- Understanding the Basics of Sheet Metal Design in SolidWorks
- The Significance of Simulation in Sheet Metal Engineering
- Challenges Faced by Students in Sheet Metal Simulation
- Case Studies: Successful Simulation Projects in SolidWorks
- Integrating SolidWorks Simulation into Academic Curriculum
- Tips and Tricks for Efficient Sheet Metal Simulation
- Looking Ahead: The Future of Sheet Metal Simulation in SolidWorks
- Conclusion:
SolidWorks, with its intuitive interface and powerful features, has emerged as a linchpin in the expansive realm of engineering and design. For students, it serves as a gateway to the intricate world of sheet metal structures, providing them with a platform to hone their skills and delve into the nuances of this specialized field. As we embark on this exploration, the focus will be on the captivating facets of simulation and analysis within SolidWorks, viewed through the discerning lens of students. The journey unfolds, offering a glimpse into the practical applications, the challenges encountered in Sheet Metal Assignment, and the valuable insights gleaned through hands-on experiences.
One of the foundational aspects that students encounter when venturing into SolidWorks is grasping the basics of sheet metal design. The software seamlessly integrates sketching and extruding tools, allowing users to transform conceptual ideas into tangible 3D models. This initial phase serves as a stepping stone, providing a solid foundation for understanding the intricacies of sheet metal modeling. As students navigate through this process, they not only acquire technical proficiency but also develop a critical eye for precision and detail—a crucial skill set in the world of engineering.
Simulation, a pivotal element in the SolidWorks repertoire, emerges as a game-changer in the analysis of sheet metal structures. Students find themselves at the crossroads of theory and application, utilizing simulation tools to predict and dissect the behavior of their designs under varying conditions. The significance of this lies not only in validating theoretical knowledge but also in fostering a deeper understanding of how sheet metal components respond to real-world scenarios. It's the bridge between classroom learning and practical implementation, a dynamic space where theories are put to the test, and insights are forged through experimentation.
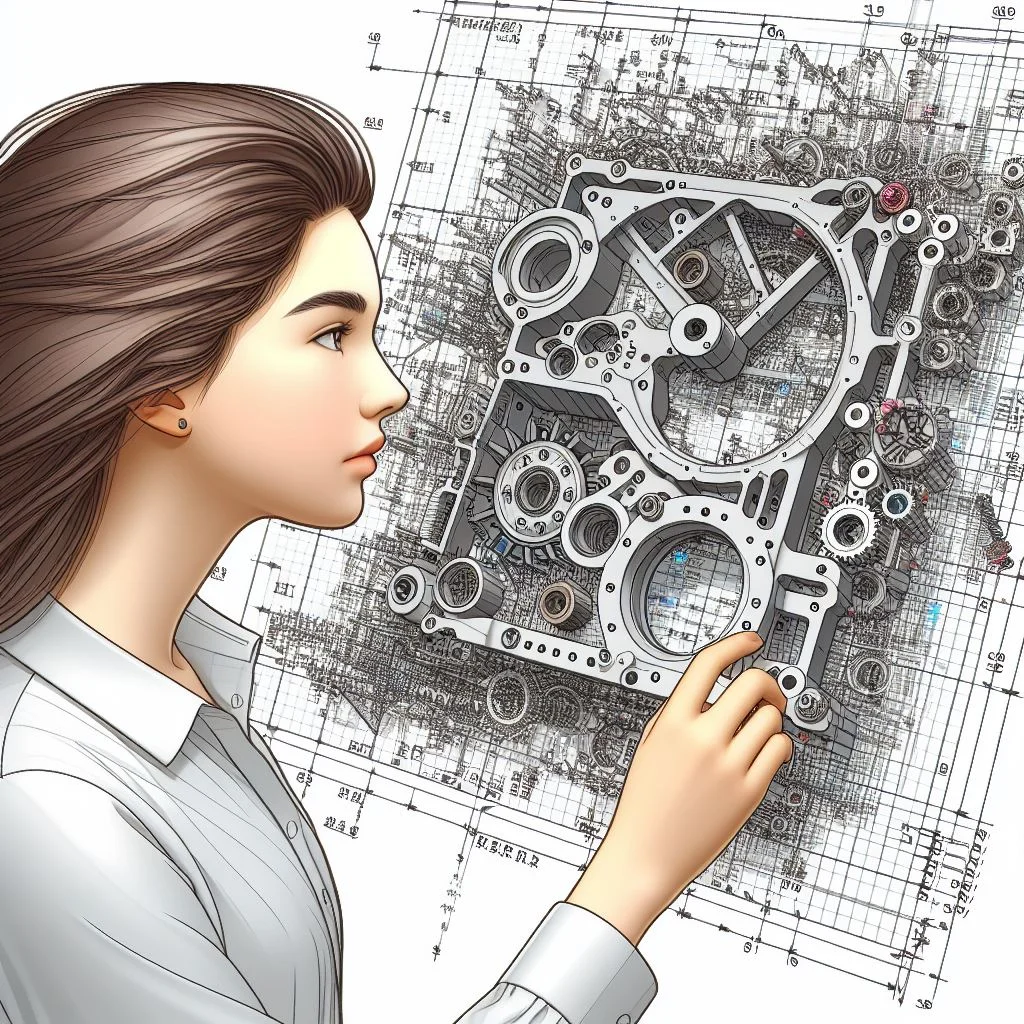
However, this journey is not without its challenges. Students often grapple with translating theoretical knowledge into practical applications. The transition from classroom exercises to real-world simulations can be daunting, and this section of the journey is where students encounter hurdles. These challenges may range from interpreting simulation results accurately to optimizing designs for better performance. The resilience built during these moments of adversity, though, becomes an invaluable asset in shaping a well-rounded engineer.
