- Understanding Solidworks Simulation Basics
- Types of Analysis in Solidworks Simulation
- Meshing Techniques for Accurate Simulations
- Troubleshooting and Common Pitfalls
- Advanced Simulation Features and Add-ons
- Real-World Case Studies
- Conclusion:
Solidworks Simulation stands as a cornerstone for engineers, offering a robust platform to scrutinize and enhance designs long before they manifest physically. For college students embarking on their SolidWorks journey, delving into the intricacies of Simulation unveils a plethora of opportunities. This guide aims to be your compass, navigating through essential concepts and techniques, ultimately steering you towards proficiency and providing help with your Simulation assignments.
The significance of Solidworks Simulation lies in its ability to bridge the gap between concept and reality. It empowers engineers to dissect their designs virtually, identifying potential flaws, and fine-tuning every detail before a physical prototype is even created. This not only saves time and resources but also ensures a more refined and reliable end product. For students venturing into the dynamic realm of Solidworks, mastering the nuances of Simulation becomes a gateway to honing practical skills crucial for a successful career in engineering.
As we navigate through this comprehensive guide, we will unravel the foundational elements that form the backbone of Solidworks Simulation proficiency. Understanding the basics of the interface, setting up simulation studies, and defining material properties are the initial stepping stones. This foundational knowledge lays the groundwork for more advanced explorations, allowing you to harness the full potential of Solidworks Simulation.
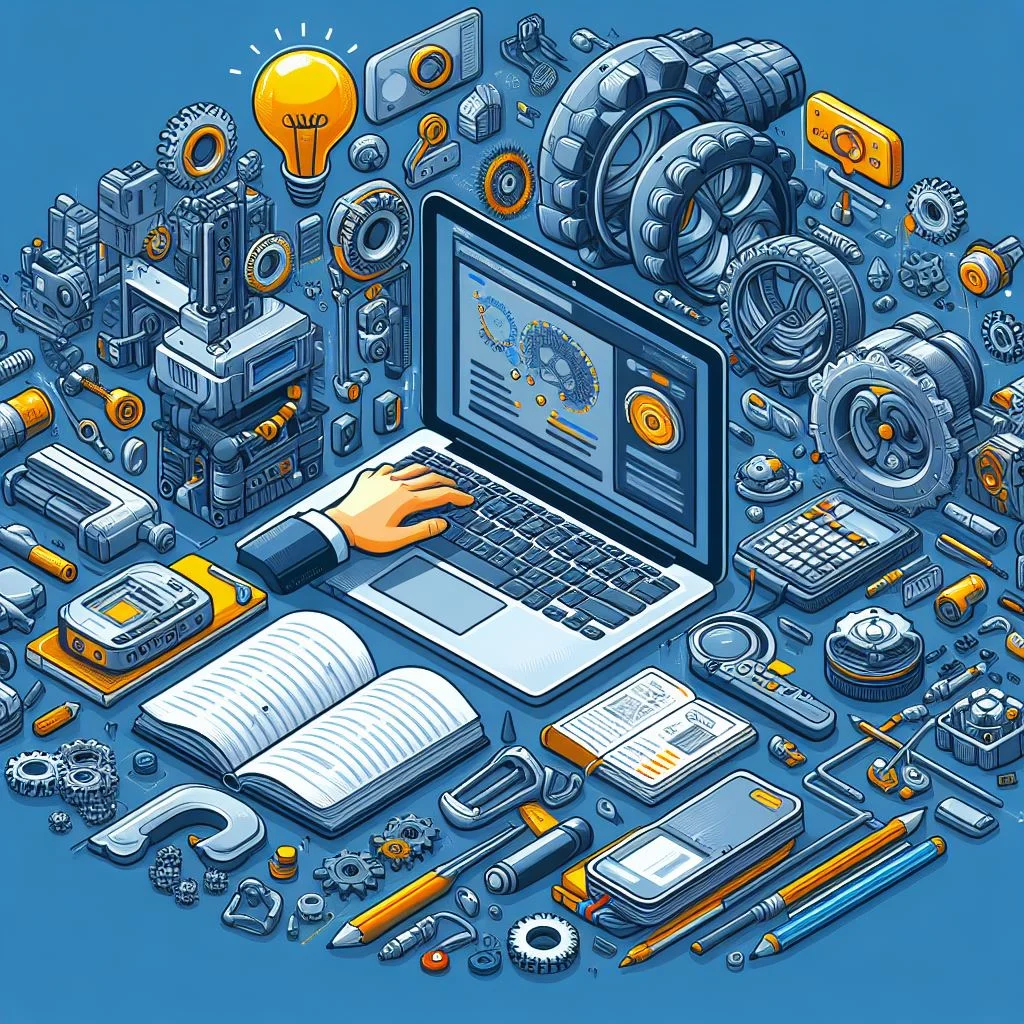
Beyond the basics, the guide will lead you through an exploration of the diverse analyses offered by Solidworks Simulation. From static and dynamic studies to thermal and frequency analysis, each analysis type serves a unique purpose. Knowing when and how to apply these analyses is key to obtaining accurate results tailored to specific engineering scenarios.
