle even the most challenging design tasks with confidence and efficiency. Whether it's sculpting organic forms, modeling intricate mechanical components, or crafting aesthetically pleasing consumer products, SolidWorks provides the tools and capabilities needed to turn imagination into reality.
By investing time in mastering these advanced techniques, designers can unlock new levels of creativity and innovation, pushing the boundaries of what's possible in 3D modeling and design. With SolidWorks as their trusted companion, designers can navigate the complexities of surfacing assignments with ease, bringing their ideas to fruition with precision and flair.
Mastering Curvature Continuity
Curvature continuity, also known as "G2 continuity," plays a pivotal role in achieving flawless transitions between surfaces, contributing to the overall quality and aesthetic appeal of the design. In SolidWorks, designers have access to a suite of tools specifically designed for analyzing and controlling curvature continuity. By mastering these tools, designers can ensure that their surfaces blend seamlessly, resulting in professional-grade outcomes for their surfacing assignments.
Achieving curvature continuity involves more than just ensuring smooth transitions between adjacent surfaces; it requires meticulous attention to detail and a thorough understanding of surface geometry. SolidWorks offers various methods for assessing curvature continuity, including curvature combs and curvature analysis tools. These tools enable designers to identify areas where curvature continuity may be lacking and make necessary adjustments to achieve the desired result.
One effective technique for achieving curvature continuity in SolidWorks is through the use of guide curves. Guide curves allow designers to control the shape of the resulting surface, ensuring that it conforms precisely to the desired curvature. By strategically placing guide curves and adjusting their parameters, designers can achieve precise control over the curvature of their surfaces, resulting in smooth transitions and a high-quality aesthetic.
In addition to guide curves, SolidWorks offers tools for controlling curvature continuity directly, such as the "Match curvature" option in surface creation features. This feature allows designers to specify the desired curvature continuity between adjacent surfaces, ensuring that they blend seamlessly without any visible discontinuities. By utilizing these advanced tools effectively, designers can achieve professional-level results in their surfacing assignments, meeting the highest standards of quality and aesthetic appeal.
Mastering curvature continuity in SolidWorks is essential for designers looking to elevate their surfacing skills and produce exceptional designs. By understanding the principles of curvature continuity and utilizing the advanced tools available in SolidWorks, designers can create surfaces that not only meet functional requirements but also exhibit a level of craftsmanship and refinement that sets them apart from the competition.
Exploring Advanced Lofting Techniques
Lofting serves as a versatile tool in the designer's arsenal, allowing for the creation of intricate shapes through the interpolation of cross-sections and guiding curves. However, as projects become more complex, traditional lofting techniques may prove inadequate in capturing the desired form accurately. SolidWorks acknowledges this challenge and provides advanced lofting options that empower designers to overcome these limitations effectively.
One such feature is the incorporation of guide curves, which offer greater control over the shape of the lofted surface. By strategically placing guide curves, designers can influence the trajectory of the lofting process, ensuring that the resulting surface conforms precisely to their design intent. Guide curves act as additional constraints, allowing for the creation of complex shapes that would be difficult to achieve using traditional lofting methods alone.
Furthermore, SolidWorks offers curvature control options within the lofting toolset, enabling designers to maintain smooth and continuous transitions between lofted sections. Curvature continuity is critical for achieving aesthetically pleasing surfaces, particularly in designs where seamless blending is essential. With curvature control, designers can adjust the curvature magnitude and direction at key points along the lofted surface, ensuring that transitions remain visually appealing and structurally sound.
These advanced lofting techniques empower designers to tackle even the most challenging design requirements with confidence. Whether creating organic forms, streamlined aerodynamic shapes, or intricate architectural details, SolidWorks provides the necessary tools to realize their vision effectively. By mastering these advanced techniques, designers can push the boundaries of what's possible in surfacing assignments, delivering exceptional results that inspire and innovate.
Optimizing Surface Geometry
Optimizing surface geometry is not just about achieving a visually appealing design; it's about ensuring that the final product is feasible for manufacturing and possesses the structural integrity necessary for its intended use. SolidWorks offers a suite of tools specifically designed to analyze and refine surface geometry, enabling designers to identify and rectify any potential issues that may compromise the quality of the design.
Surface irregularities and sharp transitions are common pitfalls in surface modeling that can lead to manufacturing challenges and structural weaknesses. SolidWorks allows designers to conduct detailed analyses of surface geometry, pinpointing areas where adjustments are needed to achieve smoother transitions and eliminate irregularities. By addressing these issues early in the design process, designers can streamline the manufacturing process and reduce the likelihood of costly errors or rework down the line.