To illuminate the practical side of SolidWorks simulation, real-world case studies stand as beacons of inspiration. These stories showcase the diverse applications of simulation in sheet metal engineering, from the automotive sector to aerospace designs. Students gain insights into how their counterparts have successfully navigated through complex projects, reinforcing the idea that the application of simulation extends far beyond the theoretical realm. These case studies not only inspire but also serve as tangible examples of what can be achieved through proficiency in SolidWorks simulation.
As academic institutions recognize the growing importance of simulation in the industry, there is a concerted effort to integrate SolidWorks into the curriculum. This strategic move aligns academic learning with industry demands, ensuring that students are well-equipped with the skills needed to thrive in their future careers. The integration of simulation into the academic framework offers students a proactive approach, enabling them to familiarize themselves with industry-standard tools and methodologies from the outset.
Yet, even with the best curriculum in place, students benefit greatly from practical tips and tricks shared by seasoned professionals. This collective wisdom, garnered from years of hands-on experience, serves as a compass for students navigating the intricate landscape of SolidWorks simulation. Whether it's optimizing mesh settings for more accurate results or efficiently utilizing boundary conditions, these insights streamline the simulation process, empowering students to navigate complexities with finesse.
Looking ahead, the future of sheet metal simulation in SolidWorks holds exciting prospects. Technological advancements continue to shape the landscape, introducing new tools and methodologies that push the boundaries of what is possible. This forward-looking perspective encourages students not just to embrace the current state of the art but also to stay attuned to emerging trends. The ability to adapt to evolving technologies positions students as innovators, ready to contribute to the ever-evolving field of sheet metal engineering.
Understanding the Basics of Sheet Metal Design in SolidWorks
SolidWorks stands out as a powerhouse for sheet metal design, providing an intuitive platform that empowers students to bring intricate structures to life. Within this dynamic environment, students are guided through the foundational principles of sheet metal design, gaining a comprehensive understanding of essential concepts. From the initial stages of sketching to the complexities of extruding, SolidWorks offers a seamless interface that fosters creativity and precision in the creation of intricate sheet metal structures.
