- Parametric Modeling for Precision
- Advanced Flattening Strategies
- Utilizing Design Tables for Efficiency
- Incorporating Simulation for Robust Designs
- Mastering Multi-Body Sheet Metal Parts
- Conclusion
SolidWorks, a cornerstone in 3D CAD design, stands out for its remarkable capabilities in sheet metal design. As engineers and designers navigate the intricacies of their craft, the quest for advanced techniques becomes paramount in elevating proficiency within the SolidWorks ecosystem. If you require assistance with your Sheet Metal assignment, mastering these advanced techniques can significantly enhance your skills and productivity within SolidWorks.
In the dynamic landscape of sheet metal design, SolidWorks continues to be a reliable ally, offering a multifaceted toolkit that caters to the ever-evolving demands of the industry. As technology progresses, the need for precision and innovation intensifies, prompting professionals to explore cutting-edge techniques that transcend conventional boundaries.
One pivotal aspect of SolidWorks sheet metal design is the realm of parametric modeling. This sophisticated technique empowers designers with unparalleled control over dimensions and relationships, ensuring a level of precision that is indispensable in intricate designs. The ability to create intelligent and adaptable sheet metal models that dynamically respond to changes not only enhances efficiency but also fosters an environment of accuracy and reliability.
A crucial component of sheet metal design lies in the creation of flat patterns for manufacturing. Advanced flattening strategies in SolidWorks unravel complexities associated with bends, ensuring that flat patterns accurately represent the intended design. Engineers delve into techniques that handle complex bends and irregular geometries with finesse, acknowledging that the accuracy of flat patterns is pivotal in the manufacturing process.
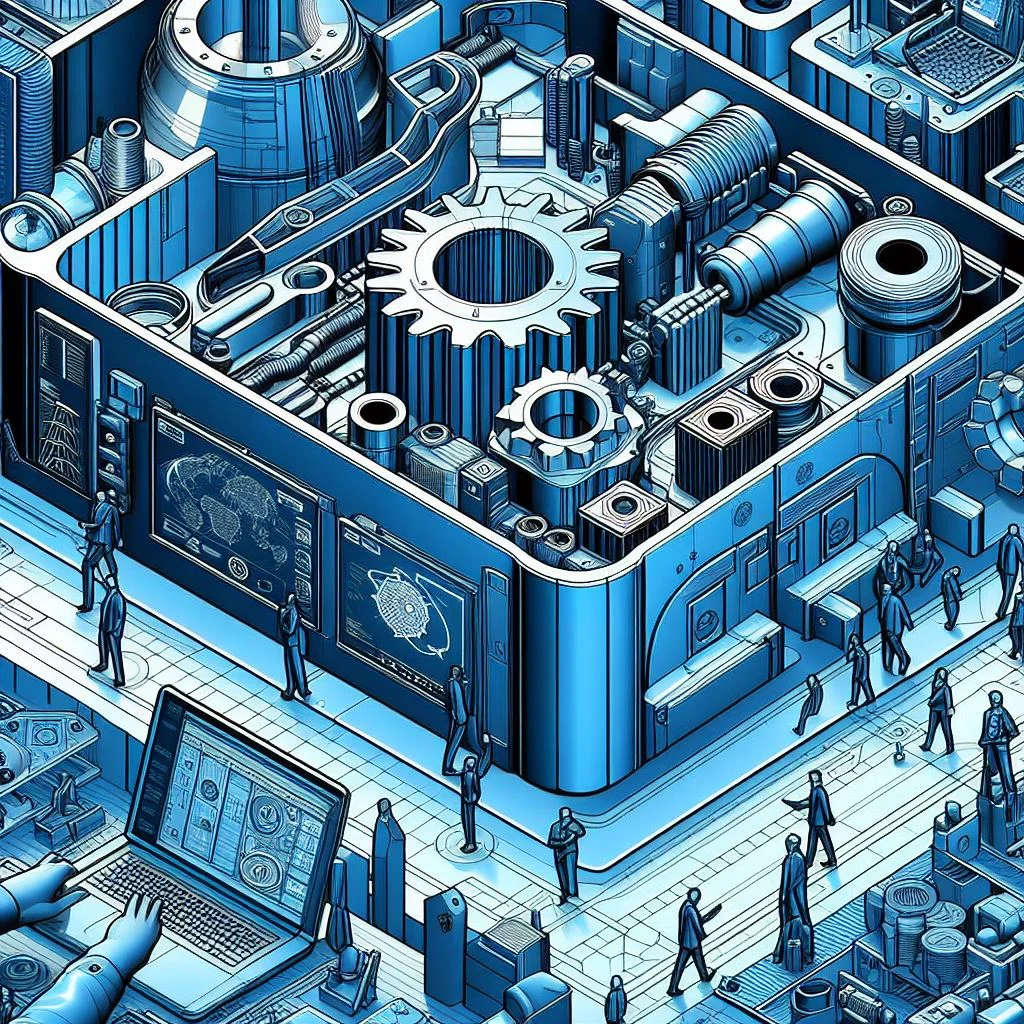
Design tables emerge as a game-changer for those seeking efficiency in SolidWorks sheet metal design. These tables allow designers to create multiple configurations, providing a systematic approach to exploring various design options. The optimization of material usage and streamlining of the design process become more accessible through the strategic implementation of design tables, marking a paradigm shift in the way designers approach their craft.
