- Understanding SolidWorks Assemblies
- Streamlining Collaborative Efforts
- Advanced Mating Techniques
- Top-Down vs. Bottom-Up Approaches
- Handling Large Assemblies with Performance in Mind
- Simulation and Analysis in Assemblies
- Case Studies: Real-World Applications
- Future Trends and Innovations
- Conclusion
In the realm of 3D CAD design, SolidWorks stands as a formidable tool, enabling engineers to bring their innovative concepts to life. One of its key features that truly shines in the face of complex engineering challenges is its assembly functionality. In this blog, we will delve into the intricacies of SolidWorks assemblies, exploring how they empower engineers to tackle the most intricate problems in the field. Whether you require assistance with your SolidWorks assignment or seek to enhance your proficiency in 3D CAD design, understanding SolidWorks assemblies can significantly elevate your capabilities and efficiency in engineering design projects.
SolidWorks, developed by Dassault Systèmes, has become synonymous with cutting-edge 3D design and engineering precision. Its assembly functionality serves as the linchpin for creating intricate models by seamlessly integrating individual components into a cohesive whole. Engineers, designers, and architects leverage this feature to conceptualize, refine, and realize their visions, regardless of the project's complexity.
The power of SolidWorks assemblies lies in their ability to mimic real-world scenarios, where components interact with one another in intricate ways. This capability enables engineers to simulate and analyze the behavior of their designs under various conditions, a crucial aspect when addressing complex engineering challenges. Assemblies, acting as virtual prototypes, allow for the identification and resolution of potential issues early in the design process, saving both time and resources.
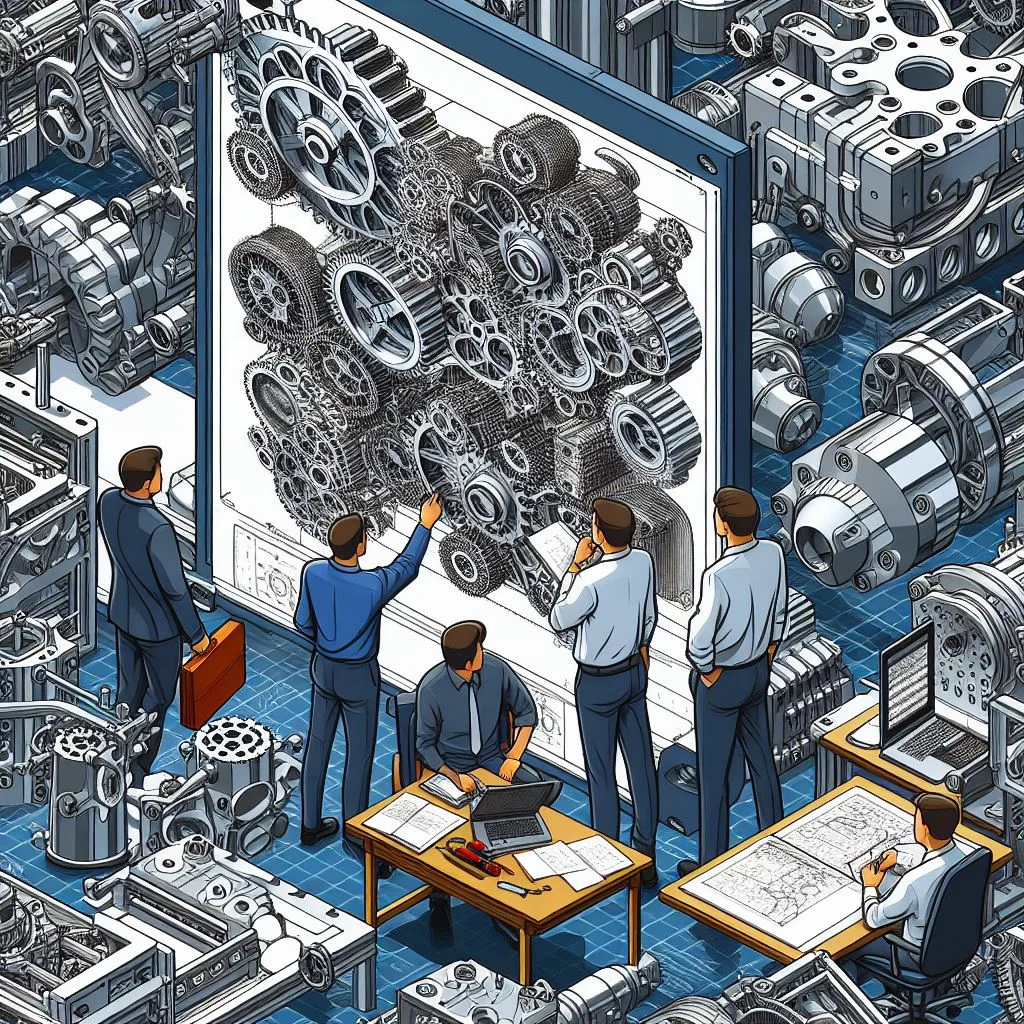
In the collaborative landscape of modern engineering projects, SolidWorks assemblies offer a dynamic platform for teamwork. With features such as version control and real-time updates, multiple team members can work concurrently on different aspects of a project. This collaborative environment fosters creativity and efficiency, ensuring that diverse perspectives contribute to the overall success of the endeavor. Comments and annotations within the assembly further enhance communication, streamlining the iterative design process.