The process begins with the art of sketching, where students lay the foundation for their designs. SolidWorks' sketching tools facilitate precision and flexibility, enabling users to articulate their ideas with unparalleled accuracy. As students progress, the journey seamlessly transitions into the realm of extruding, where 2D sketches transform into 3D models. This transformative stage not only emphasizes the depth and dimensionality of sheet metal structures but also familiarizes students with the software's extrusion capabilities.
What sets SolidWorks apart in sheet metal design is its arsenal of unique tools tailored explicitly for this specialized field. These tools cater to the intricacies of working with malleable materials, allowing students to bend, fold, and shape sheet metal with unparalleled control. From the creation of flanges to the incorporation of intricate details, SolidWorks equips students with a diverse toolkit that enhances their ability to navigate the complexities of sheet metal modeling.
The Significance of Simulation in Sheet Metal Engineering
Simulation stands as a pivotal aspect in the realm of sheet metal engineering, acting as a formidable ally in guaranteeing the structural integrity of intricate components. Within the vast repertoire of SolidWorks simulation tools, students find a versatile toolkit that enables them to anticipate and scrutinize the behavior of sheet metal structures across a spectrum of conditions. This proficiency is invaluable in real-world engineering projects, where the ability to predict outcomes and assess structural responses is a cornerstone of success.
SolidWorks, a trailblazer in the field, equips students with simulation tools that transcend mere theoretical understanding. By immersing themselves in the software, students gain a hands-on experience that goes beyond textbooks. They learn to navigate the complexities of structural analysis, gaining insights into how various factors—such as material properties, loads, and environmental conditions—interact and influence the performance of sheet metal structures.
The practical implications of simulation become evident through real-world applications and case studies. As students engage in these studies, they witness firsthand how simulation in SolidWorks becomes a strategic asset in designing components for industries ranging from automotive to aerospace. Whether predicting the impact of external forces or optimizing designs for weight and durability, the applications are as diverse as the engineering landscape itself.
In essence, SolidWorks simulation empowers students to bridge the gap between theory and application, fostering a holistic understanding of sheet metal engineering. As they explore the capabilities of simulation tools, students not only enhance their technical proficiency but also cultivate a mindset geared towards innovation and problem-solving—a mindset that is invaluable as they embark on their professional journeys in the world of engineering.
Challenges Faced by Students in Sheet Metal Simulation
While SolidWorks equips students with robust simulation tools, translating theoretical knowledge into practical applications poses a common challenge. Students grapple with the intricate balance required to seamlessly integrate their understanding of sheet metal simulation principles into real-world scenarios. One prevalent hurdle is the initial learning curve associated with mastering the diverse features and functionalities of SolidWorks simulation tools.
Moreover, students often encounter difficulties in accurately defining material properties, boundary conditions, and constraints. These foundational elements play a pivotal role in the accuracy of simulations, making it imperative for students to grasp their significance. Lack of hands-on experience can contribute to misconceptions or oversights in setting up simulations, leading to inaccurate results.
Another notable challenge is the optimization of simulation parameters. Students may struggle to identify the most suitable meshing techniques, simulation types, and convergence criteria for a given sheet metal structure. This dilemma highlights the importance of not only understanding the software but also developing a deep comprehension of the underlying engineering principles driving simulation processes.
To address these challenges, students can benefit from practical exercises that bridge the gap between theory and application. Incorporating real-world projects into coursework allows students to navigate the complexities of sheet metal simulation, enhancing their problem-solving skills and fostering a holistic understanding of engineering principles. Additionally, mentorship programs and collaborative learning environments provide valuable support, enabling students to exchange insights and collectively overcome challenges encountered during sheet metal simulation endeavors. By acknowledging and actively addressing these challenges, students can fortify their simulation and analysis skills, ensuring a smoother transition from theoretical concepts to hands-on proficiency in SolidWorks.
Case Studies: Successful Simulation Projects in SolidWorks
In this section, we will delve deeper into the fascinating realm of real-world projects carried out by students utilizing SolidWorks simulation for sheet metal engineering. The versatility of SolidWorks becomes evident as we explore a spectrum of applications, ranging from automotive components to intricate aerospace designs.
