- Understanding the Importance of Finite Element Analysis (FEA) in Engineering
- The Concept of Finite Element Analysis
- Applications of Finite Element Analysis in Engineering
- Benefits of Implementing Finite Element Analysis
- Strategies to Optimize Finite Element Analysis Assignments
- Preprocessing: Mesh Generation and Model Simplification
- Material Modeling and Accurate Boundary Conditions
- Iterative Analysis and Convergence
- Post-processing: Analyzing and Interpreting Results
- Results Visualization and Analysis
- Sensitivity Analysis and Design Optimization
- Conclusion:
Finite Element Analysis (FEA) is a fundamental computational technique used in engineering to evaluate and improve complex systems and structures. By breaking complex issues down into smaller, more manageable pieces, it revolutionizes the traditional design and analysis process. This enables engineers to simulate real-world conditions and predict how the system will behave under different loads and constraints. Achieving trustworthy engineering solutions necessitates the accurate and effective execution of FEA assignments. In order to improve the overall quality of engineering results, this blog explores the optimization of Finite Element Analysis assignments. Engineering disciplines such as structural analysis, heat transfer, fluid dynamics, and electromagnetic simulations all use FEA extensively. Engineers can evaluate a structure's strength, stability, and performance, analyze heat flow patterns, model fluid behavior, and investigate electromagnetic properties by using FEA. Engineers are given the tools they need to use FEA to simulate and analyze complex systems, which helps them make better decisions, and better designs, save money, and lower the risk of failure. Several tactics can be used throughout the FEA workflow to optimize Finite Element Analysis assignments. Preprocessing ensures accurate results and effective computations by generating meshes and simplifying models. For accurate simulations to be produced, boundary conditions and material properties must be defined correctly. Convergence techniques and iterative analyses are used to improve the model's accuracy. Effective visualization, sensitivity analysis, and design optimization techniques are used in post-processing to analyze and interpret results.
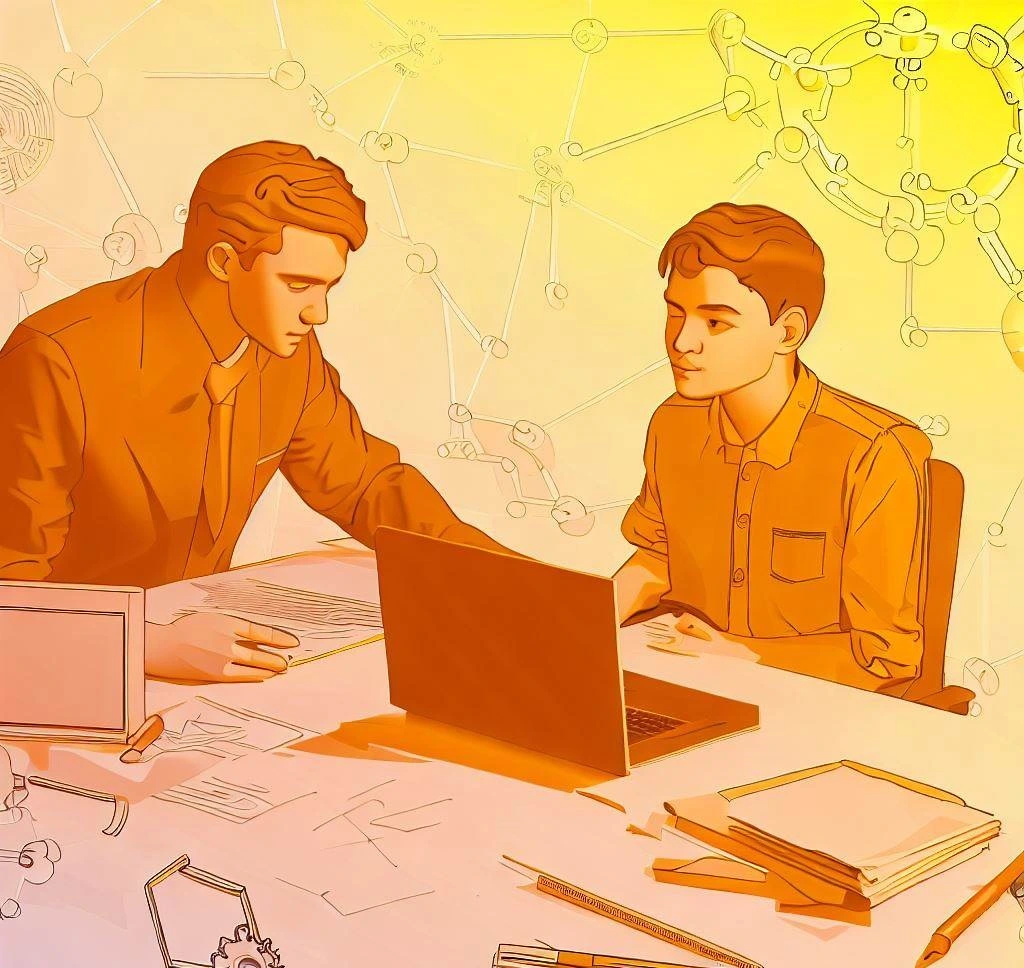
Understanding the Importance of Finite Element Analysis (FEA) in Engineering
Due to its capacity to precisely simulate and analyze complex systems, Finite Element Analysis (FEA) has enormous significance in the field of engineering. Engineers can learn important information about how complex structures behave under various loading conditions by using the numerical method known as finite element analysis (FEA). Engineers can assess the performance, dependability, and safety of designs using this computational technique, making it a vital tool for improving engineering solutions. Numerous engineering disciplines use