- Understanding Sheet Metal Basics
- Material Selection and Thickness
- Bend Radius and K-Factor
- Sheet Metal Features in Solidworks
- Utilizing Solidworks Sheet Metal Tools
- Design Intent and Sketching Techniques
- Sheet Metal Parameters and Rules
- Bend Tables and Gauge Tables
- Best Practices for Sheet Metal Assignments
- Design for Manufacturability
- Sheet Metal Simulation and Validation
- Documenting Sheet Metal Designs
- Conclusion
Understanding Sheet Metal Basics
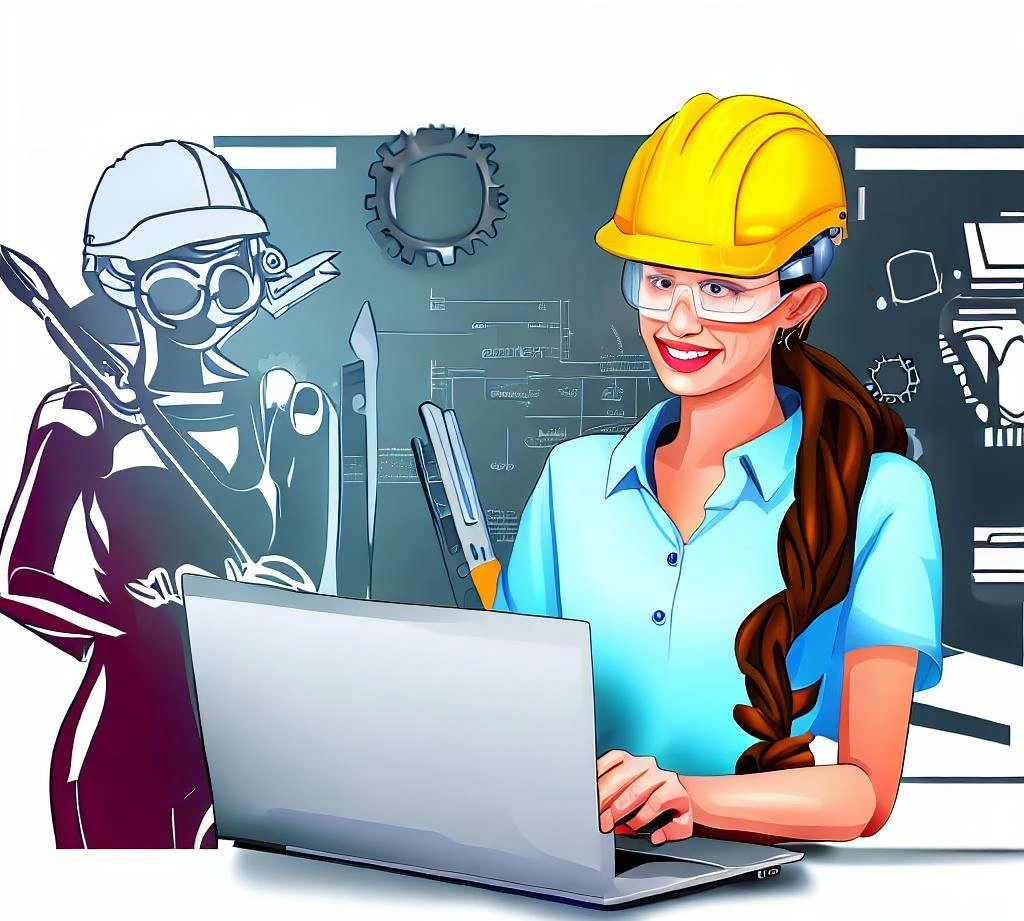
It's crucial to understand the foundational ideas of sheet metal design before delving into the specifics of Solidworks. The thickness, bend radius, and flat pattern of sheet metal parts serve as distinguishing factors. Learn the terms for flanges, tabs, and bends since these are the fundamental elements of sheet metal design. Understanding sheet metal thickness is essential because it affects the part's strength and flexibility. Contrarily, the bend radius establishes the curvature of the bends and affects the part's overall shape. Last but not least, the flat pattern shows how the unfolded sheet metal part will appear in 2D. Understanding how the flat pattern is created and how it relates to the finished bent shape is crucial. You will be better able to use Solidworks' capabilities and produce precise and effective sheet metal designs if you have a firm grasp of these fundamental ideas.
