- Design Optimization
- Design for Manufacturability (DFM)
- Material Selection and Thickness Optimization
- Design Reuse and Automation
- Production Optimization
- Nesting and Material Utilization
- Integration with Manufacturing Equipment
- Collaboration and Documentation
- Design Review and Collaboration
- Documentation and BOM Generation
- Conclusion
With its cutting-edge features and capabilities, Solidworks, a potent software tool, has revolutionized the sheet metal design and production industry. Engineers and designers can create effective and optimized sheet metal designs with the help of this ground-breaking software, which boosts productivity and results in significant cost savings. In the context of this blog post, we will explore a variety of methods and approaches aimed at maximizing effectiveness in sheet metal projects by utilizing Solidworks' features. Professionals in the field can take advantage of a vast array of tools and functionalities provided by Solidworks to streamline their design processes, reduce material waste, and ultimately increase productivity and cost-efficiency. Join us as we examine the enormous potential that Solidworks offers in the field of sheet metal design and production. You'll learn how its cutting-edge features can completely change the way you approach these tasks and produce results that are incredibly efficient and effective.
Design Optimization
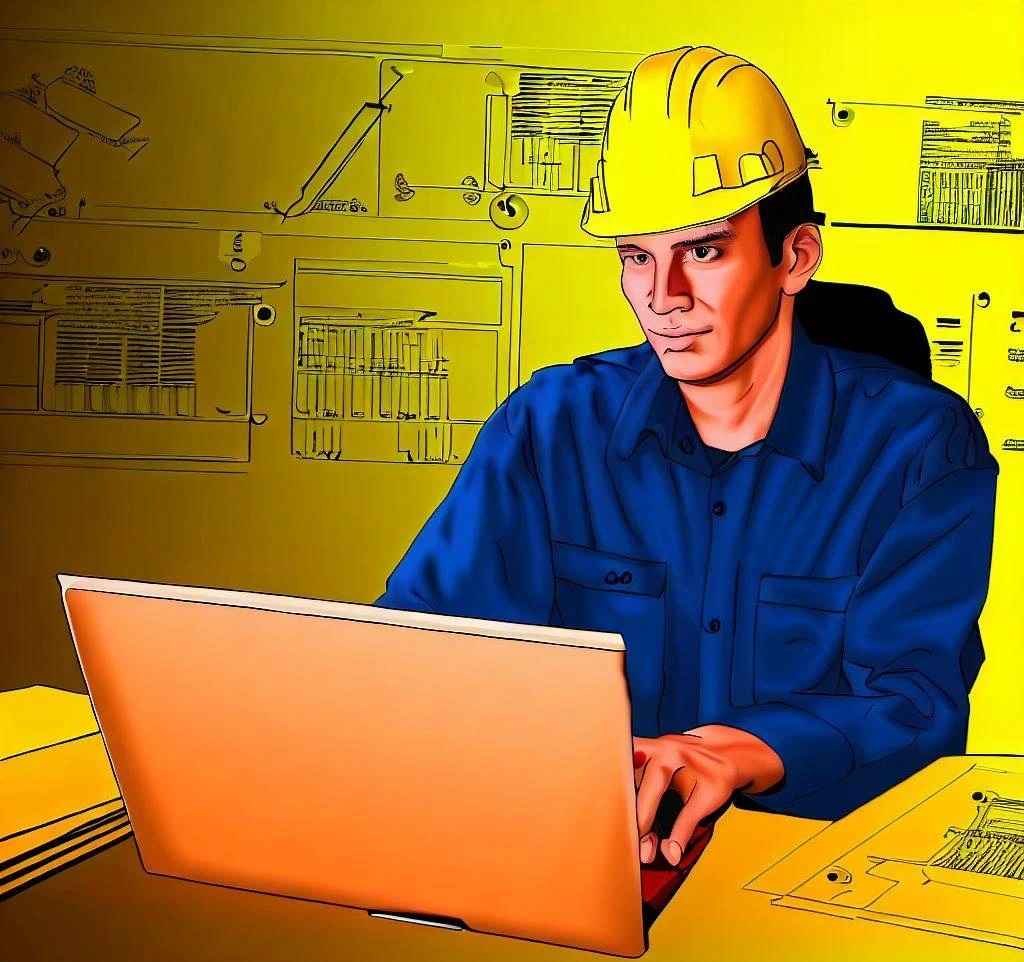
The effectiveness of sheet metal assignments can be significantly increased through design optimization, and Solidworks offers the features and tools required to do so. Solidworks' powerful design tools can be used by engineers to produce optimized designs that not only meet all functional requirements but also cut down on material consumption and production costs. Engineers can evaluate the performance of their designs under various loading conditions and pinpoint areas for improvement by utilizing Solidworks' advanced features, such as virtual testing and simulation. They can then improve their designs and make well-informed decisions to get the best results. Engineers can assess different material options and determine the ideal thickness that balances performance, weight, and cost using Solidworks' functionalities for material selection and thickness optimization. Engineers can maximize the effectiveness of their sheet metal projects through design optimization using Solidworks, which will improve product quality, lower costs, and boost customer satisfaction.
