- Understanding Finite Element Analysis (FEA) in SolidWorks:
- The Significance of Validation in FEA:
- Ensuring Accuracy in Simulation
- Addressing Boundary Conditions
- Verification: A Key Step in the Process:
- Model Verification Techniques
- Importance of Material Properties
- Common Challenges in FEA Validation:
- Meshing Issues
- Sensitivity to Initial Conditions
- Case Studies: Real-world Application of FEA Validation:
- Automotive Design Example
- Structural Analysis in Mechanical Engineering
- Best Practices for FEA Validation in SolidWorks Assignments:
- Collaboration and Peer Review
- Continuous Learning and Skill Development
- Conclusion:
In the realm of SolidWorks assignments at the college level, Finite Element Analysis (FEA) plays a pivotal role in simulating real-world conditions to validate and verify designs. This blog delves into the importance of FEA validation and verification in ensuring accurate results for SolidWorks assignments, shedding light on its significance in the academic context.
Finite Element Analysis serves as the cornerstone of modern engineering simulations. As students embark on SolidWorks assignments, understanding the essence of FEA becomes paramount. It goes beyond mere simulation; it's a method to ascertain that the virtual representation aligns with physical realities. Achieving this alignment involves a careful dance of validation and verification.
Validation, in the context of FEA, is akin to fact-checking. It involves scrutinizing the simulated results against real-world data, ensuring that the virtual prototype behaves as expected in practical scenarios. This process demands a meticulous understanding of the physical principles governing the system under examination.
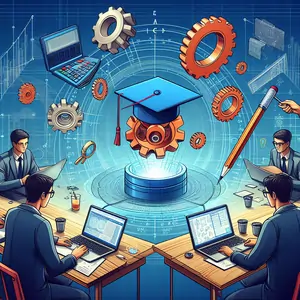
Verification, on the other hand, is the internal scrutiny of the simulation model. It's the close inspection of the mathematical model's fidelity to the intended design. This step becomes crucial in avoiding computational errors and instilling confidence in the accuracy of the virtual prototype.
Understanding the interplay between these two processes is fundamental. Accuracy in FEA is not a mere luxury; it's a prerequisite for meaningful engineering insights. A miscalculation at the simulation stage can reverberate throughout the design process, leading to suboptimal solutions and potential setbacks.
Consider the student grappling with a complex structural design in a SolidWorks assignment. The correct simulation of stress distribution, material behavior, and load-bearing capacities becomes the litmus test for their comprehension of both SolidWorks and engineering principles. Here, FEA is not just a tool; it's a pedagogical medium ensuring that theoretical knowledge translates into practical proficiency.
FEA, however, is not without its challenges. Meshing issues, often encountered in simulations, can significantly impact the accuracy of results. A poorly defined mesh can lead to inaccuracies in stress concentrations and deformation patterns. Sensitivity to initial conditions is another hurdle. Small variations in the starting parameters can yield vastly different results, necessitating a cautious and iterative approach.
In navigating these challenges, the student not only learns the intricacies of FEA but also hones problem-solving skills—an invaluable asset in the professional realm. The diligence required in addressing meshing problems or sensitivity to initial conditions mirrors the meticulousness demanded in real-world engineering projects.
In conclusion, the mastery of FEA validation and verification is not just a checkbox in a student's academic journey. It's a gateway to precision, a bridge connecting theoretical knowledge to real-world applications. As SolidWorks assignments become more intricate, the role of FEA in ensuring accuracy becomes even more pronounced, shaping not only designs but also the engineers of tomorrow. For those seeking assistance, remember that understanding and mastering FEA is crucial to solving your FEA assignment effectively.
Understanding Finite Element Analysis (FEA) in SolidWorks:
SolidWorks, renowned for its prowess in 3D modeling and simulation, stands out as a versatile tool that integrates Finite Element Analysis (FEA) to evaluate the structural integrity and performance of various designs. In the academic realm, SolidWorks becomes an invaluable resource, offering students the opportunity to bridge theoretical knowledge with practical application.
FEA, as a simulation method, enables users to analyze complex structures and systems, simulating real-world conditions to predict how designs will behave under different circumstances. SolidWorks, with its user-friendly interface and robust capabilities, empowers students to explore the intricacies of FEA, providing a hands-on experience that goes beyond theoretical concepts.