Material Selection and Thickness
The selection of sheet metal is an important step in the design and manufacturing processes. Think about things like strength, corrosion resistance, and cost when choosing the material. Each material has distinct qualities that can affect how well your sheet metal part performs. Also, pay close attention to the thickness of the sheet metal. The thickness affects the part's manufacturability as well as its strength. While thicker materials offer greater strength but may be more difficult to bend and form, thinner materials are more flexible but may need additional support or reinforcement. For your sheet metal design to have the desired functionality and manufacturing potential, finding the ideal balance between material choice and thickness is crucial.
Bend Radius and K-Factor
For precise sheet metal design, knowledge of the bend radius and K-factor concepts is essential. The tightness of a bend is determined by the bend radius, which also has an impact on the part's overall shape and appearance. To make sure that the bend radius matches your design requirements, it is crucial to give it careful thought. The ratio of the neutral axis to the material thickness is represented by the K-factor, on the other hand. It is used to determine the bend allowance and takes the behavior of the material during bending into account. With the help of the tools provided by Solidworks, bend allowances can be calculated based on the bend radius and K-factor, enabling accurate flat patterns and precise modeling. You can achieve precise bend locations and reduce the possibility of deformation in your sheet metal design by precisely defining the bend radius and applying the proper K-factor.
Sheet Metal Features in Solidworks
A number of sheet metal features available in Solidworks are made with streamlining sheet metal design and fabrication in mind. To make the most of the software's capabilities, become familiar with these features. Some of the most important features in Solidworks include bend reliefs, base flanges, edge flanges, and miter flanges. In the design and fabrication of sheet metal, each feature has a specific function. Edge flanges are used to add flanges along the edges while base flanges are used to shape the sheet metal part initially. Bend reliefs and miter flanges can be used to make angled bends and reduce stress concentrations. Try out these features to get a full understanding of their capabilities and restrictions. You can efficiently create complex and precise sheet metal designs by utilizing Solidworks' sheet metal features.
Utilizing Solidworks Sheet Metal Tools
To simplify sheet metal design, Solidworks provides a number of specialized tools and features. Users of these tools can complete sheet metal assignments with greater efficiency and accuracy, regardless of their level of design expertise. Users can create complex and accurate sheet metal parts with ease thanks to Solidworks' specialized sheet metal capabilities. Base flanges, edge flanges, miter flanges, bend reliefs, and other sheet metal features are available in the software's extensive library, making it simple to create and alter sheet metal components to meet project requirements. Furthermore, the capability of Solidworks to compute bend allowances based on the bend radius and K-factor ensures precise bend locations and reduces the possibility of deformations during the manufacturing process. Solidworks users can streamline their sheet metal design workflows and produce high-quality results quickly by utilizing these specialized tools and features.
Design Intent and Sketching Techniques
Before creating sheet metal parts in Solidworks, it is essential to establish a clear design intent. Structure your model to account for any potential alterations that may be necessary during the design process. Use sketching strategies like fully defining sketches to make sure that your geometry is stable and simple to edit. To precisely define the shape and dimensions of your sheet metal parts, use construction lines and geometric relationships. Additionally, use symmetry to your advantage to streamline the design process and guarantee uniform, balanced models. You can create sheet metal designs that are adaptable, versatile, and simple to change by paying attention to the design intent and using efficient sketching techniques.
Sheet Metal Parameters and Rules
A variety of parameters and rules created especially for sheet metal design are available in Solidworks. Utilize these features to tailor your designs and fit them to your manufacturing needs and design limitations. To automate the design process and cut down on errors, define defaults for sheet metal thickness, corner reliefs, and bend allowances. You can ensure consistency among your sheet metal designs and improve workflow by establishing these limits and guidelines. Iterations and changes can be made quickly by adjusting the parameters as necessary, which ultimately reduces time spent and raises the caliber of the final design.
