- Understanding the Basics of Sheet Metal Design
- The Importance of Accurate Measurements
- Material Selection Matters
- Mastering SolidWorks Sheet Metal Tools
- Utilizing the Base Flange Feature
- Working with Bend and Hem Features
- Incorporating Gussets and Fillets
- Optimizing Your Workflow in SolidWorks
- Using Design Tables for Iterative Design
- Taking Advantage of Sheet Metal Flat Pattern
- Best Practices for Collaboration and Documentation
- Annotating and Detailing Your Design
- Collaborating with Others in SolidWorks
- Conclusion
In the intricate world of sheet metal design, harnessing the capabilities of SolidWorks can be a game-changer. SolidWorks, a leading 3D modeling software, empowers engineers and designers with a suite of tools tailored for precision and efficiency in sheet metal projects. This article unfolds practical tips to elevate your proficiency in SolidWorks for sheet metal assignments, unraveling the intricate process of transforming digital designs into tangible, precisely crafted metal components.
Navigating the nuances of sheet metal design begins with a comprehensive understanding of SolidWorks' fundamental features, especially when seeking assistance with your Sheet Metal assignment. Accurate measurements, a cornerstone of any successful design, are effortlessly achieved through tools like Smart Dimension. Material selection is equally pivotal, and SolidWorks' extensive material library, coupled with simulation capabilities, facilitates informed decisions on durability, cost-effectiveness, and performance. As we delve deeper, we'll explore the intricate dance between SolidWorks tools, from the foundational Base Flange feature to the nuanced Bend and Hem features, empowering designers to shape metal seamlessly. Whether you are a novice embarking on your first sheet metal project or a seasoned professional seeking to refine your skills, this exploration of SolidWorks for sheet metal design promises practical insights to elevate your assignments.
Understanding the Basics of Sheet Metal Design
Sheet metal design is a meticulous craft, and SolidWorks provides the foundational tools to bring precision to your creations. At its core, accurate measurements form the backbone of any successful sheet metal project. SolidWorks' Smart Dimension tool empowers you to meticulously define sizes and positions, ensuring your design adheres to exact specifications. Equally important is the judicious selection of materials; SolidWorks offers a comprehensive material library, allowing you to match the physical properties of your design with the right material. As you embark on your sheet metal design journey in SolidWorks, mastering these basics sets the stage for the seamless translation of your digital concepts into precisely fabricated physical realities.
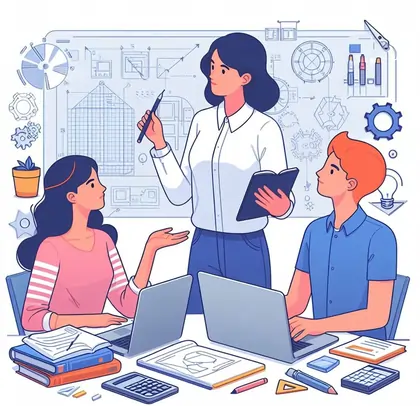
The Importance of Accurate Measurements
Accurate measurements form the bedrock of successful sheet metal design in SolidWorks. In the realm of precision engineering, even the slightest deviation can lead to significant errors in the final product. SolidWorks, equipped with its advanced dimensioning tools like Smart Dimension, empowers designers to define and manipulate measurements with utmost precision. A profound understanding of these tools ensures that every component's size and position are meticulously determined, guaranteeing the integrity of your sheet metal design. Whether you're crafting a complex enclosure or a simple bracket, the reliability of your measurements directly impacts the manufacturability and functionality of the final product. In SolidWorks, embracing the mantra of "measure twice, cut once" becomes a digital reality, allowing you to translate your design intent into a flawlessly engineered sheet metal masterpiece.
Material Selection Matters
In the realm of sheet metal design, the significance of material selection cannot be overstated. SolidWorks empowers designers with a comprehensive material library, offering a diverse range of options to align with varying project requirements. When crafting your sheet metal masterpiece, delving into this library with a discerning eye is crucial. Consider not only the physical attributes of materials but also their manufacturability and the intended application of the final product. SolidWorks provides a unique opportunity to simulate different material properties, allowing you to fine-tune your design for optimal strength, weight, and cost-efficiency. So, whether you're aiming for structural robustness or aiming to keep things lightweight, making informed choices within SolidWorks can be the key to elevating your sheet metal designs from good to exceptional.