Simulation tools embedded within SolidWorks play a pivotal role in achieving robust and reliable sheet metal designs. Engineers delve into the nuances of simulation, predicting and mitigating potential issues such as deformations and stresses. By incorporating simulation early in the design process, professionals ensure that the final product not only meets but exceeds performance expectations, laying the foundation for successful manufacturing.
Multi-body sheet metal parts add another layer of complexity to the SolidWorks repertoire. Engineers master the art of creating and managing multiple bodies within a single part file, a technique that proves invaluable in handling intricate assemblies seamlessly. This proficiency in managing complex assemblies further solidifies SolidWorks as a comprehensive solution for sheet metal design challenges. With multi-body capabilities, designers gain the flexibility to create sophisticated components within a unified environment, allowing for efficient collaboration and easy modifications. This feature is particularly beneficial when dealing with assemblies requiring intricate interlocking or overlapping sheet metal parts, providing designers with unparalleled control over the entire design process. As SolidWorks continues to evolve, mastering multi-body sheet metal parts becomes an essential skill, empowering engineers to navigate the intricate landscape of sheet metal design with confidence and precision.
Parametric Modeling for Precision
Parametric modeling stands as a cornerstone in the realm of SolidWorks for sheet metal design, offering designers unparalleled control over their creations. In this sophisticated technique, the intricate dance of dimensions and relationships is orchestrated with precision, enabling a profound level of customization. Imagine a world where your sheet metal models are not static entities but intelligent, adaptive structures that seamlessly respond to changes in real-time.
At the heart of parametric design lies the ability to manipulate and refine dimensions effortlessly. SolidWorks empowers designers to create models with dynamic relationships, ensuring that alterations to one aspect of the design automatically trigger adjustments in related components. This not only expedites the design process but also guarantees a level of accuracy that is paramount in sheet metal fabrication.
The dynamic nature of parametric modeling proves particularly beneficial in scenarios where design changes are frequent or inevitable. With a few clicks, designers can modify dimensions, alter angles, or redefine relationships between features, and witness the entire model adapt instantaneously. This real-time responsiveness not only saves valuable time but also reduces the likelihood of errors, fostering a design environment that prioritizes precision and efficiency.
Furthermore, parametric modeling facilitates the creation of intelligent sheet metal designs that can be easily modified for various use cases. Whether it's tweaking dimensions for different material thicknesses or adapting a design to meet specific manufacturing constraints, the versatility inherent in parametric modeling allows designers to explore multiple iterations effortlessly.
In essence, delving into the world of parametric modeling within SolidWorks unveils a realm of design possibilities where precision and adaptability coalesce. This technique not only elevates the efficiency of sheet metal design but also empowers designers to push the boundaries of creativity, knowing that their models can seamlessly evolve with their vision. SolidWorks, with its robust parametric capabilities, becomes not just a tool but a partner in the journey towards creating sheet metal masterpieces.
Advanced Flattening Strategies
In the realm of sheet metal design within SolidWorks, the pursuit of advanced flattening strategies is a crucial aspect that can significantly impact the manufacturing process. Beyond the basics, it's essential to delve into more intricate techniques to ensure the accuracy of flat patterns, especially when dealing with complex designs.
