- The Role of SolidWorks in Product Design
- 3D Modeling and Visualization
- Parametric Design
- Simulation and Testing
- Collaboration and Communication
- Streamlining the Manufacturing Process with SolidWorks
- Design for Manufacturability (DFM)
- CAD-to-CAM Integration
- Rapid Prototyping
- Bill of Materials (BOM) Management
- Design Reuse and Standardization
- Case Study: SolidWorks in Action
- Design Iteration and Simulation
- Design Collaboration
- Manufacturability Analysis
- Rapid Prototyping
- BOM Management
- CAD-to-CAM Integration
- Conclusion
In today's rapidly evolving manufacturing landscape, efficiency and precision are paramount. Companies are constantly seeking ways to optimize their product design and manufacturing processes to deliver high-quality products while minimizing costs and lead times. SolidWorks, a leading computer-aided design (CAD) software, has emerged as a powerful tool for achieving these goals. In this blog, we'll delve into how you can effectively utilize SolidWorks to complete your Solidwork assignment streamline the manufacturing process, and enhance product design. This, in turn, will lead to improved productivity and competitiveness.
The Role of SolidWorks in Product Design
In the realm of modern product design, innovation and precision are the cornerstones of success. SolidWorks, a robust computer-aided design (CAD) software, has emerged as a driving force behind transformative product design processes. With its intuitive interface and comprehensive toolset, SolidWorks empowers designers and engineers to create, refine, and perfect 3D models of products that push the boundaries of innovation. Let's explore how SolidWorks plays a pivotal role in the product design phase, harnessing its capabilities to foster creativity, enhance collaboration, and ensure the highest levels of quality.
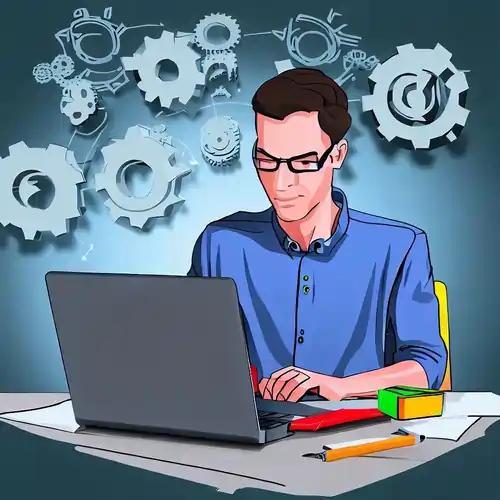
3D Modeling and Visualization
At the heart of SolidWorks lies its remarkable 3D modeling capabilities. Designers can translate their ideas from conceptual sketches into highly detailed and intricate 3D models. Every aspect of the design, from external surfaces to internal components, can be meticulously crafted within the software's virtual environment. This level of detail goes beyond aesthetics—it allows designers to visualize the product from every angle and perspective.
The power of 3D modeling extends to conveying ideas to stakeholders. SolidWorks enables designers to create realistic renderings and visualizations that provide a tangible glimpse into the final product. These visualizations aid in effectively communicating design intent and capturing the essence of the product for presentations, marketing materials, and discussions with clients.
Parametric Design
SolidWorks introduces the concept of parametric design, a game-changer in the world of product development. Parametric design allows engineers to establish relationships between different features of a model. This means that when one dimension or aspect of the design is altered, the entire model adapts accordingly. This dynamic functionality accelerates the design iteration process.
With parametric design, changes can be made quickly and effortlessly, eliminating the need to start from scratch with each modification. This agility in design exploration encourages creativity, experimentation, and refinement. As a result, designers can explore a wide range of design possibilities and rapidly converge on the optimal solution.
Simulation and Testing
SolidWorks empowers engineers to go beyond static designs by introducing simulation and testing within the software itself. Engineers can subject their 3D models to real-world conditions, performing stress analyses, thermal simulations, fluid flow analyses, and more. This virtual testing environment allows for the identification of potential weak points, bottlenecks, or inefficiencies within the design.
By simulating real-world scenarios, engineers can gain insights into how the product will perform in different environments and under various forces. This proactive approach helps detect design flaws early on, mitigating the risk of costly errors during manufacturing or deployment. SolidWorks' simulation capabilities are instrumental in enhancing product reliability and durability.
