- Understanding Finite Element Analysis (FEA)
- The Role of SolidWorks in FEA
- Key Strategies for Effective FEA Optimization
- Geometry Simplification for Efficient Analysis
- Material Selection and Properties
- Boundary Conditions and Constraints
- Meshing Techniques for Accurate Simulations
- Case Studies: Realizing the Power of FEA Optimization
- Overcoming Common Challenges in FEA Optimization
- Interpreting Analysis Results
- Optimizing for Multiple Performance Metrics
- Addressing Nonlinearities in FEA
- Future Trends: FEA and the Evolution of Design Optimization
- Conclusion
In the ever-evolving landscape of engineering and design, staying ahead requires leveraging advanced tools and techniques that not only keep pace with technological advancements but also enhance the precision and efficiency of the design process. SolidWorks, a renowned name in computer-aided design (CAD), stands at the forefront of these innovations, offering a myriad of features that empower engineers to bring their ideas to life seamlessly. Among the powerful tools embedded in SolidWorks, Finite Element Analysis (FEA) emerges as a cornerstone for engineers aiming to optimize their designs comprehensively.
Finite Element Analysis (FEA) is a computational method that has revolutionized the way engineers approach design challenges. It involves breaking down complex structures into smaller, more manageable elements, allowing for a detailed analysis of their behavior under various conditions. The strength of FEA lies in its ability to simulate real-world scenarios, enabling engineers to predict and refine the performance of their designs with a high degree of accuracy. This predictive capability is invaluable in identifying potential issues and inefficiencies early in the design phase, saving both time and resources.
The application of FEA within the SolidWorks environment opens up a realm of possibilities for design engineers. It serves as a virtual testing ground where concepts can be validated, refined, and optimized before the physical prototype is even created. This not only accelerates the product development cycle but also minimizes the risk of costly errors. As design complexity continues to increase, FEA becomes indispensable, offering insights into structural integrity, thermal performance, and fluid dynamics, among other critical aspects.
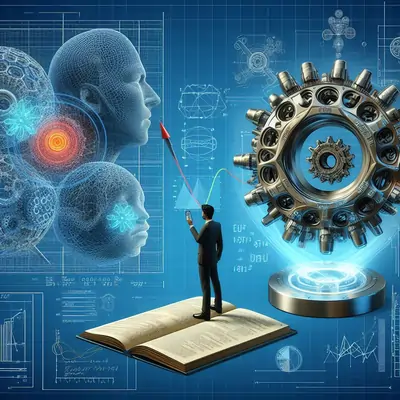
One of the key advantages of integrating FEA into SolidWorks is the seamless collaboration between the design and analysis phases. Engineers can iteratively refine their designs based on FEA results, fostering an iterative and informed decision-making process. This integration eliminates silos between design and analysis teams, promoting a holistic approach to product development.
Beyond its immediate benefits, the utilization of FEA in SolidWorks aligns with broader industry trends emphasizing sustainability and efficiency. By optimizing designs through virtual testing, engineers contribute to the reduction of physical prototypes, minimizing material waste and energy consumption. This not only aligns with environmental goals but also has a positive impact on the overall cost-effectiveness of the design process.
In essence, the ability to solve your SolidWorks assignment and FEA together form a symbiotic relationship that empowers design engineers to navigate the complexities of modern product development. This blog will delve into the intricacies of optimizing designs through the application of FEA, exploring its benefits and providing valuable insights for design engineers, ultimately paving the way for a future where innovation and efficiency go hand in hand.
Understanding Finite Element Analysis (FEA)
Before delving into optimization strategies, let's establish a foundational understanding of Finite Element Analysis (FEA). Finite Element Analysis is a numerical technique employed by engineers to simulate the behavior of structures and components under various conditions. In the world of SolidWorks, FEA becomes a powerful ally, providing a virtual testing ground where designs can be subjected to a range of forces, pressures, and thermal effects, mimicking real-world scenarios.
FEA divides complex structures into smaller, more manageable elements, allowing engineers to analyze each segment's behavior individually. The interaction between these elements generates a comprehensive picture of how the entire structure will respond to external stimuli. This simulation capability is particularly valuable during the early stages of design, enabling engineers to identify potential weaknesses, optimize material usage, and refine their models before physical prototyping.
