- Creating Ribs
- 1. Sketch the Profile:
- 2. Choose the Rib Tool:
- 3. Select the Sketch:
- 4. Define Rib Parameters:
- 5. Complete the Rib:
- 6. Adjust as Needed:
- Creating Patterns
- Linear Pattern:
- Circular Pattern:
- Sketch Driven Pattern:
- Curve Driven Pattern:
- Fill Pattern:
- Mirror Pattern:
- Applications of Patterns and Ribs in SolidWorks
- 1. Product Design:
- 2. Mold Design:
- 3. Aerospace Engineering:
- 4. Automotive Engineering:
- 5. Architectural Design:
- Conclusion
SolidWorks is a powerful and versatile 3D CAD (Computer-Aided Design) software used extensively in the engineering and design industries. It offers a wide range of tools and features to help users create complex and intricate designs with ease. In this blog, we will delve into two essential aspects of SolidWorks: creating ribs and patterns. These tools are indispensable for students and professionals alike, as they can significantly enhance your design capabilities. If you need assistance with your SolidWorks assignment, don't hesitate to reach out for help.
Creating Ribs
Creating ribs in SolidWorks is a crucial skill for anyone involved in 3D modeling, particularly in engineering and product design. Ribs are structural elements that play a pivotal role in enhancing the strength, rigidity, and durability of your 3D models. They are commonly employed in various applications, from consumer products like smartphones and household appliances to heavy-duty industrial machinery. SolidWorks simplifies the process of creating ribs, making it accessible to both beginners and experienced users. Let's take a closer look at the steps involved in creating ribs and why they are such an essential feature in the world of 3D modeling.
1. Sketch the Profile:
The first step in creating ribs in SolidWorks is to sketch the profile of the rib. This profile defines the shape and dimensions of the rib, and it acts as a blueprint for the rib's geometry. When creating this sketch, you have the flexibility to design ribs of various shapes, sizes, and configurations to meet the specific requirements of your project. Whether you need a thin, elongated rib for a delicate consumer product or a thicker, more robust rib for an industrial machine, SolidWorks allows you to sketch the perfect profile.
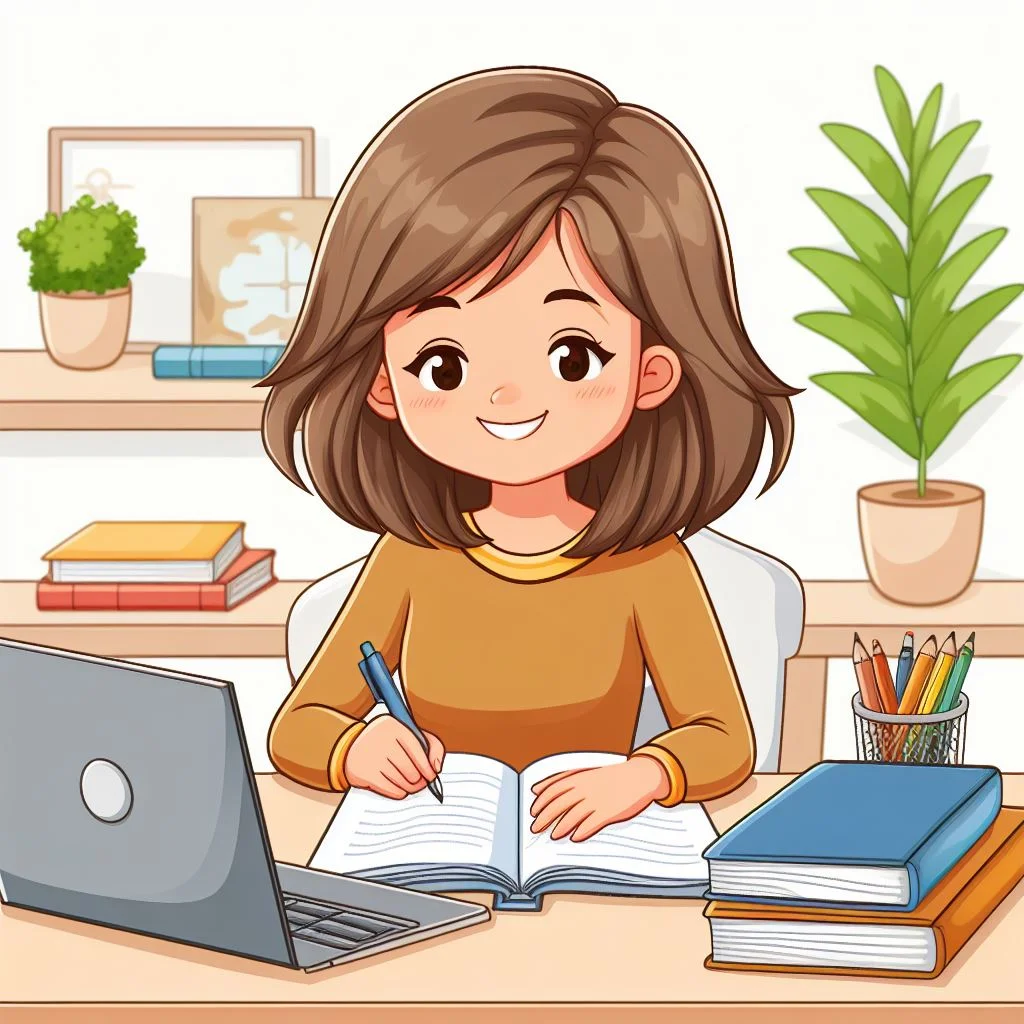
2. Choose the Rib Tool:
After sketching the rib profile, navigate to the "Features" tab in SolidWorks and select the "Rib" tool. This tool is the gateway to converting your 2D sketch into a 3D rib that integrates seamlessly into your model. It initiates the process of creating the rib, allowing you to define various parameters that will determine the rib's final appearance and function.
3. Select the Sketch:
With the "Rib" tool activated, the next step is to select the sketch you created in the first step. SolidWorks automatically recognizes this sketch as the profile for the rib, which means you don't need to perform any complex manual selections. This streamlined approach ensures that you're working with the correct sketch, preventing errors and saving you time during the modeling process.
4. Define Rib Parameters:
Once the sketch is selected, you can access the PropertyManager on the left side of the SolidWorks interface. Here, you have the opportunity to specify various parameters that define the rib's characteristics. These parameters include:
