- Understanding the Foundation of Weldment Documentation
- Enhancing Communication Through Detailed Drawings
- Navigating the Challenges of Weldment Tolerances Documentation
- Compliance and Regulations: A Documentation Imperative
- Streamlining Workflow with Documented Procedures
- The Evolving Role of Digital Documentation in Weldments
- Mitigating Risks Through Comprehensive Documentation
- Conclusion
In the realm of SolidWorks assignments, the meticulous process of documenting weldments holds paramount significance. Proper documentation not only ensures a seamless workflow but also plays a pivotal role in the overall success of a project. In this blog, we delve into the various facets of why adequate documentation is indispensable in the realm of weldment assignments. If you need help with your weldment assignment we're here to provide guidance and support throughout your academic journey.
In the dynamic field of engineering, precision and accuracy are the cornerstones of success. Weldments, involving the fusion of various components to create a unified structure, demand a meticulous approach to documentation. The process of creating comprehensive records detailing the specifications, tolerances, and assembly procedures forms the backbone of a successful weldment project.
One of the primary reasons documentation is crucial in the context of SolidWorks weldments is the need for clear communication. A well-documented project serves as a shared language among team members, allowing engineers, fabricators, and stakeholders to interpret and execute tasks with precision. Detailed drawings, a fundamental component of documentation, provide a visual representation that transcends linguistic barriers, ensuring everyone involved is on the same page.
Moreover, the documentation process is intricately linked to the establishment of a robust foundation for any engineering endeavor. Understanding the foundational principles of weldment documentation involves recognizing the critical parameters that contribute to the project's success. This includes defining weldment features, specifying materials, and establishing tolerances that align with the project's design objectives.
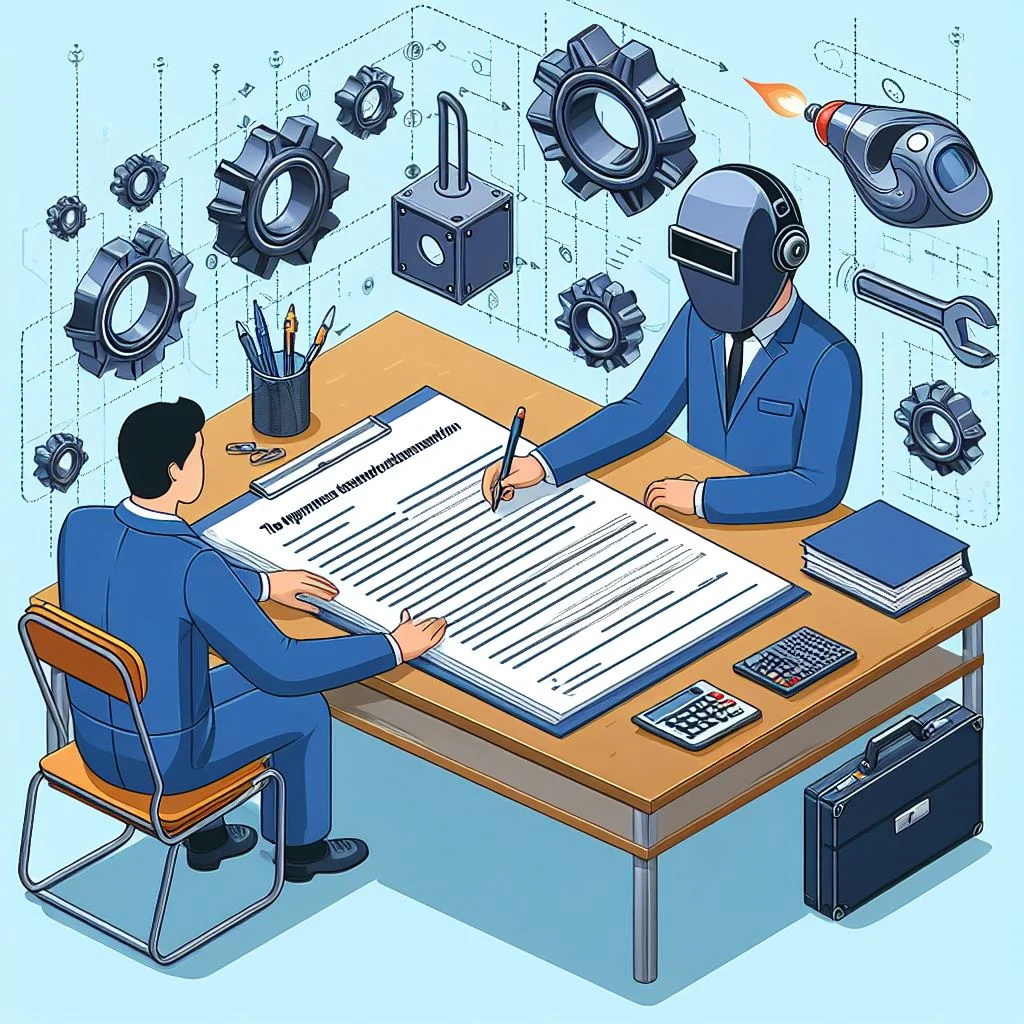
As projects become more complex, the importance of documenting tolerances in weldments becomes increasingly evident. Tight tolerances are often a necessity to ensure the structural integrity and functionality of the final product. Documenting tolerances meticulously allows for the identification of potential challenges early in the design phase, facilitating adjustments that prevent costly errors during fabrication.