Meshing, a critical aspect of simulation, will be thoroughly discussed. Meshing techniques, encompassing element types, size considerations, and best practices, will be demystified. Striking the right balance between accuracy and computational efficiency is a skill that sets proficient Solidworks Simulation users apart.
Boundary conditions and constraints play a pivotal role in the accuracy of simulations. This guide will provide insights into the application of realistic conditions and constraints, ensuring that your virtual simulations closely mirror real-world scenarios. Material selection and properties, another critical aspect, will be explored in detail. The guide will delve into choosing materials, assigning properties, and validating selections, ensuring a nuanced understanding of material behaviors.
To elevate your simulation prowess, the guide will venture into parametric studies and optimization techniques. This advanced skill set allows you to systematically tweak design parameters to achieve optimal results. It also sheds light on how Solidworks Simulation can streamline the iterative design process, a valuable asset in the professional engineering landscape.
Fatigue analysis, an often-overlooked yet crucial aspect of design validation, will be a focal point. Understanding how components endure cyclic loading conditions is imperative for predicting the lifespan of designs. The guide will provide insights into fatigue analysis tools within Solidworks Simulation, equipping you to assess the durability of your designs comprehensively.
No learning journey is complete without addressing challenges. Troubleshooting common pitfalls in Solidworks Simulation will be a dedicated segment. From convergence issues to interpreting complex results, this section aims to empower you with the skills needed to navigate potential hurdles seamlessly.
As we delve deeper, the guide will unravel advanced features and add-ons that amplify Solidworks Simulation capabilities. Thermal-fluid coupling, non-linear analysis, and other sophisticated tools will be discussed, offering a glimpse into the expansive possibilities of this powerful software.
Real-world case studies will serve as the culmination of your learning experience. By applying the acquired knowledge to practical scenarios, you will witness how Solidworks Simulation has been successfully employed across diverse industries. These case studies provide a bridge between theoretical understanding and real-world application, reinforcing the practical relevance of Solidworks Simulation proficiency.
In conclusion, this guide aspires to be your compass in the realm of Solidworks Simulation. It doesn't just scratch the surface; it dives deep into the intricacies, providing a holistic understanding that goes beyond textbooks. Whether you're a college student venturing into simulation or an engineer looking to enhance your skills, this guide is tailored to elevate your Solidworks Simulation proficiency. As we navigate through key concepts and techniques, remember that mastery is not just a destination but a continuous journey of exploration and growth in the dynamic field of engineering.
Understanding Solidworks Simulation Basics
Solidworks Simulation Basics serve as the cornerstone of your journey into the realm of virtual testing and analysis. Familiarizing yourself with the intuitive interface is the initial step, providing you with a user-friendly platform to navigate through the intricacies of simulation studies. Setting up a simulation study is a pivotal aspect, involving defining the problem, selecting appropriate analysis types, and specifying desired outcomes. This phase requires meticulous attention to detail, as accurate setup directly influences the reliability of simulation results.
Understanding the nuances of material properties is equally paramount. Solidworks Simulation allows you to simulate the behavior of various materials under different conditions. Dive into the extensive material library, explore material properties, and learn how to apply them to your models. This hands-on exploration with simple examples empowers you to comprehend the essentials of material selection, ensuring the accuracy and relevance of your simulation studies.
By immersing yourself in these foundational aspects, you lay the groundwork for a comprehensive understanding of Solidworks Simulation. The hands-on experience with the interface, simulation setup, and material properties not only demystifies the initial learning curve but also instills confidence in your ability to conduct effective simulations in diverse engineering scenarios.
Types of Analysis in Solidworks Simulation
Explore the diverse range of analyses Solidworks Simulation offers, providing engineers with a robust toolkit for design validation. Static studies focus on understanding the effects of loads and forces on a stationary model, allowing for the assessment of structural integrity. Dynamic studies, on the other hand, consider the impact of time-dependent loads, offering insights into how structures respond to varying forces over time.
Thermal analysis becomes crucial when dealing with heat transfer within a system. By simulating temperature distribution and heat flow, engineers can optimize designs for efficient thermal management. Frequency analysis, another vital type, helps in understanding the natural frequencies and modes of vibration in a structure. This is especially significant in scenarios where resonance or vibration can impact the performance and reliability of the design.