Collaboration and Communication
In today's interconnected world, collaboration is paramount. SolidWorks recognizes this and offers tools that facilitate seamless collaboration among cross-functional teams. Designers, engineers, and other stakeholders can work collaboratively within the same SolidWorks model, making real-time changes and annotations.
This real-time collaboration streamlines the communication process. Design decisions can be discussed, evaluated, and refined within the software itself. As a result, everyone involved in the project remains informed and aligned, ensuring that design changes are accurately implemented and that the final product aligns with the collective vision.
Streamlining the Manufacturing Process with SolidWorks
In today's competitive landscape, achieving operational efficiency and reducing time-to-market are critical for any manufacturing company. SolidWorks, a versatile and robust CAD software, has emerged as a cornerstone in streamlining the manufacturing process. Beyond its capabilities in designing and visualizing products, SolidWorks offers a suite of tools and features that directly contribute to a more efficient and cost-effective manufacturing journey. Let's explore how SolidWorks achieves this objective through various methodologies:
Design for Manufacturability (DFM)
Design for Manufacturability (DFM) is a fundamental concept that involves designing products in a way that optimizes the ease of production. SolidWorks plays a pivotal role in promoting DFM by offering a range of tools that facilitate manufacturability analysis during the design phase. Designers can evaluate the feasibility of various manufacturing processes, such as machining, sheet metal bending, and injection molding, within the software's virtual environment.
Identifying potential manufacturing challenges early on is a hallmark of SolidWorks' contribution to DFM. By simulating manufacturing processes, designers can anticipate issues and make informed design adjustments to simplify production and reduce the likelihood of costly errors during the manufacturing stage. This proactive approach not only ensures smoother production but also leads to higher-quality products.
CAD-to-CAM Integration
The transition from design to manufacturing traditionally involves the manual translation of design data into machine instructions for Computer-Aided Manufacturing (CAM) systems. SolidWorks revolutionizes this process through seamless CAD-to-CAM integration. By directly interfacing with CAM software, SolidWorks automates the generation of machine instructions based on the design.
This integration eliminates the need for manual data entry, reducing the risk of errors and saving substantial time. The design's accuracy is maintained during the transition, ensuring that the manufactured product faithfully represents the original design. As a result, companies can accelerate their production timeline while maintaining consistency and precision in the manufacturing process.
Rapid Prototyping
Rapid prototyping is an essential step in product development, allowing manufacturers to validate designs and gather feedback before full-scale production. SolidWorks facilitates rapid prototyping by providing the capability to generate files compatible with various rapid prototyping technologies, including 3D printing.
Manufacturers can leverage SolidWorks' 3D models to create physical prototypes that closely resemble the final product. This allows for comprehensive testing, validation, and user feedback collection. By identifying and addressing potential design flaws and improvements early on, companies can avoid costly revisions during mass production, ultimately reducing time-to-market and enhancing product quality.
Bill of Materials (BOM) Management
Effective Bill of Materials (BOM) management is crucial for a smooth manufacturing process. SolidWorks offers robust tools for creating, organizing, and managing BOMs. The BOM provides a comprehensive list of components and materials required for assembling the product.
By utilizing SolidWorks for BOM management, companies streamline procurement processes and reduce the risk of missing components or discrepancies. Accurate BOM management ensures that the right materials are sourced and available when needed, minimizing production delays and enhancing overall efficiency.
Design Reuse and Standardization
SolidWorks empowers companies to establish a library of standardized components and assemblies that can be reused across multiple projects. This approach significantly accelerates the design process by eliminating the need to recreate common components from scratch for each new project.
Moreover, design reuse and standardization maintain consistency in design and manufacturing practices. This consistency enhances efficiency by reducing the potential for errors and ensuring that proven designs are carried forward. The result is a reduction in design time and manufacturing complexity, leading to tangible time and cost savings.
Case Study: SolidWorks in Action
To better understand the practical application of SolidWorks in optimizing product design and manufacturing, let's delve into a detailed case study involving a consumer electronics company that is developing a new smartphone model. This case study showcases how various features and tools within SolidWorks contribute to each stage of the product development lifecycle, ultimately leading to an efficient and high-quality manufacturing process.