In addition to fostering precision and communication, documentation serves as a cornerstone for compliance with industry standards and regulations. Weldment projects must adhere to specific codes and safety standards to guarantee the structural integrity and safety of the final product. Proper documentation ensures that every step of the project aligns with these standards, mitigating risks and liabilities associated with non-compliance.
The role of documentation extends beyond the traditional pen-and-paper methods. In today's digital age, the integration of digital tools in weldment documentation has become a transformative force. Three-dimensional modeling, collaborative platforms, and real-time updates have revolutionized the way engineers approach and execute weldment assignments. Digital documentation not only enhances accuracy but also promotes a more streamlined and collaborative workflow.
Furthermore, a comprehensive documentation framework contributes to the efficiency of the entire project lifecycle. Well-documented procedures, from assembly processes to quality checks, provide a roadmap for project execution. This streamlining of workflows minimizes errors, reduces ambiguity, and ultimately accelerates project completion without compromising on quality.
In conclusion, the importance of proper documentation in SolidWorks weldment assignments cannot be overstated. It is a multifaceted tool that ensures precision, facilitates clear communication, aids in compliance with industry standards, and streamlines project workflows. As the engineering landscape evolves, embracing innovative digital documentation methods becomes imperative for staying ahead in the realm of weldment design and fabrication.
Understanding the Foundation of Weldment Documentation
In any engineering project, establishing a robust foundation is key to ensuring the success and longevity of the endeavor. When it comes to weldments, this foundation is intricately tied to the comprehension of fundamental aspects of documentation. The significance of this understanding cannot be overstated, as it sets the stage for the entire project lifecycle.
Comprehending the nuances of weldment documentation involves a multifaceted approach. First and foremost, engineers must have a profound grasp of the core principles that govern the welding processes. This includes an in-depth understanding of metallurgy, material properties, and the intricacies of weld joint design. By delving into these principles, engineers can make informed decisions about the appropriate welding techniques, ensuring the structural integrity and performance of the final product.
Moreover, outlining the essential components that contribute to the foundation of sound weldment documentation is imperative. This encompasses creating a comprehensive bill of materials (BOM), detailing welding symbols and specifications, and providing clear instructions for fabrication and assembly. Engineers must meticulously plan and document each step, fostering a transparent and systematic workflow that is essential for project success.
In essence, the foundation of weldment documentation is a blend of theoretical knowledge and practical application. It is a dynamic process that evolves with the project's complexity, requiring adaptability and a keen eye for detail. As we journey through this exploration of weldment documentation, we will uncover the intricacies that make it an indispensable pillar in the world of engineering.
Enhancing Communication Through Detailed Drawings
In the intricate web of engineering projects, effective communication stands out as the linchpin for success. Detailed drawings play a pivotal role in establishing this seamless communication, acting as a universal language that transcends the boundaries of spoken or written words. These drawings serve as the visual blueprints that convey intricate details, specifications, and dimensions, fostering a clear understanding among diverse stakeholders involved in a weldment project.
One of the remarkable aspects of detailed drawings is their ability to bridge communication gaps among team members, fabricators, and stakeholders with different technical backgrounds or linguistic preferences. In the absence of a common spoken language, these drawings become the shared dialect that everyone involved can comprehend. Through a careful and precise representation of weldment components, connections, and tolerances, detailed drawings ensure that the vision of the project is universally understood, reducing the risk of misinterpretation and errors.
Moreover, the art of creating these drawings goes beyond mere technicalities. It involves a thoughtful consideration of how visual information can be presented in a way that resonates with everyone involved. Clarity, consistency, and adherence to industry standards are key elements that contribute to the effectiveness of detailed drawings in conveying the nuances of a weldment project. In essence, these drawings serve as a visual contract, ensuring that all parties involved are on the same page and aligned towards the common goal of achieving precision in the weldment project.
Navigating the Challenges of Weldment Tolerances Documentation
Precision is indeed the essence of engineering, and weldment tolerances serve as the fine threads that weave it into the fabric of a successful project. However, navigating the intricacies of documenting weldment tolerances comes with its own set of challenges. One of the primary hurdles lies in striking the delicate balance between the desired precision and the practical constraints of manufacturing processes.