In addition to addressing surface irregularities, optimizing surface geometry also involves ensuring that the design meets specific manufacturing requirements and constraints. SolidWorks provides tools for assessing factors such as draft angles, wall thickness, and material properties, allowing designers to fine-tune the design to meet the demands of the manufacturing process. By optimizing surface geometry to align with manufacturing capabilities, designers can minimize production costs and maximize efficiency.
Furthermore, optimizing surface geometry can enhance the overall performance and functionality of the design. Smooth, well-defined surfaces are not only visually pleasing but also contribute to the structural integrity and durability of the final product. By refining surface geometry to eliminate unnecessary complexities and reinforce critical areas, designers can create designs that excel in terms of both form and function.
In conclusion, optimizing surface geometry is a crucial step in the design process that impacts the manufacturability, structural integrity, and performance of the final product. SolidWorks provides designers with the tools they need to analyze, refine, and optimize surface geometry, ensuring that their designs are not only aesthetically pleasing but also practical, functional, and cost-effective to manufacture. By prioritizing surface optimization, designers can create designs that stand out for their quality, reliability, and innovation.
Incorporating Organic Shapes
Many design projects necessitate the emulation of organic shapes inspired by nature or biological forms. SolidWorks stands out in this regard, offering powerful tools like freeform modeling and surface sculpting. These techniques enable designers to tap into their creativity and craft captivating designs that transcend the constraints of traditional CAD modeling. With freeform modeling, designers can manipulate surfaces in a more intuitive manner, sculpting intricate details and fluid contours with ease. This approach grants them the freedom to explore complex shapes and experiment with different forms, ultimately leading to more visually striking and innovative designs. Similarly, surface sculpting allows designers to sculpt surfaces using a variety of tools and brushes, simulating the tactile experience of working with clay or other sculpting mediums. This hands-on approach fosters a deeper connection between the designer and the design, resulting in designs that feel more organic and expressive. By incorporating these organic modeling techniques into their surfacing assignments, designers can break away from the rigidity of traditional CAD modeling and explore new realms of creativity. Whether designing futuristic concept cars, ergonomic consumer products, or avant-garde architectural structures, SolidWorks empowers designers to push the boundaries of what's possible and create designs that captivate and inspire.
Conclusion
Mastering advanced techniques in SolidWorks surfacing opens up a world of possibilities for designers, enabling them to confront intricate design challenges with confidence and ingenuity. Armed with a thorough comprehension of surface modeling fundamentals, designers can embark on their projects equipped with the knowledge to navigate complex surfaces adeptly. Leveraging the diverse array of advanced tools provided by SolidWorks empowers designers to push the boundaries of creativity and precision in their designs, achieving results that exude professionalism and finesse.
Furthermore, prioritizing curvature continuity and optimization ensures that designs maintain a seamless and aesthetically pleasing appearance while also adhering to practical considerations such as manufacturability and structural integrity. By honing these critical aspects of surfacing assignments, designers can elevate their work to new heights, delivering solutions that not only meet but exceed the expectations of clients and collaborators.
SolidWorks emerges as the ultimate ally for designers seeking to realize their vision and bring their ideas to fruition. With its intuitive interface and robust feature set, SolidWorks provides a platform for innovation and exploration, empowering designers to unleash their creativity and transform concepts into tangible reality. Whether crafting intricate consumer products, engineering complex machinery, or designing captivating architectural structures, SolidWorks equips designers with the tools they need to turn inspiration into innovation.
Moreover, the versatility of SolidWorks extends beyond traditional CAD modeling, allowing designers to seamlessly integrate organic shapes and freeform designs into their projects. This flexibility enables the creation of designs that transcend conventional boundaries, capturing the essence of nature and human creativity in equal measure. By embracing the full potential of SolidWorks, designers can break free from limitations and embark on a journey of discovery and innovation.
In conclusion, mastering advanced techniques in SolidWorks surfacing is not merely about mastering a software tool—it is about unlocking the boundless potential of design. With dedication, practice, and a willingness to push the envelope, designers can leverage SolidWorks to create designs that inspire, innovate, and leave a lasting impression. As technology continues to evolve and new challenges emerge, SolidWorks remains a steadfast companion for designers, guiding them on their quest to redefine what is possible in the realm of 3D modeling and design.