- Understanding the Assignment Requirements
- Initial CAD Modeling
- Performing Finite Element Method (FEM) Analysis
- Evaluating Performance Metrics
- Iterative Design Refinement
- Conclusion and Recommendations
- Tips for Success in Solidworks Assignments
- Conclusion
Solidworks assignments represent a significant component of engineering education, challenging students with intricate tasks that blend CAD modeling, Finite Element Analysis Assignment Help, and performance evaluation. Projects like Electric Motors and Hybrid Drives exemplify these challenges, requiring a deep understanding of concepts like electric motors, hybrid drives, and energy storage devices. This guide aims to equip students with essential strategies and insights to excel in their Solidworks assignments, regardless of the specific project details.
Solidworks assignments not only test theoretical knowledge but also demand practical application of engineering principles. They serve as a bridge between classroom learning and real-world engineering scenarios, preparing students for the complexities they will face in their careers. By mastering Solidworks, students develop critical skills in design optimization, structural analysis, and performance prediction—skills that are highly valued in industries ranging from automotive to aerospace.
Understanding the foundational principles of Solidworks is crucial for tackling assignments effectively. Begin by immersing yourself in the fundamental concepts related to your project's scope.
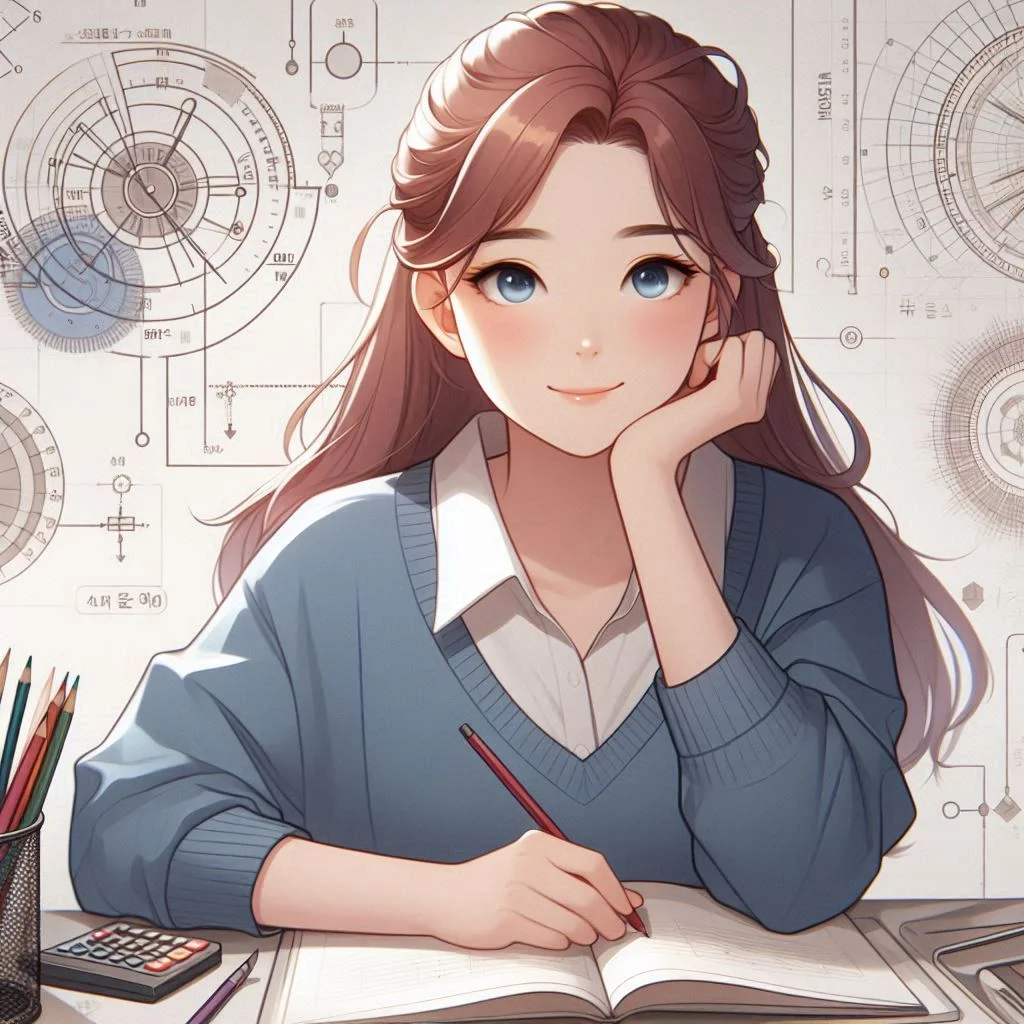
For instance, in projects involving electric motors and hybrid drives, delve into the operational principles of electric motors, the integration of hybrid drive technologies, and the role of energy storage devices in enhancing efficiency and sustainability.