In the realm of weldments, factors such as material properties, welding techniques, and environmental conditions can introduce variables that impact tolerances. Documenting these intricacies requires a keen understanding of the interplay between design specifications and real-world manufacturing constraints. A misjudgment in tolerances can lead to issues such as weld distortion, material stress, or compromised structural integrity.
Meticulous documentation is the beacon that guides engineers through this maze of challenges. It involves not only specifying the desired tolerances but also providing comprehensive guidelines on how to achieve and verify them. This may include detailing the acceptable deviations, recommended welding procedures, and inspection methods to ensure that the end product aligns with the stringent quality standards set forth in the initial design.
Furthermore, the documentation process must be agile enough to accommodate changes or unforeseen issues during the manufacturing phase. Clear communication channels between design teams and manufacturers, documented contingency plans, and real-time updates to tolerance specifications all contribute to the resilience of the project in the face of challenges.
Compliance and Regulations: A Documentation Imperative
In the intricate landscape of weldments, compliance with industry standards and regulations is non-negotiable. This segment explores the vital role documentation plays in ensuring adherence to codes, standards, and safety regulations, ultimately contributing to the longevity and reliability of welded structures.
Understanding and navigating the complex web of industry standards is crucial in the world of weldments. Documentation serves as the linchpin, providing a comprehensive record of every step taken to comply with these standards. Weldments are subject to a myriad of codes and regulations, whether it be the American Welding Society (AWS) standards, ISO standards, or specific guidelines dictated by regulatory bodies.
Proper documentation not only demonstrates a commitment to quality but also acts as a safeguard against potential legal issues. In the event of an audit or inspection, having a meticulously documented trail ensures transparency and provides evidence of compliance. This level of documentation extends beyond meeting the bare minimum requirements; it serves as a testament to a commitment to excellence, instilling confidence in clients, stakeholders, and regulatory authorities.
Furthermore, as standards evolve and new regulations emerge, documented processes allow for agile adaptation. Regular updates to documentation ensure that projects stay aligned with the latest industry requirements, guaranteeing that welded structures not only meet current standards but also anticipate future changes. In essence, the documentation imperative in compliance and regulations is not just a box to be checked but a dynamic tool that fosters a culture of continuous improvement and unwavering commitment to quality and safety.
Streamlining Workflow with Documented Procedures
Efficiency serves as the lifeblood of successful project management, and in the realm of weldment assignments, the implementation of well-documented procedures is the linchpin for achieving this efficiency. The streamlining of workflows through meticulous documentation extends across various stages of a project, leaving an indelible mark on its overall success.
In the assembly processes, detailed documentation acts as a guiding light, offering a roadmap for the seamless integration of individual components. Precise instructions on part orientation, alignment, and welding sequences ensure that the assembly process unfolds with clockwork precision. This not only minimizes the likelihood of errors but also accelerates the assembly phase, contributing to significant time savings.
Quality checks, a cornerstone of any engineering project, are elevated to a new standard with thorough procedural documentation. The guidelines for inspecting welds, assessing material integrity, and conducting non-destructive testing are clearly outlined, leaving no room for ambiguity. This not only enhances the accuracy of quality assessments but also establishes a standardized approach that aligns with industry best practices.
Consistency, a hallmark of well-executed projects, is nurtured through documented procedures. Every team member, regardless of their role, can refer to a standardized set of guidelines, ensuring that each task is executed uniformly. This not only fosters a sense of cohesion within the team but also contributes to the creation of a reliable and consistent end product.
Moreover, the overall project efficiency experiences a significant boost as a result of well-documented procedures. The reduction in errors, the acceleration of processes, and the establishment of a standardized workflow collectively contribute to timely project completion. The time saved can be redirected towards refining and optimizing other aspects of the project, further enhancing its overall quality and success. In essence, the incorporation of detailed procedural documentation in weldment assignments becomes the catalyst for achieving operational excellence and project triumph.
The Evolving Role of Digital Documentation in Weldments
In an era dominated by technological advancements, digital documentation has indeed emerged as a transformative game-changer in the landscape of weldment assignments. The integration of digital tools has redefined how engineers approach and execute projects, bringing a host of benefits that extend beyond traditional documentation methods.
One of the noteworthy advantages is the utilization of 3D modeling in weldment assignments. This advanced modeling technique provides a holistic view of the project, allowing engineers to visualize and analyze the weldment structures in a three-dimensional space. The precision offered by 3D modeling significantly enhances the accuracy of documentation, leading to more accurate representations of weldment components and assemblies.
Collaborative platforms further amplify the impact of digital documentation. In a globally connected world, team members may be dispersed across different geographical locations. Collaborative platforms bridge this gap by facilitating real-time communication and collaboration. Engineers can work seamlessly on shared documents, make simultaneous modifications, and receive instant feedback, fostering a collaborative environment that transcends physical boundaries.