Understanding the nuances of advanced mating techniques is paramount for engineers aiming to master SolidWorks assemblies. The mating of components within an assembly dictates their spatial relationships, and SolidWorks provides a spectrum of mating options. From the foundational coincident and concentric mates to the more intricate mechanical mates, each technique plays a crucial role in achieving design accuracy. Engineers must navigate these options skillfully to create robust and functional assemblies.
When it comes to approaching the assembly process, engineers often face the decision between a top-down or bottom-up design methodology. The top-down approach involves creating an overarching skeleton or master model, influencing the design of individual components. On the other hand, the bottom-up approach involves assembling components independently and then combining them into a larger assembly. The choice between these methods depends on project requirements, with each offering distinct advantages and considerations.
For projects involving a multitude of components, the challenge extends beyond conceptualization and design to the practical realm of performance optimization. Large assemblies can strain system resources, affecting software performance and user experience. SolidWorks addresses this concern by providing tools for optimizing performance, including simplification techniques, level of detail settings, and configurations. These strategies empower engineers to navigate and manipulate large assemblies efficiently.
In the realm of simulation and analysis, SolidWorks assemblies offer a robust suite of tools. Engineers can subject their designs to real-world conditions, assessing factors like stress, motion, and interference. This capability is invaluable for validating the performance and reliability of complex assemblies, ensuring that the end product meets the stringent requirements of the intended application.
As we transition from theory to application, real-world case studies illuminate the practical impact of SolidWorks assemblies in diverse industries. These examples showcase how engineers have harnessed the capabilities of SolidWorks to overcome complex challenges, from designing intricate machinery to optimizing structural components. The versatility of SolidWorks is evident as it caters to the unique demands of fields as varied as aerospace, automotive, and consumer electronics.
Looking ahead, the trajectory of SolidWorks assemblies hints at exciting developments. The continuous evolution of this software aligns with the ever-changing landscape of engineering. Future enhancements may include more intuitive features, enhanced collaboration tools, and even greater capabilities for handling massive assemblies. As technology advances, SolidWorks remains at the forefront, ready to empower engineers in tackling the next generation of complex engineering problems.
Understanding SolidWorks Assemblies
SolidWorks assemblies play a pivotal role in bringing intricate engineering designs to fruition by seamlessly integrating individual components and sub-assemblies. At the core of this capability lies the well-defined assembly structure, a fundamental aspect that engineers must grasp to navigate the complexities of their projects effectively.
The assembly structure in SolidWorks serves as a digital representation of how different parts come together to form the final product. This hierarchical arrangement not only mirrors the physical assembly process but also streamlines the design workflow. Understanding the interplay between components and their relationships within the structure is crucial for creating robust and functional models.
Mates, another key element in SolidWorks assemblies, govern the spatial relationships between components. These relationships define how parts interact and move relative to each other. Exploring the diverse mate options, including concentric mates for coaxial alignment, coincident mates for precise positioning, and mechanical mates for intricate motion control, empowers engineers to create assemblies with the desired functionality.
Furthermore, the significance of hierarchical organization cannot be overstated when managing complex projects. SolidWorks allows for the creation of sub-assemblies, enabling a modular approach to design. This modularization enhances collaboration, as different teams can work on specific sub-assemblies concurrently, promoting efficiency and parallel development.
Streamlining Collaborative Efforts
Collaboration is a cornerstone in engineering projects, and SolidWorks assemblies excel in providing a conducive environment for multiple team members to work seamlessly together. This collaborative potential goes beyond just assembling parts; it encompasses a suite of features designed to enhance teamwork and streamline the design process.
SolidWorks assemblies incorporate robust version control mechanisms, ensuring that all team members are on the same page regarding the evolution of the project. This helps prevent conflicts and confusion that may arise when dealing with different iterations of a design. With version control, engineers can confidently make modifications, knowing that the entire team can access the latest updates in real-time.
The inclusion of comments within SolidWorks assemblies further facilitates communication among team members. Engineers can leave notes, suggestions, or explanations directly within the assembly file, fostering a dynamic and iterative design process. This collaborative annotation system enhances clarity, reduces errors, and promotes a shared understanding of the project's intricacies.