In the academic setting, students engaging with SolidWorks gain a profound understanding of FEA's role in design validation. This section aims to shed light on the transformative impact of FEA in SolidWorks assignments, serving as a bridge between classroom learning and real-world applications. As students navigate the software, they not only enhance their technical proficiency but also cultivate a problem-solving mindset crucial for success in the professional arena.
SolidWorks' FEA capabilities become a cornerstone for students aspiring to enter fields where design precision is paramount. This overview sets the stage for a comprehensive exploration of how FEA validation and verification contribute to the accuracy of SolidWorks assignments, ultimately preparing students for the challenges and opportunities that lie ahead in their academic and professional journey.
The Significance of Validation in FEA:
Finite Element Analysis (FEA) in SolidWorks hinges on the principle of validation to ensure the accuracy and reliability of simulation results. It serves as the litmus test, scrutinizing the virtual behavior of a design against real-world conditions. By emphasizing the need for precise validation, SolidWorks assignments gain credibility, offering students a deeper understanding of the principles governing their designs.
Validation in FEA is synonymous with aligning simulation outcomes with empirical data, a process vital for predicting how a design will perform under different circumstances. It is not merely about achieving results but achieving results that mirror the physical reality. This alignment contributes to the trustworthiness of SolidWorks assignments, as stakeholders can rely on the virtual predictions to inform decision-making processes.
One crucial aspect of validation revolves around the establishment of accurate boundary conditions. Inaccuracies in setting up boundary conditions can skew results, leading to a misrepresentation of a design's real-world behavior. Achieving precision in this area involves a meticulous understanding of the physical constraints and environmental factors impacting the design. It's not just about the simulation; it's about recreating reality within the virtual realm.
Moreover, validation acts as a quality assurance checkpoint in the design process. It ensures that the assumptions made during simulation align with the physical world, allowing for a more informed evaluation of a design's performance. In the educational context, mastering the art of validation in FEA not only enhances academic projects but also prepares students for the demands of real-world engineering, where accuracy is paramount.
As students delve into the realm of SolidWorks assignments, a keen appreciation for the significance of validation in FEA becomes a cornerstone for academic excellence and a foundation for future engineering endeavors. It is the gateway to precision, unlocking the potential to design with confidence and foresight.
Ensuring Accuracy in Simulation
Validation in Finite Element Analysis (FEA) is the linchpin for ensuring the accuracy of simulation results, establishing a crucial link between virtual models and real-world performance. The essence of validation lies in the meticulous comparison of simulated data with empirical observations, offering a benchmark for the credibility of SolidWorks assignments.
Accurate simulation results not only validate the design but also instill confidence in its real-world applicability. This validation process involves a comprehensive analysis of various factors, including material properties, geometric intricacies, and loading conditions. The closer the alignment between simulated and real-world outcomes, the more reliable and trustworthy the SolidWorks assignment becomes.
Validation is not merely a checkbox in the design process; it is a continuous loop of refinement, feedback, and improvement. It ensures that the simulated behavior accurately mirrors the physical reality, providing students with a robust foundation for engineering principles and practices.
In essence, the critical role of validation in FEA goes beyond mere accuracy—it is the gateway to creating designs that stand the test of practical application, preparing students for the challenges of real-world engineering scenarios. Mastering this aspect of SolidWorks assignments enhances not only academic performance but also lays the groundwork for success in the professional realm.
Addressing Boundary Conditions
The accuracy of Finite Element Analysis (FEA) hinges on the precise definition of boundary conditions, making it a pivotal aspect of the validation process. Accurate boundary conditions are akin to setting the stage for a realistic simulation, ensuring that the virtual model behaves in a manner representative of its real-world counterpart.
Challenges often arise in establishing boundary conditions due to the complexity of systems and the dynamic nature of external influences. In this context, it becomes imperative to address these challenges systematically. Best practices involve a combination of theoretical understanding, empirical knowledge, and, often, a trial-and-error approach.
Highlighting the impact of boundary conditions on the validation process, this aspect of FEA demands meticulous attention to detail. From restraining degrees of freedom to accurately representing external loads, the setup of boundary conditions significantly influences the reliability and precision of simulation results.