Imagine a group of engineering students collaborating to optimize the design of a car chassis using SolidWorks simulation. By subjecting the sheet metal structure to virtual stress tests and load simulations, they were able to enhance the chassis's durability while minimizing weight – a critical factor in automotive design. The insights gained from this project not only contributed to academic excellence but also provided valuable solutions for the automotive industry's ongoing pursuit of efficiency and performance.
On a different note, consider a team of aerospace engineering students employing SolidWorks simulation to analyze the structural integrity of aircraft components. Through intricate simulations of forces, vibrations, and thermal stresses, they ensured that the sheet metal structures could withstand the harsh conditions of flight. These case studies not only showcase the depth of SolidWorks capabilities but also underscore its significance in shaping advancements in critical industries.
These student-led projects not only inspire with their ingenuity but also serve as powerful educational tools. By examining these case studies, readers gain a profound understanding of how SolidWorks simulation can be harnessed to address real-world engineering challenges. As we navigate through these success stories, the limitless possibilities of simulation in the field of sheet metal engineering come to life, leaving a lasting impression on both aspiring and seasoned engineers alike.
Integrating SolidWorks Simulation into Academic Curriculum
Recognizing the growing importance of simulation in the industry, educational institutions are actively integrating SolidWorks into their academic curriculum. This strategic shift aligns with the industry's demand for engineers well-versed in simulation tools, equipping students with practical skills for the dynamic world of engineering. The benefits of this integration are manifold, as students not only gain proficiency in SolidWorks but also develop a deeper understanding of the role simulation plays in real-world scenarios.
One significant advantage is the bridging of the gap between theoretical knowledge and hands-on application. By incorporating SolidWorks simulation into coursework, students experience a seamless transition from classroom concepts to practical problem-solving. This enhances their ability to analyze and optimize sheet metal structures, laying a robust foundation for their future careers. Moreover, exposure to industry-standard simulation tools during academic years gives students a competitive edge, making them more attractive to prospective employers seeking candidates with practical skills.
However, the integration of SolidWorks simulation into the academic curriculum is not without its challenges. Institutions face the task of ensuring that faculty members are well-trained and updated on the latest features of SolidWorks. This training is crucial to enable educators to effectively impart knowledge and guide students in utilizing simulation tools to their full potential. Additionally, the cost implications of acquiring licenses for educational purposes and maintaining hardware compatibility present logistical challenges for institutions with limited resources.
Nevertheless, overcoming these challenges is essential for preparing students for real-world engineering challenges. Integrating SolidWorks simulation into academic programs fosters a culture of innovation and critical thinking, nurturing a new generation of engineers capable of addressing complex design and analysis problems. As simulation continues to play a pivotal role in the industry, educational institutions embracing this trend contribute significantly to the professional development of their students, empowering them to excel in the competitive field of engineering.
Tips and Tricks for Efficient Sheet Metal Simulation
Practical insights from seasoned professionals play a pivotal role in augmenting a student's proficiency in SolidWorks simulation. As students embark on their journey of mastering sheet metal simulation, incorporating tried-and-true tips and tricks can be instrumental in navigating the complexities of the software.
One key piece of advice is to prioritize a systematic approach to the simulation process. Breaking down the task into smaller, manageable steps not only makes it more approachable but also facilitates a deeper understanding of the underlying concepts. Seasoned users often stress the importance of meticulous planning, emphasizing the creation of a well-organized workflow that aligns with the specific requirements of sheet metal simulation projects.
Furthermore, the judicious use of constraints and boundary conditions emerges as a recurring theme in the tips shared by experienced users. Students are encouraged to delve into the nuances of constraint application, understanding how it influences the simulation outcomes. A strategic approach to defining boundary conditions ensures a more accurate representation of real-world scenarios, contributing to the reliability of the simulation results.