Mastering SolidWorks Sheet Metal Tools
Mastering SolidWorks Sheet Metal Tools is a transformative step toward becoming a proficient designer. The Base Flange feature serves as the cornerstone, enabling the definition of initial parameters and setting the stage for intricate sheet metal designs. Delve into the intricacies of Bend and Hem features to precisely shape and refine your creations, gaining control over bend angles, radii, and edge aesthetics. The incorporation of Gussets and Fillets adds structural integrity and a polished finish to your designs. By understanding how to efficiently use these features, designers can elevate their sheet metal creations from mere concepts to manufacturable, resilient products. SolidWorks empowers users with a toolbox rich in functionality, encouraging exploration and experimentation to unlock the full potential of sheet metal design.
Utilizing the Base Flange Feature
The Base Flange feature in SolidWorks serves as the cornerstone for initiating any sheet metal design. This powerful tool allows designers to define the fundamental parameters of a sheet metal part, setting the stage for subsequent features. With the Base Flange, users can precisely specify sheet thickness, bend radii, and even incorporate relief cuts where necessary. SolidWorks offers flexibility by accommodating a variety of bend conditions, enabling the creation of complex geometries. By mastering the intricacies of the Base Flange feature, designers gain a solid foundation for crafting intricate sheet metal components, ensuring accuracy from the outset of the design process.
Working with Bend and Hem Features
SolidWorks' Bend and Hem features are indispensable when it comes to shaping and refining your sheet metal designs. The Bend feature allows for precise control over the angle, radius, and direction of bends, offering the flexibility needed to achieve the desired structural integrity. Mastering this feature ensures that your designs not only meet but exceed manufacturing standards. Additionally, the Hem feature adds the finishing touch by creating smooth edges, enhancing both the aesthetics and functionality of your sheet metal part. Understanding the nuances of these features empowers designers to create sheet metal components that are not just accurate in form but also optimized for performance and visual appeal. Whether you're working on prototypes or production-ready parts, harnessing the potential of Bend and Hem features in SolidWorks elevates your sheet metal designs to new heights of precision and craftsmanship.
Incorporating Gussets and Fillets
Gussets and fillets are the unsung heroes of sheet metal design, contributing both to structural integrity and aesthetic appeal. SolidWorks simplifies the process of integrating these elements seamlessly into your design. When strategically placed, gussets act as reinforcements, enhancing the rigidity of joints and corners, thereby fortifying your sheet metal part against potential stress points. Understanding how to employ fillets is equally crucial; these subtle curves not only elevate the visual finesse of your design but also play a pivotal role in reducing stress concentrations. SolidWorks' dedicated features for gussets and fillets empower designers to fine-tune the balance between strength and aesthetics, resulting in sheet metal creations that marry form and function effortlessly.
Optimizing Your Workflow in SolidWorks
Efficiency is the cornerstone of successful sheet metal design, and SolidWorks offers a plethora of tools to optimize your workflow. Embracing the power of Design Tables can significantly expedite the iterative design process, allowing you to seamlessly experiment with various configurations. Whether you're exploring different sizes, materials, or manufacturing constraints, Design Tables serve as a dynamic solution. Additionally, the Sheet Metal Flat Pattern feature is a game-changer for ensuring a smooth transition from digital design to physical creation. Learning how to generate and manipulate flat patterns not only enhances precision but also streamlines the manufacturing phase. By integrating these tools effectively into your workflow, SolidWorks becomes not just a design platform, but a catalyst for efficiency in sheet metal design projects.