By simulating real-world conditions, FEA empowers engineers to predict and improve the performance of their designs. It goes beyond traditional hand calculations, offering a detailed analysis of structural integrity, thermal characteristics, and fluid dynamics. SolidWorks integrates FEA seamlessly into its interface, providing users with a user-friendly platform to perform complex simulations and make data-driven decisions throughout the design process.
Understanding the principles of FEA sets the stage for leveraging its capabilities to optimize designs effectively. Now, let's explore how SolidWorks harnesses the power of FEA in the pursuit of design excellence.
The Role of SolidWorks in FEA
SolidWorks, a frontrunner in Computer-Aided Design (CAD) software, plays a pivotal role in revolutionizing the design process by seamlessly incorporating Finite Element Analysis (FEA) into its comprehensive workflow. SolidWorks stands out for its user-friendly interface, powerful modeling capabilities, and, notably, its integration of FEA tools.
Engineers benefit from a cohesive environment where the transition from design creation to simulation is seamless. SolidWorks provides a suite of sophisticated simulation tools that allow users to subject their designs to virtual testing under various conditions. This integration eliminates the need for external FEA software, streamlining the workflow and fostering a more efficient design process.
What sets SolidWorks apart is its capacity to empower engineers to perform detailed and precise simulations. The software's FEA capabilities enable engineers to validate and refine their designs with a level of precision that is crucial in today's competitive engineering landscape. Users can explore the structural integrity, thermal behavior, and fluid dynamics of their designs, gaining invaluable insights before physical prototypes are even considered.
Moreover, SolidWorks fosters a collaborative environment, allowing interdisciplinary teams to work seamlessly. Engineers can share models, simulation data, and insights, fostering effective communication and reducing the potential for errors or misinterpretations.
In essence, SolidWorks not only simplifies the integration of FEA into the design process but elevates it to a level of sophistication that empowers engineers to push the boundaries of innovation. The software serves as a catalyst for efficient, accurate, and collaborative design, enabling engineers to bring their concepts to life with confidence and precision.
Key Strategies for Effective FEA Optimization
In the intricate world of Finite Element Analysis (FEA), mastering key strategies is essential for unlocking the full potential of design optimization within SolidWorks. One fundamental strategy is the art of geometry simplification, where intricate structures are distilled into more manageable forms without compromising accuracy. SolidWorks provides engineers with a suite of tools to accomplish this, allowing for the creation of simplified models that retain the essential features of the original design.
A pivotal aspect of design optimization lies in material selection and understanding material properties. SolidWorks facilitates the simulation of various materials, empowering engineers to explore different scenarios virtually. This knowledge helps in making informed decisions regarding material choices, ultimately leading to optimized designs with enhanced performance characteristics.
Accurately defining boundary conditions and constraints is another critical strategy for obtaining realistic simulation results. SolidWorks allows engineers to precisely set environmental constraints and structural boundaries, ensuring that the simulation closely mirrors real-world conditions. This attention to detail is paramount in gaining insights into how a design will perform under various circumstances.
Meshing techniques play a crucial role in achieving accurate simulations. SolidWorks provides advanced meshing tools that give engineers control over mesh density and quality. Refined meshing techniques allow designers to strike a balance between accuracy and computational efficiency, ensuring that the simulation results are both reliable and manageable.
These strategies collectively form the backbone of effective FEA optimization in SolidWorks, providing designers with the tools and insights needed to refine designs, enhance performance, and streamline the overall design process. By integrating these principles into their workflow, engineers can unlock new levels of efficiency and innovation in their projects.
Geometry Simplification for Efficient Analysis
Streamline your FEA process by mastering the art of geometry simplification. Learn techniques to reduce complex structures without compromising accuracy, optimizing analysis time and resource utilization.
Simplifying complex geometries is an art that can significantly impact FEA efficiency. By reducing intricate structures to more manageable forms, engineers can accelerate analysis times without sacrificing precision. SolidWorks provides a suite of tools that aids in this process, allowing for the creation of simplified models that maintain the essence of the original design.
Material Selection and Properties
Uncover the impact of material selection on design optimization. Explore how SolidWorks allows engineers to simulate different material properties, aiding in the identification of optimal choices for enhanced performance.
The choice of materials plays a pivotal role in design optimization. SolidWorks facilitates the simulation of various material properties, enabling engineers to explore different scenarios without the need for physical prototypes. Understanding how different materials behave under specific conditions empowers designers to make informed decisions, leading to optimized structures with enhanced performance characteristics.