Bend Tables and Gauge Tables
To improve the effectiveness of your sheet metal design process, Solidworks provides the convenience of bend tables and gauge tables. Based on the material thickness and bend radius, bend tables specify the bend allowances and bend deductions. You can automatically determine the precise dimensions needed for precise bending by using bend tables. Contrarily, gauge tables offer a library of common sheet metal thicknesses, making it simpler to choose the right thickness for your design. By including these tables in your design process, you can expedite the process and guarantee consistency in all of your sheet metal designs. You can speed up the design process, do away with manual calculations, and increase the accuracy of your sheet metal parts by utilizing bend tables and gauge tables.
Best Practices for Sheet Metal Assignments
Along with mastering Solidworks' tools and features, there are a few best practices that can boost your output and the caliber of your sheet metal assignments. It is crucial to design with manufacturability in mind first and foremost. To ensure efficient manufacturing procedures and affordable production, take into account variables like material availability, standard tooling sizes, and fabrication techniques during the design phase. Solidworks' sheet metal simulation and validation tools can also be very helpful for your designs. You can identify and fix design flaws early on and save time and resources by using simulations to analyze stress distribution, deformation, and manufacturability. Finally, thorough documentation is essential for finishing sheet metal projects successfully. To provide clear manufacturing instructions, create detailed drawings with flat patterns, bend lines, hole locations, and annotations. By adhering to these best practices, you can use Solidworks to streamline your workflow, increase the precision of your designs, and produce excellent results for your sheet metal assignments.
Design for Manufacturability
When working on sheet metal projects in Solidworks, it's crucial to take manufacturing into account from the beginning of your design. Consider elements like the availability of materials, typical tool sizes, and fabrication methods. By keeping manufacturability in mind when designing, you can ensure that your creations can be manufactured effectively, which lowers production costs and boosts overall manufacturing productivity. You can optimize your designs for seamless production and achieve cost-effective manufacturing outcomes by taking these factors into account during the design phase.
Sheet Metal Simulation and Validation
You can validate your sheet metal designs using Solidworks' potent simulation tools before going into production. Analyse elements like stress distribution, deformation, and manufacturability using these simulation tools. You can find potential design flaws early in the process by using simulations, which will save a lot of time and resources. You can use simulation to make sure your designs can withstand the anticipated loads and work as intended. It also enables you to determine whether your designs are capable of being manufactured, highlighting any potential problems that might occur during the fabrication process. Your sheet metal designs can be made more reliable and high-quality by utilizing Solidworks' simulation features.
Documenting Sheet Metal Designs
Successful sheet metal part fabrication depends on accurate and thorough documentation. Make thorough drawings with flat patterns, bend lines, hole locations, and annotations. Drawings that are accurately dimensioned and annotated provide clear manufacturing instructions, ensuring that your designs are faithfully translated into physical components. Effective documentation of your sheet metal designs lowers the possibility of misunderstandings and mistakes during the manufacturing process. Additionally, it makes it easier for designers, engineers, and fabricators to communicate with one another and stay on the same page. You enable effective and seamless production by providing thorough documentation, which produces high-quality sheet metal parts that adhere to the necessary specifications.
Conclusion
In conclusion, you can significantly improve your capacity to efficiently complete sheet metal assignments by comprehending the fundamentals of sheet metal design, utilizing Solidworks' sheet metal tools, and adhering to best practices. Solidworks provides a flexible platform with features tailored specifically for sheet metal design, allowing you to produce reliable and precise designs. Throughout the design process, it's crucial to take manufacturability into account to make sure that your creations can be produced effectively. You can find and fix potential problems before production by simulating and validating your designs using Solidworks' simulation tools, which will help you save time and resources. Furthermore, thorough documentation that includes specific drawings guarantees effective communication and smooth production. You will be well-prepared to handle sheet metal projects using Solidworks by adopting these suggestions, maximizing your productivity, and obtaining high-quality results. Utilize Solidworks' powerful sheet metal features to explore your creative potential in the field of sheet metal design.