- Understanding Multiphase Flow
- 1. Gas-Liquid Flow
- 2. Gas-Solid Flow
- 3. Liquid-Liquid Flow
- Challenges in Simulating Multiphase Flow
- 1. Phase Interaction Modeling
- 2. Interface Tracking and Surface Tension
- 3. Computational Resources and Meshing
- Tackling Complex Assignments in Multiphase Flow
- 1. Problem Formulation and Boundary Conditions
- 2. Model Selection and Validation
- 3. Meshing and Grid Independence Study
- 4. Simulation Setup and Solver Settings
- Conclusion
The study of fluid flow has been completely transformed by computational fluid dynamics (CFD), which has given engineers and researchers invaluable knowledge of how fluids behave in various engineering applications. Multiphase flow is a difficult and fascinating field of study among the complex phenomena encountered in CFD. The simultaneous movement of various fluid phases, such as gases, liquids, and solid particles within a system, is known as multiphase flow. Chemical processing, oil and gas, environmental engineering, and biomedical engineering are just a few of the sectors where it is crucial. For processes to be optimised, performance to be predicted, and engineering systems to be safe and reliable, the multiphase flow must be accurately understood and simulated. An in-depth discussion of multiphase flow and its role in computational fluid dynamics is provided in this blog. The various types of multiphase flow, such as gas-liquid flow, gas-solid flow, and liquid-liquid flow, will be examined, as well as the difficulties in simulating and analysing these intricate systems. We will discuss the main challenges encountered when tackling assignments related to multiphase flow in CFD, from phase interaction modelling to interface tracking and surface tension effects. Engineers and researchers can improve their abilities to deal with real-world fluid flow problems and optimise the performance of various engineering applications by unravelling the complexities of multiphase flow and comprehending the methodologies used to address its complexities.
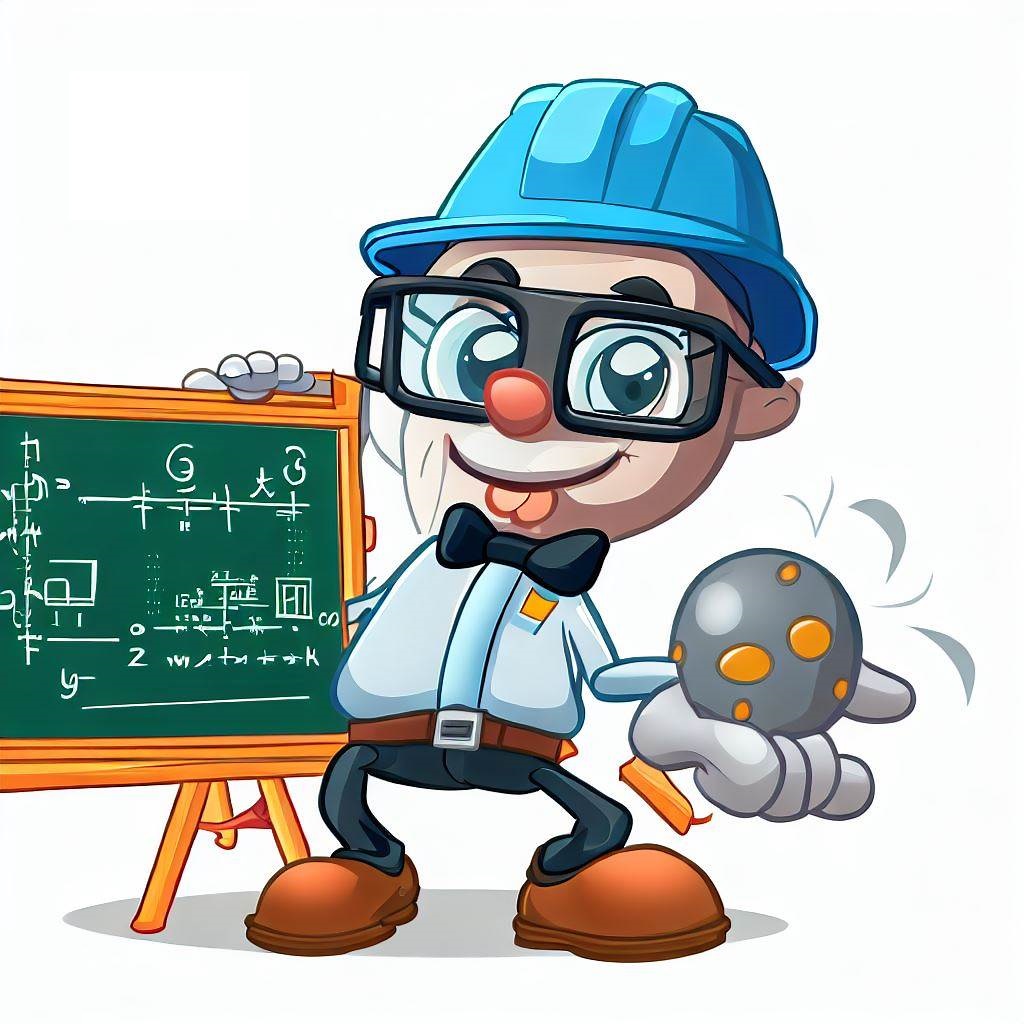
Understanding Multiphase Flow
Multiple fluid phases must move through and interact with one another simultaneously within a system, which is known as multiphase flow, a complex phenomenon found in many engineering fields. It includes a variety of flows, such as liquid-liquid, gas-liquid, and gas-solid flows. Each of the four types of gas-liquid flow, bubbly flow, slug flow, annular flow, and mist flow, has its own unique properties, such as dispersed gas bubbles, alternating gas and liquid sections, a thin liquid film surrounding a gas core, or tiny liquid droplets suspended in a gas phase. In fluidized beds, particle transport systems, and pneumatic conveying, there is an interaction between a gas phase and solid particles. Two immiscible liquids can flow together in a liquid-liquid flow, which has uses in emulsion formation, oil-water separation, and chemical processing. Designing effective machinery, optimising industrial processes, and ensuring safe and dependable operation all depend on an understanding of the behaviour of the multiphase flow. Researchers and engineers can gain important insights into the intricate nature of multiphase flow and create precise models and simulations to address real-world engineering challenges by investigating the dynamics and interfacial interactions between fluid phases. Let's examine the three main categories of multiphase flow to gain a better understanding.
1. Gas-Liquid Flow