Boundary Conditions and Constraints
Navigate the nuances of setting boundary conditions and constraints in FEA simulations. Understand how these factors influence results and learn best practices for ensuring realistic and reliable analyses.
Setting accurate boundary conditions and constraints is crucial for obtaining realistic simulation results. In SolidWorks, engineers can define the environmental constraints and structural boundaries with precision. This ensures that the simulation mirrors real-world conditions, providing insights into how the design will perform under various circumstances. Mastering this aspect of FEA optimization is fundamental for achieving reliable and meaningful results.
Meshing Techniques for Accurate Simulations
Dive into the world of meshing and discover its pivotal role in achieving accurate simulations. Explore SolidWorks' meshing tools and techniques to refine your analysis, striking a balance between accuracy and computational efficiency.
Meshing is a critical step in FEA that involves dividing the model into smaller elements for analysis. SolidWorks offers advanced meshing tools that allow engineers to control the density and quality of the mesh. By employing refined meshing techniques, designers can strike a balance between accuracy and computational efficiency, ensuring that the simulation results are both reliable and manageable. Understanding how to optimize meshing parameters is key to harnessing the full potential of FEA in SolidWorks.
These strategies collectively form the backbone of effective FEA optimization in SolidWorks, empowering engineers to refine designs, enhance performance, and streamline the overall design process. By integrating these principles into their workflow, designers can elevate their projects to new levels of efficiency and innovation.
Case Studies: Realizing the Power of FEA Optimization
Illustrate the effectiveness of FEA optimization through real-world case studies. Explore success stories where SolidWorks and FEA have collaborated to overcome design challenges, resulting in superior products.
Real-world case studies showcase the tangible benefits of incorporating FEA into the design process. In one instance, a leading aerospace company utilized SolidWorks and FEA to optimize the structural integrity of a critical aircraft component. Through meticulous simulation, the engineers identified weak points, enabling them to reinforce the design and significantly enhance its performance under varying flight conditions.
Another compelling case involves a consumer electronics manufacturer striving to reduce product weight while maintaining durability. SolidWorks' FEA capabilities allowed the engineers to experiment with different materials and configurations, leading to a breakthrough design that not only met weight reduction goals but also exceeded expectations in terms of product lifespan.
These case studies highlight the versatility of FEA in addressing diverse design challenges, proving its effectiveness in creating superior and innovative products.
Overcoming Common Challenges in FEA Optimization
Design engineers often encounter various challenges when implementing Finite Element Analysis (FEA) for optimization. One common hurdle involves the interpretation of analysis results. Deciphering the data generated by FEA simulations can be complex, requiring a nuanced understanding of how different factors influence the overall performance of a design. Engineers must develop a proficiency in extracting meaningful insights from results to inform subsequent design decisions accurately.
Another noteworthy challenge is optimizing for multiple performance metrics. In real-world applications, designs are often subjected to a range of criteria, from structural integrity and weight reduction to cost-effectiveness. Striking the right balance between these diverse metrics is crucial for achieving a holistic optimization. Design engineers need to adopt a multidimensional approach, considering various factors simultaneously to create designs that excel across multiple parameters.
Addressing nonlinearities in FEA is another significant challenge. Real-world materials and structures often exhibit nonlinear behaviors that can impact the accuracy of simulations. SolidWorks, with its advanced capabilities, empowers engineers to navigate these nonlinear complexities effectively. Understanding and accommodating nonlinearities is essential for ensuring the reliability of FEA results and, consequently, the success of the design optimization process.
Interpreting Analysis Results
Deciphering FEA analysis results can be challenging, requiring a keen understanding of the data generated by simulations. Engineers must not only identify patterns and trends but also discern the implications for their designs. Gain insights into interpreting and understanding results effectively to ensure informed decision-making during the design optimization process.
Navigating through the intricacies of analysis output involves assessing factors such as stress distribution, deformation patterns, and safety margins. By developing a nuanced understanding of these results, engineers can make informed adjustments to enhance the overall performance and reliability of their designs. This section explores practical tips and strategies for effectively interpreting FEA analysis results, empowering engineers to extract actionable insights.
Optimizing for Multiple Performance Metrics
Design optimization goes beyond a singular focus—it involves balancing various performance metrics to create a well-rounded and efficient product. Learn to strike a harmonious equilibrium between critical factors such as structural integrity, weight reduction, and cost-effectiveness. Discover strategies for optimizing designs that meet diverse criteria, ensuring that the final product excels in multiple dimensions.