Real-time updates represent a pivotal aspect of SolidWorks assemblies, enabling instantaneous synchronization of changes across the entire team. This feature ensures that all team members have access to the latest modifications made by their colleagues, promoting a cohesive and synchronized approach to the design process.
Advanced Mating Techniques
Mating components within a SolidWorks assembly is a nuanced task that demands a deep understanding of advanced mating techniques. In the realm of 3D CAD design, precision is paramount, and the way individual parts come together significantly impacts the overall accuracy of the design.
Concentric mates, a fundamental aspect of mating, align components based on their concentric surfaces or axes. This technique ensures that cylindrical or spherical elements share a common center point, promoting symmetry and eliminating misalignments.
Coincident mates, on the other hand, involve aligning faces or edges precisely. This technique is crucial when dealing with parts that need to seamlessly fit together, leaving no room for gaps or misfits. Achieving a flawless connection between components enhances the overall structural integrity of the assembly.
Mechanical mates introduce a dynamic aspect to the mating process by simulating mechanical interactions. Engineers can simulate gears, cams, and other intricate mechanical connections within the assembly, providing a realistic representation of how the components will behave in the actual product.
A comprehensive understanding of these advanced mating techniques is indispensable for addressing intricate engineering challenges. The meticulous application of concentric, coincident, and mechanical mates not only ensures design accuracy but also lays the foundation for a robust and seamlessly functioning assembly. Engineers armed with this knowledge can navigate complex designs with confidence, knowing that each component's placement is meticulously calculated to meet the highest standards of precision and functionality.
Top-Down vs. Bottom-Up Approaches
When confronted with the task of designing complex assemblies in SolidWorks, engineers often find themselves at a crossroads – choosing between the top-down and bottom-up design approaches. Each method carries its own set of advantages and disadvantages, demanding careful consideration to align with project goals and constraints.
Top-down design involves starting with an overarching concept and breaking it down into smaller components. This approach allows for a holistic view of the project from the outset, facilitating better coordination among different elements. Engineers can establish key parameters and relationships early on, ensuring a cohesive and integrated final product. However, it requires a thorough understanding of the entire system upfront, which may pose challenges when dealing with highly intricate designs.
On the other hand, the bottom-up approach begins with individual components that are gradually assembled to form the complete design. This method provides a more detailed understanding of each part, making it particularly useful for intricate and specialized components. It allows for flexibility in handling complex geometries and facilitates parallel development. Nonetheless, challenges may arise in ensuring the seamless integration of diverse components, especially as the project scales up.
The decision between these approaches hinges on project requirements, team expertise, and the nature of the design challenge. In scenarios where a clear overall vision exists and inter-component relationships are well-defined, a top-down approach might be preferable. Conversely, for projects with a multitude of intricate parts or where flexibility in component design is crucial, a bottom-up strategy may be more suitable.
Ultimately, successful assembly design in SolidWorks involves a judicious combination of these approaches, leveraging the strengths of each to achieve optimal results. By carefully evaluating the specific demands of a project, engineers can determine the most effective strategy, ensuring efficiency and success in tackling complex engineering problems.
Handling Large Assemblies with Performance in Mind
Assemblies comprising a multitude of components pose a unique set of challenges, often taxing system resources and compromising overall performance. To navigate this hurdle effectively, engineers can employ a variety of strategic measures aimed at optimizing performance.
One key approach involves the judicious use of simplification techniques. By identifying non-essential details or components that do not significantly impact the overall functionality of the assembly, engineers can streamline the model without sacrificing its core integrity. This not only reduces the computational load but also enhances the efficiency of the design process.
Furthermore, the manipulation of level-of-detail settings emerges as a powerful tool in managing large assemblies. Engineers can create simplified representations of intricate components, adjusting the level of detail based on the specific requirements of the task at hand. This adaptive approach ensures that the system dedicates resources proportionately, preserving computational power for critical aspects of the assembly.
Configurations also play a pivotal role in optimizing performance. By creating different configurations for various states of the assembly, engineers can selectively load components as needed, minimizing the strain on resources. This dynamic configuration management allows for a more responsive and resource-efficient handling of large assemblies during different stages of the design process.
Simulation and Analysis in Assemblies
SolidWorks distinguishes itself by extending its functionality beyond the conventional design scope, providing engineers with robust simulation and analysis tools. These tools play a pivotal role in elevating the design process from mere visualization to a comprehensive evaluation of performance and behavior under diverse conditions.
Engineers harness SolidWorks' simulation capabilities to subject their assemblies to a battery of tests, replicating real-world scenarios and environmental factors. Through finite element analysis (FEA) and other simulation techniques, they can gauge how the components within the assembly interact, identifying potential weak points, stress concentrations, or areas requiring optimization.