Knowing when and how to apply each type of analysis is key to obtaining accurate results for different scenarios. For instance, a structural component in a static environment may require static analysis, while a component subjected to dynamic forces necessitates a dynamic study. By understanding the nuances of each analysis type, engineers can tailor their simulations to match real-world conditions, ensuring the reliability and safety of their designs across various applications.
Meshing Techniques for Accurate Simulations
In the realm of Solidworks Simulation, understanding meshing techniques is pivotal for ensuring accurate and reliable results. Meshing, essentially dividing a model into discrete elements, plays a crucial role in the precision of simulations. Delving deeper into this aspect involves exploring various element types, considering mesh size, and adopting best practices to strike the delicate balance between accuracy and computational efficiency.
When it comes to meshing, the choice of element types can significantly impact simulation outcomes. Solid elements, shell elements, and beam elements each have their advantages and are suited to different types of structures. Grasping when to employ each type is fundamental to achieving realistic simulations that mirror the behavior of physical components.
Mesh size considerations are equally critical. A fine mesh may offer more accurate results, but it comes at the cost of increased computational resources. On the other hand, a coarse mesh speeds up calculations but might sacrifice accuracy. Learning how to optimize mesh density based on the intricacies of your model is an essential skill in Solidworks Simulation.
Best practices in meshing involve a holistic approach, considering the geometry, material properties, and the physics of the simulation. Techniques such as local mesh refinement in areas of interest and mesh sensitivity studies contribute to refining the mesh for better accuracy without unnecessary computational burden.
In essence, mastering meshing techniques is an art that involves a nuanced understanding of simulation requirements and a judicious application of Solidworks Simulation tools. As you delve into the intricacies of meshing, you equip yourself with the skills needed to produce simulations that not only meet industry standards but also stand as reliable predictors of real-world behavior.
Troubleshooting and Common Pitfalls
Even seasoned users encounter challenges in Solidworks Simulation, and navigating through these issues is a crucial aspect of mastering the software. One common hurdle users face is convergence issues during simulations. This occurs when the solver struggles to reach a stable solution, leading to failed analyses. Understanding the root causes of convergence problems, such as inadequate mesh refinement or inappropriate boundary conditions, is essential. The guide will provide insights into identifying these issues and implementing corrective measures to ensure smooth convergence.
Interpreting simulation results can be another stumbling block for users. The abundance of data generated by Solidworks Simulation requires a keen understanding to extract meaningful insights. This section will shed light on result interpretation, including stress and displacement plots, as well as factors affecting accuracy. Users will learn how to discern between realistic outcomes and numerical artifacts, enhancing the reliability of their analyses.
Furthermore, the guide will address challenges related to model geometry and constraints that might lead to unrealistic or inaccurate results. By recognizing and troubleshooting these common pitfalls, users can refine their simulation skills and achieve more accurate and reliable analyses, contributing to the overall success of their engineering projects.
Advanced Simulation Features and Add-ons
Delving into the realm of advanced simulation features and add-ons is a crucial step for aspiring Solidworks Simulation experts. Beyond the foundational concepts, exploring sophisticated tools can significantly enhance your simulation capabilities.
One noteworthy feature is thermal-fluid coupling, a powerful tool for scenarios where heat transfer and fluid flow are intricately linked. This capability is especially valuable in industries like electronics, where understanding how heat dissipates through components is critical for design optimization. By mastering thermal-fluid coupling, you can simulate the behavior of complex systems with greater accuracy, ensuring your designs meet thermal performance requirements.
Another advanced aspect is non-linear analysis, which comes into play when dealing with materials exhibiting nonlinear behaviors, such as plastic deformation or large displacements. Understanding the intricacies of non-linear analysis allows you to model real-world scenarios more accurately, providing insights into how materials respond under extreme conditions. This is particularly valuable in fields like structural engineering and automotive design, where components may experience nonlinear deformations under varying loads.
Moreover, Solidworks Simulation offers additional add-ons that cater to specific industry needs. These may include modules for acoustics, motion analysis, and electromagnetic simulations. Exploring these add-ons expands your toolkit, allowing you to tackle a broader range of simulation challenges across diverse applications.
Incorporating advanced features and add-ons into your Solidworks Simulation skill set empowers you to tackle complex engineering problems with confidence. Understanding when and how to leverage these tools ensures that you not only meet industry standards but also push the boundaries of innovation in your simulations, setting you apart as a proficient and versatile simulation engineer.