- Thickness:You can determine the thickness of the rib, allowing you to control its structural integrity. A thicker rib will provide more rigidity and strength, while a thinner rib may be used for decorative purposes or to save material.
- Draft:Draft is an angle applied to the rib's sides, making it easier to remove from a mold or casting. The draft angle can be adjusted to suit the manufacturing process or assembly requirements.
- Rib Start and End Constraints: You can specify where the rib starts and ends, which is particularly useful for designing complex geometries or ensuring that the rib aligns precisely with other components in your model.
5. Complete the Rib:
After defining the rib's parameters to your satisfaction, you can proceed by clicking the green checkmark in the PropertyManager. This action confirms your rib design, prompting SolidWorks to generate the rib according to the specified parameters. The software's robust modeling capabilities ensure that your rib seamlessly integrates with the existing model, adhering to the sketch's profile and any additional constraints you've set.
6. Adjust as Needed:
One of the significant advantages of working with SolidWorks is the flexibility it offers even after you've created a rib. If you find that you need to make adjustments to the rib's dimensions, draft angle, or any other parameters, you can easily do so. SolidWorks allows for intuitive and real-time modifications, enabling you to refine your design as you see fit. This adaptability is invaluable, especially in the iterative design process, where changes may be frequent.
Ribs are indispensable structural elements in 3D modeling, particularly in SolidWorks, and mastering their creation is vital for anyone working in design and engineering. They provide the strength and rigidity necessary for a wide range of applications, from everyday consumer products to heavy industrial machinery. The process of creating ribs in SolidWorks is both straightforward and flexible, allowing you to design and fine-tune your rib profiles to meet your project's unique requirements. This versatility, combined with the software's editing capabilities, empowers you to create robust and efficient 3D models that excel in terms of both aesthetics and functionality. So, whether you're a student or a professional, remember that ribs are the backbone of your designs, and SolidWorks is the tool that enables you to bring them to life with precision and ease.
Creating Patterns
Patterns are a fundamental part of parametric modeling in SolidWorks. They allow you to replicate features, sketches, or components in a systematic and efficient manner. SolidWorks offers several types of patterns, each serving different purposes.
Linear Pattern:
A linear pattern replicates features or components in a linear direction. Here's how to create one:
- Select Feature:Start by selecting the feature you want to pattern.
- Choose the Linear Pattern Tool:In the "Features" tab, click on the "Linear Pattern" tool.
- Define Direction:Specify the direction in which you want to create the pattern. You can choose an edge, sketch line, or any other reference.