CAD modeling forms the cornerstone of Solidworks assignments, enabling students to translate conceptual designs into detailed digital prototypes. The ability to accurately model components and assemblies lays the groundwork for subsequent analysis and simulation tasks. By leveraging Solidworks' robust suite of CAD tools, students can create intricate designs that meet specified performance criteria and design constraints.
Finite Element Analysis (FEM) emerges as a pivotal tool in evaluating the structural integrity and performance of Solidworks models. This numerical technique divides complex structures into smaller, manageable elements, allowing for detailed analysis of stress distribution, deformation behavior, and response to applied loads. Through FEM simulations, students gain insights into how their designs behave under different operational conditions, identifying areas of potential improvement and optimization.
Successful completion of Solidworks assignments hinges on effective project management and systematic problem-solving strategies. Documenting each phase of the assignment—from initial concept development to final simulation results—ensures clarity, traceability, and accountability throughout the design process. This documentation serves as a valuable reference for future projects and facilitates collaborative efforts with peers and instructors.
Understanding the Assignment Requirements
The first step in tackling any Solidworks assignment is to grasp the assignment requirements fully. For projects involving complex systems like Electric Motors and Hybrid Drives, it's crucial to immerse yourself in the underlying principles. Begin by researching and understanding concepts such as:
- Electric Motors: Delve into the fundamentals of electric motor operation, encompassing various types such as DC motors, AC motors, and their specialized variants like brushless DC motors. Understand the components that make up an electric motor, including the stator, rotor, and commutator, and how these components interact to produce mechanical motion. Gain insights into the specific roles electric motors play within hybrid drive systems, from providing propulsion to energy regeneration during braking.
- Hybrid Drives: Explore the intricacies of hybrid drive technologies that combine internal combustion engines with electric propulsion systems. Analyze integration strategies that optimize energy efficiency and minimize environmental impact, such as series, parallel, and series-parallel hybrid configurations. Investigate performance enhancements over conventional powertrains, including improved fuel economy, reduced emissions, and enhanced torque delivery across varying driving conditions.
- Energy Storage Devices: Investigate the diverse array of energy storage solutions employed in hybrid vehicles, ranging from rechargeable batteries to ultra-capacitors. Examine their respective advantages and limitations concerning energy density, power output, charge-discharge cycles, and environmental sustainability. Evaluate their impact on system design, considering factors such as packaging constraints, weight distribution, and overall vehicle performance metrics.
Initial CAD Modeling
With a solid understanding of the assignment's technical aspects, proceed to CAD modeling using Solidworks. CAD (Computer-Aided Design) serves as the foundation for visualizing and simulating complex engineering designs. Follow these steps to create a robust CAD model:
- Structural Design Considerations: Incorporate design constraints such as maximum stiffness and minimum weight. For instance, in web or truss-type structures, emphasize geometry that optimizes structural integrity without compromising weight efficiency.
- CAD Model Development: Utilize Solidworks tools to translate conceptual designs into detailed CAD models. Pay attention to geometric accuracy, component interconnections, and spatial relationships essential for subsequent analysis and simulation.
- Iterative Refinement: CAD modeling often involves iterative refinement. Start with preliminary sketches and progressively add complexity and detail. Validate each design iteration against initial specifications and project requirements.
Performing Finite Element Method (FEM) Analysis
Once your CAD model is complete, the next critical phase is Finite Element Method (FEM) analysis. FEM is a powerful numerical technique used to simulate and evaluate structural behavior under various load conditions. Here’s how to approach FEM analysis effectively:
- Solid Mesh Generation: Convert your CAD model into a finite element mesh using Solidworks simulation tools. The mesh discretizes the model into smaller elements, facilitating accurate stress and displacement calculations.