Real-time updates represent yet another facet of the digital revolution in weldment documentation. Traditional methods often entail time-consuming revision processes, with updates requiring manual implementation. With digital documentation, changes can be implemented instantly, ensuring that all team members are working with the latest information. This agility not only accelerates project timelines but also minimizes the risk of errors associated with outdated documentation.
In essence, the evolving role of digital documentation in weldments goes beyond mere adaptation; it represents a paradigm shift in how engineers conceive, communicate, and execute weldment assignments, ushering in an era of unprecedented precision, efficiency, and collaboration.
Mitigating Risks Through Comprehensive Documentation
In the intricate landscape of weldment assignments, the importance of mitigating risks cannot be overstated. Every engineering project inherently carries a level of uncertainty, and weldment assignments are no exception. Comprehensive documentation emerges as a powerful ally in navigating these uncertainties, effectively serving as a robust risk mitigation strategy.
A critical aspect of this risk mitigation lies in the proactive identification of potential challenges. Through thorough documentation, engineers can anticipate and analyze potential stumbling blocks before they manifest into critical issues. This foresight allows for the implementation of preemptive measures, ensuring that the project remains on course and disruptions are minimized.
Moreover, a well-documented approach acts as a shield against unforeseen obstacles that may arise during the various phases of a weldment project. Whether it's changes in design specifications, material shortages, or unexpected fabrication issues, having a comprehensive documentation framework provides a roadmap for swift decision-making and problem resolution.
In essence, the role of documentation in risk mitigation extends beyond a mere record-keeping function. It becomes a dynamic tool that empowers engineers to proactively manage and navigate the challenges inherent in weldment assignments, fostering a resilient project environment. As the saying goes, "forewarned is forearmed," and in the realm of weldments, comprehensive documentation serves as the sentinel that guards against the uncertainties that may arise, ensuring smoother project progression and successful outcomes.
Conclusion
In conclusion, the importance of proper documentation in weldment assignments cannot be overstated. As we've traversed through the various dimensions of this critical aspect, it becomes evident that meticulous documentation is the linchpin that holds together the entire fabric of a successful SolidWorks project.
Effective documentation serves as the glue that binds project teams, fabricators, and stakeholders in a unified understanding of the project's intricacies. The foundation of weldment documentation is rooted in a comprehensive comprehension of its fundamental aspects. From understanding the material properties to delineating welding symbols and annotations, a well-established foundation sets the stage for a smooth and error-free project execution.
Detailed drawings emerge as the unsung heroes of communication in the engineering realm. These drawings transcend linguistic barriers, enabling a seamless exchange of information between diverse teams involved in the weldment project. The intricate details captured in these drawings become a visual language, ensuring that everyone involved is on the same page, thereby reducing the chances of misunderstandings and errors.
Tolerances, a critical component of weldment design, often present challenges that can impede the overall success of a project. However, through meticulous documentation of tolerances, engineers can navigate these challenges adeptly. By clearly defining and communicating tolerances, the risk of errors and deviations is significantly reduced, ensuring the final product meets the stringent quality standards expected in engineering projects.
Compliance and adherence to industry regulations are imperative in the field of weldments. Documentation acts as a safeguard, ensuring that every step of the project aligns with the prescribed standards and safety regulations. The documentation process becomes a crucial tool for quality assurance, providing a roadmap to compliance that guarantees the integrity and safety of the welded structures.
The streamlining of workflows through documented procedures is a key outcome of effective documentation practices. These procedures serve as a guide, ensuring that every step of the project, from assembly processes to quality checks, is conducted with precision and consistency. By providing a standardized framework, documented procedures minimize errors, enhance efficiency, and contribute to the overall success of the weldment assignment.
In the digital era, the role of documentation has evolved with the advent of advanced technologies. Digital documentation, facilitated by 3D modeling and collaborative platforms, has revolutionized the way weldment assignments are approached. Real-time updates, interactive models, and collaborative tools have enhanced the efficiency of project teams, fostering a more dynamic and responsive approach to documentation.
Mitigating risks is an inherent aspect of any engineering project, and comprehensive documentation emerges as a powerful risk mitigation strategy. By identifying potential challenges, establishing preemptive measures, and documenting risk management protocols, engineers can navigate uncertainties with confidence, ensuring that the project progresses smoothly even in the face of unforeseen obstacles.
In essence, the journey through the nuances of weldment documentation highlights its indispensability in the holistic success of SolidWorks projects. It goes beyond being a mere administrative task; it is the bedrock upon which precision, compliance, and efficiency are built. As SolidWorks continues to evolve, so too does the role of documentation, becoming not just a requirement but a strategic asset that propels engineering projects toward excellence and reliability.