- Set Spacing and Count:Determine the spacing between instances and the number of instances you want to create.
- Additional Options:You can choose to vary the instance parameters, like angle or size, if needed.
- Complete the Pattern:Click the green checkmark to generate the linear pattern.
Circular Pattern:
A circular pattern replicates features or components around a specified axis. Follow these steps to create one:
- Select Feature: Choose the feature you want to pattern.
- Use the Circular Pattern Tool:Go to the "Features" tab and select the "Circular Pattern" tool.
- Define Axis:Specify the axis around which you want to create the pattern.
- Set Spacing and Count:Determine the number of instances and the angle between them.
- Additional Options: You can choose to vary the instance parameters, like size or orientation, as required.
- Complete the Pattern:Click the green checkmark to create the circular pattern.
Sketch Driven Pattern:
A sketch-driven pattern allows you to create a pattern based on a 2D sketch. Here's how to do it:
- Select Feature: Start by selecting the feature you want to pattern.
- Choose Sketch-Driven Pattern:In the "Features" tab, click on the "Sketch-Driven Pattern" tool.
- Select Sketch: Pick the 2D sketch that will drive the pattern.
- Define Spacing and Count:Determine the number of instances and the spacing between them, which can be adjusted based on the sketch.
- Complete the Pattern:Click the green checkmark to generate the sketch-driven pattern.
Curve Driven Pattern:
A curve-driven pattern replicates features or components along a selected curve. Here's how to create one:
- Select Feature:Choose the feature you want to pattern.
- Use the Curve-Driven Pattern Tool:Go to the "Features" tab and select the "Curve-Driven Pattern" tool.
- Select Curve:Pick the curve along which you want to create the pattern.
- Set Spacing and Count:Determine the number of instances and the spacing along the curve.
- Additional Options: You can choose to vary the instance parameters, such as size or orientation.
- Complete the Pattern:Click the green checkmark to create the curve-driven pattern.
Fill Pattern:
A fill pattern replicates a feature or component across a selected area. Here's how to create one:
- Select Feature:Choose the feature you want to pattern.
- Use the Fill Pattern Tool:In the "Features" tab, click on the "Fill Pattern" tool.
- Select Area: Pick the area on the face or plane where you want to create the pattern.
- Set Spacing and Count: Determine the spacing and number of instances within the selected area.
- Complete the Pattern:Click the green checkmark to generate the fill pattern.
Mirror Pattern:
A mirror pattern creates a mirrored copy of a feature or component. Here's how to do it:
- Select Feature:Choose the feature you want to mirror.
- Use the Mirror Tool: In the "Features" tab, click on the "Mirror" tool.
- Select Face or Plane:Select the face or plane across which you want to mirror the feature.
- Complete the Pattern: Click the green checkmark to create the mirrored pattern.
Applications of Patterns and Ribs in SolidWorks
Now that you've learned how to create various patterns and ribs in SolidWorks, it's essential to understand their practical applications.
1. Product Design:
- Ribs are used to add strength and rigidity to products, ensuring they can withstand loads and stress.
- Patterns are used to replicate identical components or features, which is useful for creating symmetrical designs or assembling complex products.
2. Mold Design:
- Patterns help create the intricate geometries found in molds for manufacturing parts.
- Ribs can be used to enhance mold stability and increase its lifespan.
3. Aerospace Engineering:
- Patterns are crucial for designing complex components such as aircraft wings.
- Ribs provide structural support to aircraft components, ensuring they can handle various aerodynamic forces.
4. Automotive Engineering:
- Patterns are used to create uniform designs for components like tires and rims.
- Ribs are employed to add strength to vehicle frames and chassis.
5. Architectural Design:
- Patterns help architects create repetitive designs for building facades, windows, and interiors.
- Ribs can be used for structural elements in architectural designs.
Conclusion
SolidWorks provides a powerful set of tools for creating patterns and ribs, enabling you to design complex and sophisticated 3D models with ease. Whether you're a student learning the ropes of CAD design or a professional looking to streamline your workflow, mastering these features is essential.
By understanding the different types of patterns and how to create them, you can save time and improve the efficiency of your design process. Moreover, utilizing ribs to reinforce and stabilize your models ensures that your designs are not only aesthetically pleasing but also structurally sound.
Remember, practice makes perfect. The more you explore and experiment with patterns and ribs in SolidWorks, the better you'll become at leveraging these tools for your design projects. So, keep designing, keep creating, and keep pushing the boundaries of what's possible with SolidWorks.