- Applying Loads and Boundary Conditions: Define realistic operating conditions by applying loads (forces, pressures, etc.) and boundary conditions (constraints, supports, etc.) to the model. This step simulates real-world scenarios and operational environments.
- Stress and Displacement Analysis: Conduct stress analysis to assess material performance under applied loads. Use Solidworks to generate visualizations such as Von Mises stress plots, which indicate areas of potential failure or deformation. Similarly, analyze displacement in both X and Y directions to evaluate structural deflection and deformation (refer to Figures 3, 4, and 5 in your assignment).
Evaluating Performance Metrics
Compare simulation results against predefined performance metrics and design constraints. Typical metrics include:
- Mass: Evaluate the actual mass of the modeled component or system and compare it with the target or benchmark values.
- Natural Frequency: Assess the natural frequency of vibration modes to ensure operational stability and mitigate resonance risks.
- Displacement and Deformation: Measure and analyze displacements in different directions to verify structural integrity and compliance with design specifications.
Use a structured approach to compile and interpret analysis outcomes. Table 1 in your assignment exemplifies this comparison, detailing how actual results deviate from initial design constraints and highlighting areas for improvement.
Iterative Design Refinement
Solidworks assignments often necessitate iterative design refinements based on simulation feedback. Embrace the iterative process by:
- Analyzing Simulation Results: Scrutinize simulation outputs to identify discrepancies, stress concentrations, or performance deficiencies.
- Implementing Design Modifications: Incorporate iterative improvements by adjusting CAD geometry, revising material properties, or optimizing load distributions. This step aims to enhance structural efficiency, minimize weight, or improve operational performance.
- Validation and Verification: Validate each design iteration through repeated FEM simulations. Verify that implemented changes effectively address identified issues and align with project objectives.
Conclusion and Recommendations
Conclude your Solidworks assignment with a comprehensive summary that encapsulates your journey from initial design to final analysis. Reflect on the achieved results, acknowledging both successes and challenges encountered along the way. Highlight deviations from the initial design constraints, emphasizing how these insights have informed your understanding of engineering principles and practical applications.
Moving forward, prioritize continuous improvement as a cornerstone of your engineering practice. Recommend iterative design refinements based on simulation outcomes, aiming to enhance structural integrity, optimize performance metrics like mass and natural frequency, and refine geometric configurations to achieve optimal results. Emphasize the value of learning through iteration, where each design iteration builds upon the last, refining your skills and expanding your knowledge base in Solidworks and mechanical design.
By embracing this approach, you not only meet current assignment objectives but also lay a foundation for tackling future engineering challenges with confidence and proficiency.
Tips for Success in Solidworks Assignments
Achieving proficiency in Solidworks assignments requires a combination of technical expertise, analytical acumen, and effective project management. Consider the following tips to optimize your learning and performance:
- Master Solidworks Tools: Familiarize yourself with Solidworks’ diverse toolset, including CAD modeling, simulation, and visualization capabilities. Practice using advanced features such as assembly design, motion analysis, and sheet metal modeling.
- Document Your Process: Maintain detailed documentation throughout the project lifecycle. Document CAD iterations, simulation settings, analysis results, and design decisions. This practice facilitates knowledge retention, project review, and future reference.
- Seek Expert Guidance: Don’t hesitate to seek guidance from Solidworks experts, instructors, or online communities. Collaborate with peers, participate in forums, or leverage academic support services to resolve technical challenges and broaden your understanding.
Conclusion
Mastering SolidWorks assignments goes beyond fulfilling academic requirements; it prepares you for real-world engineering challenges. By embracing projects like Electric Motors and Hybrid Drives and applying structured methodologies, you develop essential skills in CAD modeling, FEM analysis, and performance evaluation. These skills are invaluable for aspiring engineers seeking to innovate and excel in the field of mechanical design.
Ready to embark on your SolidWorks journey? Approach your next assignment with confidence and a strategic mindset. For additional guidance or expert assistance, visit SolidworksAssignmentHelp.com to explore comprehensive support tailored to your academic needs.