Real-World Case Studies
Real-world case studies serve as a bridge between theoretical knowledge and practical application, offering invaluable insights into how Solidworks Simulation is actively shaping various industries. In the automotive sector, engineers utilize Solidworks Simulation to optimize vehicle designs for enhanced safety and performance. By simulating crash scenarios, structural integrity, and fluid dynamics, automotive manufacturers can iteratively refine their designs before physical prototyping, saving both time and resources.
In the aerospace industry, Solidworks Simulation plays a pivotal role in ensuring the structural integrity and aerodynamic efficiency of aircraft components. Engineers can simulate the impact of extreme conditions such as turbulence, high-speed maneuvers, and thermal variations, enabling them to design aircraft that meet rigorous safety and performance standards.
Consumer electronics benefit from Solidworks Simulation by enabling designers to assess the structural integrity, heat dissipation, and overall durability of electronic devices. This ensures that products meet user expectations for reliability and performance while accelerating the product development cycle.
These real-world applications underscore the versatility of Solidworks Simulation across diverse industries. By leveraging simulation tools, professionals can make informed decisions, reduce design iterations, and ultimately bring innovative and reliable products to market. As aspiring engineers, exploring these case studies provides a glimpse into the transformative impact Solidworks Simulation can have on shaping the future of design and engineering.
Conclusion:
In conclusion, embarking on the journey of mastering Solidworks Simulation is a rewarding endeavor that equips students with invaluable skills applicable across various industries. As you wrap up this comprehensive guide, reflect on the key takeaways that will serve as pillars in your proficiency.
Understanding the foundational concepts of Solidworks Simulation sets the stage for success. Whether you are simulating static structures or dynamic assemblies, a strong grasp of the basics, including setting up studies, defining materials, and applying boundary conditions, forms the bedrock of accurate simulations. This knowledge not only ensures the reliability of your analyses but also sets you apart as a proficient Solidworks Simulation user.
As you navigate the diverse types of analyses available in Solidworks Simulation, from thermal studies to frequency analyses, recognize the versatility of the tool. Each analysis type serves a unique purpose, and mastering when to apply them enables you to address a wide range of engineering challenges effectively.
The meticulous attention to meshing techniques is a crucial aspect of achieving accurate simulation results. The choices you make regarding element types, mesh size, and refinement directly impact the precision of your simulations. Balancing the need for finer detail with computational efficiency is an art that comes with practice and experience.
Boundary conditions and constraints play a pivotal role in replicating real-world scenarios in simulations. A nuanced understanding of how these factors influence results allows you to create simulations that mirror actual working conditions, providing insights into the behavior of your designs under various circumstances.
Material selection is an art that goes beyond mere assignment – it involves a deep understanding of material properties and their impact on the performance of your designs. Solidworks Simulation offers extensive material databases, and mastering their utilization ensures that your simulations accurately represent the physical behavior of materials under different conditions.
Parametric studies and optimization techniques take your simulation skills to a level where you can systematically explore design variations. This capability not only aids in achieving optimal results but also streamlines the design iteration process, allowing for quicker and more informed decision-making.
Fatigue analysis, an often-overlooked but critical aspect, adds a layer of sophistication to your simulations. Evaluating the durability of your components under cyclic loading conditions is essential for predicting the lifespan of your designs, especially in industries with stringent performance requirements.
As you encounter challenges and pitfalls in your simulation journey, remember that troubleshooting is an integral part of the learning process. Identifying common issues and developing problem-solving skills contribute to becoming a proficient Solidworks Simulation user.
Delving into advanced features and add-ons further expands your simulation capabilities. Whether you are dealing with thermal-fluid coupling or exploring non-linear analysis, these tools offer solutions for complex engineering problems. The application of these advanced features in real-world scenarios elevates your proficiency to a level where you can tackle intricate challenges with confidence.
In your ongoing quest for mastery, consider exploring real-world case studies that showcase the practical applications of Solidworks Simulation across industries. These examples provide insights into how simulation is employed in solving complex engineering problems, offering inspiration for your own projects.
For those seeking further learning resources, Solidworks communities, forums, and online courses can be invaluable. Engaging with a community of fellow learners and experienced professionals allows you to stay updated on the latest developments, share experiences, and seek guidance when needed.
As you hone your Solidworks Simulation skills, consider the myriad career paths open to those with expertise in simulation. Industries such as automotive, aerospace, manufacturing, and robotics actively seek professionals proficient in simulation tools. Whether you choose a career in product design, analysis, or research and development, your mastery of Solidworks Simulation positions you as a valuable asset in the engineering landscape.
In essence, mastering Solidworks Simulation is not just about acquiring technical skills; it's about developing a mindset of precision, problem-solving, and continuous learning. The knowledge gained from this comprehensive guide is a stepping stone to a fulfilling journey in the realm of simulation, where each challenge becomes an opportunity for growth and innovation.