Using Design Tables for Iterative Design
Design Tables in SolidWorks serve as a dynamic canvas for iterative refinement, enabling a seamless exploration of various configurations within your sheet metal design. These tables empower you to efficiently manipulate dimensions, materials, and other critical parameters, allowing for rapid adjustments and experimentation. As you delve into the intricacies of iterative design, understanding how to harness the full potential of Design Tables becomes a game-changer. By strategically organizing and modifying data in these tables, you not only enhance your workflow but also pave the way for a more systematic and insightful approach to refining your sheet metal designs. Mastery of this feature not only boosts efficiency but opens up new dimensions of creativity, turning the design process into a dynamic, interactive journey.
Taking Advantage of Sheet Metal Flat Pattern
Mastering the Sheet Metal Flat Pattern feature in SolidWorks opens a gateway to precision in manufacturing. The Flat Pattern is not just a visual representation; it's a practical template for transforming digital designs into physical reality. SolidWorks simplifies this process, allowing you to generate accurate flat patterns effortlessly. Understanding how to manipulate and refine these flat patterns is crucial for ensuring that your sheet metal part can be precisely cut and bent in the real world. By delving into the intricacies of the Flat Pattern feature, you empower yourself to bridge the gap between virtual design and tangible creation, making your sheet metal projects not just digitally sound but seamlessly manufacturable.
Best Practices for Collaboration and Documentation
Collaboration and documentation are the bedrock of successful engineering projects, and SolidWorks offers a robust set of tools to facilitate these crucial aspects. When it comes to collaboration, leveraging SolidWorks' collaborative features, such as PDM, can significantly enhance teamwork efficiency. PDM enables seamless version control, change tracking, and secure data management, ensuring that everyone on the team is working with the most up-to-date information. In terms of documentation, SolidWorks provides intuitive annotation and detailing tools, allowing engineers to communicate design intent clearly. Ensuring that your sheet metal design is thoroughly annotated with dimensions, notes, and symbols not only aids in understanding but also becomes invaluable when passing on the project to others or revisiting it in the future. Embracing these best practices within SolidWorks transforms it from a mere design tool into a comprehensive platform for fostering collaboration and maintaining meticulous project documentation.
Annotating and Detailing Your Design
In the intricate world of sheet metal design, effective communication of design intent is as crucial as the design itself. SolidWorks offers a suite of annotation and detailing tools that can transform your 3D model into a comprehensive blueprint. Utilize the power of dimensions, geometric tolerances, and surface finishes to precisely convey critical information. Seamlessly integrate notes and symbols to highlight manufacturing specifications and assembly instructions. This meticulous annotation not only serves as a roadmap for fabrication but also facilitates collaboration by ensuring that every team member interprets the design parameters accurately. Mastery of these annotation and detailing features in SolidWorks elevates your designs from digital concepts to tangible realities with unmatched precision.
Collaborating with Others in SolidWorks
Collaboration is the heartbeat of innovation, and SolidWorks provides a robust platform for seamless teamwork in sheet metal design projects. The Product Data Management (PDM) features in SolidWorks empower multiple users to collaborate effectively. With PDM, team members can concurrently work on the same design, ensuring real-time updates and minimizing the risk of conflicting changes. Version control becomes intuitive, allowing for a clear audit trail of modifications. Additionally, communication is enhanced through integrated commenting and annotation tools, facilitating a dynamic exchange of ideas and feedback. SolidWorks' collaborative capabilities not only improve efficiency but also foster a synergistic environment where the collective expertise of a team can be harnessed to achieve optimal sheet metal designs.
Conclusion
In conclusion, the journey through SolidWorks for sheet metal design is a transformative experience, unlocking a realm of precision and creativity for engineers and designers alike. By delving into the nuances of accurate measurements, judicious material selection, and mastering the formidable array of SolidWorks features, you empower yourself to create sheet metal designs that are not only structurally sound but also visually compelling. From the foundational Base Flange feature to the intricacies of bends, hems, gussets, and fillets, SolidWorks provides a comprehensive toolkit. Remember to optimize your workflow through Design Tables, embrace the power of the Sheet Metal Flat Pattern, and prioritize collaboration and documentation. As you navigate this digital terrain, you're not just designing; you're sculpting possibilities. So, seize the potential within SolidWorks, and let your sheet metal designs unfold with the precision and innovation that this powerful tool offers.