Collaboration and knowledge-sharing among peers also feature prominently in the tips provided by industry professionals. Encouraging students to actively engage in forums, discussion groups, and collaborative projects fosters a community of learning where insights and experiences can be exchanged. This not only broadens the perspectives of aspiring engineers but also exposes them to diverse problem-solving approaches, enriching their skill set.
Looking Ahead: The Future of Sheet Metal Simulation in SolidWorks
As technology continues to advance, the landscape of sheet metal simulation in SolidWorks undergoes a dynamic transformation. The latest trends and advancements in SolidWorks simulation tools offer a profound glimpse into the future of sheet metal engineering, presenting students with exciting opportunities and challenges. One notable trend on the horizon is the integration of artificial intelligence (AI) and machine learning (ML) algorithms into SolidWorks simulation, revolutionizing the accuracy and efficiency of predictive modeling.
AI-powered simulations can analyze vast datasets, enabling engineers to predict the behavior of sheet metal structures with unprecedented precision. This not only enhances the reliability of simulations but also accelerates the design iteration process, allowing for quicker and more informed decision-making. As students engage with these cutting-edge tools, they gain invaluable exposure to the intersection of engineering and AI, preparing them for a tech-driven future.
Furthermore, the future of sheet metal simulation in SolidWorks emphasizes sustainability and environmental considerations. With an increasing focus on eco-friendly design practices, simulation tools are evolving to assess the environmental impact of sheet metal structures. Students will play a pivotal role in shaping a sustainable future by mastering simulation techniques that prioritize efficiency while minimizing ecological footprints.
Conclusion:
In conclusion, the transformative role of SolidWorks simulation in shaping the next generation of engineers cannot be overstated. As technology continues to advance, the ability to simulate and analyze sheet metal structures becomes increasingly crucial in various industries. By immersing themselves in the world of SolidWorks simulation, students not only enhance their technical skills but also develop a mindset that is vital for innovation and excellence in the ever-evolving field of engineering.
Embracing the challenges presented by sheet metal simulation is a fundamental step toward personal and professional growth. It's through overcoming obstacles and pushing the boundaries of one's understanding that true mastery is achieved. SolidWorks provides a dynamic platform for students to navigate complexities, fostering resilience and problem-solving abilities that are indispensable in real-world scenarios.
The opportunities presented by sheet metal simulation are vast, offering students a chance to engage with cutting-edge technologies and contribute to groundbreaking projects. As students venture into the professional realm, the skills honed through SolidWorks simulation become a valuable asset. Whether working in automotive design, aerospace engineering, or any other field, the ability to simulate and analyze sheet metal structures gives engineers a competitive edge and opens doors to exciting career prospects.
Moreover, SolidWorks simulation instills a passion for innovation and excellence. The iterative nature of simulation encourages students to continuously refine and optimize their designs, pushing them to think creatively and critically. This mindset not only benefits individual projects but also fosters a culture of continuous improvement that is vital for success in the fast-paced world of engineering.
By encouraging students to embrace the challenges inherent in sheet metal simulation, educators play a pivotal role in nurturing the next generation of forward-thinking engineers. Providing a supportive environment where students can explore, experiment, and learn from both successes and failures is key to fostering a passion for innovation. SolidWorks serves as a powerful tool in this educational journey, empowering students to push boundaries and explore the limitless possibilities of sheet metal engineering.
In essence, SolidWorks simulation is not just a tool; it's a catalyst for growth and development. It shapes engineers who are not afraid to tackle complex problems, who are driven by curiosity, and who possess the skills to bring their ideas to life. As we look to the future, the impact of SolidWorks on the engineering landscape is undeniable, with each student trained in its intricacies contributing to a collective pool of knowledge that propels the industry forward.
In conclusion, let us celebrate the transformative journey that SolidWorks simulation offers to aspiring engineers. Through challenges and opportunities alike, it equips students with the skills, mindset, and passion needed to thrive in a world that demands constant innovation and excellence. The future of engineering is in the hands of those who embrace the power of simulation, and SolidWorks stands as a guiding force in this exciting and ever-evolving landscape.