Design for Manufacturability (DFM)
Design for Manufacturability, or DFM, is a crucial idea in designing sheet metal. It entails creating components and assemblies that are simple to produce, put together, and maintain. Solidworks offers a variety of DFM-supporting tools, including the capacity to conduct interference checks, examine manufacturability, and assess assembly workflows. Engineers can minimize manufacturing errors and shorten production times by incorporating DFM principles into the design process. A smooth manufacturing process is ensured by Solidworks' interference checks, which help find potential conflicts or collisions between components. The software's manufacturability analysis feature evaluates the design's viability by taking into account things like material constraints and manufacturing potential. Engineers can also assess assembly sequences using Solidworks, ensuring logical and effective assembly procedures. Engineers who use Solidworks can optimize their designs for ease of manufacturing by concentrating on DFM, which boosts productivity and lowers costs.
Material Selection and Thickness Optimization
Efficiency can be significantly impacted by selecting the proper material and optimizing the thickness of sheet metal components. Engineers can evaluate various material options and simulate how a design will perform under various loading scenarios using Solidworks. Designers can choose the best material and thickness to meet design requirements while reducing weight and cost by running virtual tests and simulations. Engineers can examine how various materials respond to various stresses thanks to Solidworks' simulation capabilities, ensuring the selection of materials with the right mechanical properties. The simulation tools in the software also assist in optimizing sheet metal component thickness and balancing structural integrity and material usage. Engineers can improve efficiency in sheet metal assignments by utilizing the best materials and minimizing unnecessary material consumption by utilizing Solidworks' material selection and thickness optimization features.
Design Reuse and Automation
The robust automation and reuse tools provided by Solidworks significantly increase the effectiveness of sheet metal projects. Engineers can quickly produce new designs based on tested solutions by building a library of standard components, templates, and design rules. Engineers can store frequently used components in Solidworks' design library, ensuring standardized and effective design procedures. Additionally, the software supports automation through the use of macros and design tables, enabling the automation of repetitive tasks and reducing errors while also saving time. Engineers can record and replay a series of commands using macros in Solidworks to automate repetitive design tasks. Design tables make it possible to control designs parametrically, making it easier to create variations based on predefined rules. Engineers can improve their workflows, cut down on design time, and maintain uniform design standards by utilizing Solidworks' design reuse and automation features. This will ultimately increase the efficiency of sheet metal assignments.
Production Optimization
Beyond design optimization, efficiency in sheet metal assignments goes beyond. To increase productivity and reduce costs, the production process must be streamlined. Numerous features in Solidworks make it easier to optimize production. Manufacturers can significantly increase productivity and cost-effectiveness with Solidworks. In order to maximize material utilization and minimize waste, manufacturers can arrange sheet metal components on larger sheets using the software's tools for efficient nesting. This lowers material costs and minimizes waste. Additionally, Solidworks integrates seamlessly with a variety of manufacturing tools, including laser cutters, CNC machines, and press brakes, allowing for direct communication and more efficient production. This integration reduces programming time and removes manual errors, improving overall productivity. Utilizing Solidworks' production optimization features, manufacturers can streamline their operations, boost productivity, and cut costs, ultimately enhancing their competitiveness in the sheet metal sector.