One key facet of advanced flattening involves tackling complex bends. SolidWorks provides tools and features that empower designers to handle intricate bends with precision. By understanding the nuances of the software, designers can navigate through the challenges posed by bends in multiple directions, ensuring that the final flat pattern reflects the intended design accurately. This capability not only streamlines the design process but also contributes to a more efficient manufacturing workflow.
Moreover, the ability to execute multiple bends within a single feature is another advanced strategy that can greatly enhance the versatility of sheet metal designs. SolidWorks allows for the creation of complex features with multiple bends, providing designers with the flexibility to craft intricate geometries. This technique proves invaluable when dealing with designs that demand a seamless integration of various bending angles within a single component.
Addressing irregular geometries is yet another dimension of advanced flattening strategies. In the real-world application of sheet metal, designs often involve irregular shapes and contours. SolidWorks equips designers with the tools to finesse these irregularities, ensuring that the flat patterns generated accurately represent the intended design. This feature becomes especially crucial in industries where precision is paramount, such as aerospace or automotive manufacturing.
In essence, mastering advanced flattening strategies in SolidWorks goes beyond the basics, enabling designers to navigate the complexities of sheet metal design with finesse. Whether it's conquering complex bends, incorporating multiple bends within a single feature, or addressing irregular geometries, these advanced techniques empower designers to elevate their sheet metal designs to new heights of precision and functionality.
Utilizing Design Tables for Efficiency
Efficiency is key in the world of design, and SolidWorks provides a powerful tool in the form of design tables for sheet metal design. Design tables offer a robust solution to streamline the design process, enabling designers to achieve optimal efficiency in their workflow. By harnessing the power of design tables, users can go beyond traditional approaches, exploring multiple configurations seamlessly.
The versatility of design tables allows designers to create a range of configurations within a single SolidWorks model. This flexibility proves invaluable when experimenting with various design options. Designers can efficiently manipulate parameters, instantly generating different iterations of the sheet metal design. This not only facilitates the exploration of creative possibilities but also enhances the ability to fine-tune designs for specific requirements.
Optimizing material usage is a crucial aspect of sheet metal design, and design tables play a pivotal role in achieving this goal. By configuring different material thicknesses, bend allowances, and other parameters within the design table, designers can assess the impact on material utilization. This iterative process ensures that the final design not only meets performance criteria but also minimizes material wastage, contributing to cost-effectiveness in manufacturing.
Moreover, design tables contribute to the standardization of designs across projects. Designers can create templates with predefined parameters, ensuring consistency in design elements and facilitating a standardized approach. This proves particularly beneficial in industries where adherence to specific standards and regulations is imperative.
In summary, the use of design tables in SolidWorks for sheet metal design goes beyond mere efficiency; it is a catalyst for innovation, optimization, and standardization. By mastering this tool, designers can elevate their capabilities, seamlessly navigating the intricate landscape of sheet metal design with precision and creativity.
Incorporating Simulation for Robust Designs
Achieve robust and reliable sheet metal designs by incorporating simulation tools within SolidWorks. Delve into the capabilities of simulation for sheet metal parts, understanding how it aids in predicting and mitigating issues such as deformations, stresses, and potential manufacturing challenges.
Simulation tools play a pivotal role in enhancing the overall robustness of sheet metal designs. By subjecting the virtual models to simulated conditions, engineers gain valuable insights into the performance of the designs under various scenarios. This process allows for the identification and mitigation of potential issues before the actual manufacturing phase, saving both time and resources.
In the realm of sheet metal design, predicting and addressing deformations is paramount. Simulation in SolidWorks empowers designers to visualize and analyze how sheet metal parts respond to forces and thermal conditions. By accurately simulating real-world conditions, engineers can tweak designs to minimize deformations, ensuring the final product meets the desired specifications.
Moreover, the simulation aids in assessing the impact of stresses on sheet metal components. Identifying stress concentrations and weak points in the design enables proactive adjustments, leading to more durable and reliable sheet metal structures. This not only ensures the longevity of the final product but also reduces the likelihood of unexpected failures during operation.
Simulation tools also prove invaluable in addressing potential manufacturing challenges. By simulating the fabrication process, engineers can anticipate issues such as material thinning, wrinkling, or other deformations that may arise during production. This foresight allows for preemptive adjustments to the design, resulting in a more manufacturable and cost-effective sheet metal component.