In conclusion, addressing boundary conditions is not merely a technical requirement; it is an art that requires a nuanced understanding of engineering principles. Mastery of this aspect not only refines FEA skills but also fortifies the foundation for accurate SolidWorks assignments, setting the stage for success in academic and professional pursuits.
Verification: A Key Step in the Process:
Verification stands as a pivotal phase in the Finite Element Analysis (FEA) process, acting as a linchpin for the reliability of SolidWorks assignments. This step involves confirming the accuracy and credibility of the simulation results, ensuring they align with the intended objectives. To achieve this, engineers and students employ various techniques that collectively contribute to the robustness of the FEA model.
Verification begins with a meticulous examination of the SolidWorks model. Engineers focus on refining the mesh, a crucial aspect of the simulation process. Mesh refinement involves breaking down the model into smaller elements, enhancing the precision of the simulation. It's a delicate balancing act, as too much refinement can lead to computational challenges, while too little may compromise result accuracy.
In addition to mesh refinement, engineers conduct convergence studies during the verification phase. These studies assess how well the solution stabilizes as the mesh size changes, providing insights into the sensitivity of the model to mesh density. By systematically refining the mesh and observing convergence patterns, engineers gain confidence in the reliability of the simulation results.
Material properties also undergo thorough scrutiny during verification. Accurate representation of material behavior is imperative for FEA success. Engineers verify that the specified material properties align with real-world characteristics, ensuring the simulation reflects the expected physical response of the material under different conditions.
The verification process, therefore, encapsulates a holistic examination of the SolidWorks model, encompassing mesh refinement, convergence studies, and material property validation. These combined efforts form the cornerstone of ensuring that FEA results accurately depict the behavior of structures and components, a crucial factor in the academic landscape and beyond.
Model Verification Techniques
In the intricate world of Finite Element Analysis (FEA), model verification stands as a critical step to guarantee the precision of SolidWorks models. Various techniques are employed to validate these models, ensuring that the simulations align closely with real-world scenarios.
Mesh refinement stands out as a primary technique, involving the subdivision of the model into smaller elements for more accurate analysis. This process enhances the simulation's reliability by capturing intricate details that might be overlooked with a coarser mesh.
Convergence studies constitute another indispensable aspect of model verification. By systematically refining the mesh and observing how the results converge to a stable outcome, engineers and students can ascertain the optimal mesh density for accurate simulations.
These techniques, alongside other sophisticated methods, contribute to the robustness of SolidWorks models, reinforcing their applicability in diverse engineering scenarios.
Importance of Material Properties
The success of Finite Element Analysis in SolidWorks assignments hinges upon the accurate representation of material properties. Deviations in material data can significantly impact the validation and verification process, introducing errors that may compromise the reliability of simulations.
Understanding the mechanical behavior of materials under different conditions is paramount. Accurate input of material properties ensures that the simulation mirrors real-world responses, allowing students and engineers to make informed decisions about the structural integrity and performance of their designs.
In the realm of FEA, meticulous attention to material data is not just a technicality but a fundamental practice. By highlighting the importance of accurate material properties, we underscore the role they play in fortifying the foundation of reliable FEA results.
Common Challenges in FEA Validation:
In the intricate world of Finite Element Analysis (FEA), validation is not without its set of challenges. One common hurdle encountered in the process is related to meshing issues. Meshing, the discretization of a model into small elements, can be a double-edged sword. While a fine mesh contributes to more accurate results, it simultaneously escalates computational demands. Striking the right balance becomes crucial. Challenges arise when meshing becomes too coarse, leading to inaccurate representations of the real-world scenario, or too fine, demanding excessive computational resources. Consequently, engineers and students must navigate this delicate balance to achieve accurate results in FEA simulations.
Sensitivity to initial conditions poses another substantial challenge in FEA validation. Small variations in the starting conditions of a simulation can yield vastly different outcomes, impacting the reliability of the results. Addressing this challenge involves meticulous attention to detail during the setup phase, as well as an understanding of how the chosen initial conditions may influence the final simulation. Navigating these challenges requires a nuanced approach, emphasizing the iterative nature of FEA validation and the need for constant refinement to ensure the accuracy of the simulation outcomes.