Optimizing for structural integrity involves ensuring that the design can withstand expected loads and environmental conditions. Simultaneously, considerations for weight reduction contribute to improved efficiency and resource utilization. Cost-effectiveness remains a pivotal factor in commercial success, making it essential to find synergies between these often competing objectives. This section provides practical guidance on navigating the complexities of optimizing for multiple performance metrics, offering a holistic approach to design enhancement.
Addressing Nonlinearities in FEA
Real-world scenarios often exhibit nonlinear behaviors that impact the performance of designs. Addressing these complexities in FEA simulations is crucial for accurate predictions and effective design optimization. Explore how SolidWorks accommodates nonlinear behaviors, providing a comprehensive approach to handling intricate challenges posed by real-world conditions.
From material nonlinearity to geometric complexities, this section delves into the various types of nonlinearities that engineers may encounter in their designs. Understand the tools and features within SolidWorks that enable the simulation of nonlinear behaviors, allowing for a more realistic representation of a design's response to external factors. By addressing nonlinearities effectively, engineers can refine their designs to better align with actual operating conditions, enhancing overall performance and reliability.
Future Trends: FEA and the Evolution of Design Optimization
As we peer into the horizon of design engineering, it becomes evident that the future holds transformative trends that will reshape the landscape of Finite Element Analysis (FEA) and design optimization. One notable trend is the integration of artificial intelligence (AI) into simulation processes. AI-driven simulations are set to revolutionize how engineers approach and execute FEA. Machine learning algorithms can analyze vast datasets, identifying patterns and optimizing designs with unprecedented speed and accuracy. This not only expedites the design iteration process but also opens doors to novel solutions that may have been challenging to discover through traditional methods.
Furthermore, the future of FEA is intertwined with the rise of cloud-based collaboration. Cloud computing offers a scalable and collaborative environment for engineers to perform simulations and share results seamlessly. This shift to the cloud facilitates real-time collaboration among team members, regardless of geographical locations. Design iterations, simulations, and analyses can be conducted collaboratively, fostering a more dynamic and efficient design process. The accessibility and flexibility provided by cloud-based FEA platforms contribute to accelerated innovation and enhanced productivity within engineering teams.
As we embrace these future trends, it's essential for design engineers to stay attuned to the evolving technological landscape. The marriage of AI-driven simulations and cloud-based collaboration signifies a paradigm shift in how we approach design optimization. By harnessing these advancements, engineers can navigate the complexities of modern design challenges with agility, pushing the boundaries of what's possible in the realm of Finite Element Analysis and design excellence.
Conclusion
In essence, mastering Finite Element Analysis (FEA) within SolidWorks isn't just about adopting a cutting-edge tool; it's about transforming your entire design philosophy. As we conclude this insightful journey, let's delve deeper into the profound implications of integrating FEA into your design repertoire.
The newfound knowledge you've gained is more than a set of technical skills; it's a gateway to innovation. FEA opens doors to previously unexplored realms of design possibilities. It encourages engineers to think beyond traditional boundaries, pushing the limits of what's achievable. By understanding the intricacies of FEA, you're not just optimizing designs; you're revolutionizing your approach to problem-solving.
Embracing the power of FEA is akin to unleashing a creative force within your team. It's about instilling a mindset that views challenges as opportunities and constraints as catalysts for ingenious solutions. FEA empowers your team to iterate rapidly, experiment fearlessly, and conceptualize designs that go beyond incremental improvements. It's the catalyst for a culture of continuous innovation, where every analysis result is a stepping stone toward a more refined and optimized design.
FEA isn't just a tool; it's a conduit for streamlining workflows. The efficiencies gained through simulation and analysis cascade through every stage of the design process. Time-consuming iterations become streamlined, and the once tedious process of trial and error evolves into a well-defined path toward perfection. SolidWorks, with its integrated FEA capabilities, becomes more than software; it becomes a collaborator, a partner in the pursuit of design excellence.
Moreover, the impact of FEA extends far beyond individual projects. It's a catalyst for elevating your entire design portfolio to new heights. The skills acquired in optimizing one project using FEA become transferable assets, enriching the collective knowledge of your team. As your team becomes adept at leveraging FEA, the ripple effect is felt across all your designs, leading to a portfolio distinguished by efficiency, reliability, and innovation.