FEA in a variety of contexts. To help identify potential failure points and optimize designs, FEA is used in structural analysis to help determine the strength, stiffness, and stability of structures. FEA aids in heat transfer analysis by analyzing the flow of heat in various materials and enhancing cooling systems. FEA-based fluid dynamics simulations help with fluid flow pattern understanding, hydraulic system design optimization, and fluid behavior prediction in a variety of situations. Engineers can study and improve electromagnetic field behavior by using electromagnetic simulations, which are made possible by FEA.
The Concept of Finite Element Analysis
By breaking down complex structures into smaller finite elements, the numerical method known as finite element analysis (FEA) can be used to solve engineering problems. A mesh is created when these components are joined at particular nodes. Engineers can simulate real-world conditions and forecast the performance of the system by using FEA to examine the behavior of individual elements and how they interact with nearby elements.
Applications of Finite Element Analysis in Engineering
FEA is frequently used in many different engineering disciplines. It has uses in electromagnetic simulations, fluid dynamics, heat transfer, and structural analysis. Among many other uses, engineers can use FEA to analyze heat flow in various materials, simulate fluid flow patterns, assess the strength, stiffness, and stability of structures, and study electromagnetic behavior.
Benefits of Implementing Finite Element Analysis
FEA can be used to improve the engineering design process in a number of ways. Engineers can optimize designs, lower costs, and lower the risk of failure with the help of FEA. It offers insights into how the system behaves, enabling advancements in efficiency, dependability, and security. Engineers can also evaluate various design alternatives with FEA, optimize material usage, and speed up development.
Strategies to Optimize Finite Element Analysis Assignments
It is essential to optimize Finite Element Analysis (FEA) assignments in order to produce precise and effective engineering solutions. The overall FEA process can be improved by using a variety of techniques. First, mesh generation and model simplification should receive careful consideration during the preprocessing stage. Engineers can guarantee accurate results while using the least amount of computational resources by specifying an appropriate mesh size and element distribution. Additionally, by eliminating superfluous details from the model, analysis speed can be greatly accelerated without compromising accuracy. Second, it is critical to assign boundary conditions and model the material accurately. To ensure accurate simulations, engineers should precisely define material properties based on experimental data or proven models. The same is true for the assignment of boundary conditions that accurately represent real-world scenarios.