Meshing Issues
In the realm of Finite Element Analysis (FEA), meshing is a critical step that can significantly impact the accuracy of simulations. One common challenge is the creation of an appropriate mesh that accurately represents the geometry and captures stress concentrations. Discuss the intricacies of meshing, addressing issues such as element distortion and skewness that can arise during the meshing process.
Mesh Density and Its Role:
Elaborate on the importance of mesh density in achieving accurate results. Discuss how a fine mesh can capture intricate details but might increase computational demands. Explore the balance between mesh refinement and computational efficiency, providing guidelines for optimal meshing strategies in different scenarios.
Solutions and Best Practices:
Offer solutions to common meshing challenges, including mesh quality improvement techniques and guidelines for selecting appropriate element types. Discuss the significance of mesh convergence studies in validating the sensitivity of results to mesh changes.
Sensitivity to Initial Conditions
Sensitivity to initial conditions is a critical consideration in ensuring the reliability of FEA simulations. Delve into the intricacies of how small variations in initial conditions can lead to significant differences in simulation outcomes.
Identifying Sensitivity Issues:
Explore scenarios where sensitivity to initial conditions becomes pronounced. Discuss how factors such as load application, material properties, and geometric imperfections can influence the sensitivity of FEA simulations.
Mitigating Sensitivity Impact:
Provide insights into strategies to mitigate sensitivity issues, emphasizing the importance of robust validation processes. Discuss techniques such as parameter studies, where variations in input parameters are systematically explored to understand their impact on results.
Advanced Simulation Settings:
Introduce advanced simulation settings and solvers that can help address sensitivity challenges. Discuss how adaptive meshing and solution refinement strategies can enhance the stability and accuracy of FEA simulations in the face of sensitivity concerns.
These additions provide a more comprehensive exploration of meshing challenges and sensitivity issues in Finite Element Analysis, offering practical solutions and insights for students grappling with these aspects in SolidWorks assignments.
Case Studies: Real-world Application of FEA Validation:
In this section, we delve into real-world applications of Finite Element Analysis (FEA) validation, demonstrating its practical significance in engineering scenarios.
Case studies provide tangible evidence of how FEA contributes to the success of SolidWorks assignments, offering insights into its application in diverse fields. One compelling example involves the automotive industry, where FEA validation ensures the structural integrity and safety of vehicle components. By subjecting designs to virtual simulations that mimic real-world conditions, engineers can optimize materials and geometries to meet stringent safety standards.
Furthermore, in the realm of mechanical engineering, FEA validation plays a crucial role in structural analysis. A case study focusing on this application reveals how FEA helps engineers optimize designs for strength, durability, and overall performance. By simulating complex interactions within structures, SolidWorks assignments benefit from the ability to predict how components will respond to various loads, enabling the creation of robust and efficient designs.
These case studies underscore the transformative impact of FEA validation, offering a bridge between theoretical concepts and practical engineering solutions. Through real-world examples, students gain a deeper appreciation for the role of FEA in ensuring the reliability and accuracy of SolidWorks assignments.
Automotive Design Example
In the realm of automotive design, FEA validation is a cornerstone in ensuring the safety and efficiency of critical components. Consider a case study where FEA is applied to assess the structural integrity of a car chassis. Explore how simulations help identify potential weak points, ensuring that the design withstands various loads and impact scenarios. Discuss the role of FEA in optimizing material usage, leading to lighter yet stronger structures that meet safety standards. This case study exemplifies how FEA contributes to the innovation and reliability of automotive designs, highlighting its indispensable role in the field.
Structural Analysis in Mechanical Engineering
In the context of mechanical engineering, structural analysis is paramount for optimizing designs for strength and durability. Present a case study that involves FEA validation in the structural analysis of a complex mechanical component. Discuss how FEA simulations assist in identifying stress concentrations, weak points, and potential failure modes. Explore the iterative design process enabled by FEA, showcasing how engineers refine and enhance structures based on simulation results. This case study emphasizes the transformative impact of FEA validation on ensuring robust and durable designs in the realm of mechanical engineering.