In essence, incorporating simulation into SolidWorks for sheet metal design is a proactive approach that significantly contributes to achieving robust and reliable outcomes. By leveraging these advanced tools, designers can optimize their designs, minimize potential pitfalls, and deliver sheet metal components that meet the highest standards of quality and performance.
Mastering Multi-Body Sheet Metal Parts
Sheet metal designs frequently demand intricate assemblies, presenting a unique set of challenges for designers. In SolidWorks, mastering the creation of multi-body sheet metal parts is a crucial skill that significantly enhances your capability to manage complexity seamlessly. This advanced technique involves understanding how to manipulate and coordinate multiple bodies within a single part file.
When working on complex sheet metal assemblies, the ability to create and manage multiple bodies within a single part file becomes invaluable. SolidWorks provides a robust environment for executing this technique, allowing designers to effectively handle intricate structures and configurations. By employing this approach, you gain the flexibility to model and modify various components independently, optimizing the design process and ensuring a more efficient workflow.
This proficiency in managing multi-body sheet metal parts goes beyond the design phase, offering advantages throughout the entire manufacturing process. It facilitates a streamlined manufacturing process by providing a clear representation of the assembly and how individual components interact. This not only enhances collaboration among team members but also contributes to better communication with manufacturers, reducing the likelihood of errors during the production stage.
Moreover, the strategic use of multi-body techniques enhances the overall design flexibility. Designers can explore multiple iterations and variations without compromising the integrity of the entire assembly. This iterative approach allows for quick and effective design changes, fostering innovation and adaptability in response to evolving project requirements.
In essence, mastering multi-body sheet metal parts in SolidWorks empowers designers to navigate the intricacies of complex assemblies seamlessly. It's a skill set that not only improves the design process but also streamlines collaboration, communication with manufacturers, and overall efficiency in bringing sheet metal designs from concept to reality.
Conclusion
In conclusion, delving into the advanced techniques of SolidWorks for sheet metal design unveils a world of unparalleled precision and efficiency. Parametric modeling emerges as the cornerstone, offering designers the ability to create intelligent and adaptable sheet metal models. The parametric approach not only ensures accuracy but also provides the flexibility to make swift adjustments as design requirements evolve. This technique, when mastered, becomes a powerful tool for designers seeking the utmost control over their sheet metal creations.
Moving on to advanced flattening strategies, the importance of creating accurate flat patterns cannot be overstated. SolidWorks empowers designers to navigate the complexities of sheet metal design by offering sophisticated solutions for handling intricate bends, multiple bends in a single feature, and irregular geometries. The ability to generate precise flat patterns is a crucial step towards seamless manufacturing processes, minimizing errors and optimizing material usage.
Design tables emerge as another pivotal feature, ushering in an era of efficiency and versatility. The capability to create multiple configurations within a single design table allows designers to explore various possibilities without the need for extensive manual adjustments. This not only expedites the design process but also enhances creativity, enabling designers to experiment with different iterations effortlessly.
Simulation becomes a game-changer in ensuring the robustness of sheet metal designs. By incorporating simulation tools, designers can anticipate and address potential issues such as deformations and stresses, paving the way for more reliable and manufacturable designs. This proactive approach not only saves time but also contributes to the overall quality and durability of the final product.
The mastery of multi-body sheet metal parts further amplifies SolidWorks' capabilities. Handling complex assemblies with finesse becomes possible, streamlining the design process and facilitating collaboration among team members. The ability to manage and manipulate multiple bodies within a single part file opens up new possibilities for creating intricate and interconnected sheet metal designs.
In essence, the journey through advanced SolidWorks techniques for sheet metal design is a transformative experience for designers and engineers alike. It empowers them to transcend conventional boundaries, fostering innovation and efficiency in every step of the design process. Whether it's through parametric modeling, advanced flattening strategies, design tables, simulation, or multi-body parts, SolidWorks provides a comprehensive toolkit for those seeking excellence in sheet metal design.
As we conclude this exploration, it's evident that the synergy between SolidWorks and advanced sheet metal design techniques offers a pathway to precision, efficiency, and creativity. Embracing these techniques not only enhances individual proficiency but also contributes to the evolution of the entire design industry, setting new standards for excellence in sheet metal design.