Design Iteration and Simulation
At the outset of the project, the design team harnesses the power of SolidWorks to create a comprehensive 3D model of the smartphone. This model includes intricate details such as the camera module, buttons, connectors, and other external features. The software's intuitive interface enables designers to visualize the product in 3D, allowing for a detailed evaluation of its aesthetics and functionality.
However, design is not solely about appearance. To ensure that the smartphone can withstand the real-world conditions it will be exposed to, the team employs SolidWorks' simulation capabilities. Stress analysis is conducted to assess how the device will respond under different forces and loads. Thermal simulations help predict how the smartphone's components will manage heat dissipation, which is crucial for preventing overheating issues. These simulations guide the design team in making informed decisions to enhance the device's durability and performance.
Design Collaboration
In a modern product development environment, collaboration among various teams is essential. The design team and the electronics engineering team work seamlessly within the SolidWorks environment to integrate the internal components into the 3D model. This collaboration ensures that the internal hardware fits perfectly within the device's external design, avoiding any conflicts or spatial constraints. Through real-time collaboration, potential clashes between design aesthetics and functional requirements are resolved efficiently, leading to a harmonious integration of form and function.
Manufacturability Analysis
One of the critical factors in successful product manufacturing is "design for manufacturability" (DFM). SolidWorks provides tools specifically designed for manufacturability analysis, allowing the team to assess how well the smartphone's casing can be manufactured using various techniques. In the case of the smartphone, the team employs SolidWorks to simulate the injection molding process, a common manufacturing method for plastic components.
During the simulation, potential issues such as air traps, warping, or material flow inconsistencies are identified. These insights inform design adjustments aimed at improving the manufacturability of the casing. By addressing these issues early in the design phase, the team minimizes the risk of manufacturing complications and reduces the likelihood of defects, ultimately leading to a smoother and more cost-effective production process.
Rapid Prototyping
With the design concept refined and validated through simulation and collaboration, the team proceeds to generate files for rapid prototyping using SolidWorks. This step allows the creation of a physical prototype of the smartphone using 3D printing technology. The prototype closely resembles the final product, enabling comprehensive testing and evaluation.
The 3D-printed prototype undergoes various tests to validate the design's functionality, ergonomics, and user experience. For example, button placements are assessed for ease of use, and the fit of internal components is verified. User feedback collected from interacting with the prototype can lead to further design refinements before mass production begins.
BOM Management
As the smartphone project advances toward mass production, effective management of the Bill of Materials (BOM) becomes crucial. SolidWorks offers tools that facilitate the creation, organization, and management of the BOM. The BOM lists all the components required to assemble the smartphone, including screws, connectors, circuit boards, and more.
SolidWorks' BOM management capabilities ensure accuracy and consistency in the list of components, reducing the risk of missing or duplicated parts. This accuracy accelerates the procurement process, prevents production delays, and contributes to the overall efficiency of the manufacturing process.
CAD-to-CAM Integration
The design journey culminates in the seamless integration between SolidWorks and computer-aided manufacturing (CAM) software. The finalized smartphone design is transferred to the company's CNC (Computer Numerical Control) machines through this integration. The CAM software interprets the 3D design data and generates precise machine instructions for the manufacturing process.
This integration eliminates the need for manual programming of the CNC machines, reducing the potential for human errors and ensuring that the physical product matches the original design with utmost accuracy. The result is a streamlined transition from the digital design phase to the physical production phase, minimizing time and resource wastage.
Conclusion
SolidWorks has revolutionized the way products are designed and manufactured. By providing a comprehensive suite of tools for 3D modeling, simulation, collaboration, and manufacturing integration, it streamlines the entire product development process. Designers and engineers can create intricate designs, simulate real-world conditions, and optimize products for manufacturing efficiency. Ultimately, SolidWorks empowers companies to bring high-quality products to market faster and more cost-effectively, giving them a competitive edge in today's dynamic manufacturing landscape. Whether it's designing consumer electronics, industrial machinery, or medical devices, SolidWorks continues to play a pivotal role in shaping the future of manufacturing.