Best Practices for FEA Validation in SolidWorks Assignments:
As students and professionals navigate the intricate landscape of SolidWorks assignments, incorporating best practices for Finite Element Analysis (FEA) validation becomes paramount. Engaging in collaborative efforts and subjecting simulations to peer review emerges as a cornerstone in refining and fortifying FEA outcomes. In this vein, fostering an environment of open communication and knowledge sharing among peers fosters a collective intelligence that can uncover potential oversights and enhance the accuracy of simulations.
Continuous learning stands out as an indispensable best practice. The dynamic nature of FEA technology necessitates a commitment to ongoing education and skill development. Students should actively seek out resources, webinars, and workshops to stay informed about the latest advancements in SolidWorks and FEA methodologies. This commitment not only ensures proficiency in current practices but also positions individuals to adapt to evolving industry standards and emerging simulation techniques.
Furthermore, encouraging a mindset of curiosity and exploration contributes to the development of a robust FEA skill set. Students should approach FEA validation as a learning experience, dissecting simulation results to understand the underlying mechanics and correlations with real-world scenarios. This hands-on exploration not only reinforces theoretical knowledge but also cultivates a deeper understanding of the intricacies involved in validating SolidWorks designs.
In conclusion, integrating collaborative efforts, continuous learning, and a mindset of exploration into the FEA validation process equips students with the tools to navigate the challenges of SolidWorks assignments effectively. These best practices not only enhance simulation accuracy but also lay the foundation for a lifelong journey of growth and proficiency in the dynamic field of Finite Element Analysis.
Collaboration and Peer Review
In the world of SolidWorks assignments and FEA, collaboration and peer review stand out as indispensable elements of the validation process. Encouraging students to work together on simulations fosters a diverse range of perspectives and insights. Through collaborative efforts, potential errors are more likely to be identified and rectified, contributing to the overall accuracy of simulation results. This section explores the benefits of teamwork in the context of FEA validation, emphasizing the collective knowledge and problem-solving capabilities that arise when individuals collaborate on SolidWorks assignments.
Continuous Learning and Skill Development
In the world of SolidWorks assignments and FEA, collaboration and peer review stand out as indispensable elements of the validation process. Encouraging students to work together on simulations fosters a diverse range of perspectives and insights. Through collaborative efforts, potential errors are more likely to be identified and rectified, contributing to the overall accuracy of simulation results. This section explores the benefits of teamwork in the context of FEA validation, emphasizing the collective knowledge and problem-solving capabilities that arise when individuals collaborate on SolidWorks assignments.
Conclusion:
In wrapping up our exploration of Finite Element Analysis (FEA) validation and verification within the context of SolidWorks assignments, it becomes evident that these skills are not mere academic exercises but pillars supporting a successful academic and professional journey.
The key takeaway lies in the profound impact of accurate simulation results on the credibility of SolidWorks assignments. Through meticulous validation and verification processes, students gain a deeper understanding of how their designs will perform in real-world scenarios. This understanding transcends the academic realm, laying the groundwork for professionals who can confidently tackle real-world engineering challenges.
Mastering FEA in SolidWorks assignments is a multifaceted skill that extends beyond the technical aspects. It cultivates a mindset of precision, attention to detail, and a commitment to excellence. These attributes are not only crucial in the academic environment but are highly valued in the professional landscape, where engineers are tasked with delivering solutions that adhere to strict performance criteria and safety standards.
Moreover, the ability to navigate challenges such as meshing issues, sensitivity to initial conditions, and the dynamic nature of FEA technology positions students as adaptable problem solvers. The experiences gained from overcoming these challenges contribute to the development of resilience and resourcefulness—qualities that are equally indispensable in the academic journey and the professional arena.
Looking ahead, the long-term benefits of mastering FEA validation and verification are manifold. Graduates equipped with these skills are better positioned for success in the job market, where proficiency in simulation tools is increasingly valued by employers. Additionally, as industries evolve and technology continues to advance, individuals adept at FEA find themselves at the forefront of innovation, contributing to the development of cutting-edge solutions and methodologies.
In essence, FEA validation and verification in SolidWorks assignments are not just academic endeavors; they are stepping stones towards a future where precision, innovation, and a commitment to excellence become the hallmarks of academic and professional success. As students embark on their journey, mastering these skills sets the stage for a fulfilling and impactful career in the dynamic field of engineering and design.