Nesting and Material Utilization
In sheet metal assignments, nesting is a crucial component of maximizing material utilization. In order to minimize waste and lower material costs, entails positioning sheet metal components on a larger sheet in the most effective way conceivable. Nesting tools from Solidworks make it easy to create the best possible part layout. These tools consider elements like material size, shape, and orientation as they analyze the geometry of the parts to determine the best arrangement for saving space. Utilizing Solidworks' nesting features, manufacturers can significantly reduce their material usage, which lowers costs and boosts productivity. By maximizing material utilization, the software improves sustainability initiatives and makes sure that resources are used efficiently during production.
Integration with Manufacturing Equipment
Press brakes, CNC machines, and other manufacturing tools used frequently in the sheet metal industry are all seamlessly integrated with Solidworks. Direct communication between Solidworks and the machinery is made possible by this integration, which speeds up the manufacturing process. Solidworks ensures accurate and effective production by removing the need for manual data translation and transfer. By directly generating machine-specific code from their Solidworks designs, engineers can cut down on programming time and do away with the possibility of data transfer errors. Engineers can validate their designs and make necessary adjustments thanks to the real-time feedback provided by the manufacturing equipment thanks to this seamless integration. Solidworks' integration with manufacturing machinery enables manufacturers to enhance production, reduce downtime, and achieve higher standards of accuracy and efficiency.
Collaboration and Documentation
Successful sheet metal projects require effective collaboration and documentation, and Solidworks offers robust tools to support these processes. With the help of features like markups, comments, and version control, engineers and designers can easily collaborate, perform design reviews, and make changes in real-time. This collaborative setting fosters efficient decision-making, encourages effective communication, and minimizes design iterations. Additionally, Solidworks makes it easier to create precise and thorough documentation, such as assembly instructions, detailed drawings, and bills of materials (BOMs). Solidworks ensures that the manufacturing team has all the information required to produce the sheet metal components effectively by automating the documentation process, which also reduces manual errors and saves time. With the collaboration and documentation tools provided by Solidworks, professionals can improve productivity, streamline workflows, and complete their sheet metal assignments successfully.
Design Review and Collaboration
Engineers can conduct design reviews and work in real-time collaboration with team members using Solidworks. Multiple stakeholders can offer feedback, make suggestions, and decide on the design by using features like markups, comments, and version control. This collaborative setting improves communication and quickens the design cycle, cutting down on design iterations and ensuring effective development. Engineers can easily highlight problematic areas and add specific instructions by annotating and marking up the design. All team members always work with the most recent design iteration thanks to the ability to track versions and changes, which prevents confusion and inconsistencies. The design review and collaboration features of Solidworks facilitate productive teamwork, speed up the decision-making process, and ultimately result in sheet metal assignments that are more effective.
Documentation and BOM Generation
Solidworks makes it easier to create precise and thorough documentation, such as assembly instructions, detailed drawings, and bills of materials (BOMs). Engineers can quickly produce intricate drawings with Solidworks that include all the details required for manufacturing and assembly. By automatically creating dimensions, annotations, and part callouts, the software ensures accuracy and coherence across all of the documentation. It is possible to design and visualize assembly instructions that will lead the manufacturing team step-by-step through the assembly procedure. Furthermore, Solidworks makes it easier to create bills of materials (BOMs), which include a list of all the parts needed for the sheet metal assignment. Solidworks ensures the manufacturing team has access to all necessary information, eliminates manual errors, and saves time by automating the documentation process. By providing clear instructions and reducing the possibility of misinterpretation or missing information during the production of sheet metal components, this thorough documentation increases efficiency.
Conclusion
In conclusion, Solidworks demonstrates its value as a powerful tool for streamlining sheet metal design and production. Engineers are given the tools they need by its sophisticated features to increase design effectiveness, reduce material usage, sped up production procedures, and improve communication and documentation. Professionals in the sheet metal industry can significantly increase productivity, cut costs, and boost efficiency by utilizing Solidworks' capabilities. Engineers can create optimized sheet metal designs that meet functional requirements while minimizing material waste and production costs with the help of Solidworks' extensive set of tools and functionalities. The software's collaboration and documentation tools promote efficient teamwork and make it easier to create precise and thorough documentation. Solidworks genuinely transforms how sheet metal projects are approached, empowering professionals to produce extraordinary results and establish themselves as industry leaders.