This simulation-driven approach enables engineers to refine their designs iteratively, fine-tuning parameters to enhance structural integrity, durability, and overall performance. By virtually testing assemblies, engineers gain insights into how they will perform in the field, reducing the likelihood of unexpected issues during the physical prototyping or production phases.
Moreover, SolidWorks' analysis tools facilitate the exploration of dynamic behaviors, such as motion studies and kinematic analyses. This empowers engineers to anticipate and address challenges related to movement, interference, or ergonomic considerations, ensuring that the final product not only meets but exceeds the necessary criteria for success.
Case Studies: Real-World Applications
To solidify our understanding, we will delve into real-world case studies that illuminate the profound impact SolidWorks assemblies have had in overcoming complex engineering challenges. These case studies serve as compelling narratives, showcasing the versatility and applicability of SolidWorks across a spectrum of industries.
In the aerospace sector, SolidWorks assemblies have been instrumental in designing intricate components of aircraft, optimizing aerodynamics, and ensuring structural integrity. By simulating various conditions and stress factors, engineers can fine-tune their designs, resulting in more efficient and safer airborne vehicles.
The automotive industry also stands as a testament to SolidWorks' prowess. From conceptualizing groundbreaking vehicle designs to streamlining manufacturing processes, SolidWorks assemblies facilitate innovation. Engineers can visualize the interplay of numerous components, ensuring seamless integration and adherence to safety standards.
Moreover, in the field of medical devices, SolidWorks has proven indispensable. Designing complex, precision instruments demands meticulous attention to detail, and SolidWorks assemblies provide a platform for engineers to achieve unparalleled accuracy. These assemblies enable the simulation of device functionality and streamline the prototyping phase, expediting the development of life-saving technologies.
Beyond these sectors, SolidWorks finds application in renewable energy projects, consumer electronics, and more. The case studies not only highlight the adaptability of SolidWorks but also underscore its role as a catalyst for innovation in diverse engineering domains. These real-world examples reinforce the notion that SolidWorks assemblies are not just a tool but a transformative force in the hands of skilled engineers, shaping the future of design and engineering.
Future Trends and Innovations
The world of engineering is dynamic, and SolidWorks, as a leading player in the field of Computer-Aided Design (CAD), is continually evolving to meet the ever-changing landscape of technological challenges. Looking ahead, we can anticipate several exciting trends and innovations within SolidWorks assemblies that are poised to redefine the way engineers approach their projects.
One notable trajectory is the integration of Artificial Intelligence (AI) and machine learning into SolidWorks assemblies. As technology advances, we can expect SolidWorks to harness the power of AI to automate certain design processes, optimize component placement, and even suggest innovative solutions based on historical project data. This shift towards AI-driven design is not only expected to enhance efficiency but also open up new avenues for creativity and problem-solving.
Additionally, the future holds promise for enhanced collaboration features within SolidWorks assemblies. With the global nature of engineering projects, the need for seamless communication and cooperation among team members is crucial. Future iterations of SolidWorks may introduce even more intuitive and real-time collaborative tools, fostering a connected and efficient work environment.
Moreover, the growing emphasis on sustainability in engineering is likely to influence SolidWorks assemblies in the future. Expect developments that align with eco-friendly design principles, including tools for material selection based on environmental impact assessments and features that facilitate the creation of energy-efficient and environmentally conscious assemblies.
Conclusion
In conclusion, SolidWorks assemblies emerge as an indispensable tool for engineers grappling with intricate design challenges. Through the exploration of assembly basics, collaborative features, advanced mating techniques, and strategies for handling large assemblies, we've uncovered the depth of SolidWorks' capabilities. The ability to seamlessly integrate top-down and bottom-up approaches further enhances its versatility, providing engineers with flexibility in their design processes.
As we navigate the intricate world of SolidWorks assemblies, it becomes evident that these features not only streamline the design phase but also foster a collaborative environment, where teams can work seamlessly towards a common goal. The advanced mating techniques discussed offer a nuanced approach to component relationships, ensuring precision and accuracy in the final product. The considerations for managing large assemblies underscore the software's commitment to performance optimization, a crucial aspect in handling complex engineering projects efficiently.
Simulation and analysis tools within SolidWorks assemblies open up new dimensions for engineers, enabling them to subject their designs to various conditions virtually. This not only reduces the need for physical prototypes but also accelerates the iteration process, ultimately leading to more refined and robust designs. The inclusion of real-world case studies further reinforces the practical application of SolidWorks assemblies across diverse industries, demonstrating its efficacy in solving complex engineering problems.
Looking ahead, the future trends and innovations in SolidWorks assemblies hold exciting prospects for the engineering community. As technology continues to advance, SolidWorks is likely to incorporate even more sophisticated features, providing engineers with cutting-edge tools to address the challenges of tomorrow. Whether it's the integration of artificial intelligence for enhanced design suggestions or further enhancements in collaborative functionalities, SolidWorks remains at the forefront of innovation.