A gas phase and a liquid phase interact during a gas-liquid flow. Examples of typical flows include mist flow, annular flow, bubbly flow, and slug flow. Small gas bubbles are dispersed throughout a liquid in a bubbly flow, whereas slug flow displays alternating sections of gas and liquid. Mist flow is characterised by tiny liquid droplets suspended in a gas phase, while annular flow happens when a thin liquid film surrounds a central gas core.
2. Gas-Solid Flow
The interaction of a gas phase and solid particles is known as gas-solid flow. It frequently occurs in particle transport systems, fluidized beds, and pneumatic conveying. Particle size, density, shape, and interactions between particles are some of the variables that affect how a gas-solid flow behaves. Designing effective machinery and optimising industrial processes requires a thorough understanding of the dynamics of the gas-solid flow.
3. Liquid-Liquid Flow
When two immiscible liquids mix, the result is called liquid-liquid flow. Chemical processing, oil-water separation, and emulsion formation frequently involve this type of flow. Interfacial tension, droplet size distribution, and individual liquid flow rates all influence how liquid-liquid flow behaves. For effective separation methods and product quality control, accurate liquid-liquid flow characterization and modelling are crucial.
Challenges in Simulating Multiphase Flow
Due to the intricate nature of the interactions between various fluid phases, simulating multiphase flow in computational fluid dynamics (CFD) presents a number of difficulties. Modelling phase interactions accurately is one of the main difficulties. The creation of suitable models is necessary to capture the dynamic behaviour and interactions between the gas, liquid, and solid phases. These models must accurately depict each phase's unique properties and interactions with other phases. Interface tracking and taking surface tension effects into account present yet another formidable challenge. For the purpose of understanding the behaviour of multiphase flows, it is essential to precisely track the motion and shape of fluid interfaces. In addition, surface tension has a big impact on the dynamics and stability of interfaces. It takes specialised numerical methods and careful consideration of the relevant physical properties to adequately account for these effects. Simulating multiphase flow is also difficult due to meshing and computational resources. Multiphase flow simulations frequently require significant computational resources because of the increased complexity and additional equations involved. A delicate balance must be struck when meshing the simulation domain properly to accurately capture flow characteristics while maintaining an affordable computational cost. To produce accurate and reliable multiphase flow simulations, it is crucial to strike a balance between computational efficiency and accuracy. To meet these challenges, multiphase flow simulations in CFD need to be more accurate and effective, which calls for ongoing improvements in modelling strategies, numerical approaches, and computational resources. Due to the intricate interactions between various fluid phases, simulating multiphase flow in CFD poses a number of difficulties. These difficulties include:
1. Phase Interaction Modeling
For realistic multiphase flow simulations, it is essential to capture the interactions between various fluid phases accurately. To describe the behaviour of each phase and their interactions, appropriate models must be developed. The Eulerian-Eulerian and Eulerian-Lagrangian methods, which treat the fluid phases as distinct entities or follow individual particles, respectively, are common approaches.