Preprocessing: Mesh Generation and Model Simplification
The preprocessing phase is essential for FEA assignment optimization. Accurate results and effective computations are guaranteed by proper mesh generation. Engineers should specify the mesh size, the components, and the boundary conditions with care. Additionally, it is possible to increase analysis speed and decrease computational complexity without compromising accuracy by using model simplification techniques.
Material Modeling and Accurate Boundary Conditions
It is crucial to accurately model material properties and set suitable boundary conditions in order to get trustworthy results. Strict definitions of material characteristics like stiffness, thermal conductivity, and fluid flow characteristics should be made using experimental data or validated models. Similarly, to ensure accurate simulation, boundary conditions should mimic real-world scenarios.
Iterative Analysis and Convergence
The iterative analysis is a useful technique for enhancing FEA assignments. Engineers can increase the precision and dependability of the output by gradually improving the model. It entails examining the initial model, identifying potential areas for development, and making the necessary corrections. In order to ensure optimal design and trustworthy engineering solutions, the process is continued until convergence is reached.
Post-processing: Analyzing and Interpreting Results
Finite Element Analysis (FEA) post-processing is a critical stage where engineers evaluate and interpret the outcomes of simulations. Engineering professionals can gain useful insights from data and make wise decisions by using efficient post-processing techniques. Results visualization, which entails presenting the data in a clear and concise manner, is a crucial component of post-processing. Engineers can visualize stress distribution, displacement patterns, and other important parameters using contour plots, animations, and graphs. With the help of this visualization, the analyzed structure's critical regions, stress concentrations, and potential failure points can be found. Another crucial part of post-processing is sensitivity analysis, which examines the effects of changing parameters on the outcomes. Engineers can assess the impact of parameters on the system's performance and decide on design changes based on this evaluation. In order to ensure compliance and pinpoint areas for improvement, post-processing also involves comparing the outcomes with design requirements and industry standards. Engineers can improve their designs, optimize performance, and provide better engineering solutions by skillfully analyzing and interpreting the findings.
Results Visualization and Analysis
Analyzing and interpreting the outcomes of FEA simulations is part of post-processing. To derive useful insights from the data, engineers should concentrate on effectively visualizing and interpreting it. Contour plots, animations, and graphs are examples of visualization techniques that can be used to locate critical regions, stress concentrations, and potential failure points.
Sensitivity Analysis and Design Optimization
Techniques for design optimization and sensitivity analysis can be used to further optimize engineering solutions. Sensitivity analysis aids in locating variables that have a big impact on how well the system works. Engineers can evaluate the impact of changing these parameters on the outcomes and adjust the design as necessary. Engineers can determine the best design configuration based on predefined objectives and constraints using design optimization techniques like topology optimization or parameter optimization.
Conclusion:
It is crucial to optimize Finite Element Analysis (FEA) assignments in order to produce precise and trustworthy engineering solutions. Engineers can improve the final results and streamline the analysis process by implementing efficient strategies throughout the FEA workflow. Mesh generation and model simplification are two preprocessing techniques that guarantee accurate results and quick computations. For reliable simulations, accurate material modeling and boundary condition assignment are essential. Convergence methods and iterative analysis are used to improve the model's accuracy. Engineers can gain important insights and make wise decisions during the post-processing phase with the aid of effective visualization and interpretation of the results. The optimization process is improved further by sensitivity analysis and adherence to design specifications. Engineers can increase design innovation opportunities, shorten the time and cost of development, and produce superior engineering solutions that achieve the desired goals by optimizing FEA assignments. Engineers can simulate and analyze complex systems using FEA, which enables them to make wise decisions, enhance designs, and reduce risks. The optimization of FEA assignments ultimately results in improved engineering solutions and advancements in the engineering discipline.