2. Interface Tracking and Surface Tension
Multiphase flow simulations must accurately track fluid interfaces and take surface tension effects into account. Heat and mass transfer processes can be significantly impacted by the shape and dynamics of interfaces, which are important in determining flow behaviour. Surface tension and interface tracking effects are handled using a variety of numerical techniques, including the volume of fluid (VOF) and level set methods.
3. Computational Resources and Meshing
Due to the increased complexity and additional equations required, simulating multiphase flow frequently requires significant computational resources. To accurately represent the flow characteristics, the simulation domain must be discretized using an appropriate meshing strategy. A significant challenge in multiphase flow simulations is striking a balance between accuracy and computational efficiency.
Tackling Complex Assignments in Multiphase Flow
To ensure accurate and trustworthy results when handling complex assignments in multiphase flow, a systematic approach is necessary. First and foremost, it's critical to define the issue and establish the desired results. It is essential to identify the fluid phases, their characteristics, and the physical phenomena that need to be modelled. Next, choosing the best modelling strategy and validating it using experimental results or analytical solutions ensures that the model is accurate and appropriate for the given problem. A grid independence study can be carried out to choose the ideal mesh size for accurate results. The identification and correction of any issues can then be accomplished by setting up the simulation, specifying the solver parameters, and running the simulation while gradually refining the mesh. Following these guidelines will enable engineers and researchers to successfully complete challenging multiphase flow assignments and gain insightful knowledge into the behaviour of these complex systems. Here are some crucial actions to think about:
1. Problem Formulation and Boundary Conditions
The problem statement and the simulation's desired result should be clearly stated. Determine the physical phenomena to be modelled, as well as the fluid phases and their properties. Depending on the simulated system, specify the boundary conditions, such as the inlet velocities, pressures, and temperature distributions.
2. Model Selection and Validation
Based on the properties of the multiphase flow, choose the appropriate modelling strategy. Make sure the model you've chosen is accurate and appropriate for the particular issue at hand by validating it against experimental data or analytical solutions. To improve the model's agreement with the experimental data, adjust the model's parameters as necessary.
3. Meshing and Grid Independence Study
Create a suitable mesh with a manageable computational cost that captures the key flow features. Assess the sensitivity of the results to changes in mesh resolution by conducting a grid independence study. This step ensures reliable and consistent results and assists in determining the ideal mesh size.
4. Simulation Setup and Solver Settings
Configure the solver settings, assign suitable initial conditions, and set up the simulation domain. To obtain precise and consistent results, carefully consider the numerical scheme and convergence criteria. It is possible to identify any problems and guarantee a smooth convergence by running a preliminary simulation with coarse grids and progressively fine tuning them.
Conclusion
In conclusion, engineers and researchers face both challenges and opportunities when analysing multiphase flow using computational fluid dynamics. We gain a deeper understanding of the interactions between various fluid phases and their effects on various engineering processes by delving into the complexities of multiphase flow. We can take on challenging tasks in multiphase flow and gain important insights into system behaviour by utilising cutting-edge modelling methodologies and simulation tools. The difficulties involved, such as precise phase interaction modelling, interface tracking, and resource management, must be acknowledged. Despite these obstacles, developments in computing power and simulation methods continue to propel the field forward and allow us to more accurately and effectively tackle complex engineering problems. We discover new opportunities for improving industrial processes, developing cutting-edge systems, and ensuring the security and dependability of engineering applications as we investigate and improve our understanding of multiphase flow. A fascinating and developing field of study, multiphase flow has a lot of potential to advance and benefit many different industries in the future.